Introducing
The Voortman Fabricator
automated fitting and full-welding machine for the steel fabricating industry
ПрокрутитьYOUR SOLUTION TO THE SHORTAGE OF QUALIFIED WELDERS
The construction industry is witnessing rapidly changing market requirements, causing several increasing challenges for structural steel fabricators. The most frequently heard challenge is the pressing need to deliver projects on schedule in combination with consistently decreasing availability of skilled fitters and welders.
This is where The Voortman Fabricator comes in, a groundbreaking automatic welding system for structural steel.
Introducing the Voortman Fabricator
The Fabricator is the premier welding system for structural steel, whose flexibility lets you choose on-the-fly between Fit & Weld or only Fit. We offer the quickest turnarounds, maximum efficiency in space utilization and choice-based flexibility - that's what makes our ROI the fastest on the market.
- Ensure on-schedule project with reliable and flexible welding capacity;
- Access a flexible workhorse free from staffing constraints;
- Achieve consistent, high-quality welds, beat material tolerances;
- Secure the quickest return on investment in the market.
HIGH
EFFECTIVE ROI
Excels in speed, agility,
space utilization,
and effortless implementation.
SMALL
FOOTPRINT
Takes up significantly less space than manual welding
VERY
FLEXIBLE
Unlike
other systems,
The Fabricator offers
both fitting only and
full welding options
EASIEST IN
THE INDUSTRY
Comes
with
automated tools that
make work preparations
unbeatably simple
COMPACT DESIGN
AND SMALL FOOTPRINT
Meet the ultimate solution for structural steel fabricators looking to optimize their workspace and streamline their production processes. With its tracks conveniently positioned on one side, loading and unloading are simple to complete. The Fabricator is a space-saving system that fits easily, even in smaller workshops, thanks to its compact design and small footprint.
PROFILE LENGTHS UP
TO 80 FT. (24M)
Welding lengths of up to 24m (80 ft.) make it the ideal choice for handling large-scale welding projects. To ensure even more precision and flexibility, the tracks are exceeding the maximum welding length. This enables the robots to select an optimal track position for welding, while also avoiding singular positions. With this advanced feature, the Fabricator provides maximum efficiency and output, allowing for faster completion of projects while maintaining high-quality standards.
EASY TO OPERATE IN
ANY ENVIRONMENT
You can load with a forklift, side loader, or overhead crane, making it easy to
operate in any workshop. Choose the method that works best for your specific layout and needs.
FAST ROTATIONS FOR
MOST EFFICIENT FLOW
Designed to deliver efficient and reliable welding, makes this the ideal system for large
assemblies with multiple components. Robust main beam rotation allows for quick
movement between weld positions, ensuring a maximum number of parts are attached in less time - making this the most cost-effective choice.
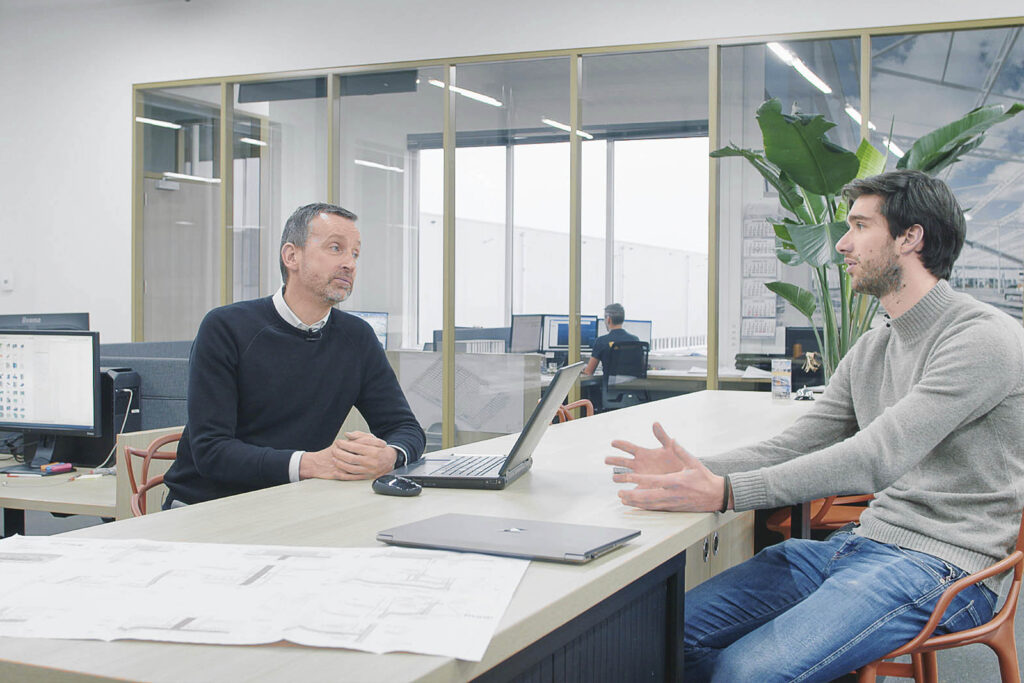
"We believe that the work you save at the back end of your production should not be pushed to the front end. We are committed to upholding this principle by providing solutions designed to make sure it doesn't happen"
HENKJAN VOORTMAN - APPLICATION ENGINEER
HIT THE GROUND RUNNING
With their easy setup process, our automatic welding robots really stand out from the crowd. But also our focus on work preparation is critical, as the success of your machine and its ROI are both highly dependent on thorough detailing and preparation.
THE CONVENIENCE OF DIGI-WELD
For decades, the structural steel industry has already relied on 3D Steel Engineering systems for a designing even the most complex structures. However, this technology was till recently still focused on generating 2D workshop drawings from a model. It wasn't designed with robotic welding in mind - meaning that retrieving digital weld data from engineering models is not a very straightforward task. To bridge the gap between manual and automated processing this data, we use DIGI-WELD: an innovative fully cloud based tool which unlocks the potential of fully automatic welding while maintaining accuracy and quality assurance standards.
DIGI-WELD is a must for The Fabricator, providing automated weld checks & fixes to simplify the complex decision-making and assessment process of welding projects.
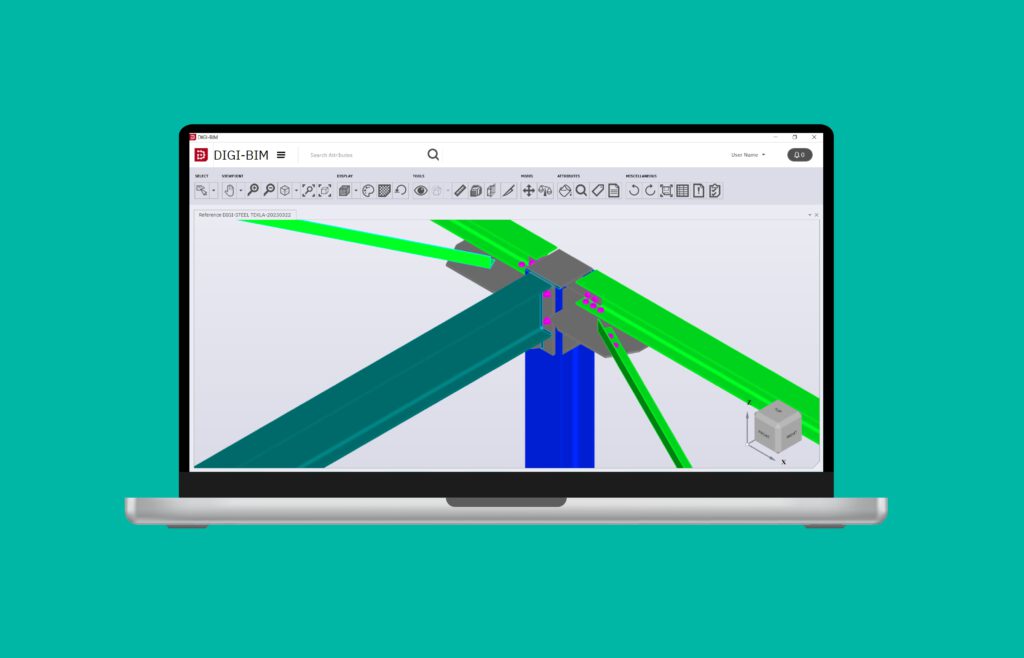
SIMPLIFY YOUR PRODUCTION TASKS WITH DIGI-WELD
EFFORTLESSLY STREAMLINE YOUR WORKFLOW WITH OUR EASY-TO-USE SOLUTION.
