ELASTYCZNE CIĘCIE I ZNAKOWANIE BLACH
Kompaktowa budowa
Szukasz kompaktowej, ale elastycznej maszyny do cięcia i znakowania blach, która oferuje wiele przemyślanych funkcji? Przedstawiamy maszyny Voortman V303 i V304. Te bliźniacze maszyny oferują identyczne funkcje i korzyści, ale z jednym kluczowym wyróżnikiem: V304 umożliwia wielopalnikowe cięcie tlenowe, wykorzystując od 3 do 6 palników.
Oba urządzenia są wyposażone w oprogramowanie VACAM wyższego poziomu, które automatyzuje proces produkcji blach i zapewnia dostęp w czasie rzeczywistym do informacji zwrotnych. Dzięki największemu panelowi dotykowemu na rynku i łatwemu w obsłudze interfejsowi operatorzy mogą bez wysiłku poruszać się po całej procedurze cięcia. Skupiamy się na zapewnieniu wyjątkowej jakości przy jednoczesnym minimalizowaniu interwencji ręcznych, zapewniając maksymalną wydajność. Dzięki „Xtensive Bevel Cutting Technology” nawet najbardziej skomplikowane cięcia kątowe są teraz w pełni zautomatyzowane, eliminując ręczne korekty czy wstępne cięcie, oszczędzając czas i wysiłek. To tylko niektóre z wielu zalet modeli V303 i V304. Przewiń dalej, aby poznać jeszcze więcej niezwykłych możliwości!
POZNAJ OFERTĘ MASZYN Z RUCHOMYM PORTALEM
Voortman przedstawia zróżnicowany wybór maszyn do obróbki blach z ruchomym portalem, zaprojektowanych z myślą o spełnieniu różnorodnych wymagań produkcyjnych. Poznaj ofertę, porównaj wspierane procesy i wybierz idealną maszynę do realizacji własnych celów produkcyjnych.
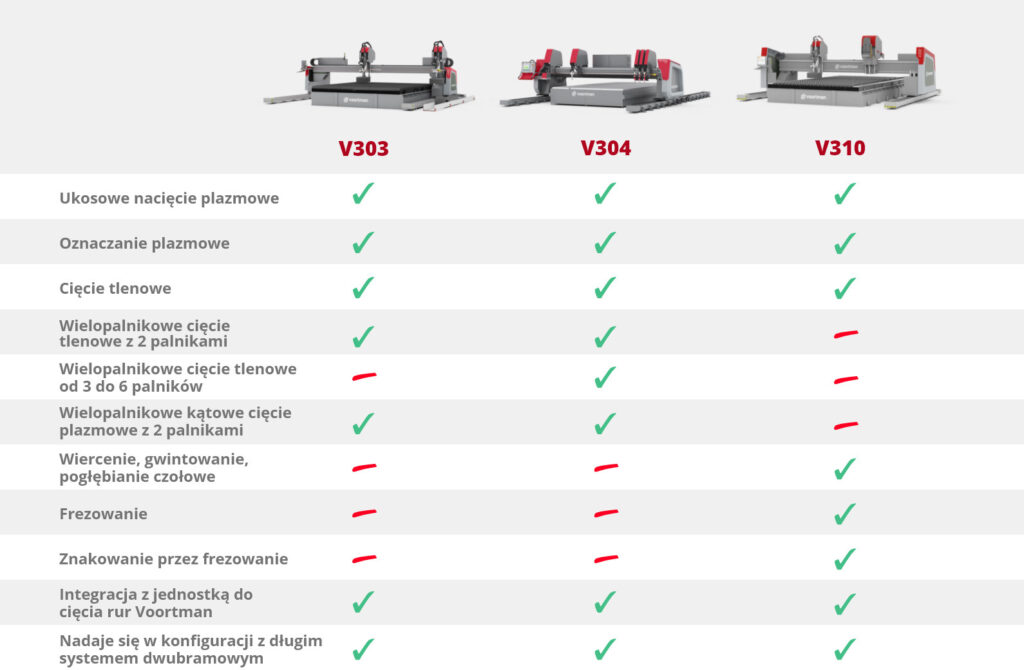
ODBLOKUJ MOC WIELOPALNIKOWEGO CIĘCIA TLENOWEGO
Z nowym Voortman V304
Zastanawiasz się nad zwiększeniem produkcji przy użyciu wielopalnikowego cięcia tlenowego? Przedstawiamy zupełny przełom – Voortman V304! Jako dumny brat V303, V304 posiada wszystkie podobne, dobrze znane funkcje, ale z dodatkiem – umożliwia obsługę wielopalnikową od 3 do 6 palników, co przynosi wiele korzyści.

