Verhoestraete Metalen
From steel distributor to innovative total supplier in metal and plate processing
Testimonial Verhoestraete Metalen
- Location:
- Employees:
- Machines:
- Size of production:
- Roeselaere, Belgium
- 48
- Voortman V304 + V310
- 23,500 m2 on 70,000 m2 site
“We have made great strides, not only at the process level and flexibility, but also in reducing order lead times linked to this machine.”
FOUR GENERATIONS OF INNOVATION IN METAL AND PLATE PROCESSING
Where Verhoestraete Metalen began as a steel distributor in 1911, today, more than a century and four generations later, the company has grown into a versatile total supplier in Belgium that offers innovative solutions in metal and plate processing. On a vast 7-acre site, the company delivers craftsmanship for top projects every day.
A perfect time to take a closer look at this growth by talking with Stéphane Verhoestraete (CEO), Yves de Smet (Head of Quality & Maintenance), and Robby Delys (Sales and Backup Production Manager).
Customer-focused customized solutions
Verhoestraete Metalen's serves a diverse client base, providing customized solutions to companies in various sectors, including food, construction, architecture, and art. “Actually, we no longer supply products, we supply complete solutions” stresses Stéphane Verhoestraete, pointing to the shift in customer demand. Something the company is seamlessly responding to.
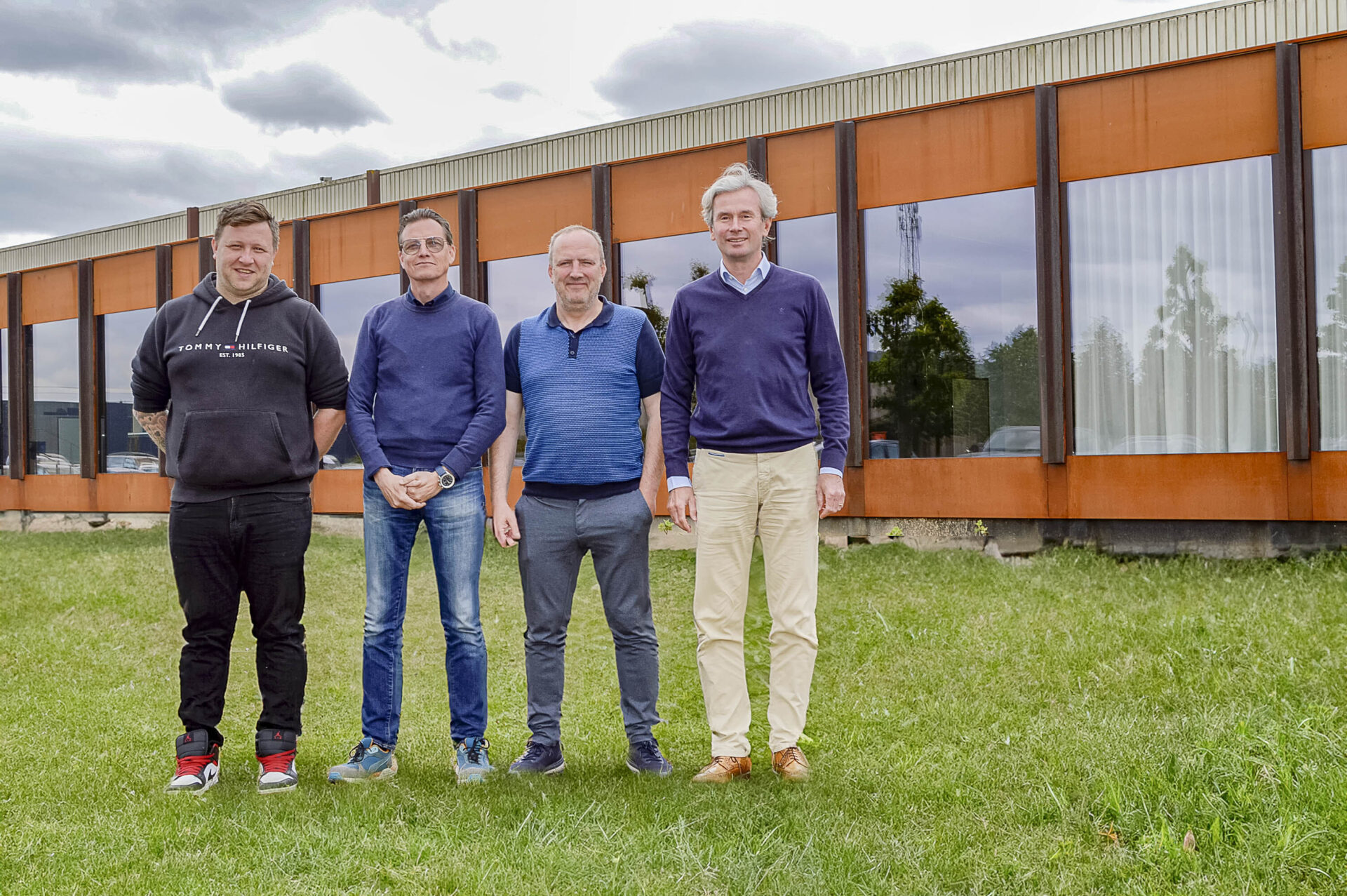
INNOVATION AND DIVERSIFICATION
While remaining true to its roots in metal processing, in response to changing customer demand, the company has significantly diversified its production capabilities in recent years. Part of this is the installation of a large 28-meter-long Voortman plate processing system, consisting of a Voortman V304 and V310. "The biggest plates we process are 12 meters long. So it's convenient that you can shift all your work from thin to thick,” Robby Delys explains.
