Rewolucja w produkcji sprzętu do recyklingu
Sukces firmy Bollegraaf dzięki Voortman V310
Referencje Bollegraaf Recycling Solutions
- Lokalizacja:
- Personel:
- Zainstalowane systemy recyklingu:
- Maszyna:
- Appingedam, Holandia
- 300
- +4.000
- Voortman V310
"Zdolność V310 do wiercenia i gwintowania około 300 otworów na prasę, co wcześniej wymagało pracochłonnej pracy ręcznej, pozwala nam teraz zaoszczędzić imponujące 3,5 dnia czasu budowy na prasę".
SKOK WYDAJNOŚCI DZIĘKI VOORTMAN V310
Od ponad sześciu dekad Bollegraaf Recycling Solutions jest jednym z liderów w dziedzinie instalacji sprzętu do recyklingu, tworząc rozwiązania, które przekształcają dzisiejsze odpady w zasoby jutra. Z zespołem 300 profesjonalistów rozmieszczonych w różnych lokalizacjach, chodzi o innowacje, zrównoważony rozwój i wywieranie wpływu na sposób, w jaki świat poddaje się recyklingowi. Ich specjalność? Tworzenie wydajnych i imponujących dużych belownic.
"Naprawdę powinniśmy byli to zrobić dużo wcześniej!" - wyjaśnił z entuzjazmem Pascall de Boer - kierownik zespołu programowania CNC w Bollegraaf. Odnosił się do zakupu maszyny do wiercenia i cięcia blach Voortman V310 ze stołem do cięcia o długości 24 metrów. To wręcz niewiarygodne, że niecałe cztery lata temu wszystkie znakowania, wiercenia i gwintowania wykonywali ręcznie. Oczywiście zaangażowanie w rzemiosło było obecne, ale czas, jaki to zajmowało, był ogromny.
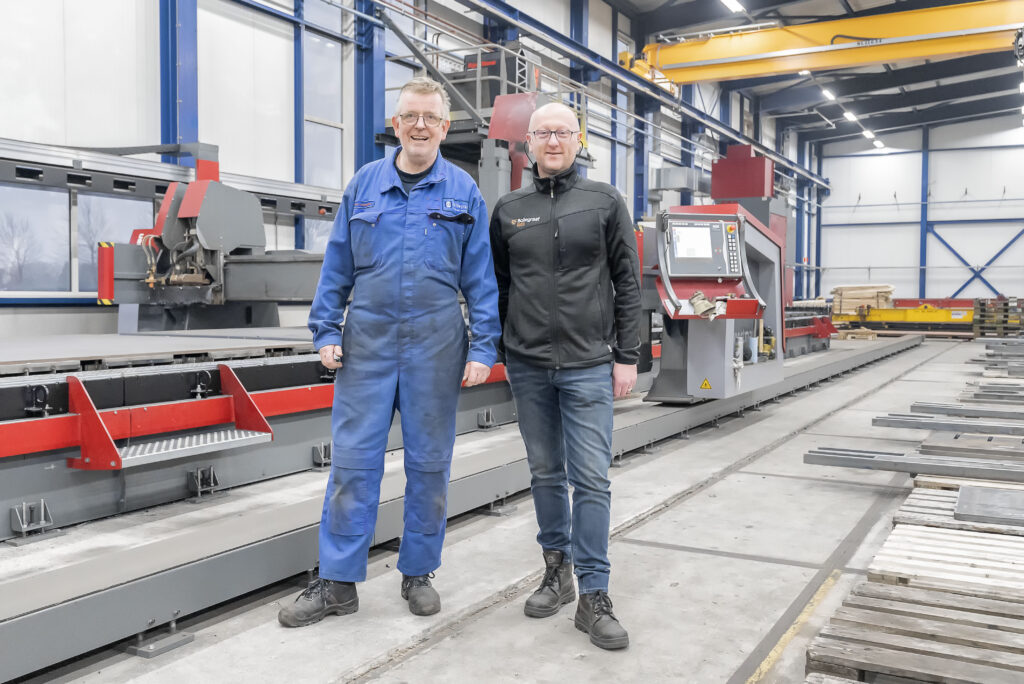
AUTOMATYZACJA: CAŁKOWITA ZMIANA ZASAD GRY
Pascall na własnej skórze doświadczył przejścia z przetwarzania ręcznego na automatyzację. Maszyna V310 szybko okazała się przełomem, zmieniając sposób działania firmy Bollegraaf, znacznie zwiększając jej wydajność i produktywność. "Zdolność V310 do wiercenia i gwintowania około 300 otworów na prasę, co wcześniej wymagało pracochłonnej pracy ręcznej, pozwala nam teraz zaoszczędzić imponujące 3,5 dnia czasu budowy na prasę".
