V842

Lasersnijden van buizen van klein tot middelgroot bereik
- Perfect voor het lasersnijden van kleine tot middelgrote buizen en ronde pijpen
- Produceert efficiënt productieklare onderdelen
- Automatisch centreer- en klemsysteem zorgt voor uitlijning en +/- 0,1 mm precisie voor nauwkeurig snijden
- Instelbare klemkracht houdt kleinere en dunnere profielen stevig vast zonder vervorming
INLEIDING
De Voortman V842 is een kosteneffectieve en efficiënte snijmachine voor laser buizen. De machine is voorzien van een automatisch centreer- en vastklemsysteem, dat zorgt voor een onberispelijke uitlijning en +/- 0,1 mm precisie voor nauwkeurige sneden. De verstelbare klemkracht van de V842 houdt kleinere en dunnere profielen stevig vast zonder vervorming.
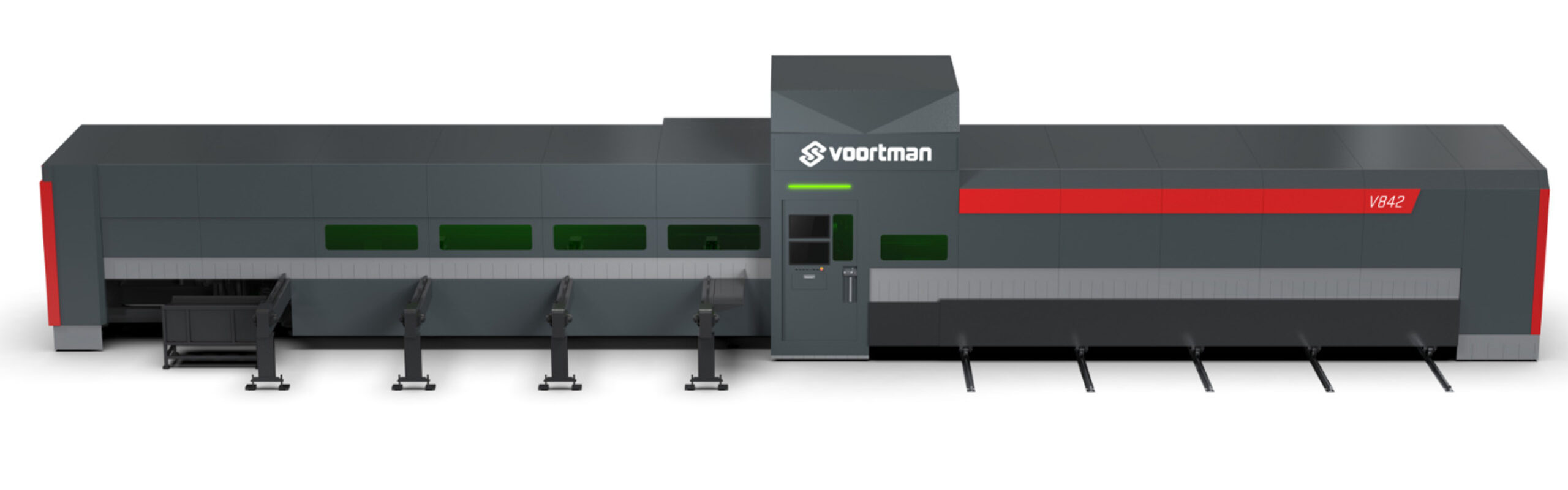

PRECISIE VASTKLEMMEN
EN SNIJDEN
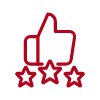
GEREED PRODUCT
NA HET SLIJPEN
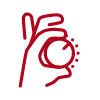
GEMAK VAN
BEDIENING

SCHERP GEPRIJSD
METVOORTMAN'S UITSTEKENDE SERVICE
Met deze snijmachine voegt Voortman een basismodel toe aan zijn portfolio. Het is een instapmodel scherp geprijsde machine die volledig is inbegrepen in de uitstekende service van Voortman. Deze combinatie maakt deze machine een zeer interessante optie om de voordelen van een samenwerking met Voortman te ervaren.
ZEER NAUWKEURIGE BEWERKING
VASTKLEMMEN EN SNIJDEN
100M/MIN POSITIONERING
MET HOGE SNELHEID
Verhoog uw productiviteit met een bewerking op hoge snelheid tot maar liefst 100 m/min. Dit indrukwekkende vermogen versnelt de bewerking van profielen,
waardoor de cyclustijden aanzienlijk korter worden en uw verwerkingscapaciteit toeneemt. U kunt er zeker van zijn dat de machine zelfs bij hoge snelheden nauwkeurig blijft uitlijnen en snijden, voor een consistente snijkwaliteit bij elke snede.
