Verhoestraete Metalen
Du distributeur d'acier au fournisseur global innovant dans le traitement des métaux et des tôles
Témoignage Verhoestraete Metalen
- Emplacement:
- Employés:
- Machines:
- Taille du site de production:
- Roeselaere, Belgique
- 48
- Voortman V304 + V310
- 23 500 m2 sur un site de 70 000 m2
« Nous avons fait de grands progrès, non seulement au niveau des processus et de la flexibilité, mais aussi dans la réduction des délais de commande liés à cette machine. »
QUATRE GÉNÉRATIONS D'INNOVATION DANS LE TRAITEMENT DES MÉTAUX ET DES TÔLES
Alors que Verhoestraete Metalen a débuté comme distributeur d'acier en 1911, aujourd'hui, plus d'un siècle et quatre générations plus tard, l'entreprise est devenue un fournisseur global polyvalent en Belgique qui propose des solutions innovantes en matière de traitement des métaux et des tôles. Sur un vaste site de 7 hectares, l'entreprise fournit chaque jour un savoir-faire artisanal pour des projets de premier plan.
Le moment est idéal pour examiner de plus près cette croissance en discutant avec Stéphane Verhoestraete (CEO), Yves de Smet (Head of Quality & Maintenance) et Robby Delys (Sales and Backup Production Manager).
Des solutions personnalisées axées sur le client
Verhoestraete Metalen's sert une clientèle diversifiée et fournit des solutions personnalisées à des entreprises de différents secteurs, notamment l'alimentation, la construction, l'architecture et l'art. « En fait, nous ne fournissons