Multi System Integration
Volledig geautomatiseerde geïntegreerde productielijn
MSI, ook wel Multi System Integration genoemd, maakt het mogelijk om uw productie volledig te automatiseren door machines aan te sluiten op dwarstransportbanden, rollentransportbanden, productbuffers en materiaalsensoren. Uw productiegegevens hoeven maar één keer te worden geïmporteerd en MSI verdeelt de gegevens vervolgens automatisch over alle machines die in uw productiesysteem zijn geïntegreerd. Het handmatig transporteren van materialen door de productielijn behoort tot het verleden door het creëren van één geïntegreerd productiesysteem. Uitgerust met VACAM, onze eigen besturingssoftware die op elke machine wordt geïnstalleerd, krijgt u de mogelijkheid om uw volledige productieproces in real time te volgen.
Een introductie tot een smart factory
We zijn gespecialiseerd in het ontwerpen en installeren van volledig geautomatiseerde productielijnen over de hele wereld, met hardware van hoge kwaliteit en geavanceerde software. Onze Multi System-benadering zorgt ervoor dat machines naadloos op elkaar aansluiten via onze VACAM-software, dwarstransporten, rollenbanen, productbuffers en materiaalsensoren.
Maar wat betekent een smart factory nou eigenlijk? Hoe worden materiaalstromen ingericht en welke keuzes worden er gemaakt op basis van geanalyseerde data? Laten we de volledig geautomatiseerde productie in deze echte smart factory eens van dichtbij bekijken!
Geautomatiseerde materiaalverwerking
Lagere arbeidskosten en meer efficiëntie dankzij geautomatiseerde materiaalverwerking
De integratie van geautomatiseerde materiaalverwerking in een volledig geautomatiseerde MSI systeem biedt aanzienlijke kostenbesparingen voor elke fabrikant van constructiestaal. Geschoold personeel is steeds moeilijker te vinden en het kan veel geld kosten om operators aan uw productieproces toe te voegen. MSI streeft ernaar om het aantal benodigde manuren per geproduceerde ton tot een minimum te beperken met ingebouwde slimme productie-algoritmen in onze eigen VACAM besturingssoftware. Elke Voortman machine draait op dezelfde besturingssoftware en wordt gesynchroniseerd met de master CNC controller, waardoor uw materiaal op afstand kan worden omgeleid en gestuurd zonder handmatige interventie.
Als staalbouwers voor het eerst een complete Voortman MSI-productielijn zien, zijn ze vaak verbaasd over de grote hoeveelheid materiaal die door het systeem beweegt met slechts een paar mensen die toezicht houden op de productie. Klanten realiseren zich al snel hoe noodzakelijk het complete systeem voor hen is om concurrentie voor te blijven en hun totale kosten per ton te verlagen.
Het verplaatsen van materiaal is niet alleen duur, maar ook tijdrovend en kan leiden tot bottlenecks in de productielijn. Vertrouwen op kranen om materiaal van de ene machine naar de andere te verplaatsen is inefficiënt. Met MSI, dat machines naadloos met elkaar verbindt in een volledig geautomatiseerd systeem, kunnen verschillende bewerkingen tegelijkertijd worden uitgevoerd, waardoor de productie-efficiëntie toeneemt en uw manuren afnemen.
Hieronder ziet u een voorbeeld van hoe een volledig geautomatiseerde productielijn eruit ziet!
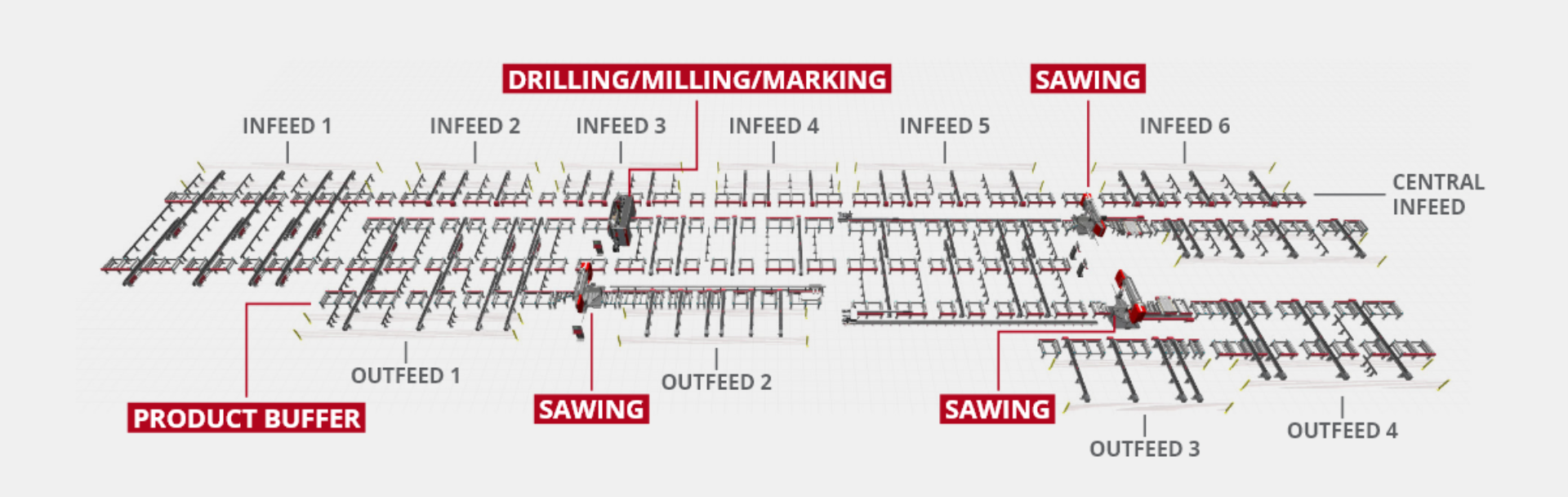
Grote flexibiliteit bij het creëren van uw optimale profiel bewerking lay-out
Uw input combineren met data om uw optimale ontwerp te creëren
Staalbouwers worden vaak geconfronteerd met uitdagingen zoals onvoldoende capaciteit, gebrek aan mankracht of beperkte werkruimte. Door een op maat gemaakte productielijn te integreren die specifiek is afgestemd op uw bedrijfsmodel, kunt u de overheadkosten aanzienlijk verlagen en tegelijkertijd uw algehele efficiëntie verbeteren, allemaal bereikt door Multi System Integration (MSI). Voortman gebruikt een op maat gemaakte datagestuurde aanpak om de beste lay-out en configuratie te bepalen die specifiek is afgestemd op uw bedrijfsmodel. We beginnen met het bepalen van uw optimale indeling voor de verwerking van profielen.