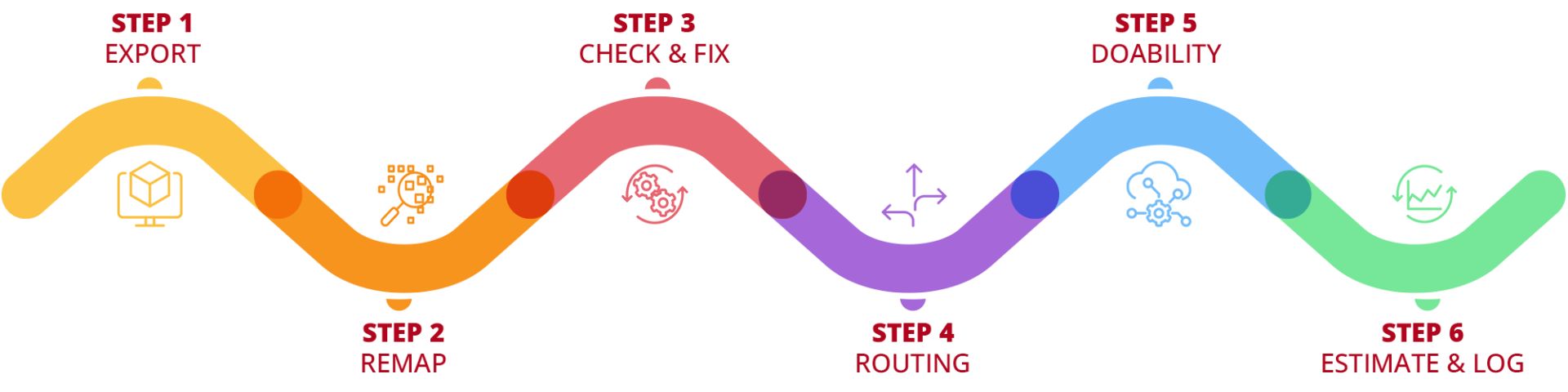
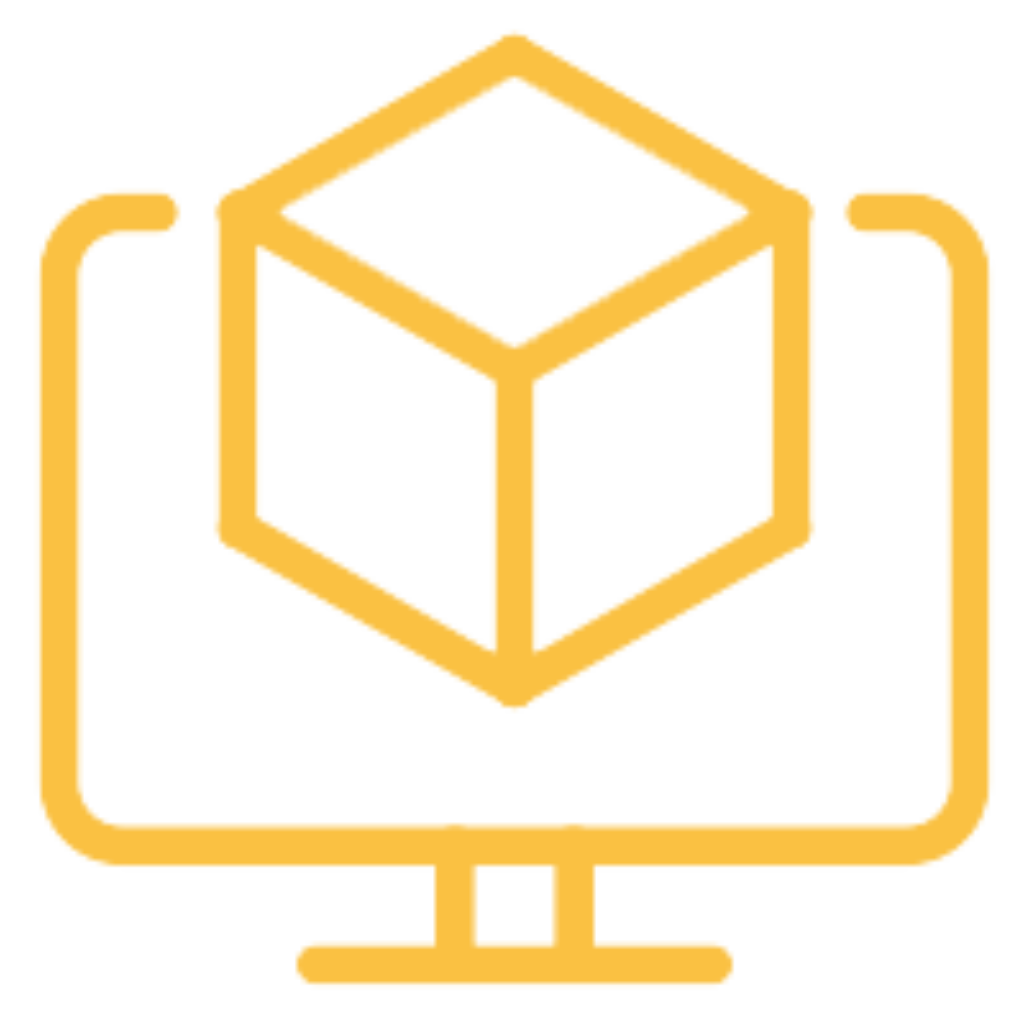
STEP 1
EFFORTLESS EXPORT OF 3-D MODELS
Our platform seamlessly integrates with Tekla using a dedicated Plugin, offering the export of models to the cloud with recognition of changes to every exported element, including Assembly, Part, weld and bolt data. This ensures you are aware of changes without the strain of manually checking.