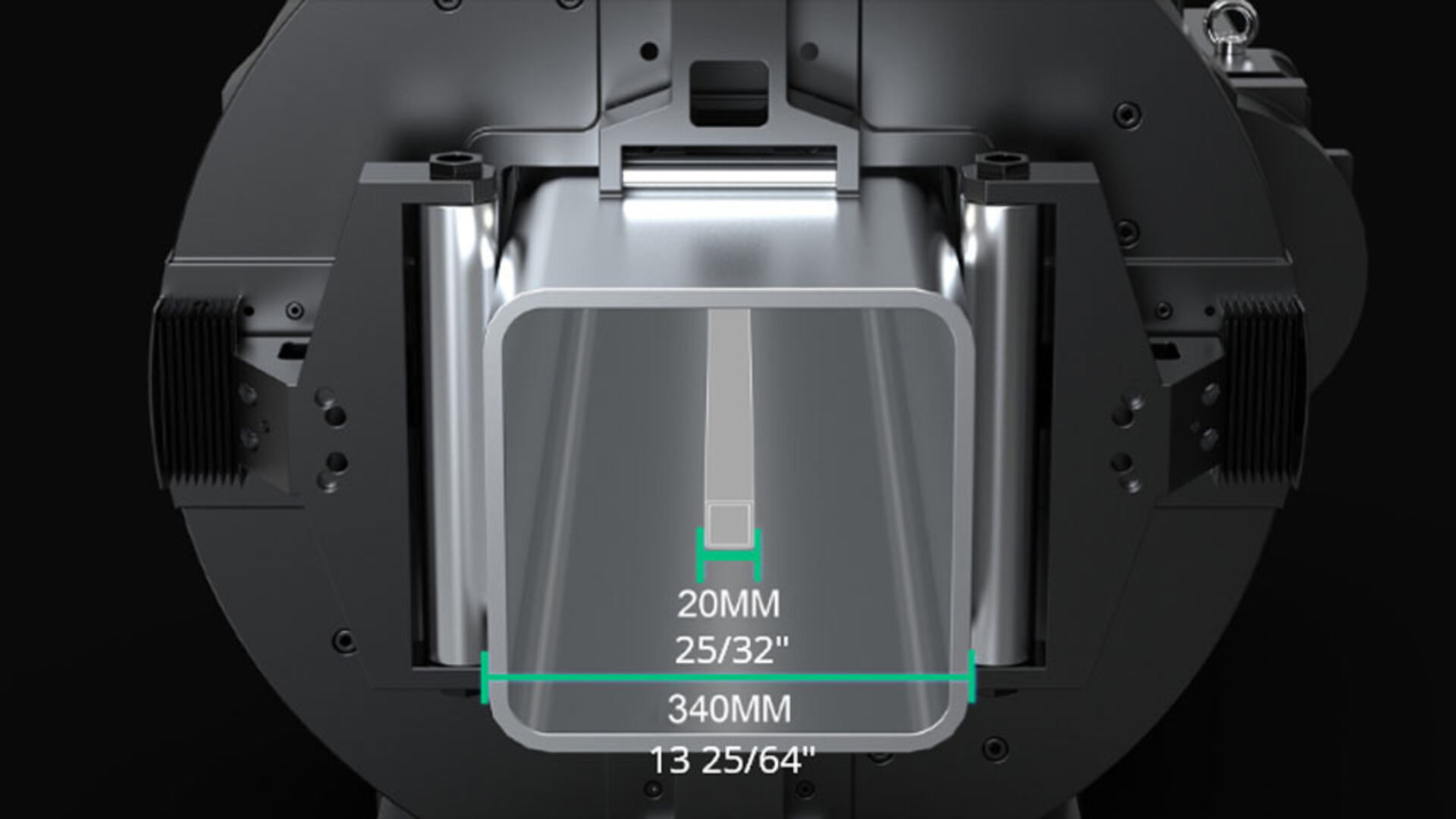
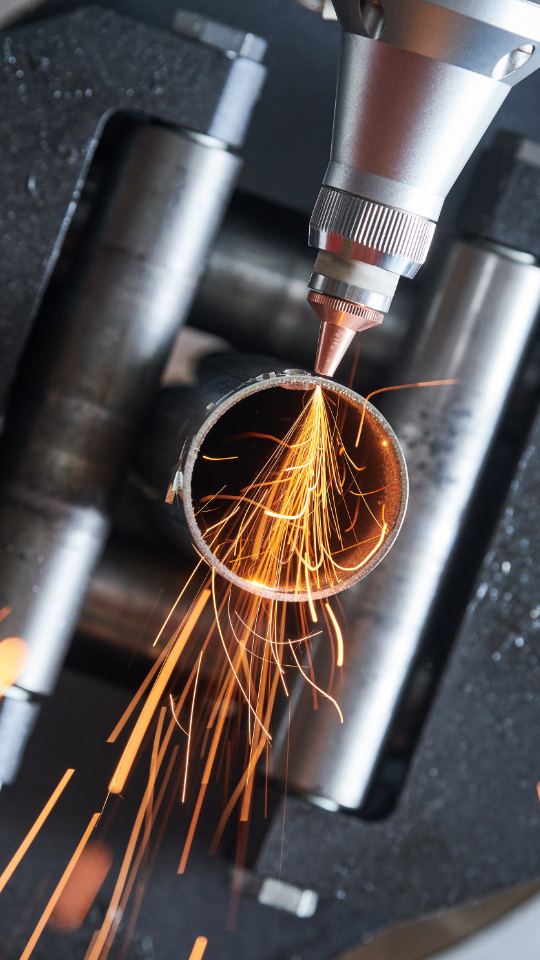
PRECISIE
VASTKLEMMEN
Nauwkeurig vastklemmen met automatische centrering voor consistente nauwkeurigheid. Bereik een ongeëvenaarde precisie met het automatische centreer- en klemsysteem van de Voortman V842, dat een onberispelijke uitlijning garandeert voor nauwkeurig zagen. Met een snijprecisie van +/- 0,1 mm kunt u vertrouwen op consistente resultaten voor verschillende buizen en ronde buizen. Deze automatisering elimineert handmatige aanpassingen, waardoor de efficiëntie zelfs bij hoge snelheden behouden blijft.