Elk bedrijf is uniek en een optimale lay-out is afhankelijk van veel factoren. Tijdens het overleg komt alles aan bod: de processen die u uitvoert, de typen profielen, uw productlengtes, de beschikbare ruimte in uw werkplaats en uw gewenste output om maar een paar factoren te noemen. Voortman is zeer flexibel en kan voor elk scenario een zo optimaal mogelijke indeling vinden. Er wordt gekozen voor een modulaire aanpak om meer flexibiliteit aan te brengen in de verwerkingsvolgorde.
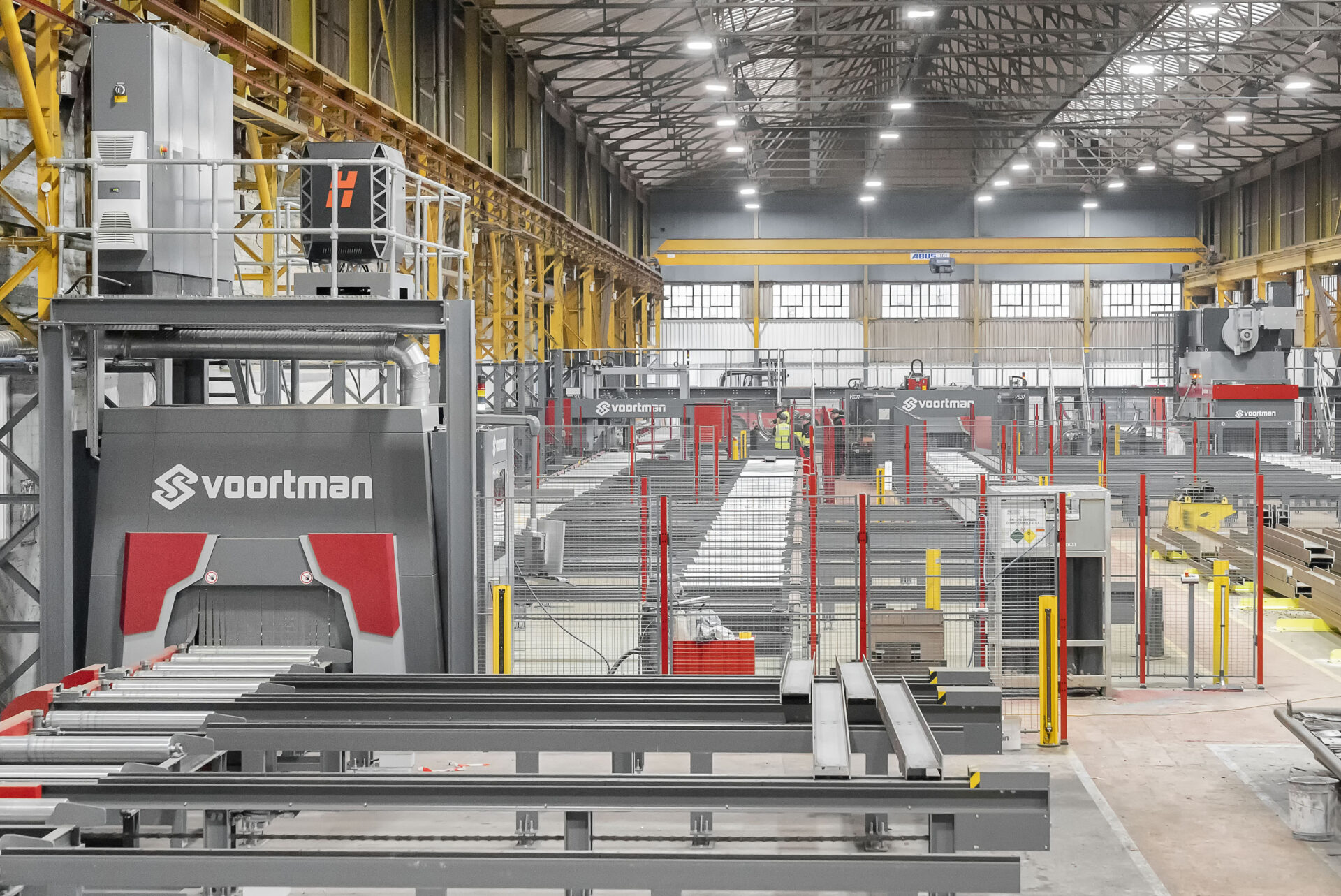
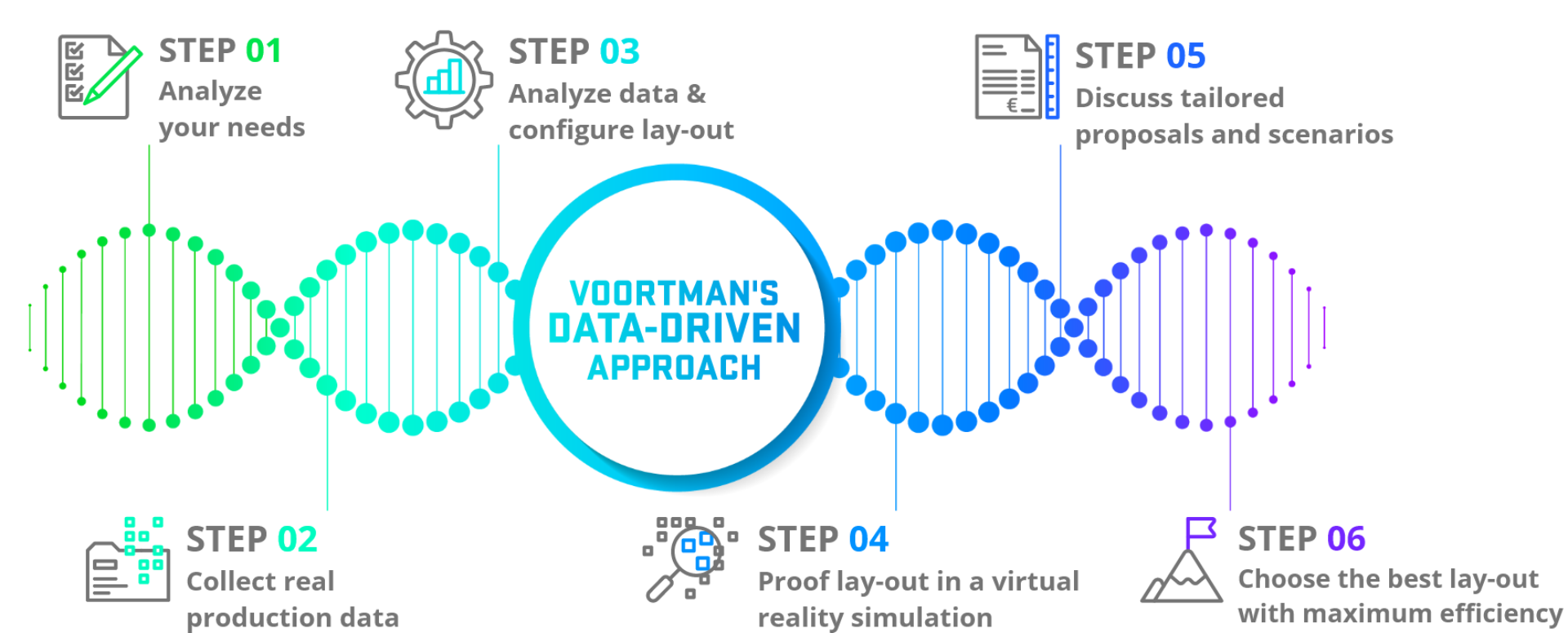
Onze datagestuurde aanpak
Om een optimale lay-out met maximale efficiëntie te bereiken, gebruiken we een gegevensgestuurde aanpak die uw input en behoeften combineert met echte data en hierbij rekening houdt met toekomstige verwachtingen. Laten we eens kijken hoe dit lay-outontwerp eruitziet!
Finley Structures omarmt efficiëntie
Finley Structures, een bedrijf uit het Verenigd Koninkrijk gevestigd in County Durham, heeft recentelijk een inbedrijfsname- en trainingsperiode gehad voor hun nieuwe geautomatiseerde Voortman machinelijn. Het bedrijf heeft geïnvesteerd in de nieuwste technologie en machines om ervoor te zorgen dat hun productieproces zo efficiënt mogelijk is. De nieuwe machinelijn heeft een unieke U-vorm die speciaal is ontworpen om in de beschikbare ruimte van de fabriek te passen. Het systeem is volledig geautomatiseerd, met een ingebouwd invoer- en buffersysteem voor meerdere uitvoerzones. De ruwe profielen worden gereinigd met de Voortman Straalmachine en vervolgens bewerkt met de drie-assige Voortman V631, die ook kan frezen om de werkdruk op de V807 robotische raveelmachine te verminderen. De profielen worden op lengte gezaagd met de Voortman Bandzaag, inclusief het verwijderen van korte stukken, en tenslotte worden de profielen afgewerkt met de all-in-one Voortman V807.
"De beslissing voor het U-vormige systeem, dat uniek is aan Voortman, was om ons in staat te stellen de belangrijkste benodigde elementen in de machinelijn toe te voegen en ook vanwege de bestaande ruimte die beschikbaar was. Toen we keken naar andere systemen die beschikbaar waren, konden die niet een systeem bedenken binnen de ruimte die we hadden. Dus kwam Voortman weer met de beste oplossing."