plus de produits, mais des solutions complètes », souligne Stéphane Verhoestraete, en évoquant l'évolution de la demande des clients. Une évolution à laquelle l'entreprise répond parfaitement.
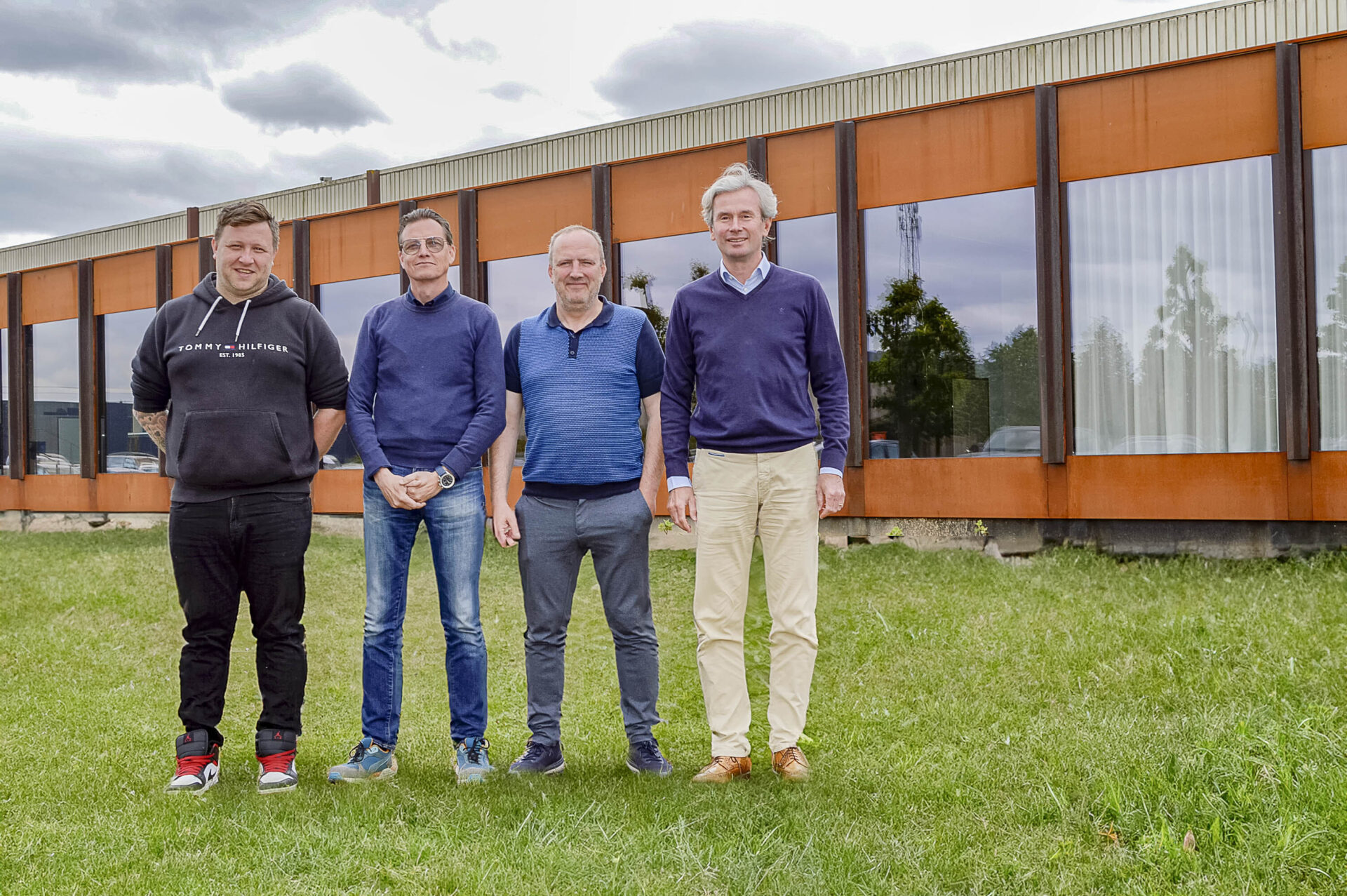
INNOVATION ET DIVERSIFICATION
Tout en restant fidèle à ses racines dans l'usinage des métaux, en réponse à l'évolution de la demande des clients, l'entreprise a considérablement diversifié ses capacités de production au cours des dernières années. L'installation d'un grand système de traitement de tôles Voortman de 28 mètres de long, composé d'une V304 et d'une V310 Voortman, en fait partie. "Les plus grandes tôles que nous traitons mesurent 12 mètres de long. Il est donc pratique que vous puissiez faire passer tout votre travail du fin à l'épais", explique Robby Delys.