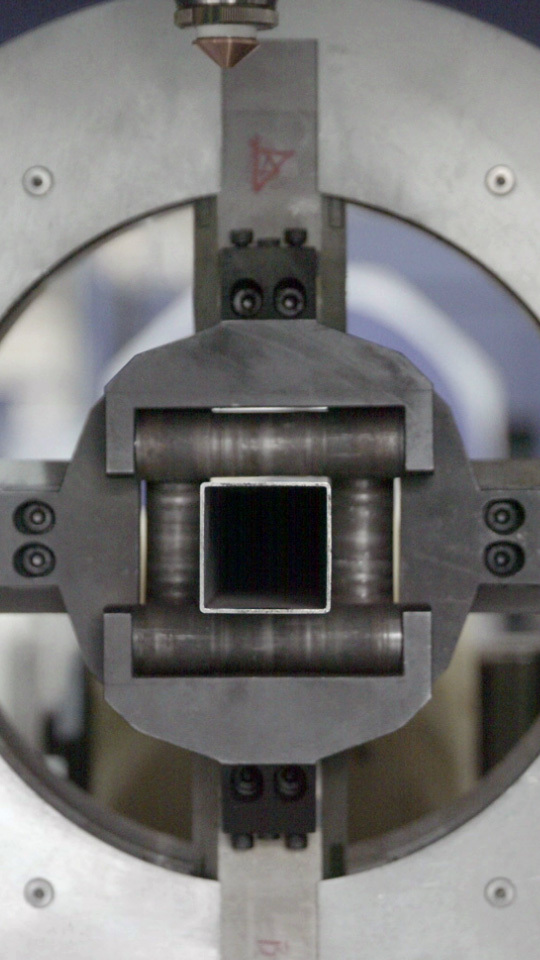
INSTELBAAR
VASTKLEMMEN KRACHT
Instelbare klemkracht voor kleinere en dunnere profielen.Ontdek de flexibiliteit van de V842, met een instelbare klemkracht die perfect is voor het hanteren van kleinere en dunnere profielen. Dit innovatieve ontwerp houdt kwetsbare materialen stevig vast zonder vervorming of beschadiging en zorgt voor topkwaliteit. Door de klemkracht automatisch aan te passen aan elke profielgrootte en -dikte, kunt u stabiele en nauwkeurige sneden maken, zelfs met lichte of kwetsbare buizen.