Oprócz automatyzacji wiercenia, maszyna wiercąca płynnie obsługuje również znakowanie tekstu i lokalizacji. "W przeszłości wszystko było znakowane ręcznie, a teraz wszystko po prostu spływa z maszyny, gotowe do pracy". Oszczędza to Bollegraafowi wiele czasu w dziale konstrukcyjnym i zapewnia precyzję, której nie można osiągnąć metodami ręcznymi.
Co więcej, głowica do cięcia pod skosem 3D maszyny znacznie poprawia precyzję, umożliwiając punktowe cięcie pod skosem bez konieczności programowania lub wiedzy operatora. "Maszyna działa w pełni automatycznie. Po skonfigurowaniu w SigmaNEST, maszyna przejmuje dane i działa płynnie. Łatwizna!"
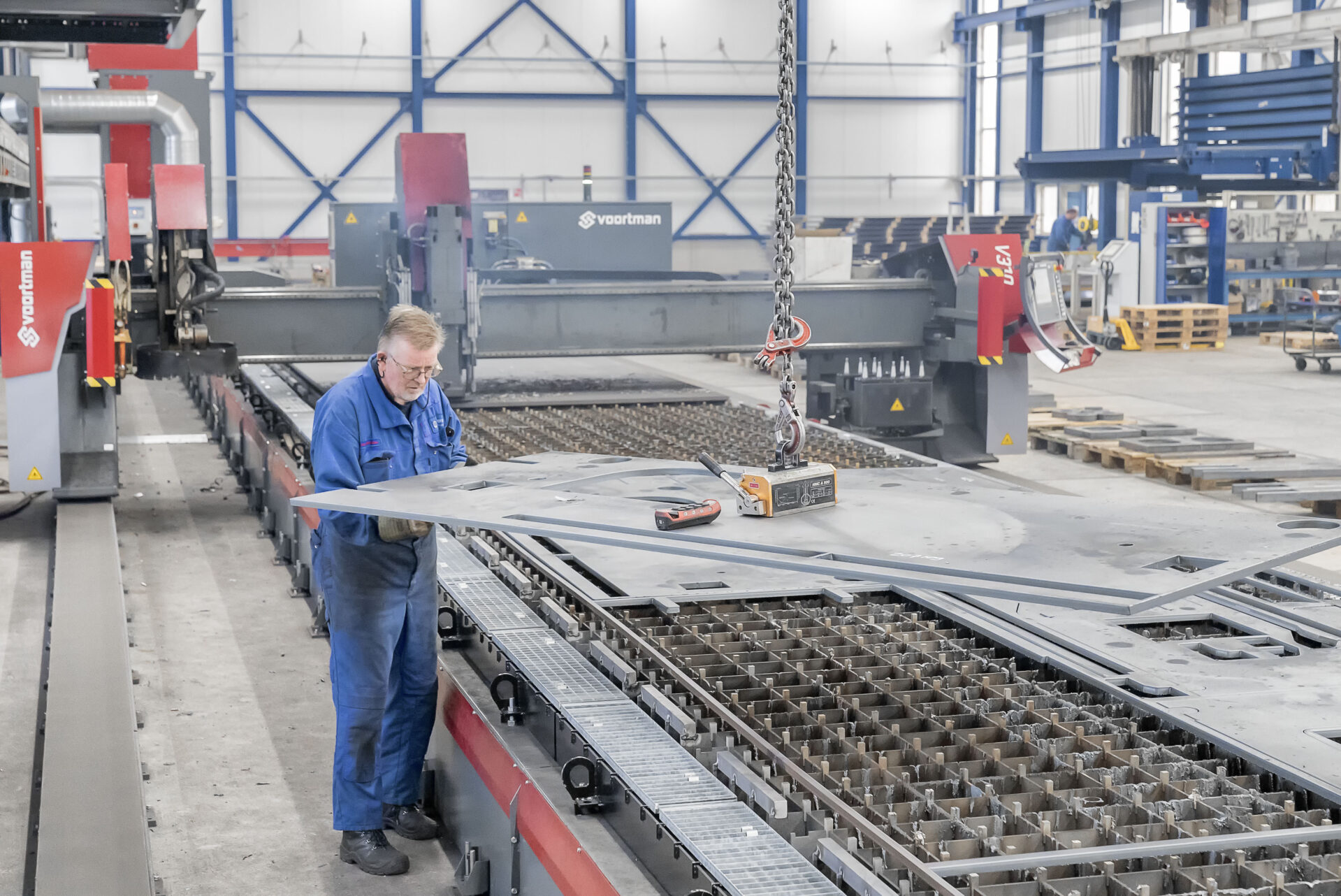
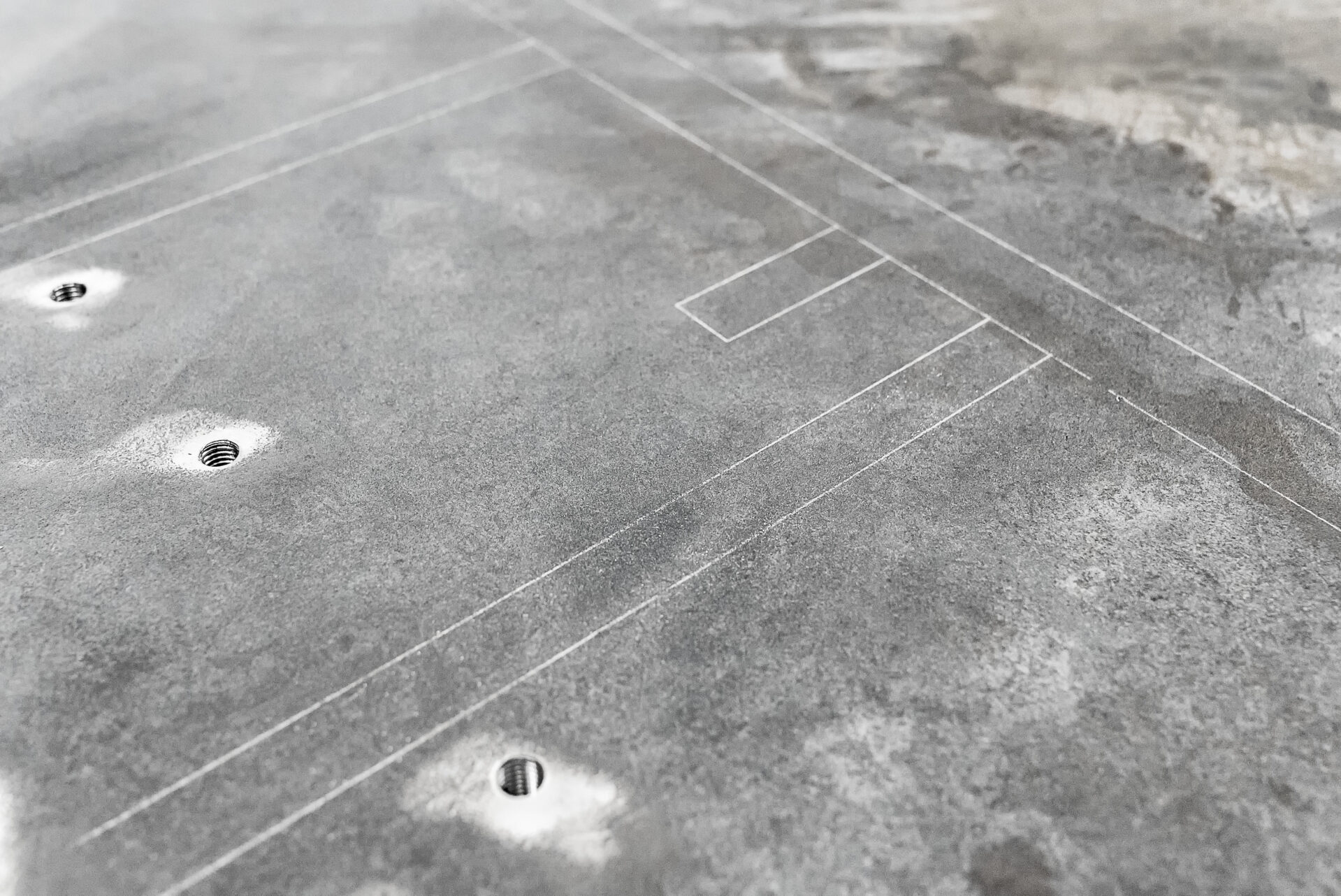
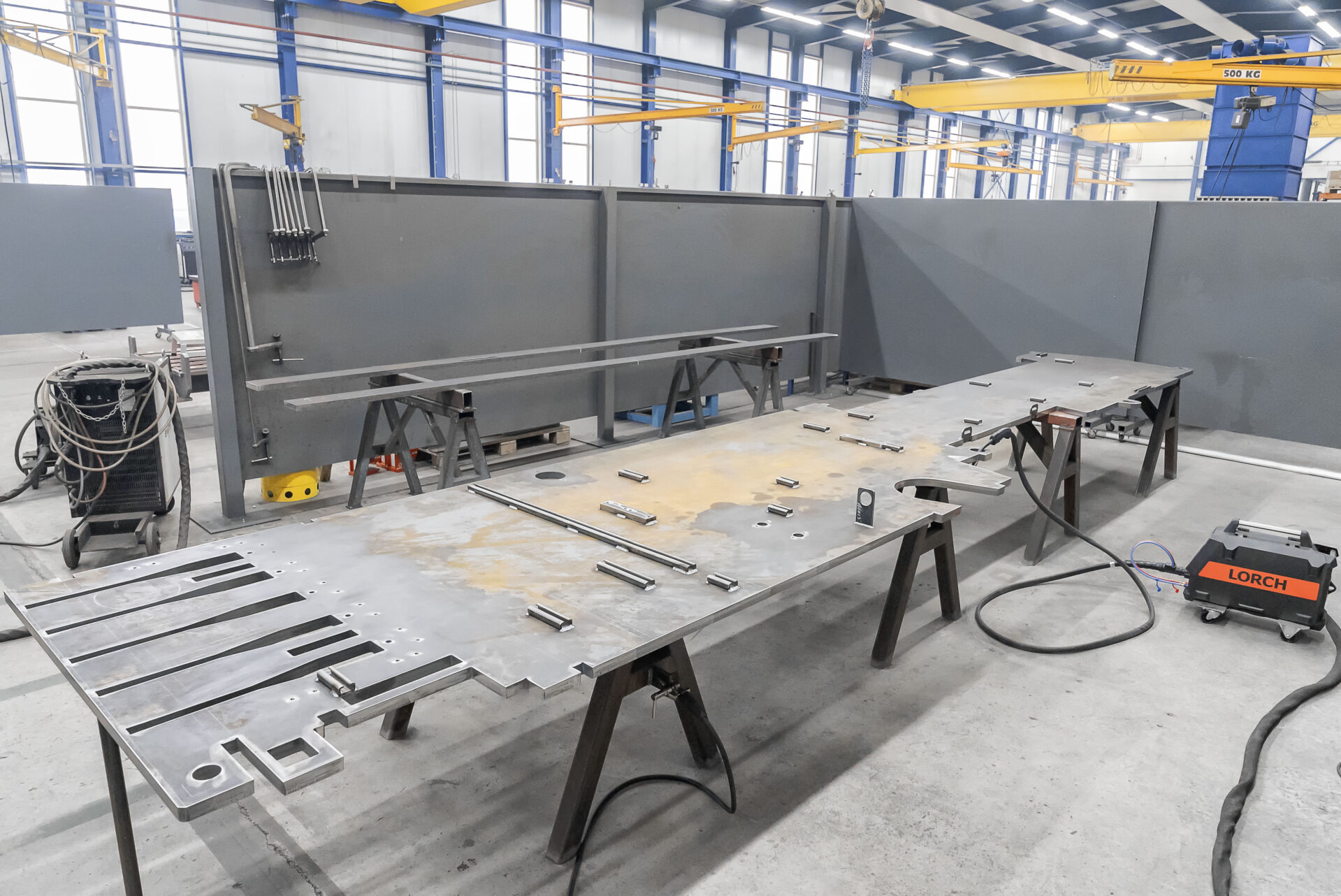
Załadunek i rozładunek blach może być wykonywany, gdy maszyna nadal przetwarza części w innej sekcji stołu.