JULIE RAISTRICK, ALGEMEEN DIRECTRICE VAN FINLEY STRUCTURES
INTEGRATIE IN UW WERKOMGEVING
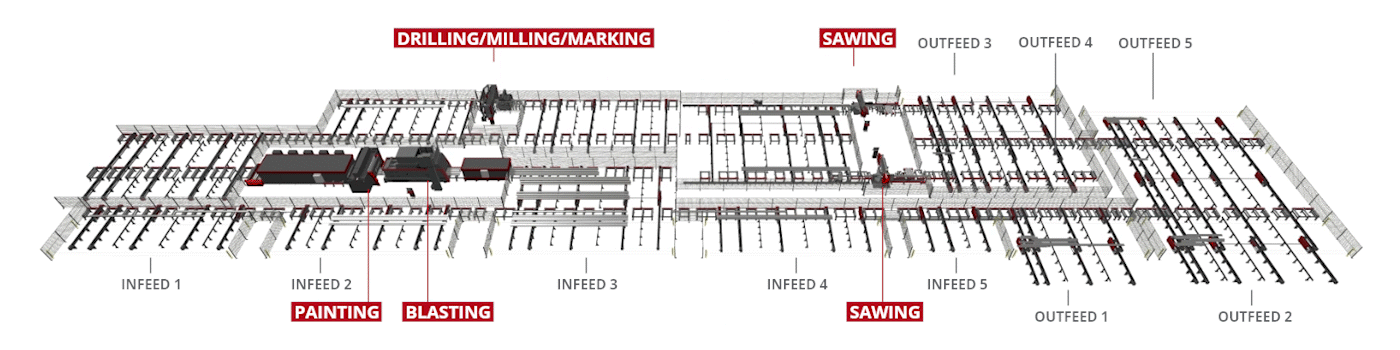
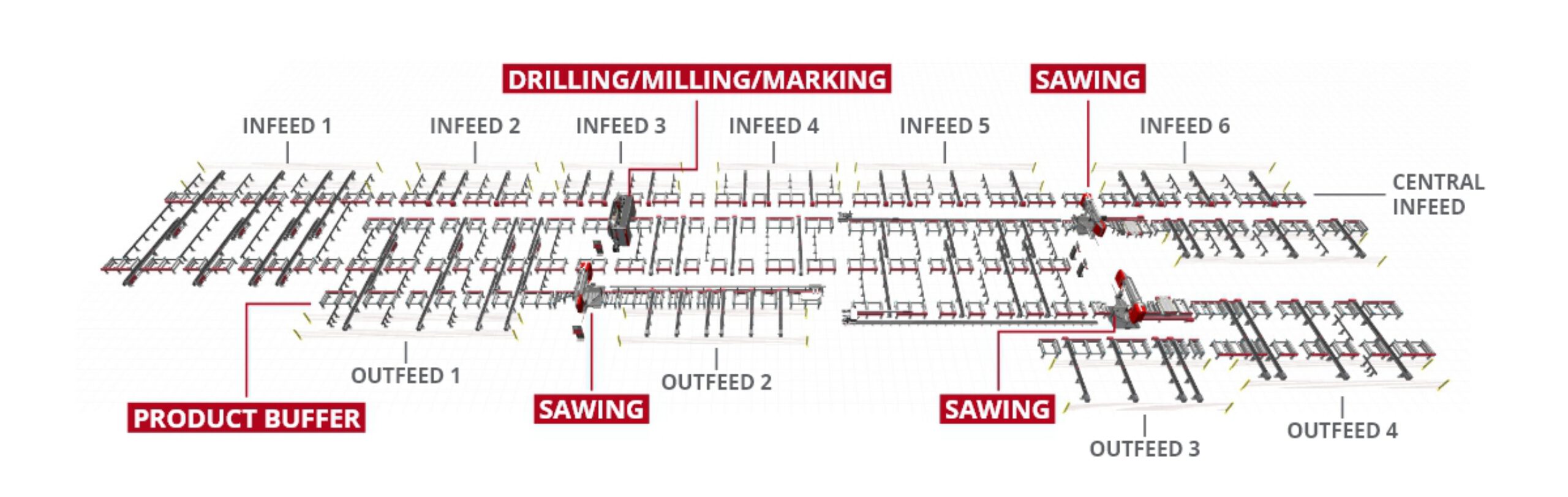
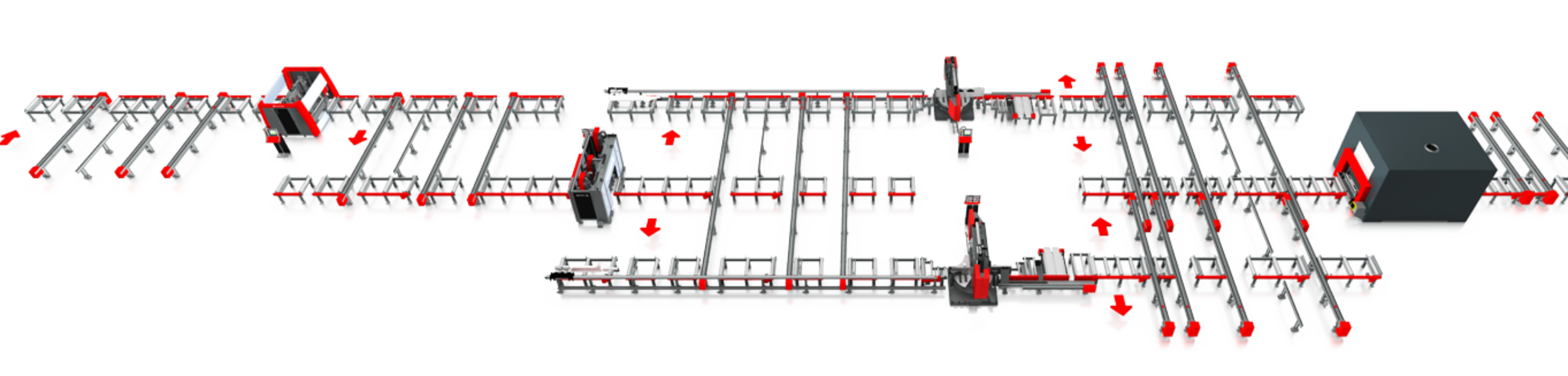
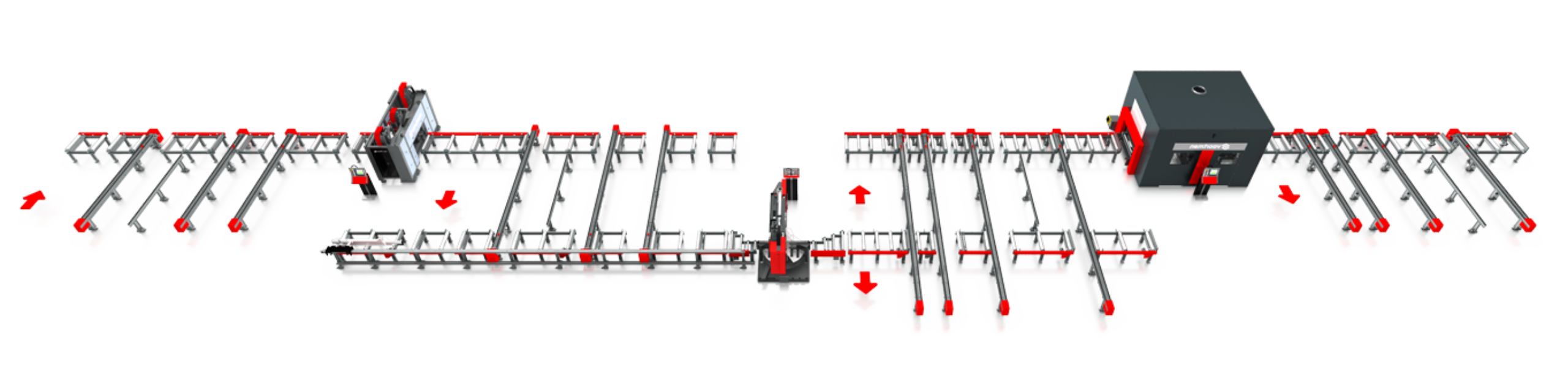
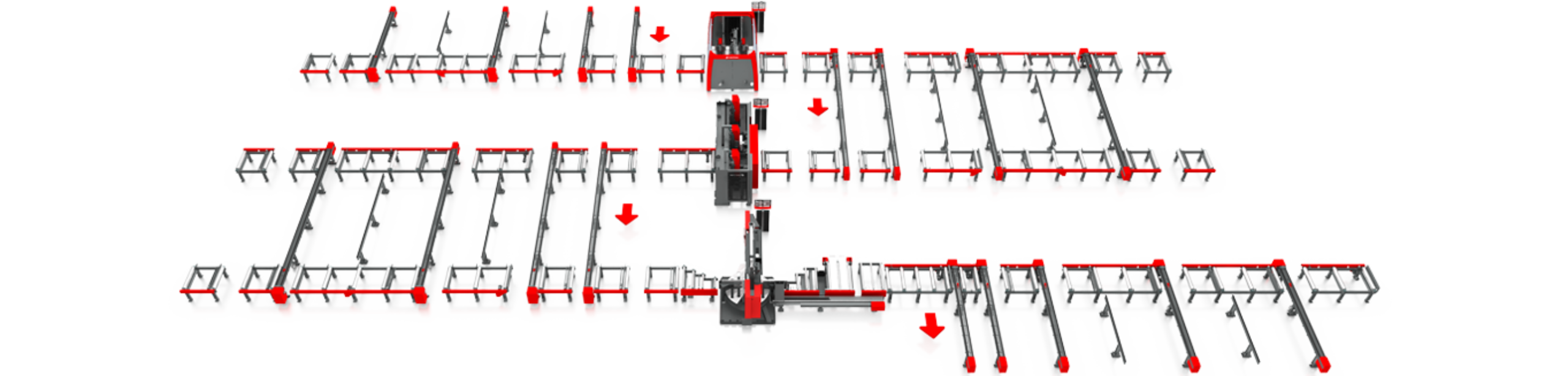
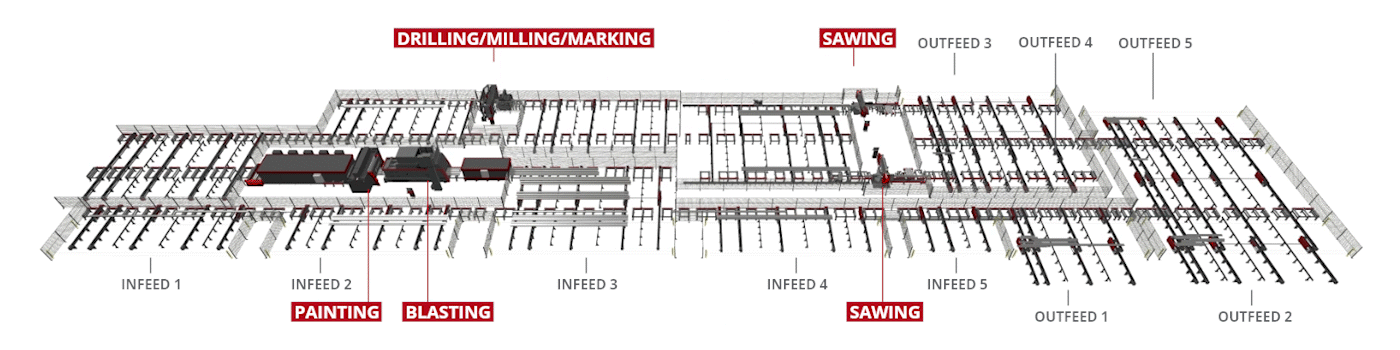
Dit voorbeeld toont de lay-out van een toonaangevende wereldwijde staalhandelaar. Deze geavanceerde productielijn bestaat uit vijf machines: twee identieke zaagmachines, de Voortman V631 boor- en freesmachine en de straal- en verflijn bestaande uit een Voortman VSB-serie en VP-serie. De creatie van deze zeer efficiënte productielijn was het resultaat van een diepgaande analyse van hun productiegegevens en