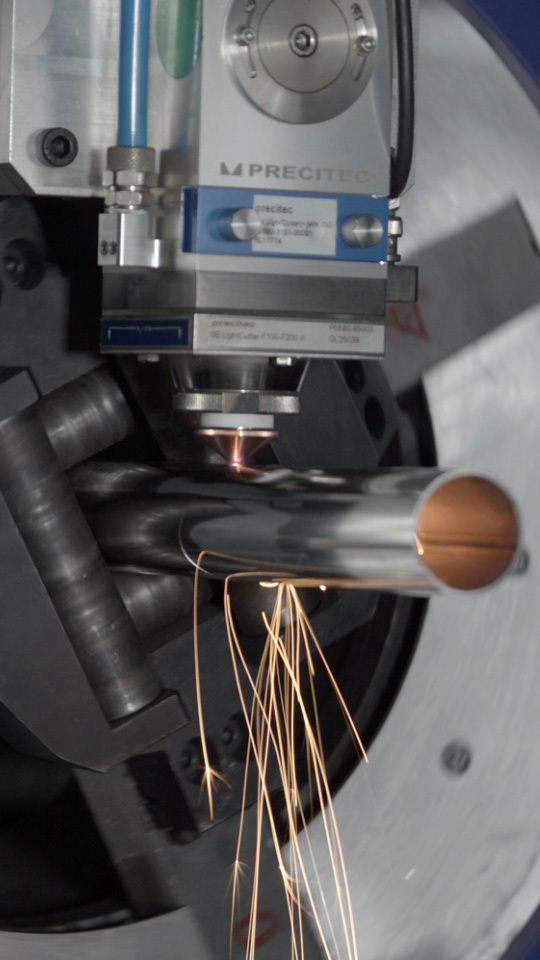
BACKANT
BEWERKING
Ook het bewerken en snijden van profielen aan de achterkant behoort tot de mogelijkheden van het geavanceerde 3-klauwplaten systeem. Met deze innovatieve mogelijkheid kunt u materiaal efficiënt aan beide uiteinden verwerken en snijden, waardoor uw productiviteit en veelzijdigheid worden gemaximaliseerd. Met een stevige grip op het profiel zorgt de machine voor nauwkeurige zaagsneden, zelfs bij toegang tot de achterkant.
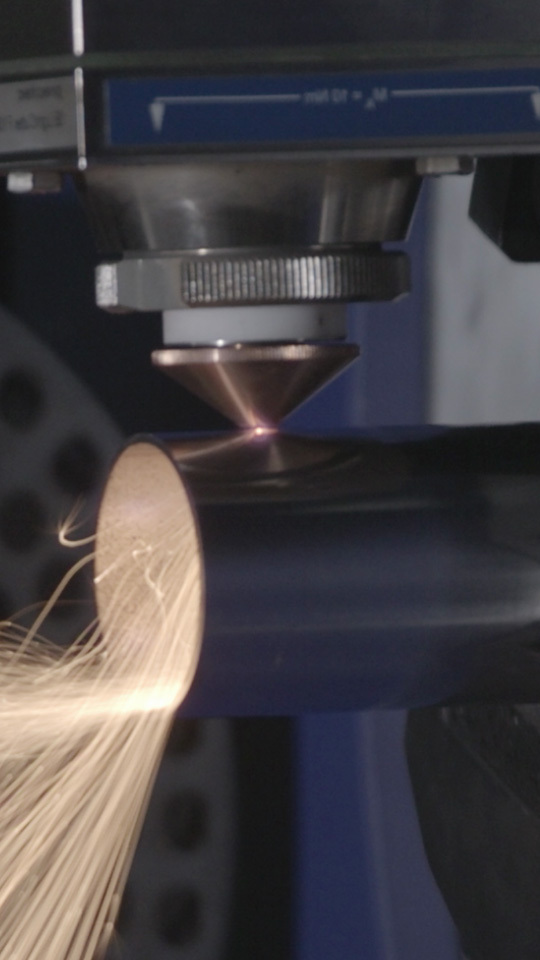
AUTOMATISCH
TAKEOVER
Automatische overname van rustmateriaal met klauwplaten. Met een intelligent spansysteem neemt de Voortman V842 automatisch rustmateriaal over tijdens het snijden. Dit innovatieve ontwerp zorgt voor naadloze overgangen en optimaal materiaalgebruik, waardoor afval wordt verminderd en de efficiëntie wordt verhoogd. Door het resterende materiaal stevig vast te houden, maken de klauwplaten het mogelijk om nauwkeurig over de hele lengte van het profiel te snijden, waardoor een effectieve bewerking van de achterkant en minimale materiaalresten mogelijk zijn.