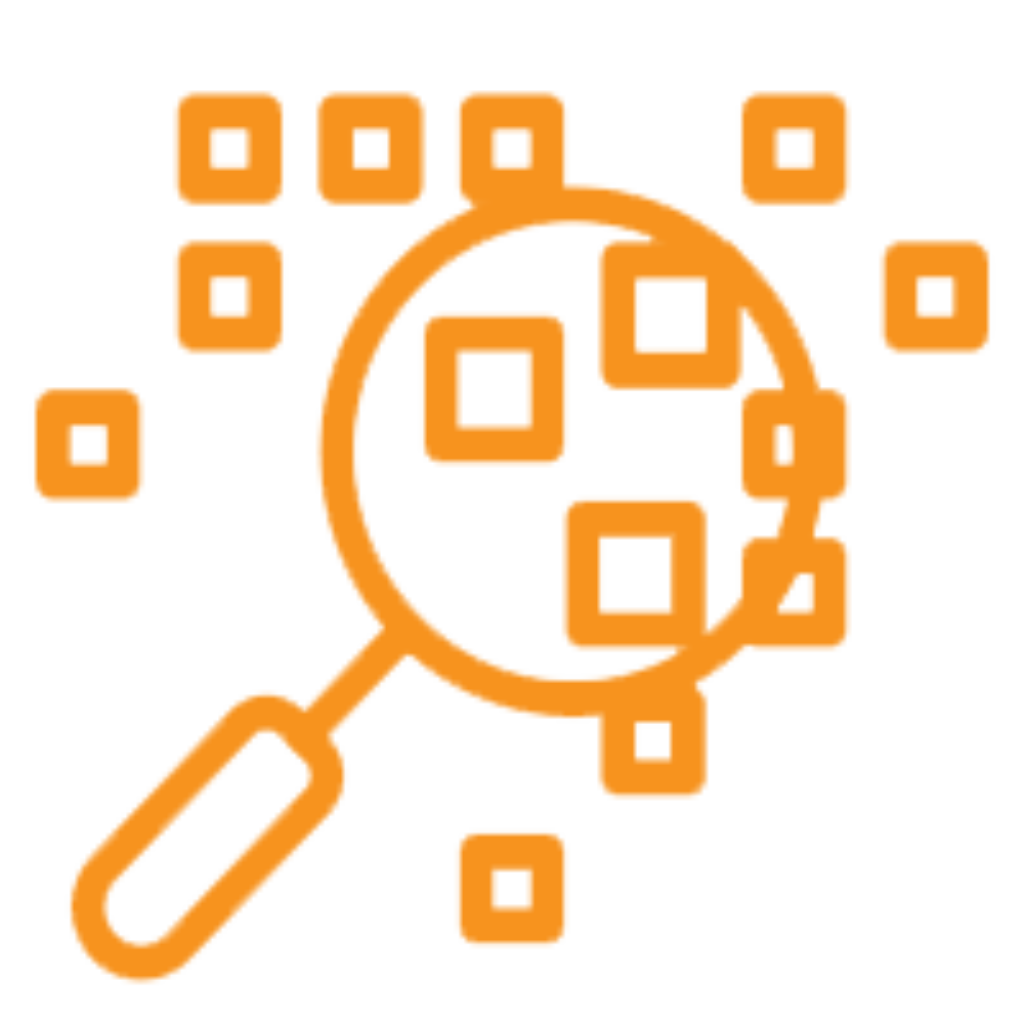
STEP 2
AUTOMATED WELD MAPPING
DIGI-WELD provides users with a visual representation of the entire 3D model. The process of model remap is operating seamlessly in the background. By utilizing configurable feasibility filters, users can quickly pinpoint and masterfully manipulate phases and assemblies that are Fabricator processing ready. It even offers advanced features such as weld restructuring and weld path generation to streamline the fabrication process.
During the remapping process, DIGI-WELD systematically restructures welds and efficiently generates weld paths for all connections throughout the model.
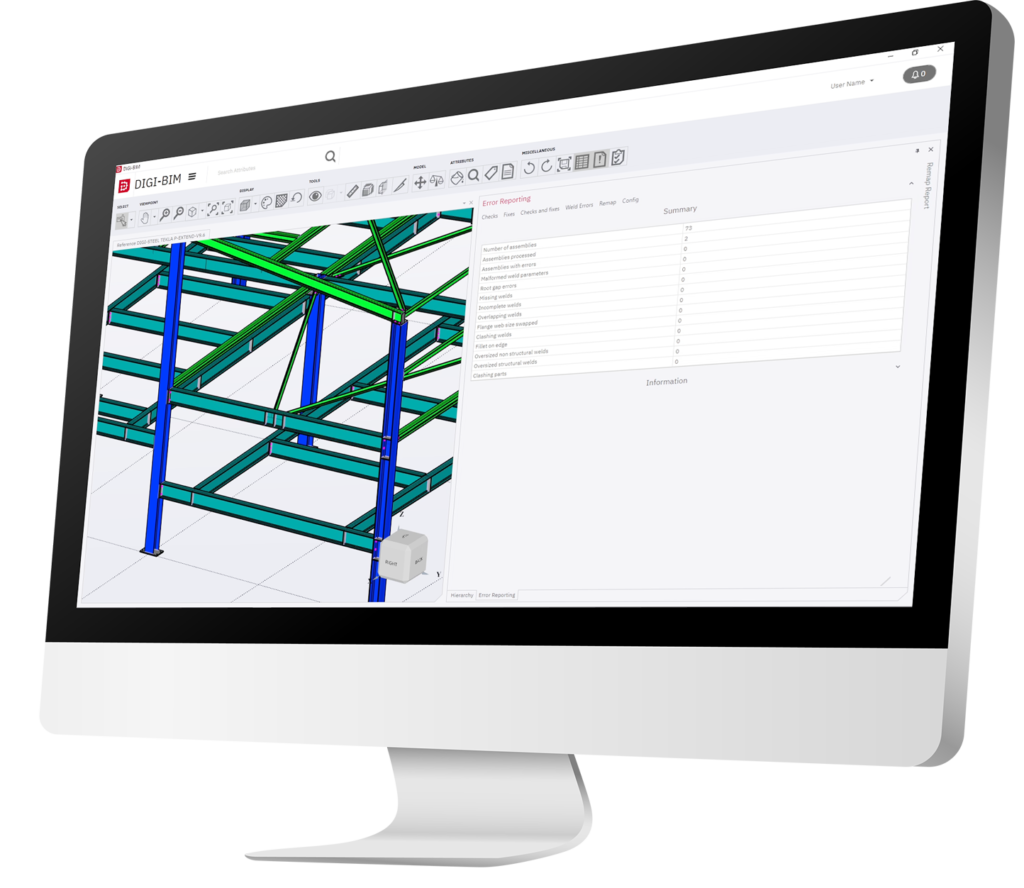
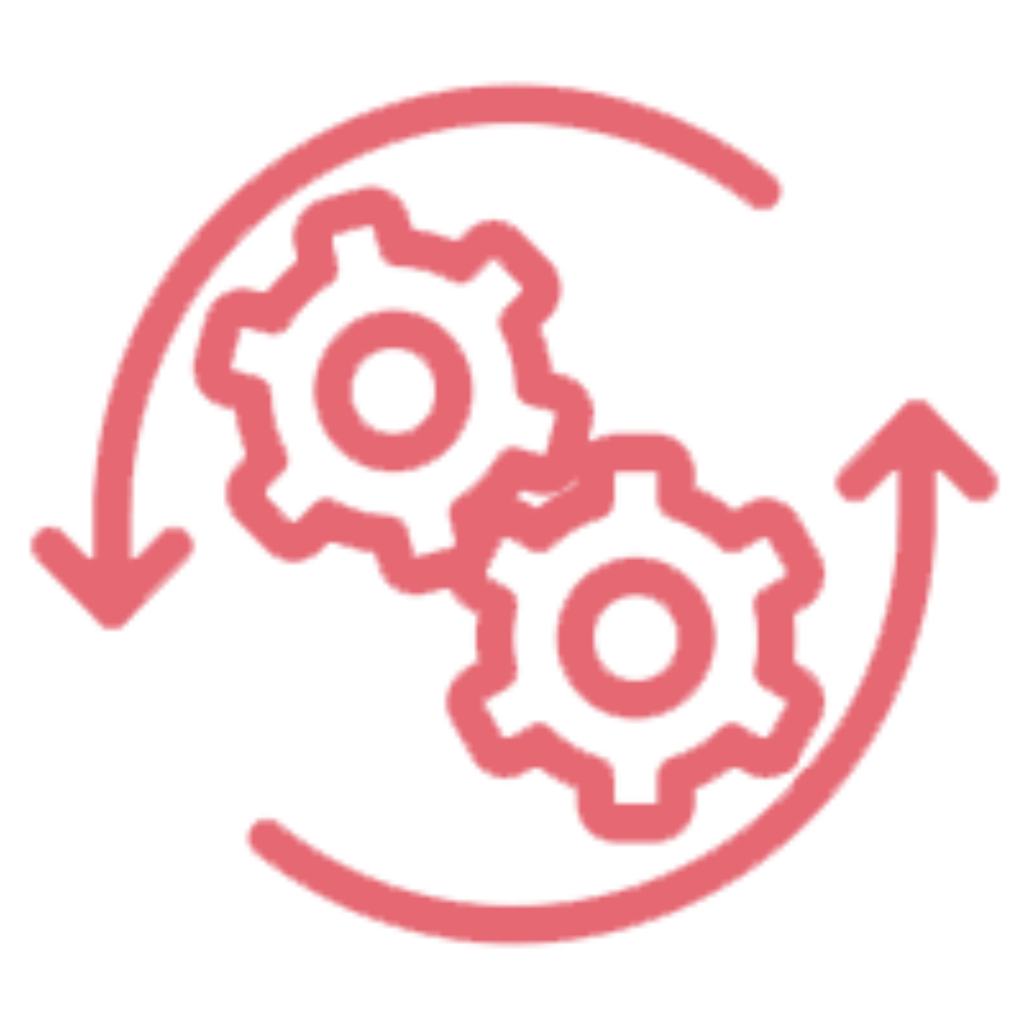
STEP 3
GET ERROR FREE MODELS
Within the DIGI-Weld cloud tool kit you can re-map the modelled welds to represent the true flow of each welds path. Automated tools are capable of detecting and correcting any mistakes in entire models all in one go. This includes missing welds, incomplete fillet or edge welds, overlapping or clashing fillet or edge welds, and overlapping or clashing ones without sufficient land coverage.