productassortiment. Voortman ontwierp en beoordeelde verschillende configuraties om tot een geoptimaliseerde lay-out te komen die een gestroomlijnde bewerking van stalen profielen mogelijk maakt.
Het proces begint met profielen die volautomatisch worden gestraald en geverft, waarna ze ofwel naar de Voortman V631 gaan voor gedetailleerd boren en frezen of rechtstreeks naar een van de twee VB serie zagen, die beide zijn uitgerust om efficiënt korte producten te verwijderen. Deze bewerking maakt deel uit van een efficiënte workflow waarbij profielen al gebufferd en automatisch getransporteerd worden naar de volgende machine in de lijn of naar een van de uitvoerlocaties. Daar aangekomen versnellen de Smart Unloading schermen het sorteerproces aanzienlijk door eenvoudig weer te geven welke profielen klaar zijn voor verzending naar de klant. De volledige lijn zorgt voor traceerbaarheid van het product, waardoor ze altijd controle houden en betrouwbare levertijden kunnen garanderen.
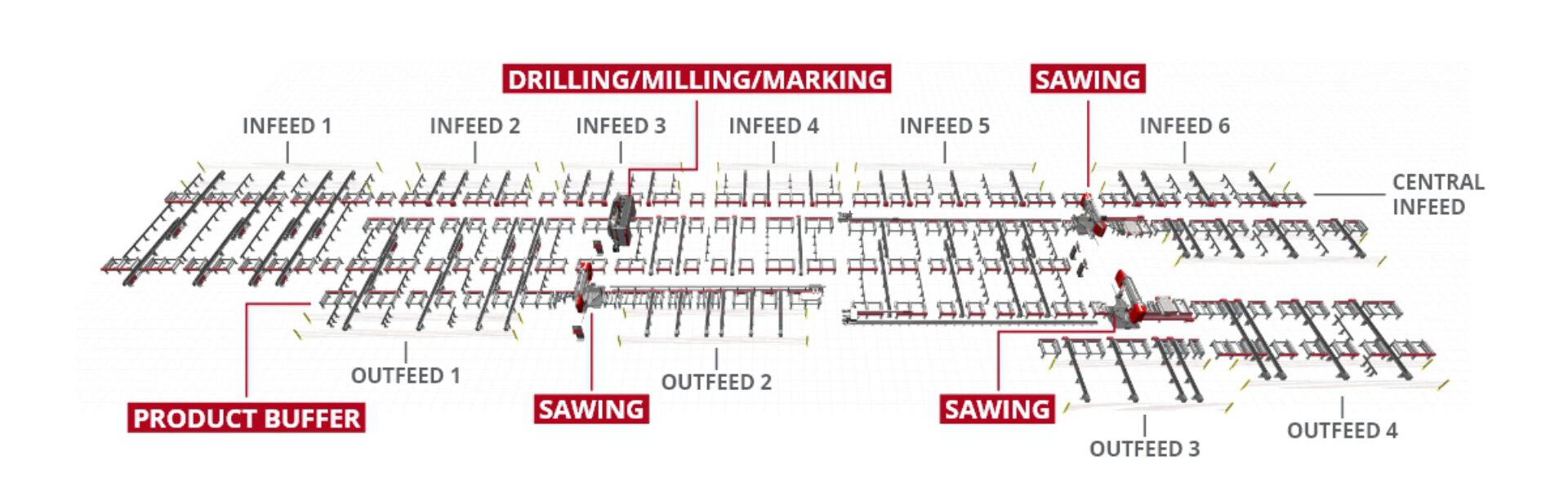
Dit voorbeeld toont de lay-out en configuratie bij een grote plaatbewerker. Een team van experts onderkende de behoefte aan optimalisatie en ontwikkelde met succes een zeer efficiënte lay-out waarmee profielen vanuit zes verschillende hallen in verschillende invoerlocaties geladen kunnen worden. Dit innovatieve ontwerp draait om strategisch geplaatste invoer- en uitvoerlocaties, evenals de naadloze integratie van gespecialiseerde machines en gestroomlijnde processen.