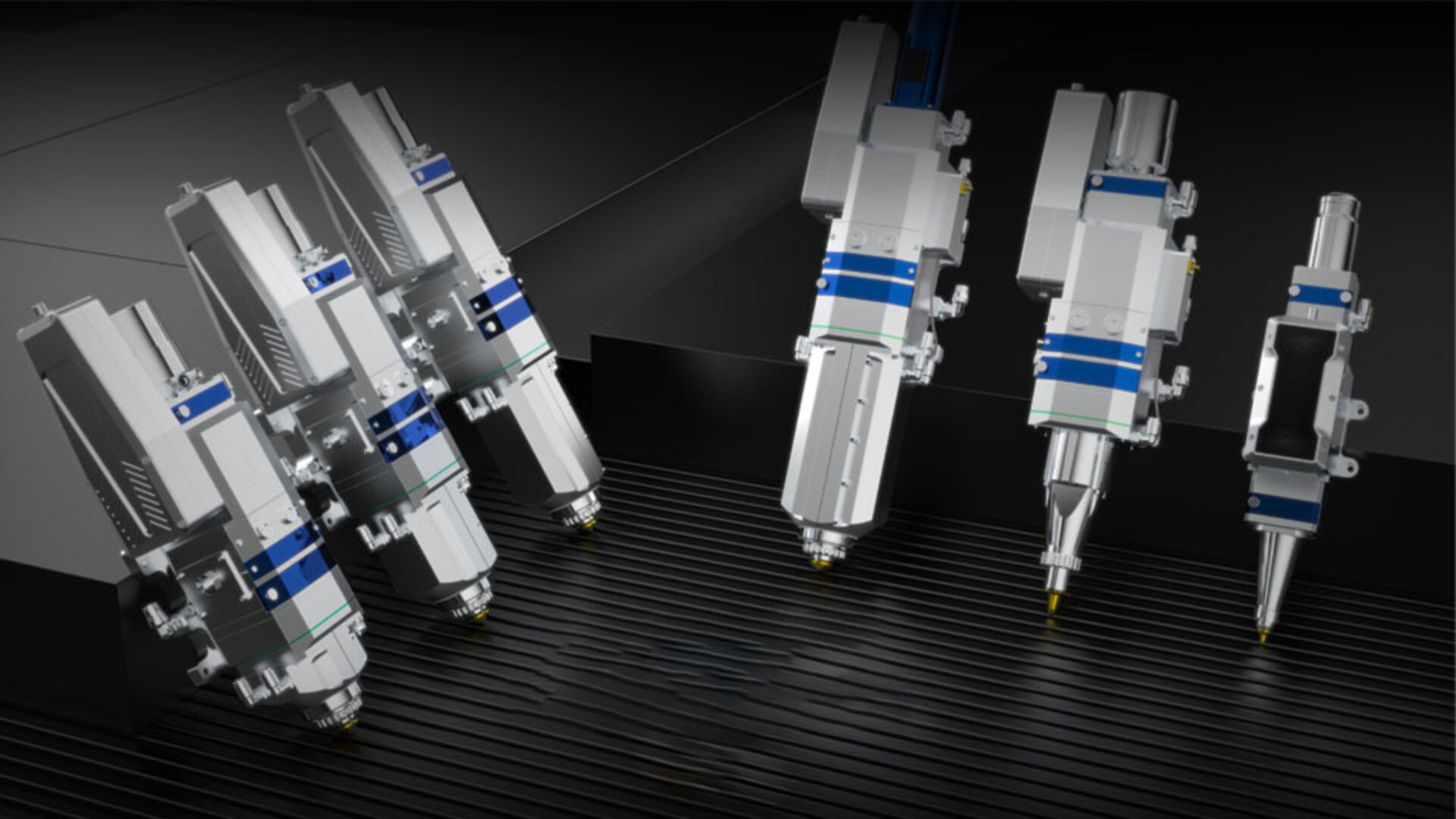
SNIJKOP(PEN)
De snijkop van de V842 is ontworpen voor zowel precisie als efficiëntie. Het innovatieve koelsysteem zorgt voor optimale prestaties en beschermt belangrijke onderdelen om de operationele tijd te verlengen. Met meerdere beschermende lenzen minimaliseert de snijkop verontreinigingen, waardoor de duurzaamheid van kritieke onderdelen wordt verbeterd. De snelle scherpstelmogelijkheden zorgen voor snellere aanpassingen en een breder scherpstelbereik, waardoor de algehele efficiëntie toeneemt. Bovendien houden intelligente bewakingsfuncties de temperatuur in de gaten. Dit doordachte ontwerp zorgt voor betrouwbare prestaties en voorkomt potentiële problemen zoals roest of vastlopen, waardoor het een waardevolle aanwinst is voor uw snijwerkzaamheden. Op basis van uw wensen kan een bepaald snijvermogen worden geconfigureerd.