Le système peut effectuer automatiquement le perçage, le taraudage, le fraisage, la découpe plasma, le chanfreinage et l'oxycoupage avec une large gamme de types et d'épaisseurs de matériaux. Auparavant, le perçage, le taraudage et la création de préparations de soudure étaient souvent effectués manuellement et sur des postes de travail distincts, ce qui entraînait un manque d'efficacité et des problèmes logistiques.
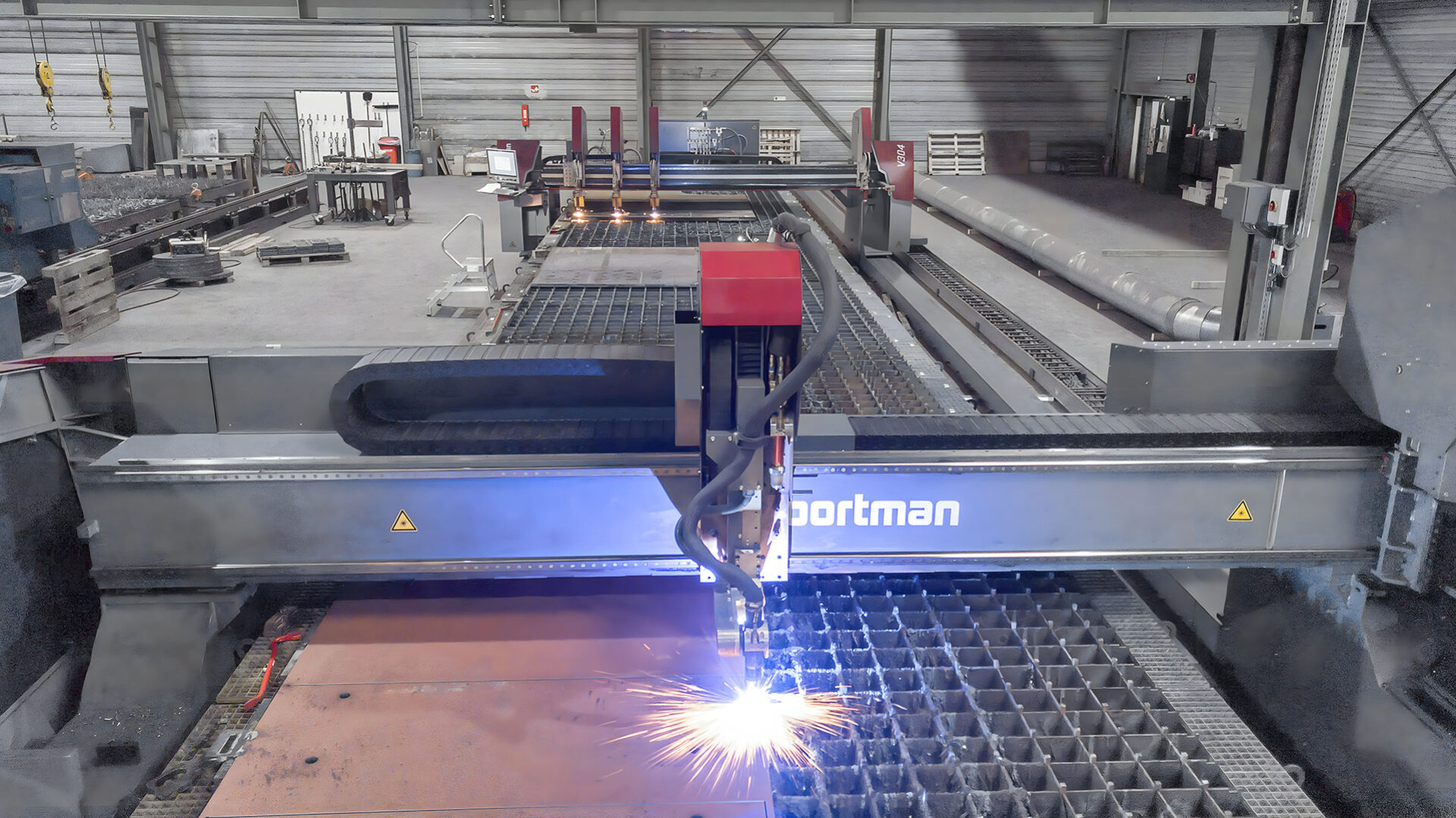
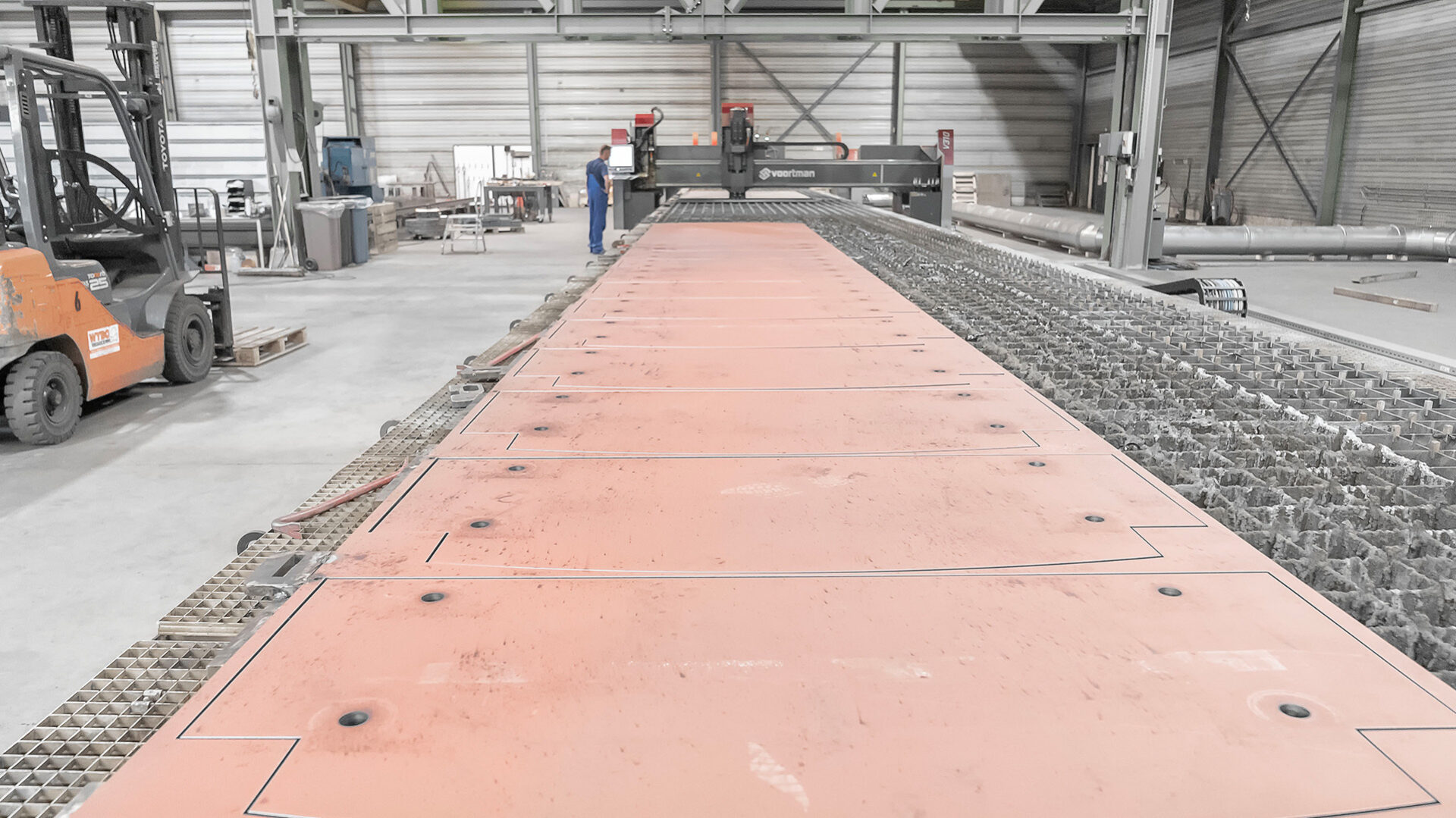
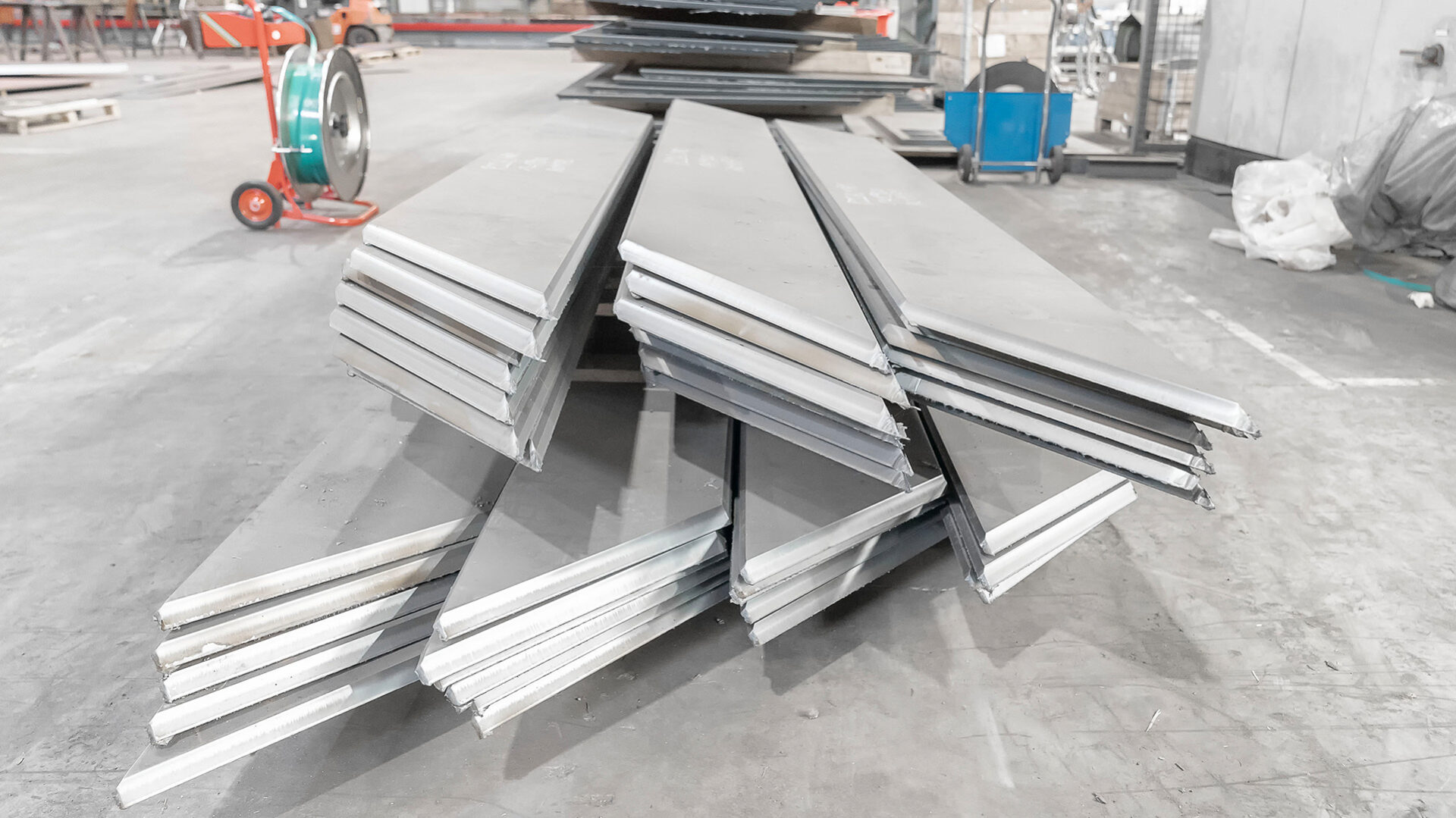
Le pont arrière découpe avec 3 torches oxyfuel, tandis que le pont avant découpe une longue tôle avec du plasma.