De Voortman V631 boor- en freesmachine en Voortman VB1250 bandzagen met een automatisch systeem voor het verwijderen van korte producten hun taken effectief uit. Daarnaast maakt een speciale route met de Voortman VB1250 bandzaag het mogelijk om grote volumes profielen en bundels te zagen. Tijdrovende materiaalbewegingen, bottlenecks en ingewikkelde logistiek worden geëlimineerd. Dankzij intelligent buffermanagement, load balancing principes en efficiënte routing kan het systeem gedurende langere perioden autonoom werken, waardoor een maximale doorvoer wordt gegarandeerd. Bovendien is de zaagcapaciteit twee keer verdubbeld en wordt de kraancapaciteit efficiënter gebruikt. De aanzienlijke toename in output markeert een aanzienlijke vooruitgang in het logistieke proces, wat resulteert in snelle doorlooptijden en een betere concurrentiepositie - van voorraad tot eindproduct.
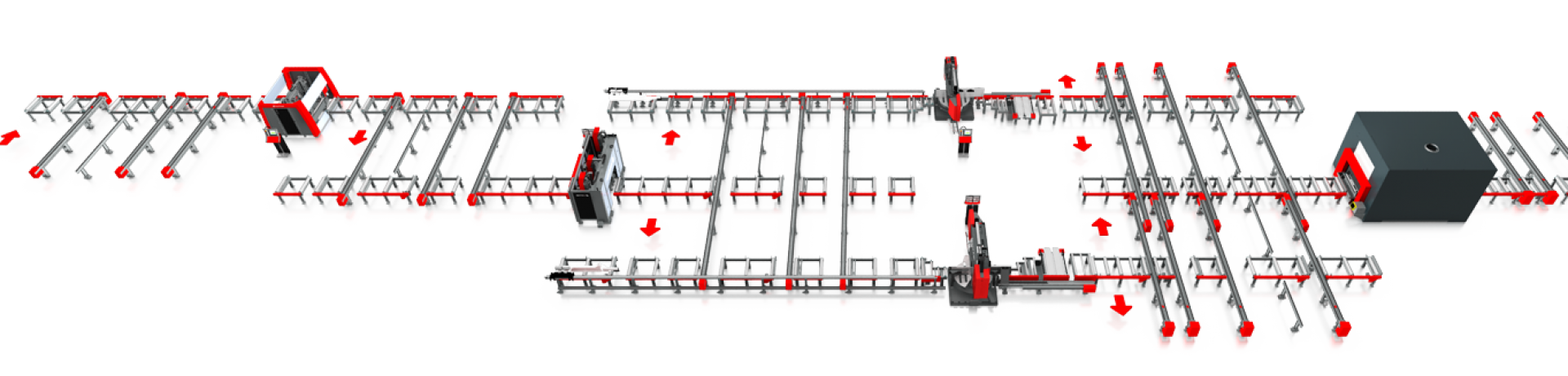
Dit voorbeeld toont de lay-out en configuratie bij een grotere staalbouwer. Uit Voortman's analyse bleek dat deze klant veel markeerwerk in zijn productie had, dus werd een aparte V704 markeermachine aanbevolen voor de lay-out. Door deze strategische stap kan de V704 zich richten op het markeren van profielen, die vervolgens worden doorgestuurd naar de V630 of V631 om te boren. Door de twee zagen iets verder in de productielijn plaatsen in plaats van aan het begin heeft het als voordeel dat ze sneller kunnen produceren omdat er minder metingen aan de voorkant nodig zijn. Ruwe profielen over de hele lengte kunnen door de markeer- en boorsystemen zonder te hoeven stoppen om te meten.
Uit de analyse bleek verder dat deze klant een hoger dan gemiddeld aantal zaagsneden uitvoert, wat een sterk argument is om te investeren in een zeer automatisch zaagproces met twee zagen en een afvoersysteem voor korte producten (SPRS) op basis van volume. Gemarkeerde en geboorde profielen kunnen gelijktijdig op lengte worden gezaagd en korte stukken worden automatisch zijwaarts getransporteerd. Wanneer er ravelingen nodig zijn, worden profielen automatisch via invoer dwarstransporten naar de raveelmachine verplaatst voor verdere bewerking, zoals het maken van ravelingen of het voorbereiden van lasnaadvoorbereidingen.