GEBRUIKSKLARE PRODUCTEN
MINIMALE NABEWERKING
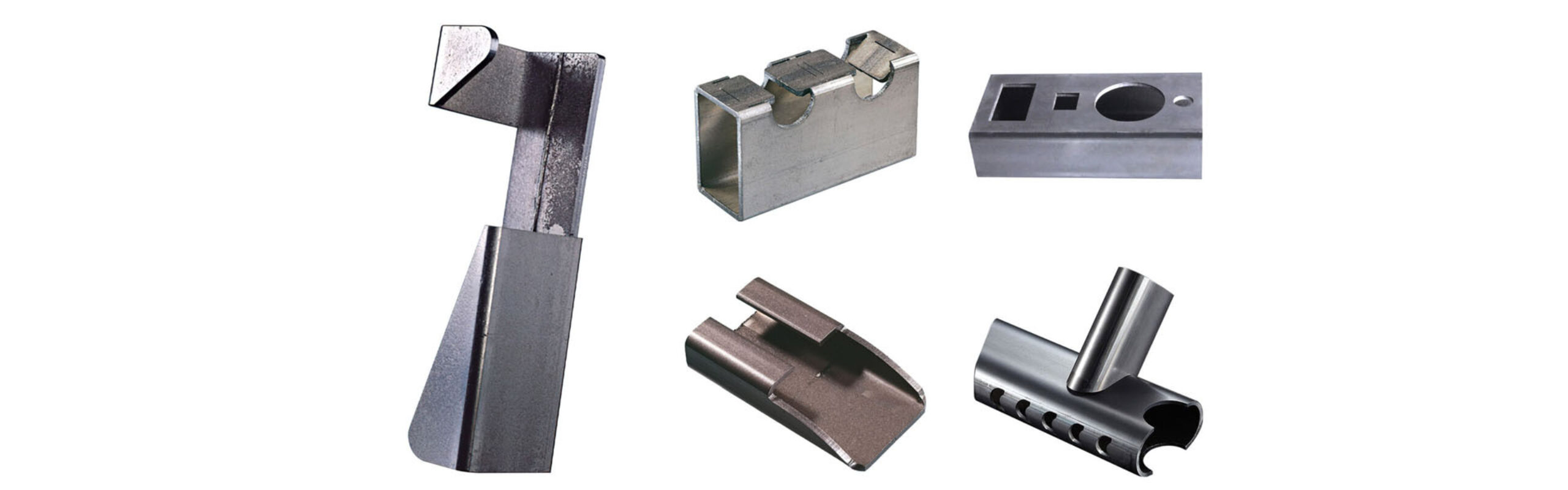
MINIMAAL
NABEWERKING
Geniet van aanzienlijke tijd- en kostenbesparingen met de V842, die weinig tot geen Nabewerking vereist. In tegenstelling tot traditionele plasmasnijmethoden die vaak restslakken achterlaten, levert onze machine sneden van hoge kwaliteit met schone randen en nauwkeurige afwerkingen. Deze minimale Nabewerking verbetert uw operationele efficiëntie, zodat u uw workflow kunt stroomlijnen en onmiddellijk uitzonderlijke resultaten kunt leveren.
ONEINDIGE ROTATIE
VAN CHUCKS
De mogelijkheid om de klauwplaten traploos te laten draaien biedt aanzienlijke voordelen bij de bewerking van buizen. Waarom? Met deze functie kunnen lange profielen continu en ononderbroken gesneden worden, waardoor de machine verschillende vormen en maten kan verwerken zonder dat herpositionering nodig is. Het verbetert de efficiëntie van uw workflow door de cyclustijden te verkorten. Traploze rotatie ondersteunt complexe snijpatronen zoals spiralen en bewerking aan de achterkant, wat veelzijdigheid biedt en de productiviteit maximaliseert in diverse toepassingen. Na het maken van sneden of gaten wordt het profiel nog een paar keer gedraaid. Hierdoor botst de laserkop niet tegen het materiaal dat overblijft na het snijden, zodat u minder vaak nozzles hoeft te vervangen.
GEREDUCEERD
RESTMATERIAAL
De V842 is ontworpen om het materiaalgebruik te optimaliseren en laat na het zagen slechts 5 mm restmateriaal over. Door het gebruik van drie klauwplaten wordt slechts minimaal materiaal verspild, wat bijdraagt aan een kosteneffectief productieproces. Dit efficiënte ontwerp maakt een nauwkeurige bewerking van lange materiaallengtes mogelijk en vermindert de rotatietraagheid, waardoor de nauwkeurigheid en prestaties verder verbeteren.
