Voortman MO Classic
Wszechstronna i bardzo dokładna przecinarka do rur o skomplikowanych kształtach i średnicy do 2000 mm
- Wszechstronna i bardzo dokładna przecinarka do rur
- Wiele procesów z plazmą i tlenem
- Rury okrągłe o średnicy do 2000 mm / 80", rury o przekroju kwadratowym i prostokątnym do 640 x 640 mm, głowice zbiorników do 2000 mm / 80"
- Wyposażona w 6 lub 7 sterowanych numerycznie osi. Dodanie opcjonalnej 7. osi CNC umożliwia cięcie rur kwadratowych i prostokątnych
- 3-wymiarowe cięcie wykonywane z użyciem plazmy i tlenu
WPROWADZENIE
Maszyna Voortman MO Classic jest przeznaczona do precyzyjnego, 3-wymiarowego profilowania rur o dużej średnicy do 2000 mm. Precyzyjne i powtarzalne działanie maszyny jest możliwe dzięki sześciu sterowanym numerycznie osiom i zaawansowanej technologii cięcia. Nawet w trudnych warunkach. Maszyna jest przeznaczona do takich branż, jak offshore, budownictwo okrętowe i stal konstrukcyjna i zapewnia wydajność oraz niezawodność w produkcji ciężkiej. Model MO Classic jest gotowy na każde wyzwanie. Uniwersalność. Wydajność. Trwała konstrukcja.
6 OSI PRZETWARZAJĄCYCH
EFEKTYWNOŚĆ I WSZECHSTRONNOŚĆ
KOMPAKTOWA KONSTRUKCJA
WYSOKA JAKOŚĆ I NIEZAWODNOŚĆ
CLASSIC SERIES
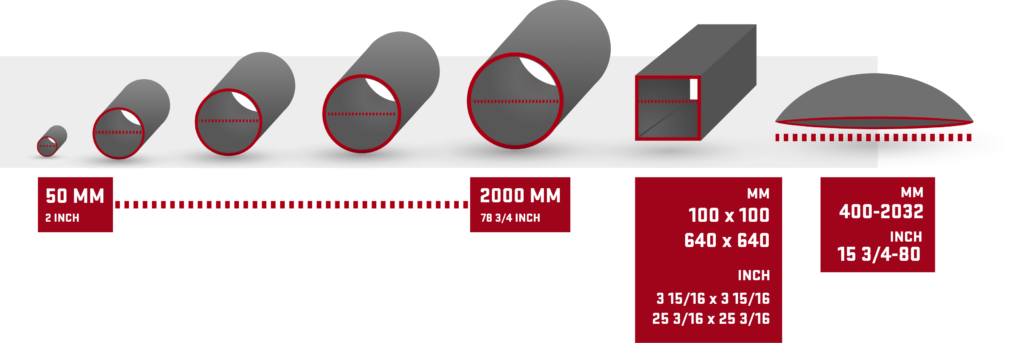
NAJWAŻNIEJSZE KORZYŚCI
WYJĄTKOWA DOKŁADNOŚĆ
DOŚWIADCZENIE KLIENTA
''Maszyna MO firmy Voortman oferowała poziom precyzji i automatyzacji, którego szukaliśmy, umożliwiając nam obsługę zarówno krótkich segmentów, jak i złożonych kształtów bez dodatkowej obróbki''
Robert van Kaam - Dyrektor CCI
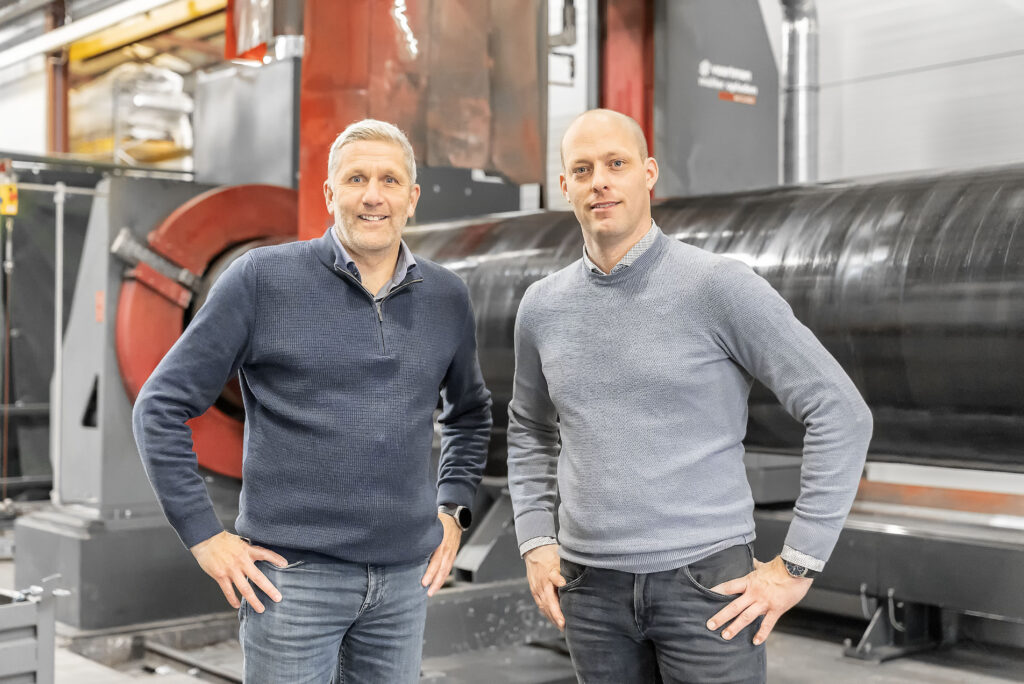
ZOPTYMALIZOWANA LOGISTYKA, PROSTSZA OBSŁUGA
I WIĘKSZA WYDAJNOŚĆ DZIĘKI AUTOMATYZACJI
Nasze zautomatyzowane systemy logistyczne są wyposażone w stojaki podające, przenośniki podające, przenośniki tnące, przenośniki odprowadzające i stojaki odprowadzające, które zapewniają optymalną wydajność procesu. Do zalet naszych systemów należy łatwość obsługi rur oraz wzrost wydajności nawet o 30%.