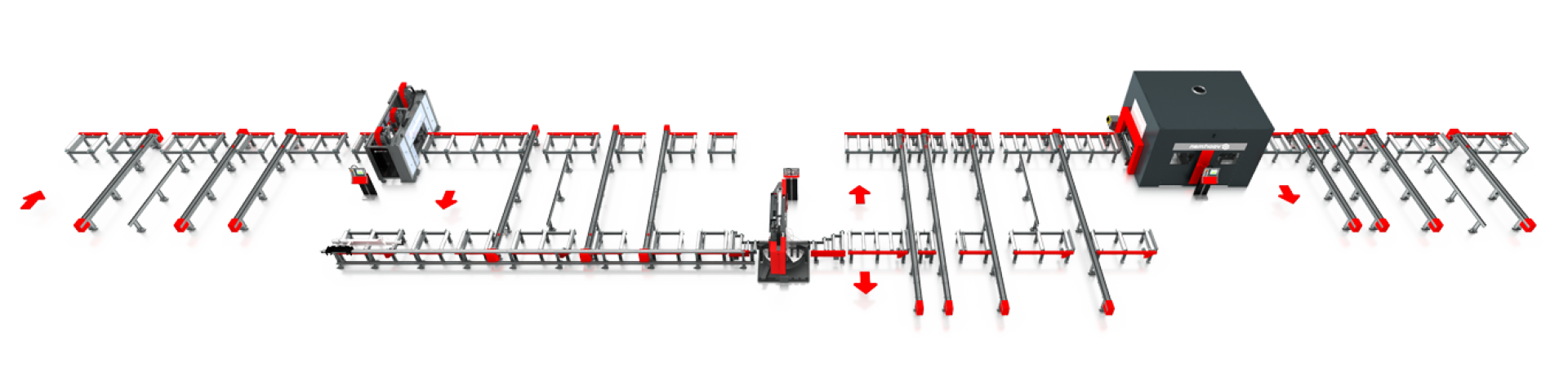
Dit voorbeeld toont een lay-out en configuratie van een middelgrote staalbouwer. In dit geval zijn geneste profielen gemarkeerd, geboord en gefreesd op de V630 / V631. Profielen gaan vervolgens automatisch naar de VB1050 zaag, waar ze op maat worden gezaagd. Afgewerkte, op maat gesneden profielen, die niet extra bewerkt hoeven te worden met de raveelmachine, kunnen na het passeren van de zaag naar rechts worden verplaatst. Wanneer de raveelmachine nodig is, worden profielen automatisch naar links getransporteerd en naar de raveelrobot verplaatst, waarna ravelingen, lasnaadvoorbereidingen, layout-markeringen en andere complexe snedes kunnen worden gemaakt.
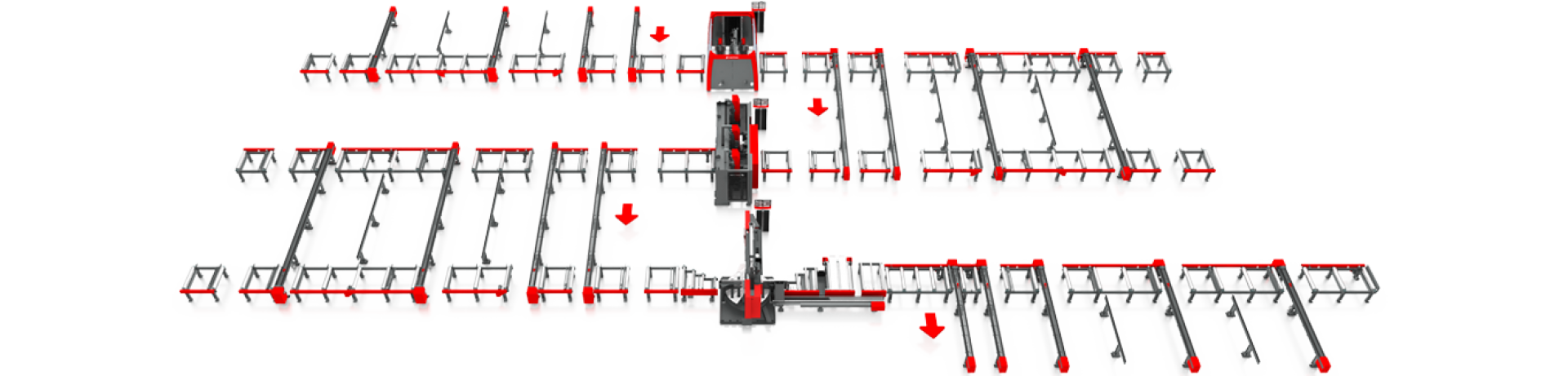
Dit voorbeeld toont een lay-out en configuratie bij een klant met weinig ruimte in zijn werkplaats. Voortman ontwierp deze "dubbele U-vorm"-configuratie om de beschikbare ruimte maximaal te benutten. Een raveelrobot werd niet in deze machinelijn opgenomen, omdat een analyse duidelijk maakte dat deze klant niet genoeg ravelingen nodig had om de investering van zo'n machine te rechtvaardigen. Analyse wees ook uit dat het verstandig was om een aparte V704 markeermachine toe te voegen om een groot volume aan lay-outmarkering aan te kunnen. De V630- of V631-boormachine wordt zodoende uitsluitend ingezet voor boren en frezen, waardoor capaciteit en output worden verbeterd. De gemarkeerde, geboorde en gefreesde profielen worden uiteindelijk door de VB1050 zaag op lengte gezaagd en automatisch naar de zijkant verplaatst via de uitvoer dwarstransporten.
EEN COMPLEET GEAUTOMATISEERDE PRODUCTIELIJN
Laten we uw lay-out ontwerpen!
Laten we starten met het vinden van de oplossing voor uw doelen! Neem vandaag contact op voor een adviesgesprek met één van onze adviseurs! Met jarenlange ervaring, bewezen oplossingen en onze wereldwijde service, maakt u het verschil met Voortman en loop voorop in uw markt!