The system can automatically perform drilling, thread tapping, milling, plasma cutting, bevel cutting and oxy-fuel cutting with a wide range of material types and thicknesses. Previously, drilling, thread tapping and the creation of weld preparations were often performed manually and at separate workstations, creating inefficiencies and logistical challenges.
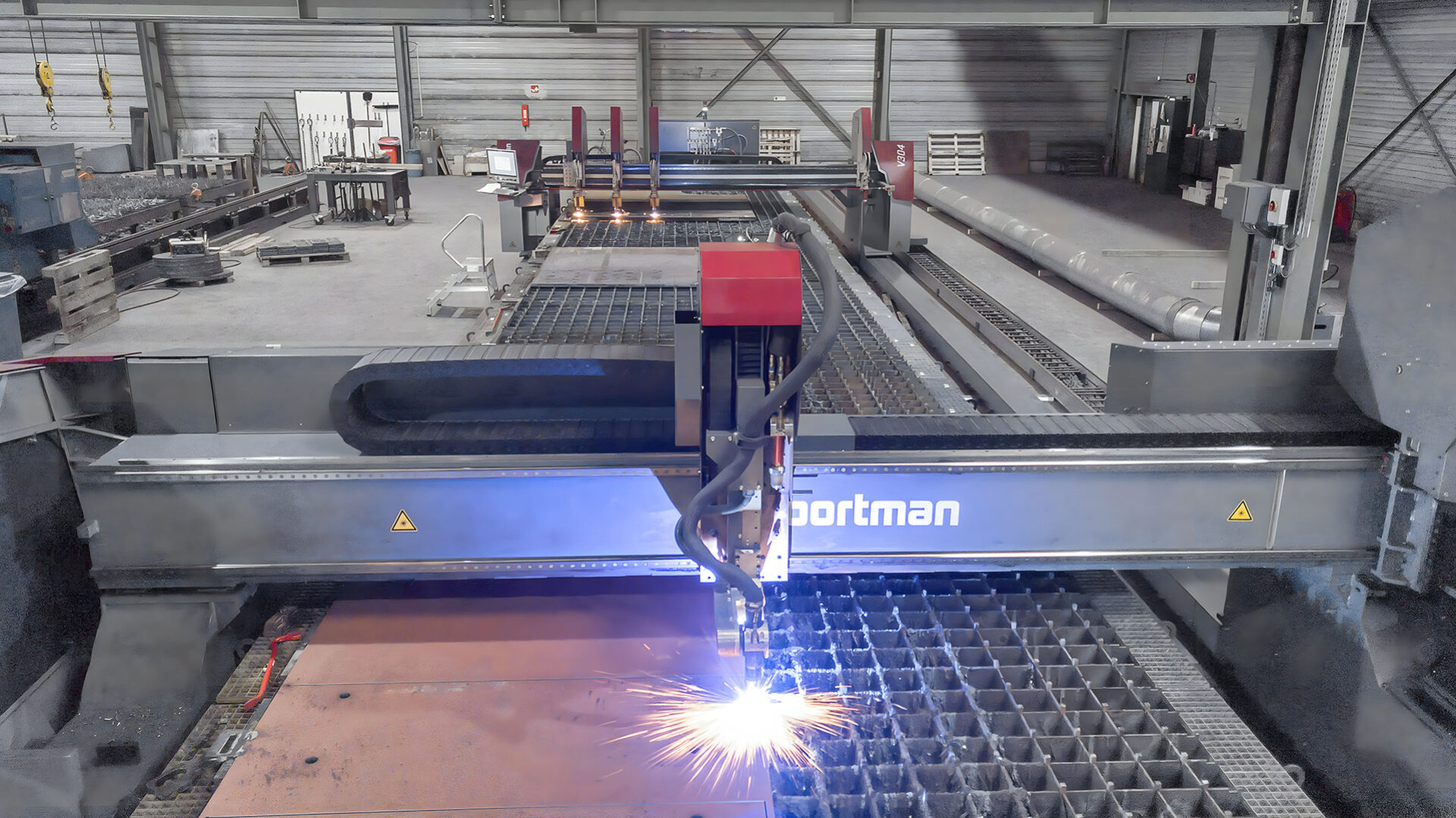