1. INTERAKCJA Z MASZYNĄ
Doskonała synergia pomiędzy maszyną a halą produkcyjną
Aby zapewnić Państwu jak najwięcej informacji zwrotnych i informacji o maszynie oraz aby Państwa maszyna do obróbki blach pracowała tak wydajnie, jak to tylko możliwe, do naszego oprogramowania sterującego VACAM dodano kilka przełomowych funkcji. Dzięki temu operator maszyny może zostać mianowany kierownikiem, ponieważ jego główne zadanie zmieni się z obsługi maszyny na załadunek i rozładunek oraz zarządzanie całym warsztatem. W jaki sposób? Przeczytaj więcej poniżej!
Optymalizacja całego procesu produkcyjnego
Idealne dopasowanie do modułów SigmaNEST
Wszystkie funkcje V303 i V304 przyczyniają się do większej interakcji i feedbacku, bardzo dobrze współgrają z istniejącymi modułami SigmaNEST. Zastosowanie zaawansowanego rozwiązania nestingu SigmaNEST w połączeniu z maszynami Voortman, pozwala na optymalizację całego procesu produkcyjnego, od przygotowania pracy do produktu końcowego, poprawiając tym samym rentowność Państwa firmy. Przyjrzyjmy się dokładniej konkretnym funkcjom SigmaNEST i korzyściom, które z nich wynikają.
2. GWARANCJA NAJWYŻSZEJ MOŻLIWEJ JAKOŚCI
Bez interwencji manualnej