Les pièces sont découpées dans la longue tôle, les trous étant d'abord percés, ce qui permet de poursuivre la découpe sans discontinuité
Des préparations de soudure parfaites créées par simple pression d'un bouton.
Robby Delys en donne un exemple : « Il est regrettable que nous n'ayons pas encore la machine pour un projet à l'époque. Nous travaillions sur un projet de réservoirs d'eau où les extrémités des tôles devaient avoir une préparation de soudure. Nous devions à chaque fois éloigner les tôles du laser pour leur donner un chanfrein, puis déplacer à nouveau la tôle pour la laminer. Aujourd'hui, avec la machine pour tôles de Voortman, tout peut être fait sur un seul système, puis la tôle est roulée. Si nous avions eu cette machine à l'époque, elle nous aurait fait gagner beaucoup de temps et nous aurait permis de travailler de manière beaucoup plus efficace. »
« Les opérations de perçage et de taraudage se déroulent même sans personnel et principalement pendant la nuit, grâce à des logiciels avancés », précise Yves De Smet. La productivité et l'efficacité se sont considérablement améliorées, tout comme la qualité et le contrôle de l'ensemble du processus de production. « Nous avons fait de grands progrès, non seulement au niveau des processus et de la flexibilité, mais aussi en réduisant les délais de commande liés à cette machine », déclare Stéphane Verhoestraete.