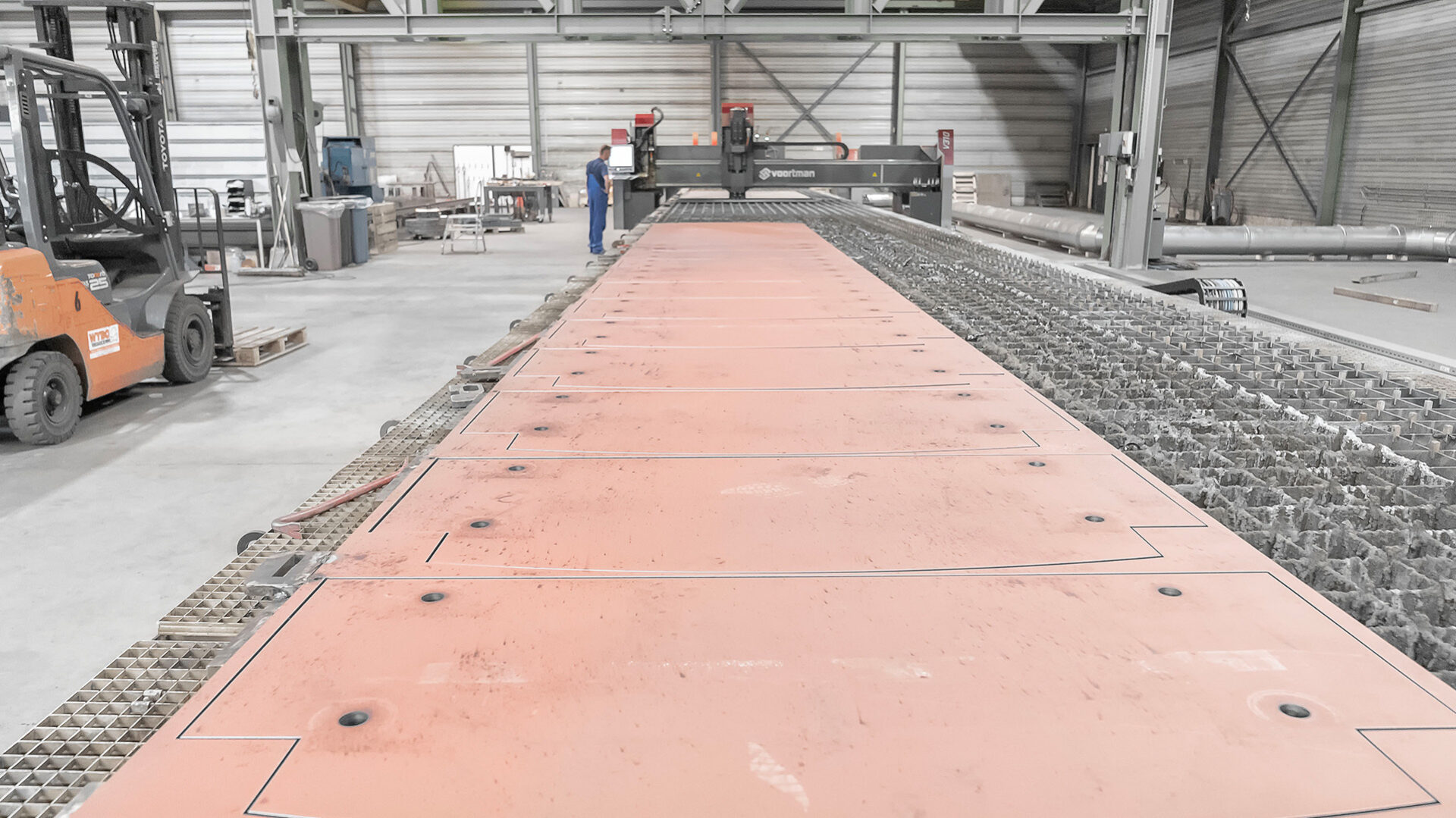
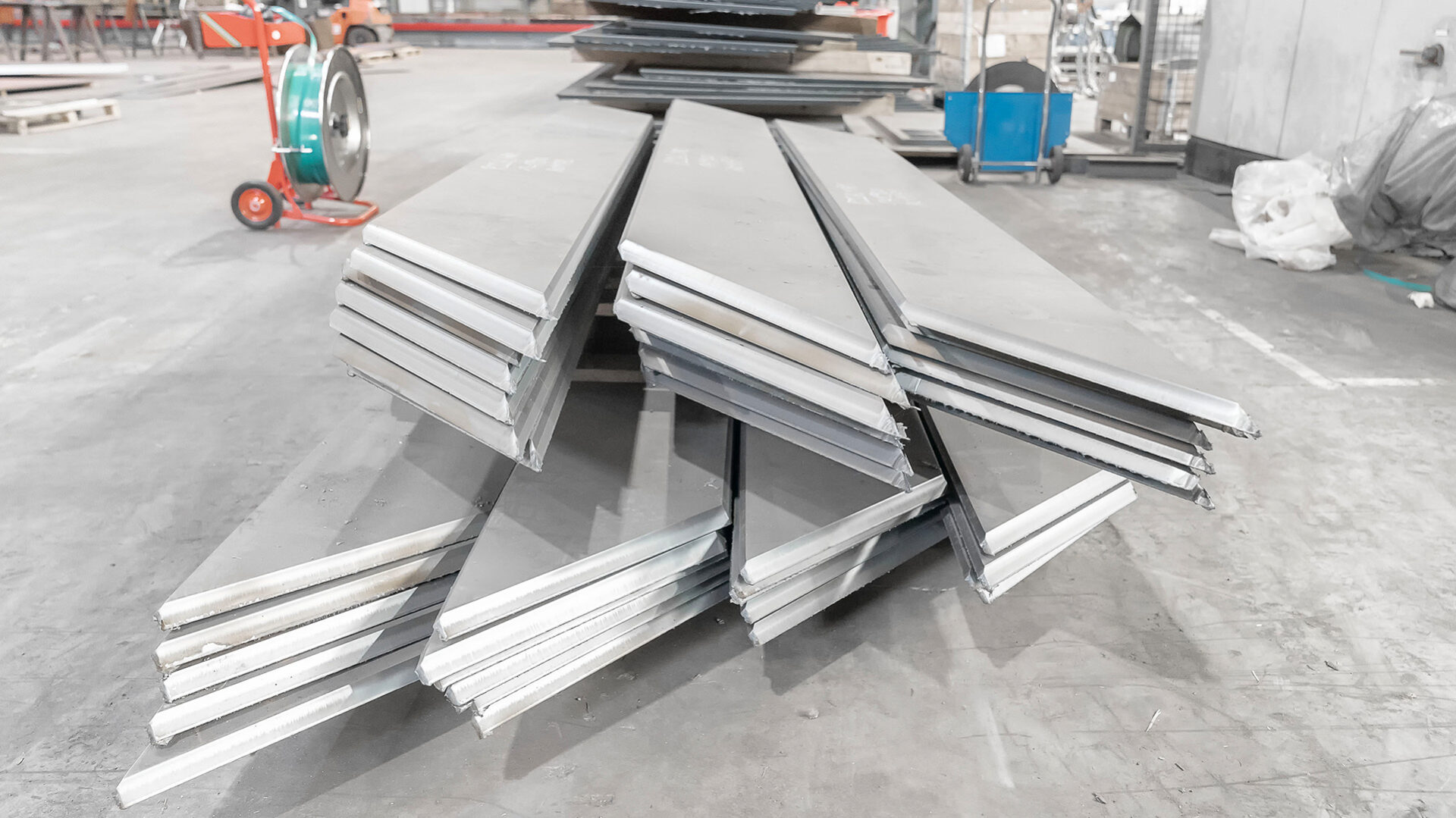
The rear bridge cuts with 3 oxyfuel torches, while the front bridge cuts a long plate with plasma.