SOFTWARE & AUTOMATISERING
GEBRUIKSVRIENDELIJK
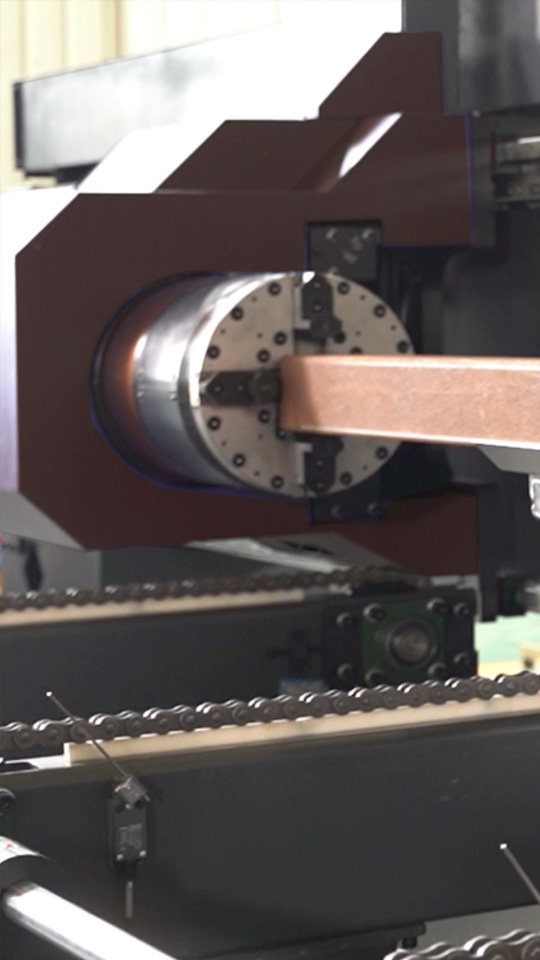
SEMI-AUTOMATISCH
LAADSYSTEEM
Het halfautomatische laadsysteem vereenvoudigt het proces om uw profielen zaagklaar te maken. Het tilt een hele bundel profielen in het materiaalmagazijn. Van daaruit plaatst de operator de profielen handmatig in het laadgebied. Het systeem scheidt vervolgens automatisch elk profiel en voert het naar de snijpositie. Dit vermindert de handmatige verwerking, bespaart tijd en verhoogt de productie-efficiëntie, terwijl ook de arbeidskosten dalen. Het is gebruiksvriendelijk en helpt uw workflow soepel en georganiseerd te houden. De lengte van de invoer kan aan uw behoeften worden aangepast.

BUNDEL
LAADSYSTEEM
Het optionele bundellaadsysteem zorgt voor een revolutie in uw workflow dankzij het geavanceerde ontwerp, dat bestaat uit een stapelbandtransporteur, een kettingtransporteur en een toevoerarmsysteem. Laad uw grondstoffen gewoon op de stapelband en kijk hoe de transportband de buizen moeiteloos in positie trekt. De kettingtransportband transporteert de materialen vervolgens naar de toevoerarm, die ze rechtstreeks naar de snijmachine brengt. Deze naadloze werking verbetert de bewerkingsefficiëntie aanzienlijk en vermindert de benodigde arbeid aanzienlijk, waardoor het een ideale oplossing is om uw productielijn te optimaliseren.
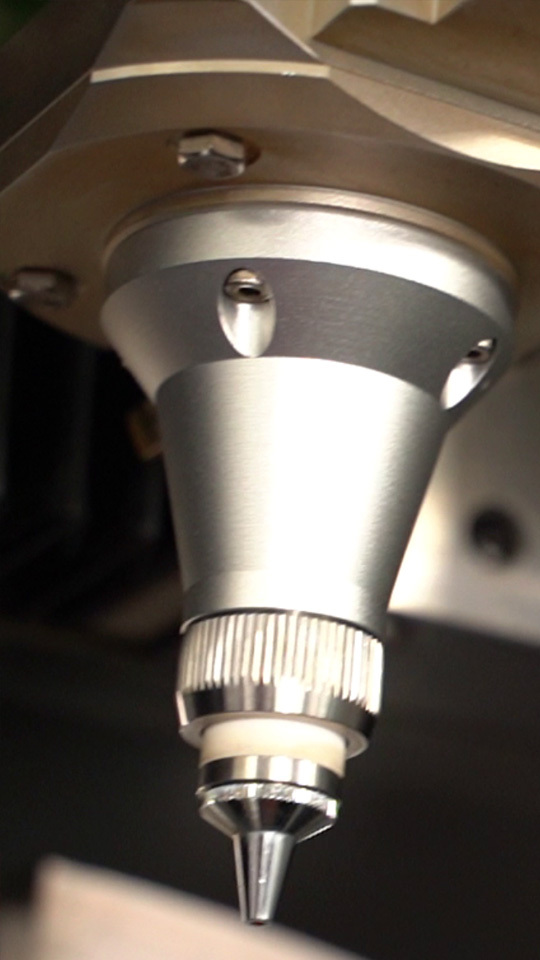
AUTO-CENTRERING
SNIJKOP
De snijkop heeft een automatische centreerfunctie die zorgt voor een nauwkeurige uitlijning bij elke snede. Deze intelligente functie maakt handmatige aanpassingen overbodig en zorgt voor consistente nauwkeurigheid in verschillende profielen. Door het instelproces te stroomlijnen, verbetert de automatische centreerfunctie de algehele efficiëntie en wordt de kans op fouten geminimaliseerd, waardoor het voor operators eenvoudiger wordt om resultaten van hoge kwaliteit te behalen.