With these tools at your disposal, you can rest assured that your work will be error-free. All verification and resolution of issues are handled in a secure cloud environment. With cloud computing you gain the ultimate flexibility; all your data can be accessed from any device, anytime. Plus, important calculations are done remotely in the cloud, so you can continue within DIGI-weld without delay.
VACAM receives all data formatted in a unique Voortman format. Our innovative data format has been specifically tailored to the needs of our machines and processes. This proprietary development enables us to surpass previous limitations and maximize our full potential.
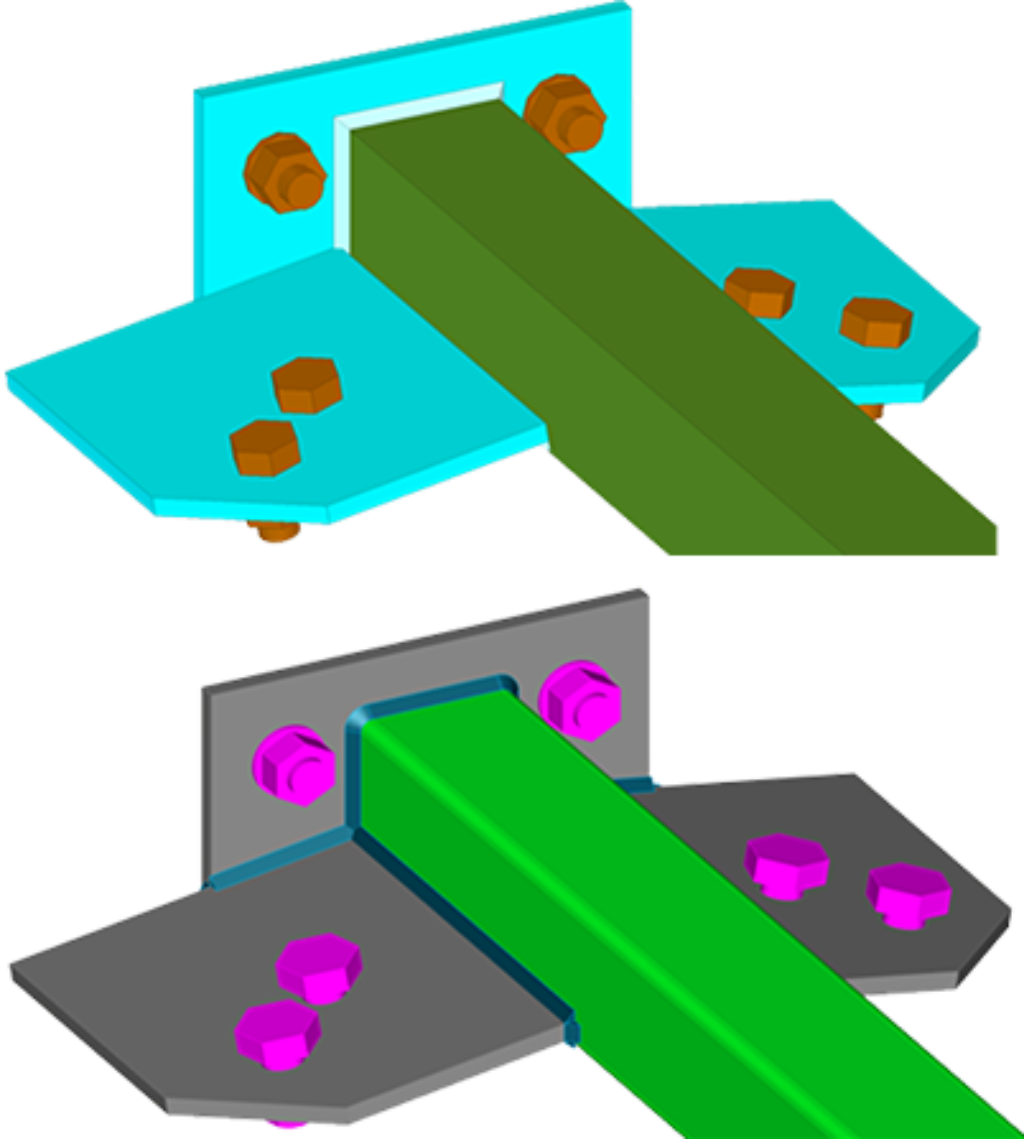
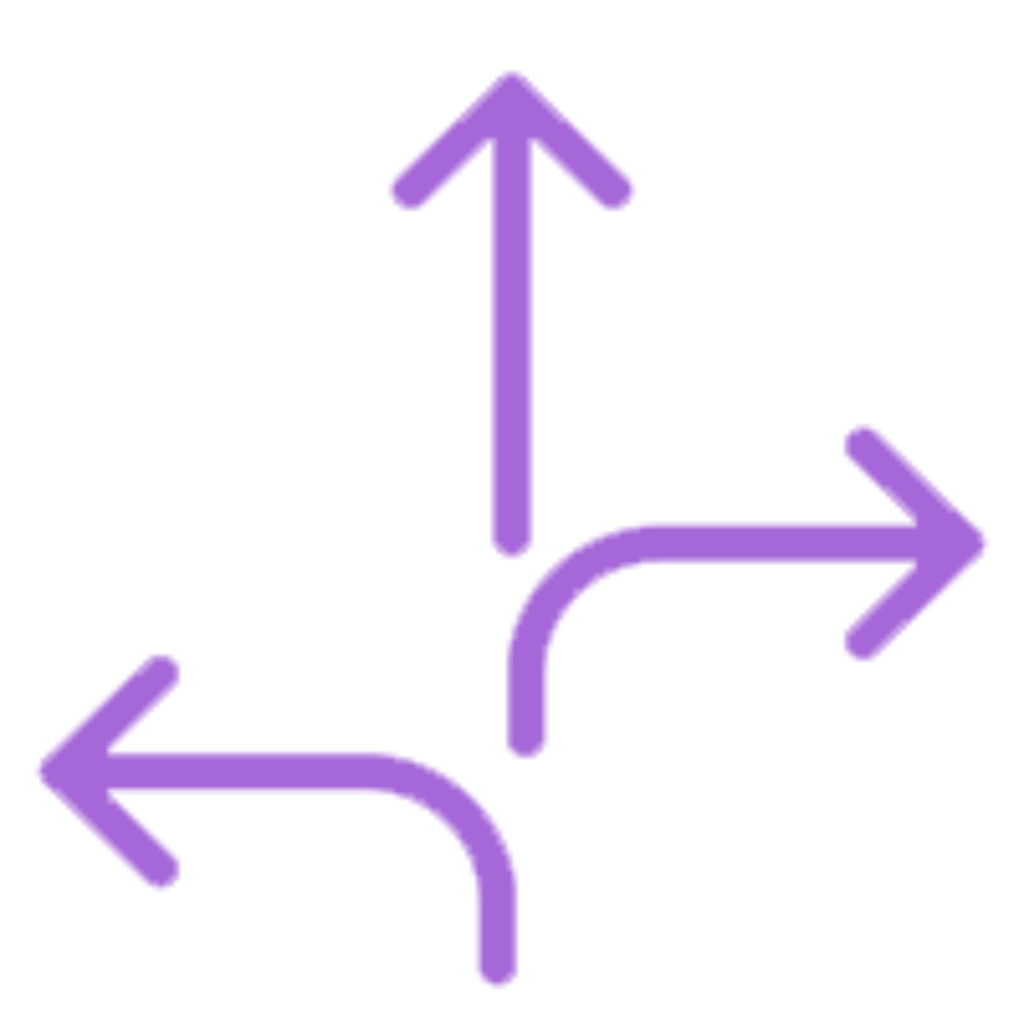
STEP 4
EVERYTHING YOU NEED IN ONE PLACE
Consider using DIGI-WELD as your one-stop distribution platform. The tool automatically verifies and repairs weld data for your entire engineering model, proving to be an optimal starting point for planning both Fabricator jobs and manual welding tasks. Combined with its user-friendly interface and comprehensive features, there is nothing to stop you from streamlining your workflows with increased efficiency and productivity.