Dzięki nowej technologii Xtensive Bevel Cutting technology nawet cięcie skomplikowanych ukosów jest w pełni zautomatyzowane i nie wymaga ręcznej korekty, czy wstępnego cięcia próbki. W połączeniu z naszym systemem Dross Inhibitor, który minimalizuje ilość żużlu podczas przebijania, TrueVolt Technology i Xtensive Hole Technology, V303 jest w stanie w pełni automatycznie ciąć najbardziej złożone produkty.
ADD-ON / Jednostka do cięcia rur Voortman
Zwiększenie elastyczności poprzez dodanie naszego jednostka do cięcia rur Voortman
Łatwy do zintegrowania i dodania do istniejącej lub nowej maszyny do obróbki płyt V303, V310 lub V304.
NAJLEPSZA JAKOŚĆ
CIĘCIA NA RYNKU
ŁATWOŚĆ INTEGRACJI
I UŻYTKOWANIA
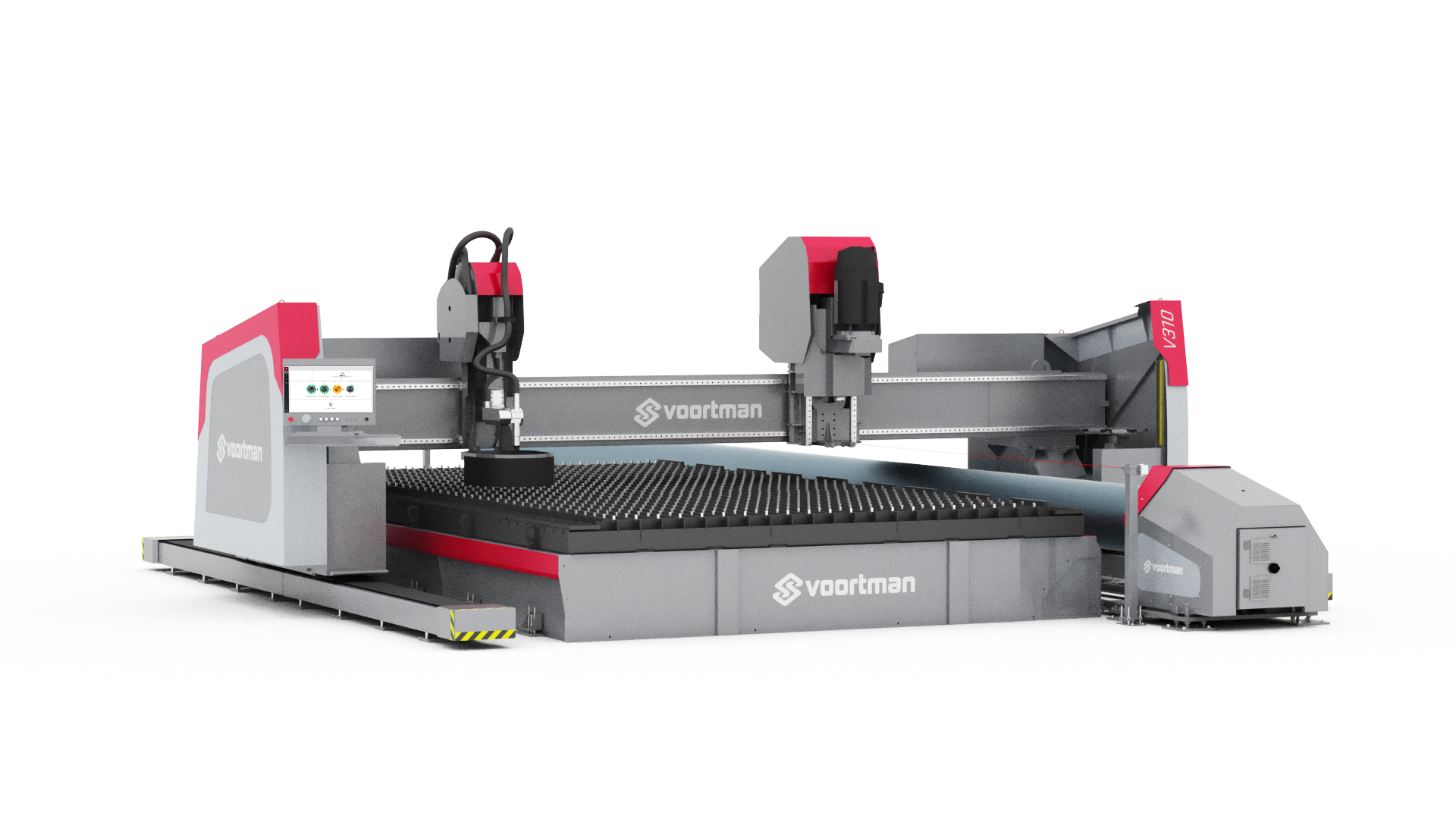
OSZCZĘDNOŚĆ CZASU
NA LOGISTYCE
MNIEJSZA ZALEŻNOŚĆ
OD DOSTAWCÓW
3. UŁATWIAJ PRACĘ
Kierownikowi hali produkcyjnej
Oczywiście są jeszcze sytuacje, w których kierownicy hal produkcyjnych zauważą konieczność przeprowadzenia operacji manualnych na maszynie lub w jej pobliżu. W takim przypadku ułatwiamy to, jak tylko to możliwe. Pomyśl o łatwym załadunku i rozładunku dzięki niskiej szynie X maszyny, łatwemu czyszczeniu stołu dzięki opracowanemu przez firmę Voortman specjalnemu stołowi do cięcia i wielu innym funkcjom.
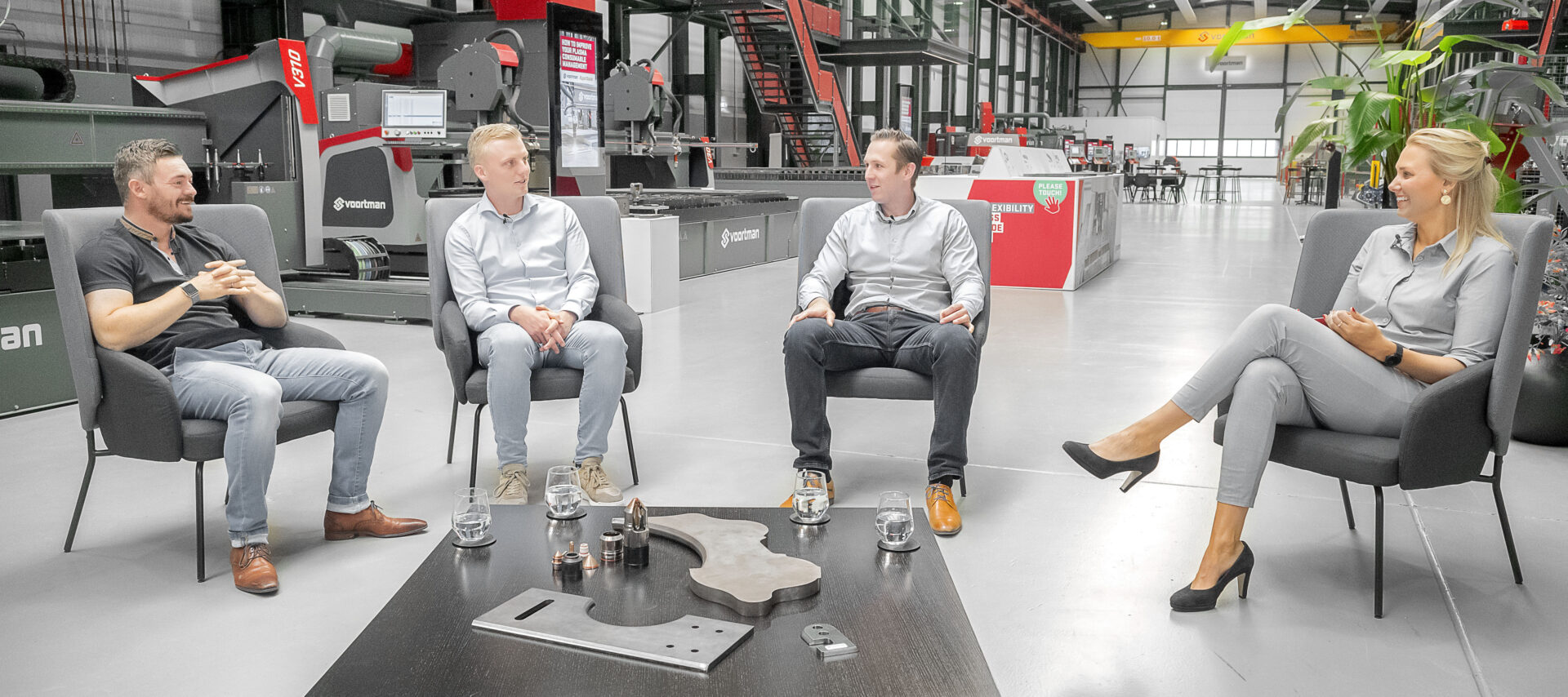