Parts are cut from the long plate, with holes pre-drilled first, allowing for a seamless continuation of the cut
Perfect weld preparations created at the touch of a button.
Robby Delys outlines an example: “It is unfortunate that we did not yet have the machine for one project at the time. We were working on a project for water tanks where the plates had to have a weld preparation. We had to move the plates from the laser each time to provide them with a bevel, then move the plate again to be rolled. Now with the Voortman machine, everything can be done on one system, and then it goes to the plate roller. If we had the machine back then, it would have saved us a lot of time and allowed us to work much more efficiently."
“The drilling and thread tapping operations even take place unmanned and mostly during the night, thanks to advanced software,” says Yves De Smet. Productivity and efficiency have improved significantly, as have quality and control over the entire production process. “We have made great strides, not only at the process level and flexibility, but also in reducing order lead times linked to this machine,” says Stéphane Verhoestraete.
PROUD AND MOTIVATED
In addition to efficiency, operators also notice a significant improvement in ease of operation. This leads to increased motivation. "The operators are proud of the machine, they can also really think about a number of things, for example are you going to drill during the day or at night, what are the risks, what does one scenario mean versus the other. They really come up with great solutions and insights because of this,” said Stéphane Verhoestraete.
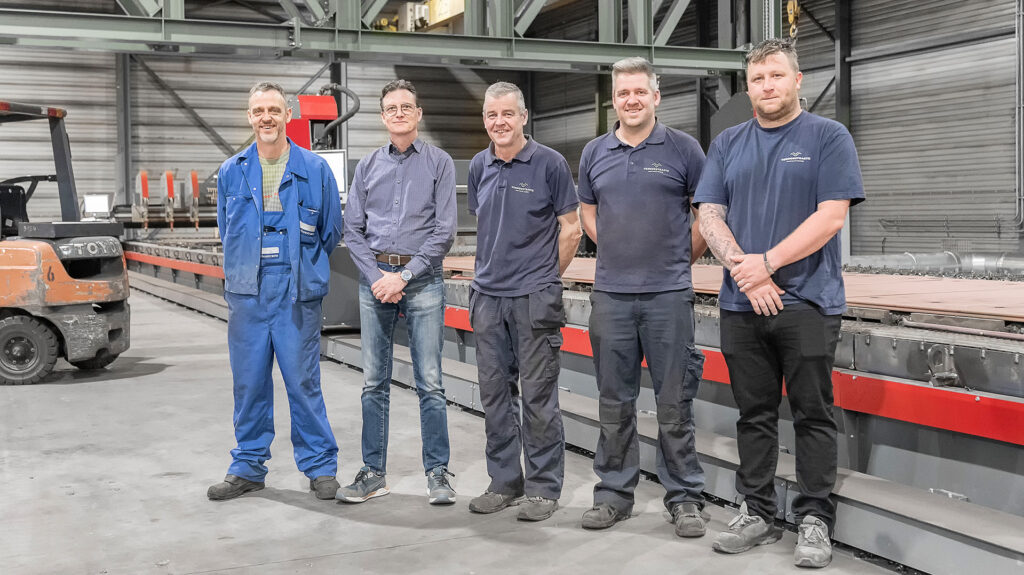
CAPACITY FOR MORE AND A VARIETY OF PROJECTS
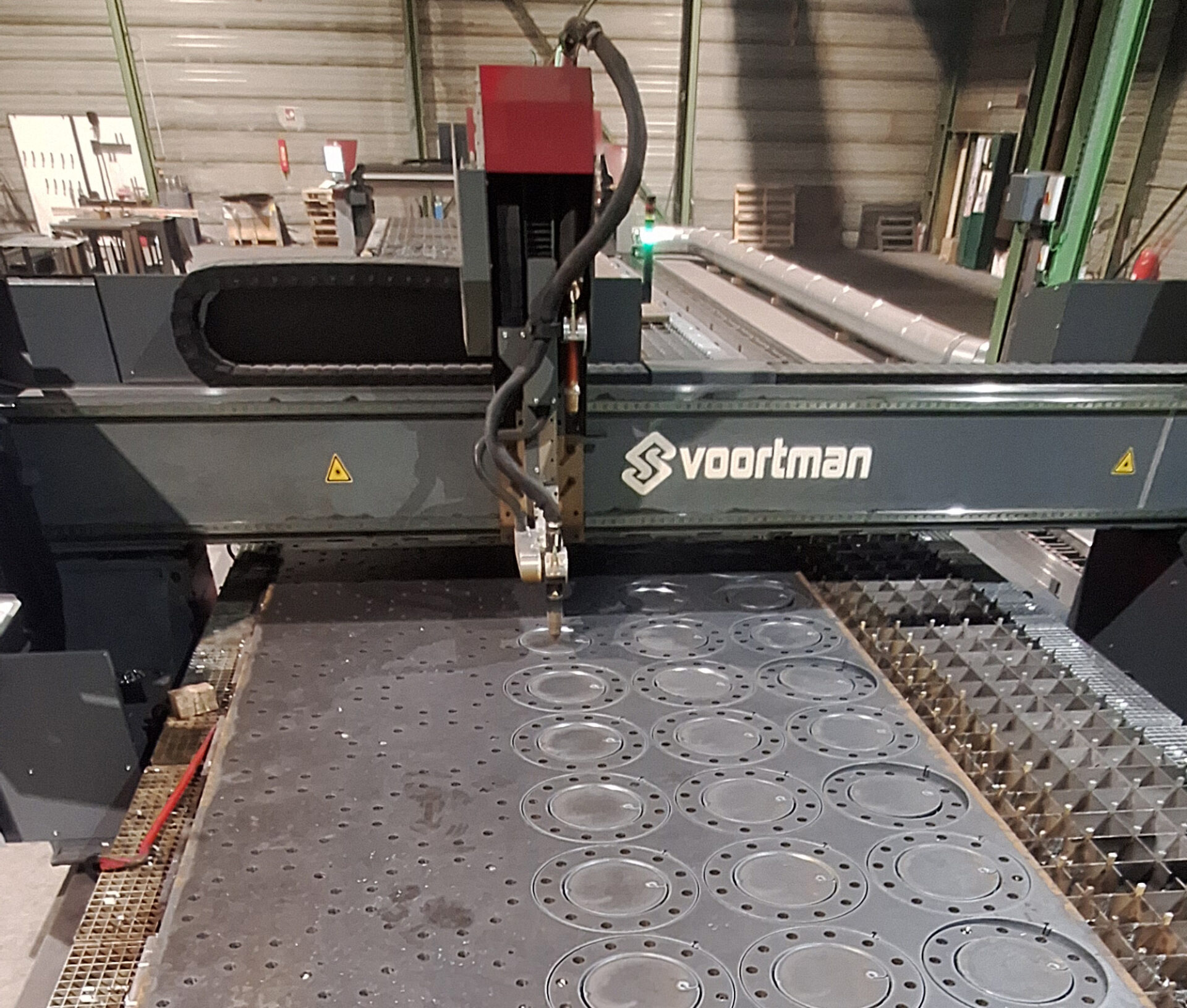
The new automated processes such as bevel cutting, drilling and milling enable Verhoestraete to take on larger and more complex projects. For example, they recently worked on the project pictured here, which required the creation of over 1,000 holes, something that would have been impossible with the manual drilling process in the old situation. “We also now have a very large project for wind turbines here at sea, which was also a project that, considering the desired number of parts, speed and lead time, we could never have done in the old situation,” Delys shares.