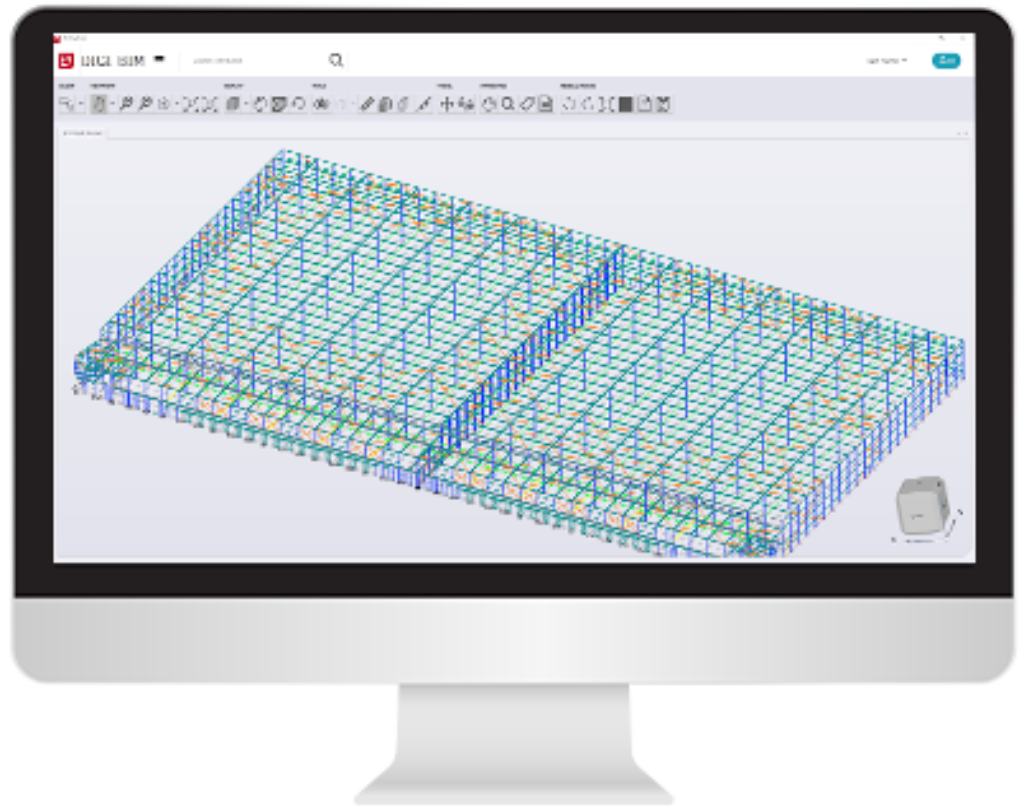
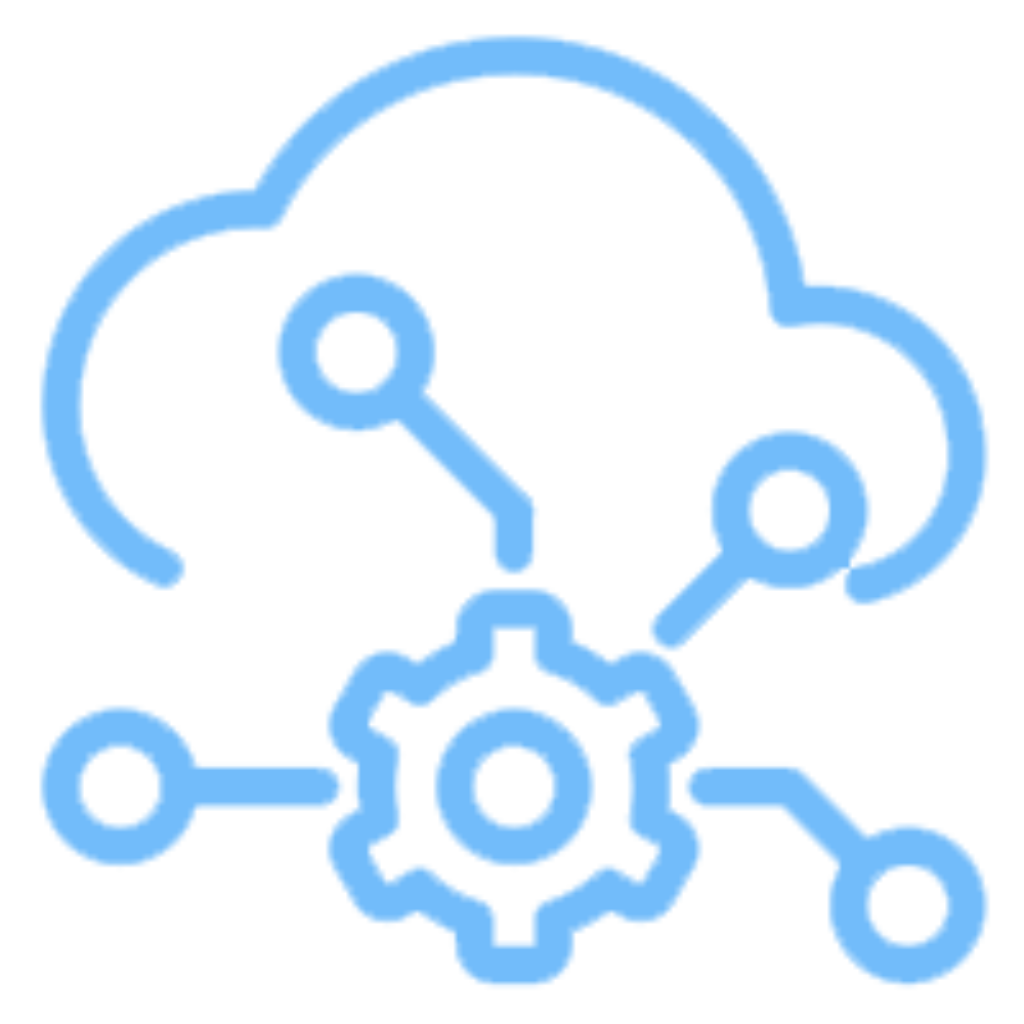
STEP 5
MAKE INFORMED DECISIONS
VACAM determines the feasibility of assemblies, production times, and more, so you can make informed decisions. It considers factors like weight, size and torch accessibility in order to determine whether a particular assembly should be fully automatically welded, partially automated or handled completely manually.