V310 automatycznie wykonuje wysokiej jakości nawiercone i gwintowane otwory wraz z precyzyjnym trasowaniem układu pod blachy.
Część ramy prasy została zmontowana, z trasowaniem układu pod blachy prowadzącym do umieszczenia części.
PRECYZJA NA ŻĄDANIE: OPANOWANIE JUST-IN-TIME I FIRST-TIME-RIGHT
V310 to przede wszystkim tworzenie najwyższej jakości części z idealnymi nacięciami i otworami, dzięki czemu wszystko jest dokładnie zmontowane. Oznacza to mniej błędów, mniej poprawek podczas montażu. I to jest dokładnie to, czego chcą, ponieważ dążą do produkcji "First-Time-Right". Eliminuje to potrzebę testowania produktów i zapobiega zwrotom wadliwych części.
Takie podejście doskonale wpisuje się w ich strategię produkcji "Just-In-Time". Pomijają zapasy i dostarczają produkty dokładnie wtedy, gdy zespół montażowy potrzebuje ich do realizacji konkretnego zamówienia klienta.
I zgadnij co? Popyt ze strony klientów wciąż rośnie...
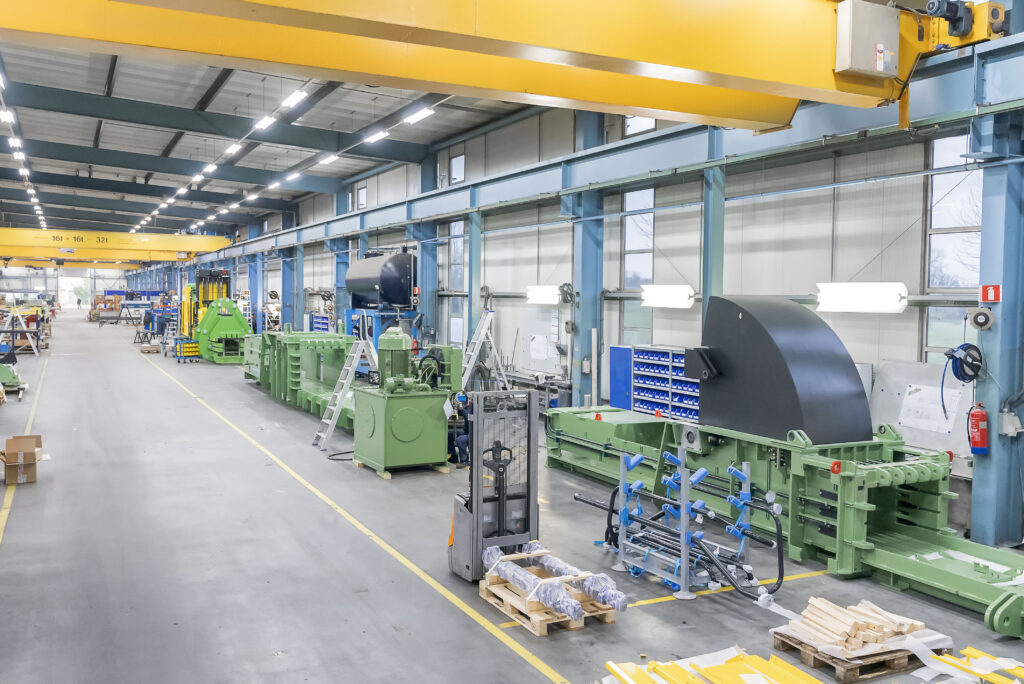

SEKRET PŁYNNEGO I SKUTECZNEGO PRZECHODZENIA Z JEDNEJ PRACY DO DRUGIEJ
Decyzja firmy o zastosowaniu 24-metrowego stołu tnącego, zdolnego do załadunku dwóch podstawowych rozmiarów blach do belownicy (13 metrów i 8 metrów), ułatwia nieprzerwaną pracę i zwiększenie dziennej wydajności. Maszyna przełącza się między blachami jak profesjonalista, bez przestojów! Pracując samodzielnie przez 8 godzin, przecina blachy o grubości od 15 do 60 mm, wykorzystując zarówno paliwo tlenowe, jak i cięcie plazmowe.
