- Blacha
- Plazma
- Cięcie
- Wiercenie
- Przemysl-produkcyjny
- Przetworstwo-stali
- Automatyzacja
Maksymalizacja wydajności: wiercenie vs. Cięcie otworów - porównanie czasowe
Różne zmienne wpływające na czas
Czy znasz idealne warunki do wiercenia vs. do cięcia plazmowego podczas produkowania otworów w stali? Na czas cięcia plazmowego w stali miękkiej wpływa głównie grubość materiału i rozmiar otworu, a czas wiercenia otworów zależy głównie od elastyczność maszyny i grubość materiału.
Zarówno wiercenie, jak i cięcie są opłacalnymi procesami wykonywania otworów, a każdy z nich ma pewne zakresy zastosowań, w których jeden jest szybszy od drugiego. Przejdźmy przez kilka przykładów ze stali miękkiej, aby zorientować się, jaka jest różnica czasu między otworami po wierceniu i cięciu. Może to pomóc Ci skłonić się ku jednemu procesowi lub drugiemu w oparciu o konkretną rzeczywistą produkcję.
Małe otwory? -Wiercenie preferowane
Porównanie wiercenie vs. Cięcie: średnice otworów 14 mm i 22 mm, grubość materiału 12mm
https://youtu.be/YTB0-ZDCcos
Istnieją problemy z jakością cięcia plazmowego, gdy średnica otworu jest mniejsza niż grubość materiału, więc w takim przypadku wiercenie jest prawie zawsze preferowane. Nawet z perspektywy czasu wiercenie jest zwykle szybsze niż cięcie w przypadku małych otworów. W przypadku średnic otworów mniejszych niż 2x grubość materiału, prędkość cięcia musi być zmniejszona, aby zmniejszyć stożek otworu do minimum. Ogólnie rzecz biorąc, mały otwór do cięcia plazmowego wydłuża czas przetwarzania, podczas gdy wiercenie otworów o małej średnicy może skrócić czas potrzebny do wyprodukowania części.
Gruby materiał? - preferowane wiercenie
Porównanie wiercenie vs. Cięcie: średnice otworów 26 mm i 32 mm, grubość materiału 25mm
https://youtu.be/h6znaml7stE
Grube materiały muszą mieć bardzo duże średnice otworów, aby cięcie termiczne było lepsze z pozycji czasu i jakości. Na filmie widać, że różnice czasowe wydają się być dość małe na jeden otwór. Jednak w dużych rozkrojach te małe sekundy mogą stanowić znaczną oszczędność czasu w trakcie procesu lub całego dnia produkcji. Wszystkie dodatkowe opcje (takie jak zaciskanie płyty lub wykrywanie wysokości) są również uwzględnione w porównaniu.
Ważne jest również, aby pamiętać, że duża liczba otworów oznacza zwykle mniej przestrzeni między poszczególnymi otworami i mniej sekwencji wykrywania wysokości przy cięciu plazmowym. Całkowita różnica dla całego rozkroju może być mniejsza niż różnica między samymi otworami, ponieważ palnik plazmowy może zmniejszyć liczbę prób wykrywania wysokości potrzebnych podczas całej produkcji.