WEBINARIUM / Voortman & Hypertherm
JAK USPRAWNIC ZARZADZANIE MATERIALAMI EKSPLOATACYJNYMI DO SYSTEMOW PLAZMOWYCH
Znalezienie odpowiedniego momentu na wymianę materiałów eksploatacyjnych jest kluczowe, prawda? Podczas naszego webinarium z Hypertherm omówiliśmy różne tematy związane z poprawą zarządzania materiałami eksploatacyjnymi do plazmy. Nasi eksperci podzielili się praktycznymi spostrzeżeniami i sprytnymi strategiami, które można natychmiast zastosować w codziennych operacjach. Przygotuj się na przeniesienie zarządzania materiałami eksploatacyjnymi do plazmy na wyższy poziom dzięki naszemu webinarium!
4. MAKSYMALNY CZAS PRACY I WYDAJNOŚĆ
Masz pełną kontrolę
Ta maszyna umożliwia wsparcie i usprawnianie obsługi manualnej. Będziesz mieć do czynienia z najkrótszymi możliwymi przestojami bez wpływu na proces cięcia i jakość produktu lub z niewielkim wpływem na jego skutki. Nasi specjaliści ds. obsługi klienta są do Twojej dyspozycji 24 godziny na dobę. Oferujemy również wiele opcji zapobiegania ewentualnym przestojom. Ponieważ wszystkie nasze maszyny do cięcia blach z ruchomym portalem używają tych samych szyn X, umożliwiają jednoczesne łączenie lub uruchamianie różnych procesów. Dlatego maszyna zawsze będzie dopasowana do pożądanej wydajności.