DIGI-WELD integrates smoothly with VACAM, streamlining production so that after importing from DIGI-WELD, no manual operation on the machine is necessary. This creates a seamless production pipeline, in which all you have to do is start production.
If an assembly cannot be welded fully,VACAM provides extensive, detailed information on which portions can and cannot be welded, with full explanations for each. VACAM also calculates the work sequence based on maximum efficiency while keeping the thermal formation of both the main and
sub-assemblies in mind, ensuring high quality results every time.
You don't have to worry about time loss during processing. It performs fast 270-degree rotations, so it doesn't matter which side is being processed. With these valuable resources, you can make informed decisions about how best to advance within your workshop
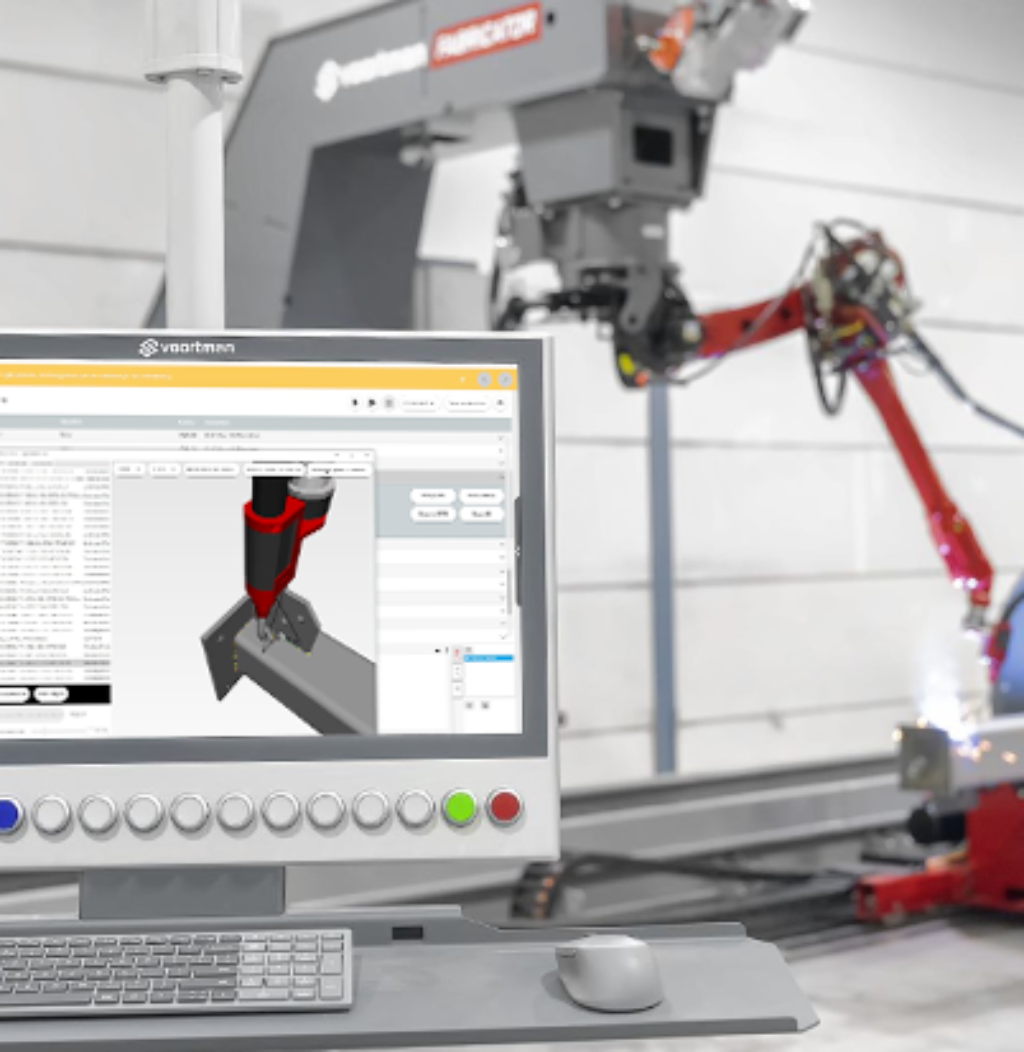
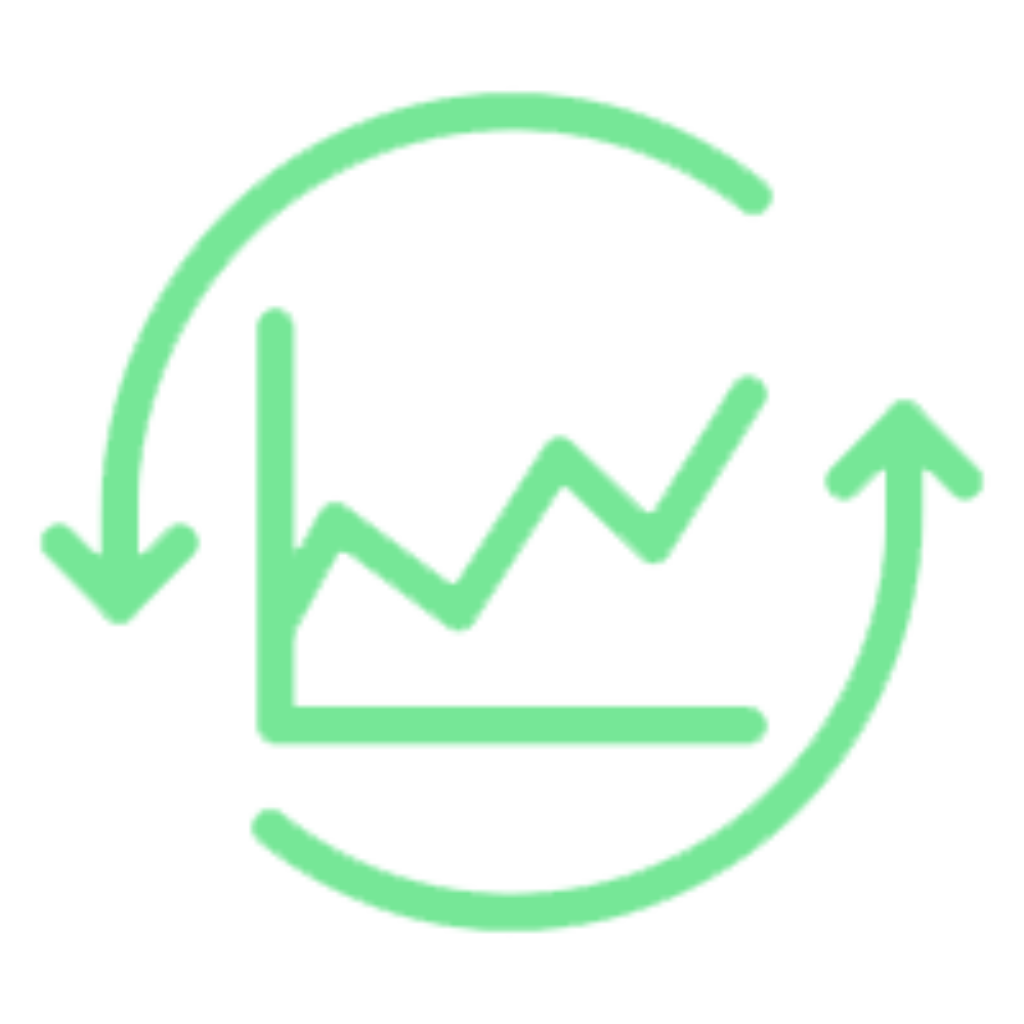
STEP 6
MAKE VALUABLE ESTIMATIONS
Time is money, and with manual estimates for complex processes like assembly and welding becoming increasingly difficult to manage, having a reliable software solution such as VACAM can really help. It assists in proper estimations while providing insightful data on production. VACAM compares empirical welding times to predicted ones and highlights lengths of all welds, complete production timelines and their respective production status updates. With VACAM, predictions become more accurate, work time more efficient, and a sharper margin for profitability can be attained.