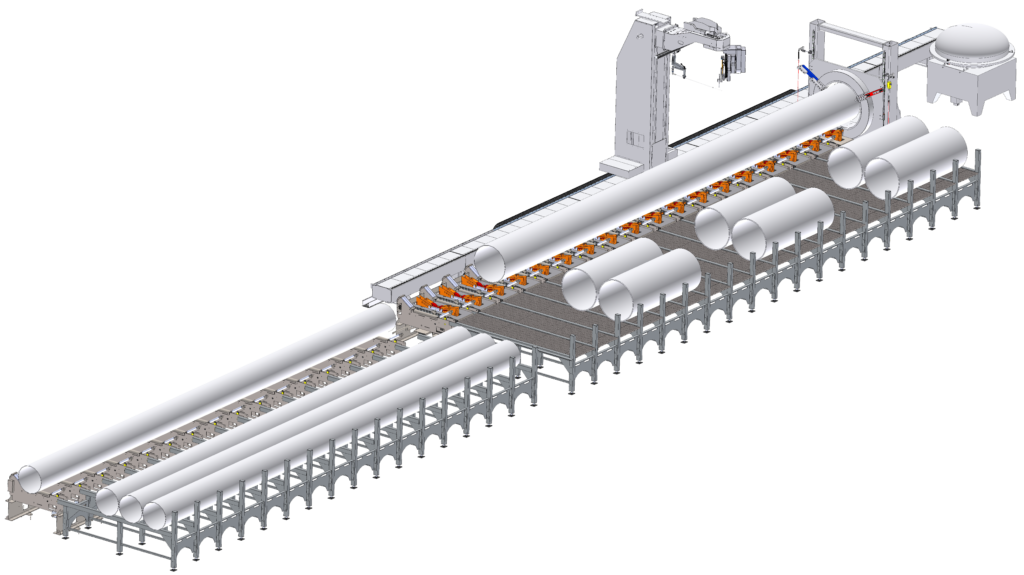
DANE TECHNICZNE
Voortman MO Classic Series | ||||
---|---|---|---|---|
1200 | 1500 | 2000 | ||
Masa maszyny standardowej | lbs | 19841.6 | 24250.85 | 28660.09 |
Liczba osi CNC | Liczba | 6-7 | 6-7 | 6-7 |
Maks. masa przedmiotu obrabianego | lbs | 26455.47 | 33069.34 | 44092.45 |
Min.–maks. zaciskana średnica okrągłej rury | inch | 2 - 48 | 3 1/8 - 60 | 3 1/8 - 80 |
Maks. wielkość otworu w uchwycie | inch | 25 9/16 | 25 9/16 | 37 3/8 |
Min.–maks. wymiary zaciskanych rur kwadratowych i prostokątnych | inch | 3 15/16 x 3 15/16 / 16 9/16 x 16 9/16 | 3 15/16 x 3 15/16 / 25 3/16 x 25 3/16 | 3 15/16 x 3 15/16 / 25 3/16 x 25 3/16 |
Min.–maks. długość przedmiotu obrabianego | inch | 11 13/16 - 944 7/8 | 11 13/16 - 944 7/8 | 11 13/16 - 944 7/8 |
Min.–maks. grubość ścianki do cięcia tlenem/plazmą | inch | 3/16 - 5 15/16 / 1/16 - 3 1/8 | 3/16 - 5 15/16 / 1/16 - 3 1/8 | 3/16 - 5 15/16 / 1/16 - 3 1/8 |
Maks. kąt palnika | ° | +/- 70 / 45 | +/- 70 / 45 | +/- 70 / 45 |