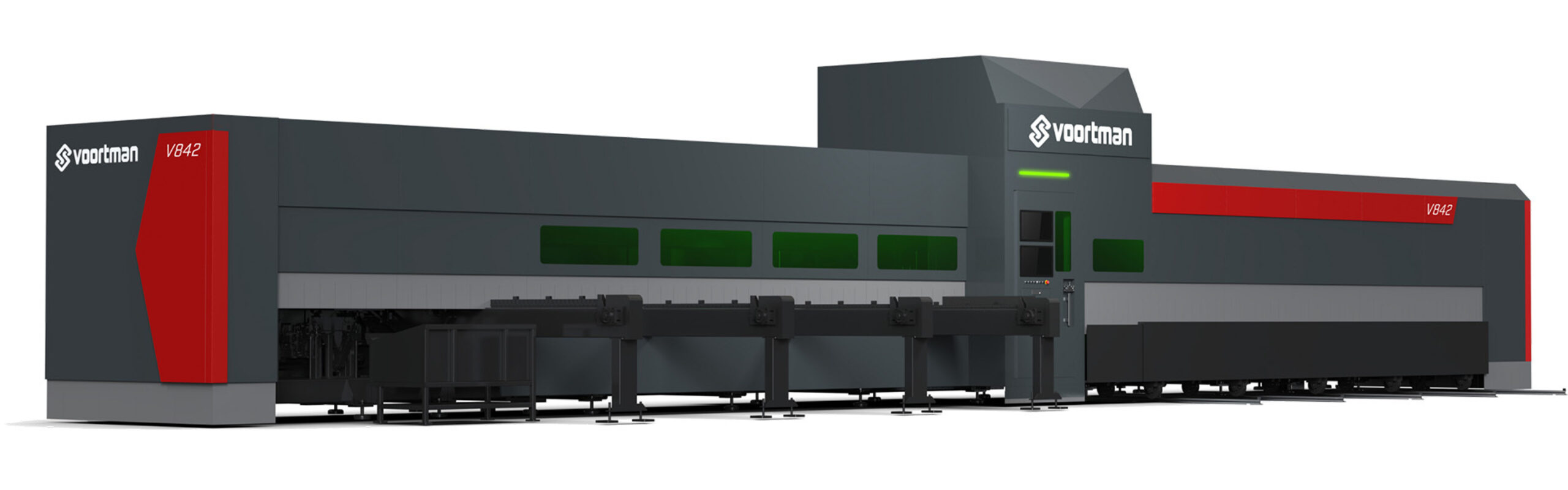
CONTROL
PANEL
Het grote 24” multi-touch bedieningspaneel biedt een aangenaam en toegankelijk werkgebied voor uw operators, met directe toegangsknoppen voor de meest kritische machinefuncties. Het bedieningspaneel heeft ook een fysiek toetsenbord van volledig formaat, waardoor de operator een state-of-the-art gebruikerservaring heeft die kan wedijveren met de beste gebruiksvriendelijke voorbeelden in de sector. Er zijn USB-poorten beschikbaar op het bedieningsstation voor het importeren/exporteren van bestanden. Het aanraakscherm is gemaakt met het oog op duurzaamheid, zodat het in elke omgeving betrouwbaar kan functioneren.
MINDER
DUBBEL WERK
De functie voor het hervatten van jobs zorgt ervoor dat uw workflow ononderbroken blijft als de stroom uitvalt of wordt onderbroken. Dankzij deze functie kan de machine automatisch verdergaan waar hij gebleven was, zodat er niet opnieuw hoeft te worden gewerkt en de algehele efficiëntie toeneemt. Hierdoor blijven uw productieschema's gehandhaafd en gaat er geen materiaal verloren.
GEAVANCEERDE
NESTING SOFTWARE
De V842 wordt uitgerust met geavanceerde besturingssoftware en nesting software die het materiaalgebruik maximaliseert en de snijprocessen stroomlijnt. Deze software ondersteunt een groot aantal bestandstypen, waaronder 3D-import zoals STEP-bestanden, en maakt een soepele bewerking van unieke vormen en profielen mogelijk om afval te verminderen. De software beschikt over modulatie van het laservermogen voor nauwkeurige aanpassingen op basis van verschillende materialen, een Z-as zweeffunctie voor aanpasbaarheid aan niet-vlakke oppervlakken en CNC compensatie om onnodige bewegingen tussen de machine en de pc te minimaliseren. Bovendien zorgt de thermische focuscompensatie voor behoud van de snijnauwkeurigheid bij hoog vermogen, zodat bij elke snede consistente resultaten van hoge kwaliteit worden verkregen.
Voortman V842 Baseline | ||
---|---|---|
V842-250 | ||
Bewerkingsvenster | 13/16" - 9-7/16" | |
Max. Totaal positioneringsgewicht | 882 lbs | |
Max. LineairPositioneringsgewicht | 30 lbs/ft | |
Max. Lengte product | 20, 30, 40 ft | |
Max. Positioneersnelheid | 320 ft/min | |
Laservermogen | 3, 6, 12 kW | |
Max. Rotatiesnelheid van Chucks | 100 rpm | |
Verplaatsing rotatieas | ∞ | |
Aantal roterende chucks | 3 |