The Fabricator is made compatible with our real-time production dashboard EVI, Extended Voortman Insights. EVI is an excellent solution to reduce production downtimes in your machines while helping to keep your productivity on track. With EVI, you gain insight into the production output, machine productivity history, and reasons for downtimes.
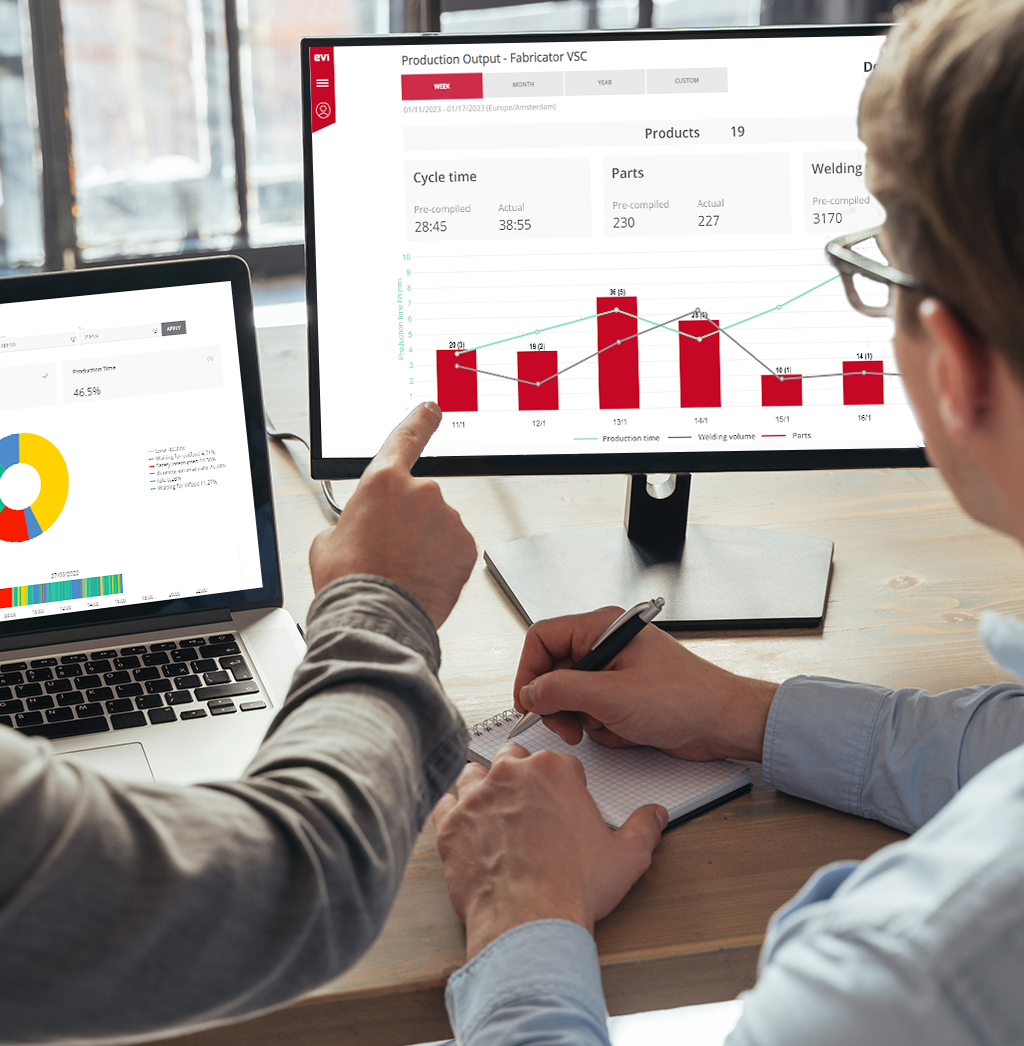
IMPORT DATA INTO FABRICATOR CONTROL FROM AN OFFICE ENVIRONMENT
WITH NO VISIBLE INTERRUPTION FOR OPERATORS RUNNING MACHINES

VALIDATE FROM THE OFFICE
Ensuring a high up-time with the Fabricator is key to achieving optimal ROI; limiting disruptions in production helps pave way for successful operation. With VACAM Office edition, work preparers can quickly import data into Fabricator control from an office environment with no visible interruption for operators running machines. The software validates imported information to guarantee everything is correct before it's processed - allowing your operator to press the button and walk away without any worries.
OPTIMIZED WELD PARAMETERS
VACAM office edition makes it easy to decide which assemblies should be produced on Fabricator. With its automated pre-check, VACAM will deliver a suitability percentage for each assembly imported and this info can even be exported and shared with external MRP software like DIGI-STEEL.
Assemblies ready for production on the Fabricator are released from VACAM Office and appear directly onto the VACAM control panel of the machine. The VACAM software ensures weld quality meets applicable standards by optimizing parameters to achieve desired results.
EXCITED ABOUT DIGI-WELD?
Simon Inman showcases how easy it is to use DIGI-WELD.
During the remapping process, Simon demonstrates DIGI-WELD's ability to efficiently restructure welds and generate weld paths for all connections in the model. The next step is the check and fix function, which utilizes automated tools to swiftly identify and correct any errors in the entire model at once. With everything accessible from the cloud, you can judge its power for yourself--try them out!
EVERY FABRICATOR SYSTEM INCLUDES HIGH END INDUSTRIAL COMPONENTS AND FEATURES:
- Industrial, 6-axis Panasonic arc welding robot
- Industrial, 6-axis Panasonic handling robot
- Single ‘One Side’ Robot track type;
- Build-in 450A welding power source type SP-Mag / Hyper Dip;
- Water cooled welding torch with quick disconnect system;
- Compressor cooling with temperature control;
- Mechanical torch cleaning unit;
- Wire Wizard package;
- Rotational positioners with hydraulic clamping. Payload up to 6.000 kg / 13.227 lbs. for 3 rotators;
- Track for (motor driven) positioners for optimal positioning and grounding;
- Automatic machine calibration;
- Automatic Tool Center Point calibration;
- Part table for positioning parts to be picked up by the handling robot;
- Complete safety according to UL /RIA;
- Autonomous weld path generation from 3-D engineering model till production;
- DIGI-WELD work preparation software
CONSISTENCY, ROUND-THE-CLOCK
Its advanced optical sensor and powerful laser line projector deliver quality control and product recognition. Next to that, it's fast rotators guarantee the most efficient assembly order, and Panasonic's controller is renowned for being the fastest and most powerful model on the market. Welding paths are automatically generated by VACAM, allowing you to automate welding processes with ease and minimal human intervention.