FIERS ET MOTIVÉS
Outre l'efficacité, les opérateurs constatent également une amélioration significative de la facilité d'utilisation. Cela se traduit par une motivation accrue. « Les opérateurs sont fiers de la machine, ils peuvent aussi vraiment réfléchir à un certain nombre de choses, par exemple allez-vous percer le jour ou la nuit, quels sont les risques, que signifie un scénario par rapport à l'autre. Cela leur permet de trouver des solutions et des idées intéressantes », a déclaré Stéphane Verhoestraete.
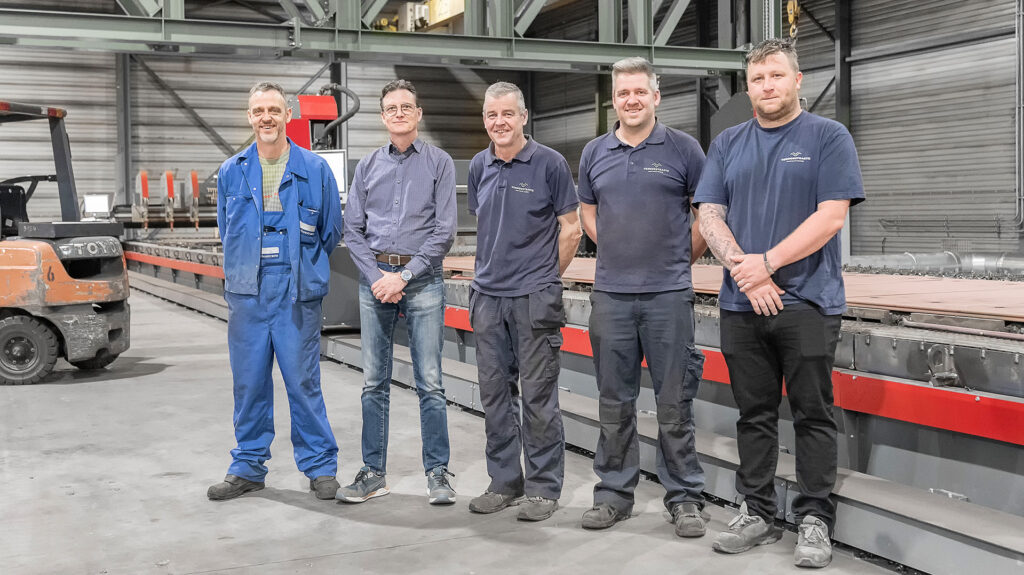
LA CAPACITÉ DE RÉALISER DES PROJETS PLUS NOMBREUX ET PLUS VARIÉS
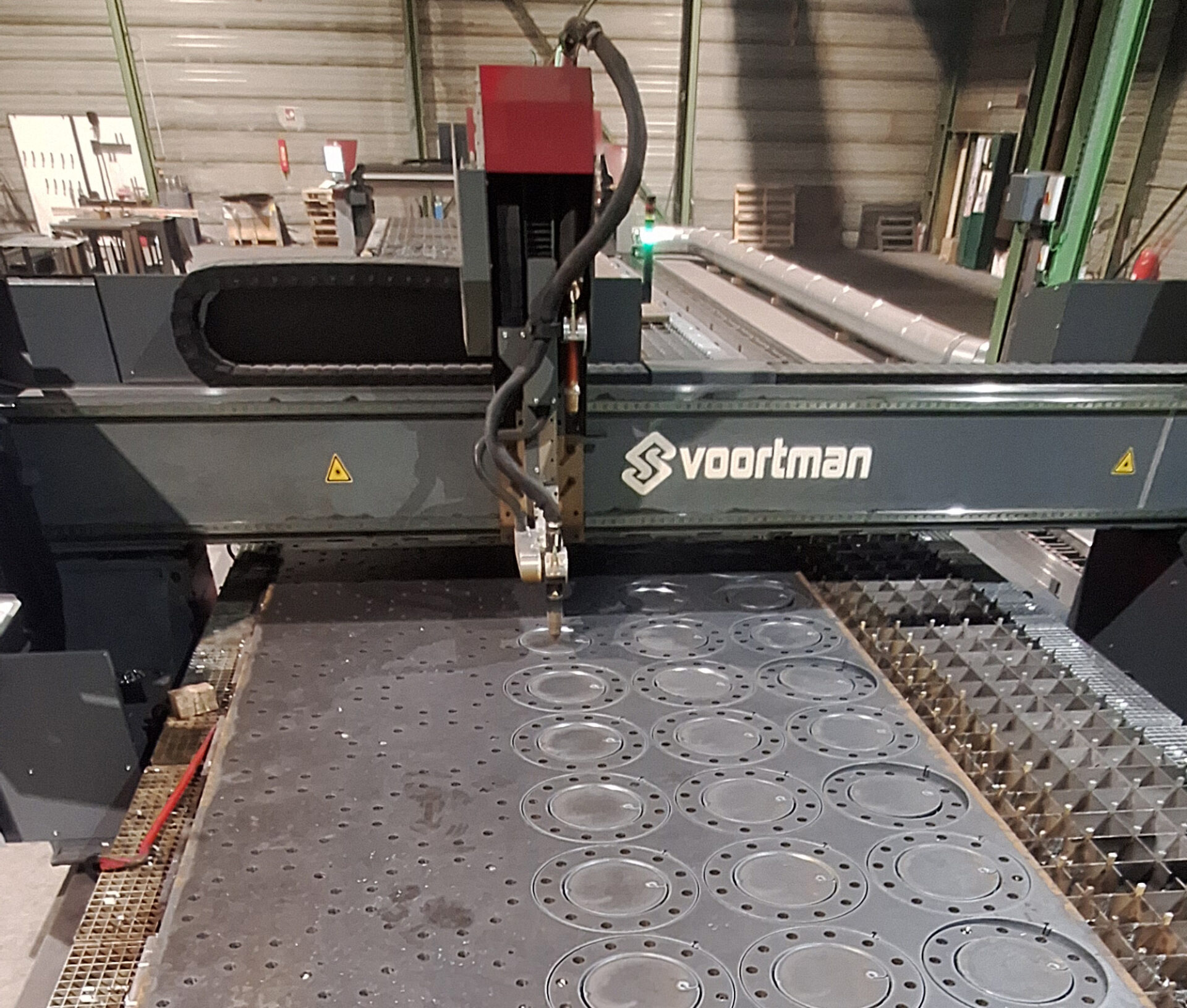
Les nouveaux processus automatisés tels que la coupe en chanfrein, le perçage et le fraisage permettent à Verhoestraete de prendre en charge des projets plus importants et plus complexes. Par exemple, ils ont récemment travaillé sur le projet illustré ici, qui a nécessité la création de plus de 1 000 trous, ce qui aurait été impossible avec le processus de perçage manuel dans l'ancienne situation. « Nous avons également un très gros projet d'éoliennes en mer, un projet que nous n'aurions jamais pu réaliser avec l'ancien système, compte tenu du nombre de pièces, de la rapidité et du délai de livraison souhaités », explique Delys.