Szeroki wachlarz w średnicach otworów? - preferowane cięcie plazmą
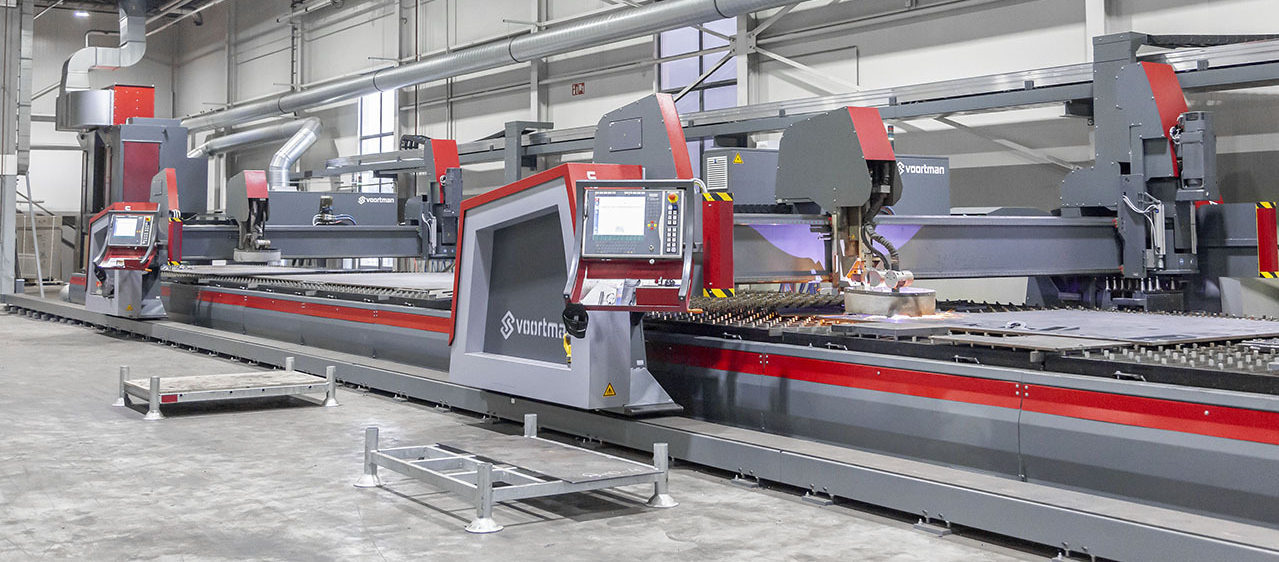
Istnieje wiele powodów dla których firmy decydują się na wycinanie otworów zamiast wiercenia. Jeśli część ma wiele różnych średnic otworów do wyprodukowania czas wiercenia wzrasta ze względu na ilość wymaganych zmian narzędzia. Każda maszyna ma również maksymalną liczbę narzędzi, które może automatycznie zmienić bez ręcznej interwencji.
Różnica czasu w wartościach bezwzględnych jest dość mała i istnieje próg rentowności, gdzie ilość różnych średnic otworów i zmian narzędzia wymaga przeciwdziałania z punktu oszczędności czasu generowanego przez wiercenie i stosowania wycinania otworów. Na przykład: w materiale o grubości 12 mm i średniej średnicy otworu 18mm próg opłacalności szacuje się przy zmianie narzędzia po wywierconych 10 otworach.
W porównaniu do starszej technologii
Ważne jest, aby wspomnieć, że nie jest to pełny przegląd wiercenia vs. cięcia. Nowe technologie, takie jak wykrywanie przebijania (sygnalizacja, kiedy blacha jest przebijana, a następnie rozpoczęcie ruchu), zwiększona średnia prędkość otworowania (poprzez optymalizację różnych prędkości w różnych sekcjach otworu) i zredukowanie początkowego wykrywania wysokości to najnowsze innowacje obecne w maszynach do cięcia plazmowego Voortman, które doprowadziły do skrócenia czasu cięcia w porównaniu do wiercenia w niektórych przypadkach. Cięcie otworów za pomocą starszej plazmy pokaże dłuższy czas cięcia w porównaniu do nowych modeli, dzięki najnowszej technologii plazmowej.
Lepsza budowa maszyny = lepsza wydajność
Powyższe porównania czasowe są w dużym stopniu zależne od konstrukcji maszyny. Maszyna o niskiej jakości może mieć niższe prędkości posuwu, które znacząco wpływają na czas wiercenia. Voortman zapewnia, użycie tylko najwyższych jakościowo komponentów w swoich niezawodnych maszynach do obróbki blach, dzięki czemu można szybko wiercić i wycinać otwory bez utraty jakości wymaganej dla projektu. Interesują Cię nasze połączone rozwiązania do wiercenia i cięcia blach? Zapoznaj się z naszymi nowymi maszynami V310, V320 i V325. Jesteś zainteresowany tylko cięciem? Maszyny do cięcia plazmowego V302 lub V304 mogą okazać się interesujące do odkrycia!
Certyfikaty, ograniczenia i oczekiwana wydajność
Wiercenie w porównaniu z cięciem jest porównywane wyłącznie z wydajnością i czasem. Jeden lub drugi proces może być również preferowany w oparciu o wymagania jakościowe. Omówimy najważniejsze czynniki, które należy rozważyć w oparciu o pozycję jakościową w przyszłym artykule. Obserwuj nasz następny artykuł, który pomoże Ci wybrać proces, który najlepiej odpowiada Twoim potrzebom!