ELIMINATE WAITING TIMES - MAXIMIZE UPTIME AND OUTPUT
With VACAM software controlling longitudinal positioning and swift beam rotation, you'll enjoy a production flow that is faster and more efficient than ever before. Plus, the Fabricator's clamping system eliminates the need for costly re-measuring. Panasonic's welding robot revolutionizes weld quality with its lightning-fast 250 times faster communication speed. Flexible notifications will alert operators of any issue so they can quickly address it without disrupting production.
WATCH NOW!
WEBINAR | ROAD TO SMART FACTORY
Reijrink and Voortman have formed a partnership to create a win-win situation. Reijrink is now able to automate its full production process with the arrival of the Fabricator. Voortman is utilizing this opportunity as a test for their machine, collecting data to expand system possibilities and increase production capacity.
Watch and learn from the steps they have taken. How do they deal with automation? What is the impact on personnel and work preparation?
VERY FLEXIBLE
Advanced robotics handle every step of production, from fitting add-on parts to full welding. This allows manual welders and assemblers to focus their energy on higher reward projects instead of routine duties. The Fabricator's versatility also enables it to scan, assemble and weld plates of all shapes and subassemblies with minimal effort. Plus, switch tables can easily be swapped for maximum efficiency during long production runs.
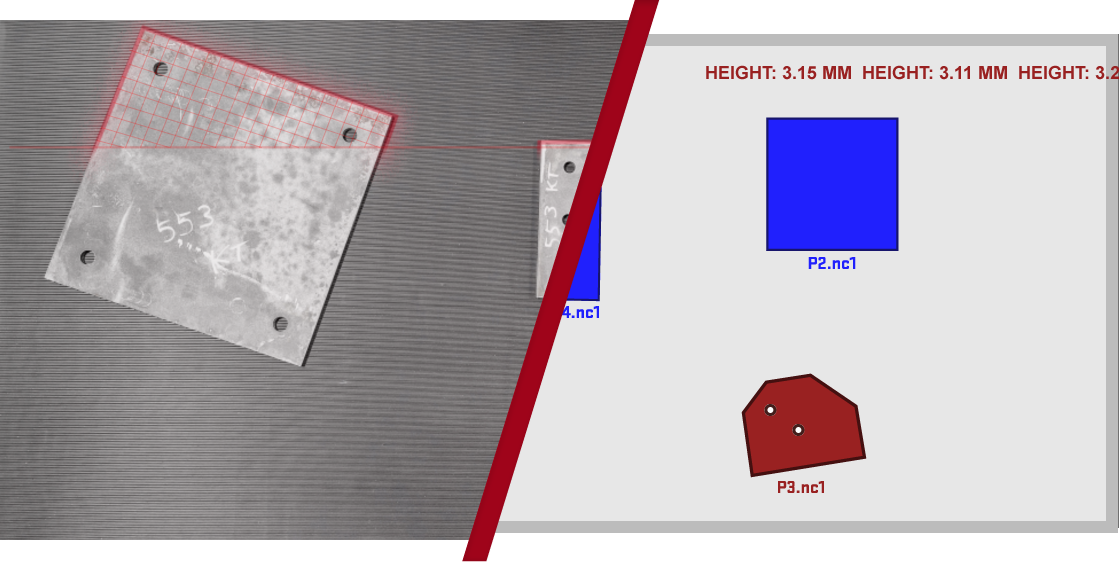
It scans for plate thicknesses, outside contours, and inside contours to ensure top-notch quality control as well as product recognition.
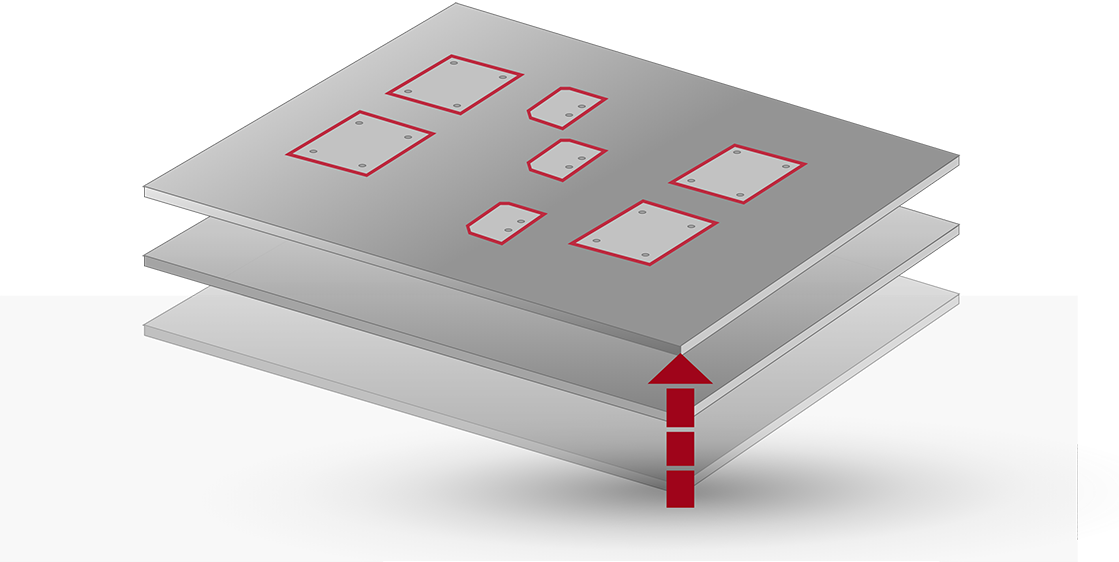
Switch tables can easily be swapped for maximum efficiency during long production runs.
MORE ON THE EXACT COMPONENTS AND FUNCTIONS
- The welding process is executed through unique integrated combination of robot, robot control, servo wire feed, and power source.
- The robot securely holds the weld torch and precisely performs each weld with accuracy.
- The
robot controller receives the specified weld paths from VACAM and translates
them into precise movements of the robot's axes, allowing for a smooth
transition between welding operations.
- The
welding source generates the precisely calibrated current and voltage that is
needed for a reliable welding result.
- A
transformer is used to convert the main supply voltage and frequency to the
appropriate values for powering the welding source and robot controller.
- During
the welding process, heat is partially absorbed by the torch, which is then
cooled by a cooling unit.
- A
Wire Wizard system utilizes wire cables, pneumatic feed assist, and the wire
guide modules to ensure a frictionless transport of the welding wire.
- A
mechanical cleaner ensures automated cleaning of the welding torch.
ENJOY THE EASE OF USE
Eliminate complex programming and training by using self-calibrating robots and automatic measurements, while its small footprint allows it to fit into any space. The Fabricator also offers a hassle-free loading process with laser guidance, so operators can stay in their vehicles. Plus, its rotators are easy to maintain for increased reliability and maximum uptime.
Specifications
Voortman Fabricator | ||
---|---|---|
Voortman Fabricator | ||
Profile types main section | H, I, U & Rectangular Tubes | |
Max. beam height | inch | 24” |
Min. beam height | inch | 3 5/32” |
Max. beam width | inch | 16 ¾" |
Min. beam width | inch | 3 5/32 |
Max. profile length | ft | 40 / 60 / 80 |
Min. profile length | ft/inch | 8,5 |
Max. assembly weight | lbs | 13.227 |
Secondary parts | Plates, Angle (L), RHS/SHS, T, I/H, U, Welded T's | |
Max. payload handling robot | lbs | 400 |
Max. weld size per layer | inch | 5/16 |
Height gantry | ft | 11,5 |