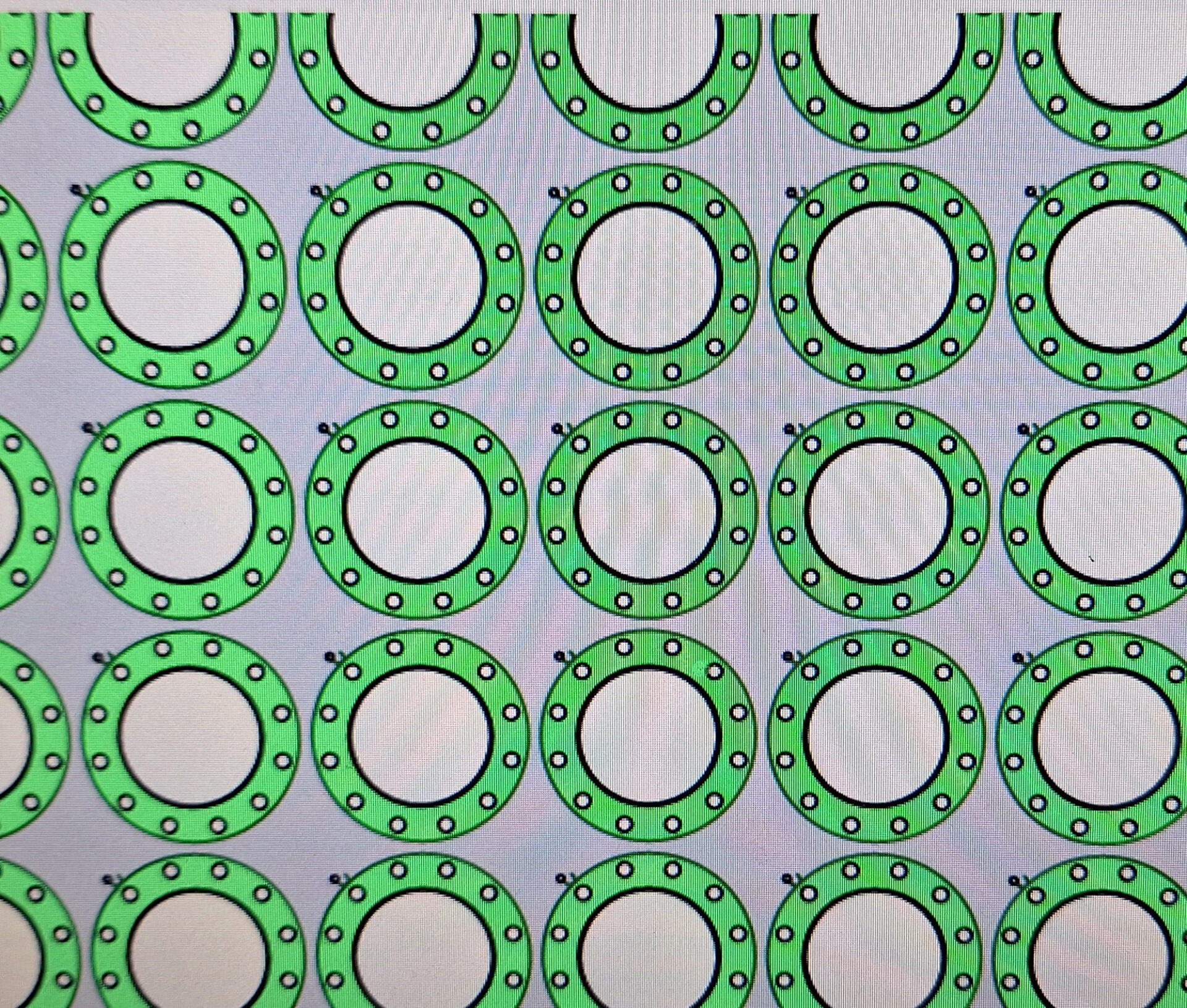
UN ONE-STOP-SHOP POUR SE DÉCHARGER DE SES RESPONSABILITÉS
Grâce à l'investissement dans la machine combinée tout-en-un de Voortman, les pièces de haute qualité sont livrées prêtes à être assemblées par le client. « Ainsi, dès que le produit sort du camion sur le site du client, ce dernier peut commencer le soudage et l'assemblage, c'est notre intention », déclare De Smet. « Alors qu'auparavant nous coupions les tôles et devions les renvoyer au client pour une finition supplémentaire ou les faire terminer par des tiers, nous pouvons désormais faire tout cela en interne. » Stéphane Verhoestraete poursuit : « En tant que centre multi service, nous voulons pouvoir décharger le client. Cette décharge va au-delà de l'ajout de valeur par le biais de la production et des opérations. Nous réfléchissons également avec le client dans le cadre du processus de conception, Verhoestraete agissant comme une extension pour les clients qui ne disposent pas de leur propre bureau d'études. » Une forme merveilleuse de co-ingénierie et de partenariat, dans laquelle l'idée du one-stop-shop s'exprime encore davantage.
LE MATCH AVEC VOORTMAN EST LÀ
Avant de procéder à l'investissement final, Verhoestraete a visité le campus Voortman à Rijssen. « La visite et la démonstration ont donné beaucoup de nouvelles idées. Il était également agréable de voir que Voortman utilise également les machines qu'ils développent eux-mêmes pour créer diverses pièces de leurs propres machines » , déclare De Smet.