Dane techniczne
Voortman V303 i V304 | |||
---|---|---|---|
Voortman V303 | Voortman V304 | ||
Szerokość robocza | feet | 6 - 10* | 6-16* |
Długość robocza | feet | 13 - 100* | 13 - 100* |
Prędkość cięcia | f/min | 0 - 23 | 0 - 23 |
Prędkość biegu szybkiego | f/min | 65 | 65 |
Maksymalna grubość cięcia | inch | 1/8 - 8 | 1/8 - 8 |
Maksymalna liczba palników plazmowych (ukosujących) | 2 | 2 | |
Maksymalna liczba jednostek tlenowych | 2 | 6 | |
*Większa szerokość i większe długości dostępne na zamówienie |
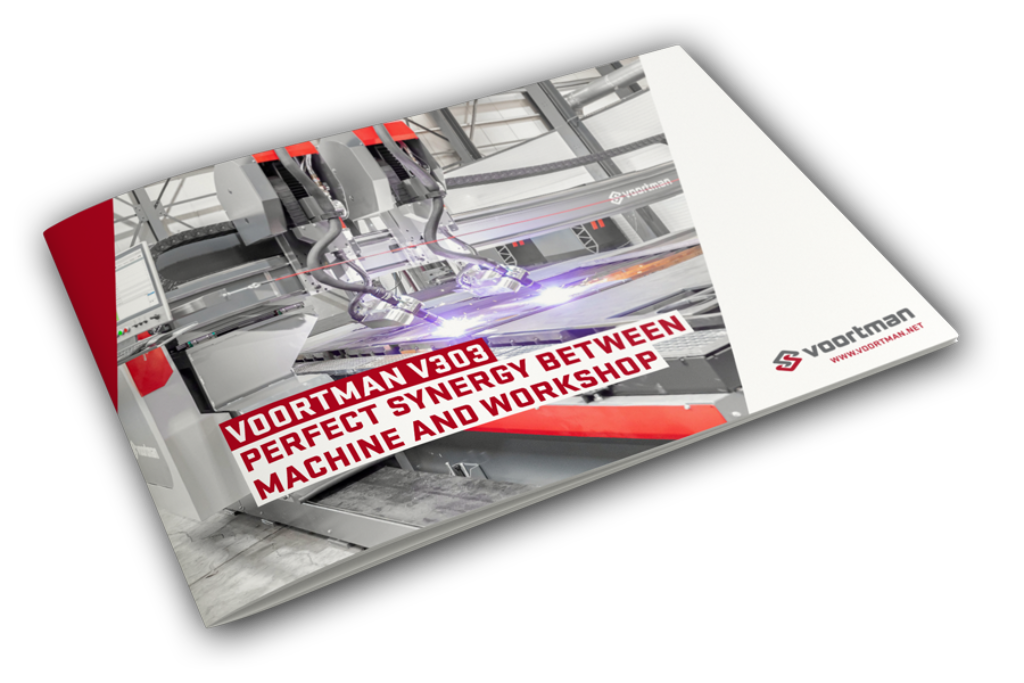
BROSZURA PRODUKTOWA V303
Chcesz szybko zapoznać się z tym, czym jest V303? Zapoznaj się z broszurą produktową V303!
SZCZEGÓŁOWA BROSZURA
Przekształć swój proces tworzenia wartości dzięki automatyzacji i cyfryzacji Voortman
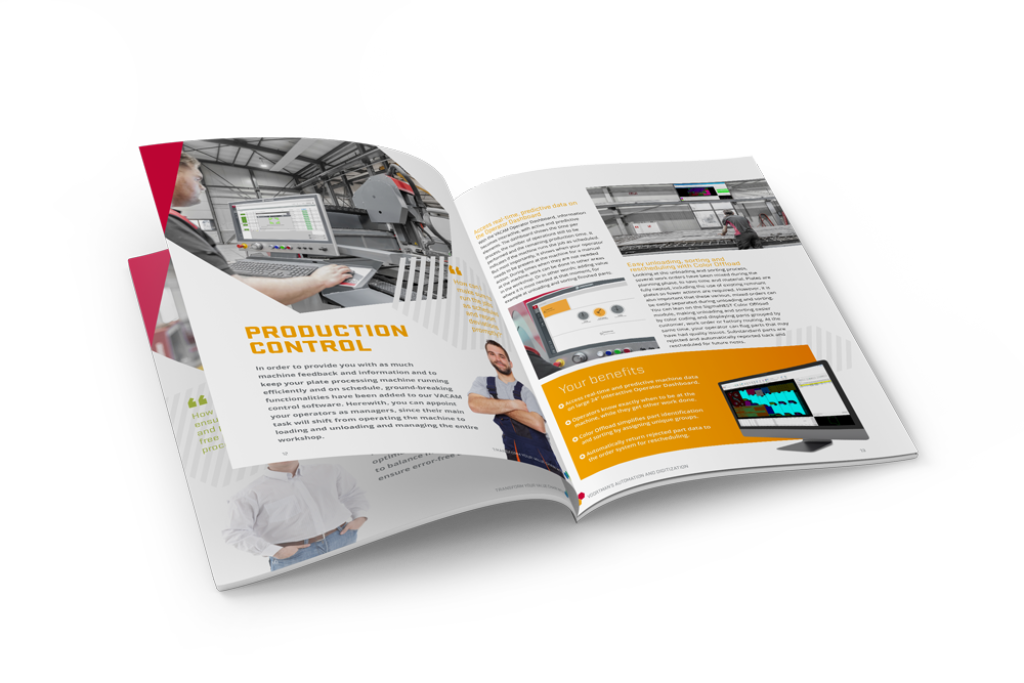