Cennym dodatkiem było wprowadzenie dodatkowego 20-częściowego zmieniacza narzędzi, opracowanego we współpracy z Voortman, który jest dodawany do standardowych 10 narzędzi w maszynie. "W prasie jest wiele różnych średnic otworów, których nie chcielibyśmy wymieniać ręcznie". Ręczna wymiana narzędzi i potencjalne przestoje są teraz zminimalizowane, a przejście od zadania do zadania przebiega płynnie.
BEZZAŁOGOWY BIEG Z MASZYNĄ, KTÓRA NIGDY NIE ŚPI
Bezzałogowe operacje znajdują się w centrum uwagi dzięki maszynie, która działa przez całą dobę bez odpoczynku. "Staramy się zmaksymalizować naszą wydajność, wykorzystując pełny potencjał maszyny, nawet poza normalnymi godzinami pracy". Unikalna funkcja wydmuchiwania wiórów, ponownie opracowana we współpracy z Voortman, usuwa wióry i zanieczyszczenia, umożliwiając wiercenie, gwintowanie i znakowanie bez nadzoru człowieka. "Ty możesz wiercić i gwintować po godzinach pracy, a następnie wznowić cięcie rano jednym naciśnięciem przycisku".
ŁATWA PRACA NA HALI PRODUKCYJNEJ
Praca na hali produkcyjnej to pestka! Niska szyna - X ułatwia pracę operatorom maszyn, bez konieczności pokonywania wysokich stopni. To znacząca poprawa w stosunku do poprzedniego modelu, który wymagał więcej wysiłku i stwarzał zagrożenie dla bezpieczeństwa.
Funkcja Kolor Rozładunku dodatkowo usprawnia przepływ pracy, zapewniając wizualną informację zwrotną o tym, które części należą do danego zamówienia i identyfikując wadliwe części na wczesnym etapie przetwarzania. "Na hali produkcyjnej operatorzy mogą oznaczać nieprawidłowe części, automatycznie uruchamiając nowe zagnieżdżenie w celu odtworzenia części". Informacje zwrotne w czasie rzeczywistym na temat stanu narzędzi i szczegółów zadania pomagają operatorom w efektywnym planowaniu i konserwacji. "Wyświetlanie czasów przetwarzania dla każdego zagnieżdżenia bezpośrednio na maszynie upraszcza planowanie, umożliwiając operatorom nadawanie priorytetów zadaniom w celu uzyskania optymalnej wydajności i wykorzystania maszyny".
RAZEM DO PRZODU: PARTNERSTWO OPARTE NA PRZYSZŁOŚCIOWYM MYŚLENIU I ZAUFANIU
Wybór Voortman był czymś więcej niż tylko maszyną; chodziło o partnerstwo. Bollegraaf odbył obszerną wycieczkę po siedzibie Voortman, a bardzo złożone kształty zostały wycięte jako produkty testowe. Ten test przeszedł śpiewająco, ale lokalna obecność Voortman i poczucie więzi odczuwane przez zespół odróżniały Voortman od innych. "Wszyscy mieliśmy wrażenie, że mamy do czynienia z bratem lub siostrą, jeśli chodzi o firmę. Po prostu idealnie do siebie pasowaliśmy". Poza oczywistymi korzyściami logistycznymi i kulturowymi, Voortman wyróżniał się jakością usług. "Obsługa jest doskonała. Wystarczy jeden telefon i masz natychmiastową odpowiedź. Planowanie jest również zawsze w porządku. Słowo jest słowem. Czyn to czyn".
Maszyna V310 naprawdę zmieniła proces przetwarzania w firmie Bollegraaf. Mniej pracy ręcznej, większa precyzja i najwyższa jakość pras. Ich inwestycja pokazuje, jak bardzo są oddani innowacjom i wydajności, utrzymując Bollegraaf w czołówce branży sprzętu do recyklingu.