La coopération avec Voortman est jugée très positive. « La machine et le service qui l'accompagne sont excellents ; il s'agit d'un ensemble complet qui est vraiment recommandé », explique Delys. « En outre, la façon dont Voortman envisage les logiciels et la numérisation est importante pour la concordance avec notre vision stratégique », ajoute Stéphane Verhoestraete.
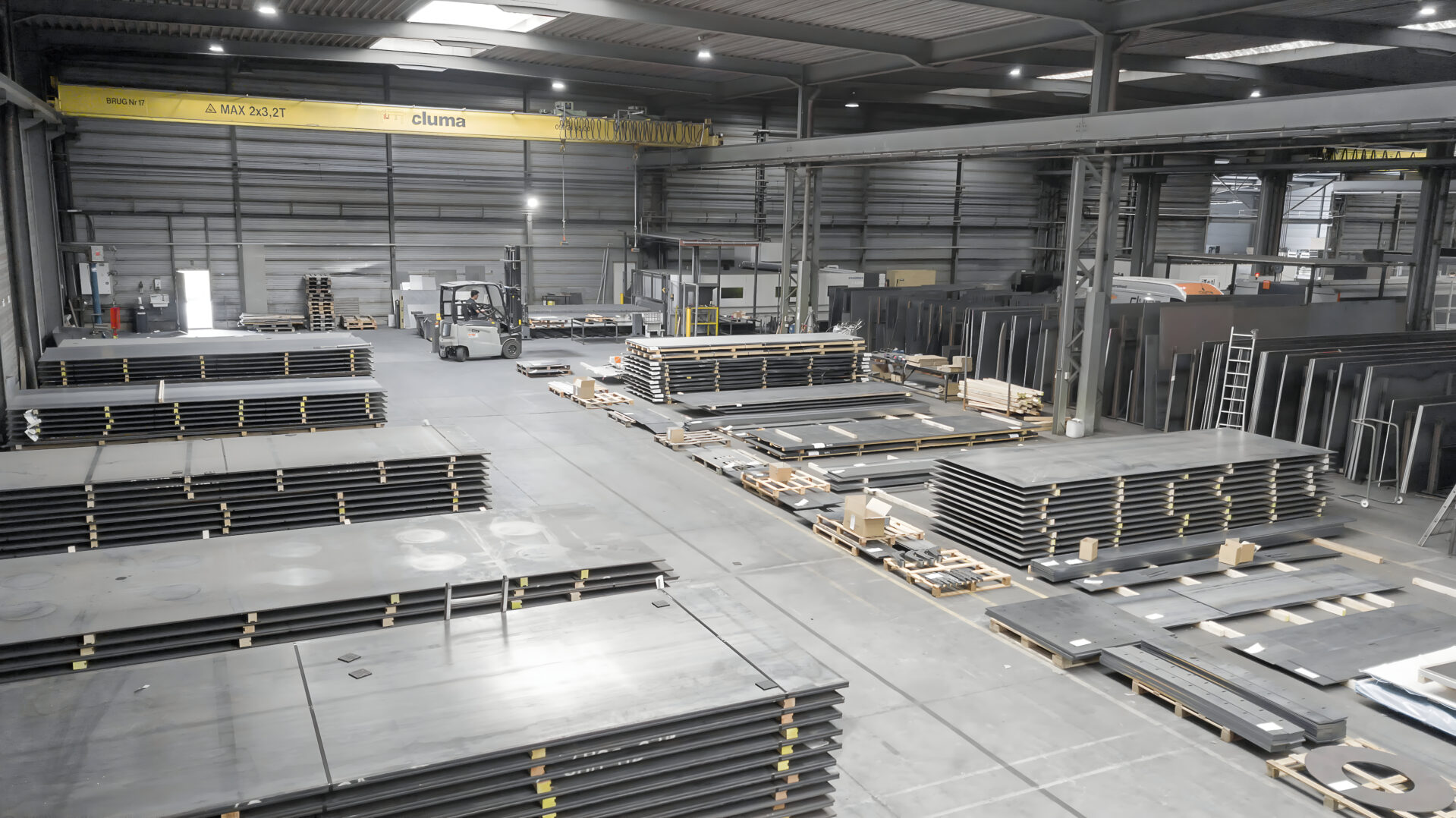
QUE NOUS RÉSERVE L'AVENIR ?
Au cours des prochaines années, Verhoestraete se concentrera sur la poursuite de l'automatisation, de la numérisation et de l'optimisation de ses processus de production. Il s'agira notamment d'adapter les logiciels afin d'automatiser davantage la partie frontale du processus de production et de repenser l'ensemble du flux dans l'atelier. Et qui sait, peut-être que cela ira de pair avec de nouvelles machines et de nouveaux logiciels....