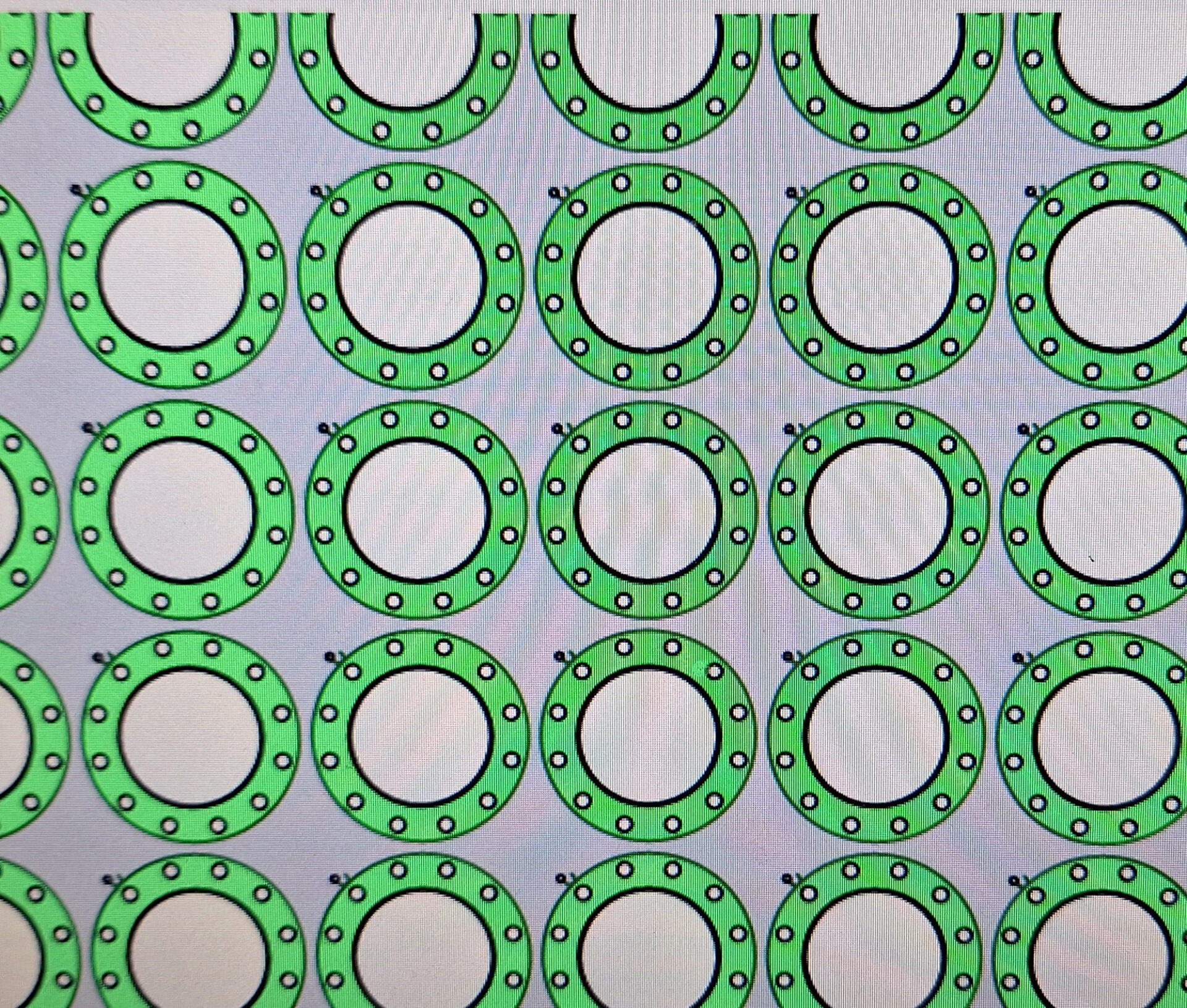
A ONE-STOP-SHOP TO UNBURDEN
With the investment in the all-in-one Voortman combi machine, high-quality parts are delivered ready for customer assembly. “So as soon as the product comes off the truck at the customer's site, the customer can start welding and assembling, that's our intention,” says De Smet. “Where we used to cut the plates and have to return them to the customer for further finishing or have them finished through third parties, now we can do all that in-house.” Stéphane Verhoestraete continues: "As a one-stop shop, we want to be able to unburden the customer.'' This unburdening goes beyond adding value through production and operations. We also think along with the customer in the design process, with Verhoestraete acting as an extension for customers without their own design office.'' A wonderful form of co-engineering and partnership, in which the one-stop-shop idea is expressed even further.
THE MATCH WITH VOORTMAN IS THERE
Before making the final investment, Verhoestraete visited the Voortman Campus in Rijssen. "The visit and demo gave many new insights. It was also nice to see that Voortman also uses the machines they develop themselves to create various parts of their own machines,” says De Smet.
The cooperation with Voortman is seen as very positive. “The machine and the service that comes with it are excellent; it is a total package that is really recommended,” explains Delys. “In addition, the way Voortman looks at software and digitalization is important for the match with our strategic vision,” adds Stéphane Verhoestraete.
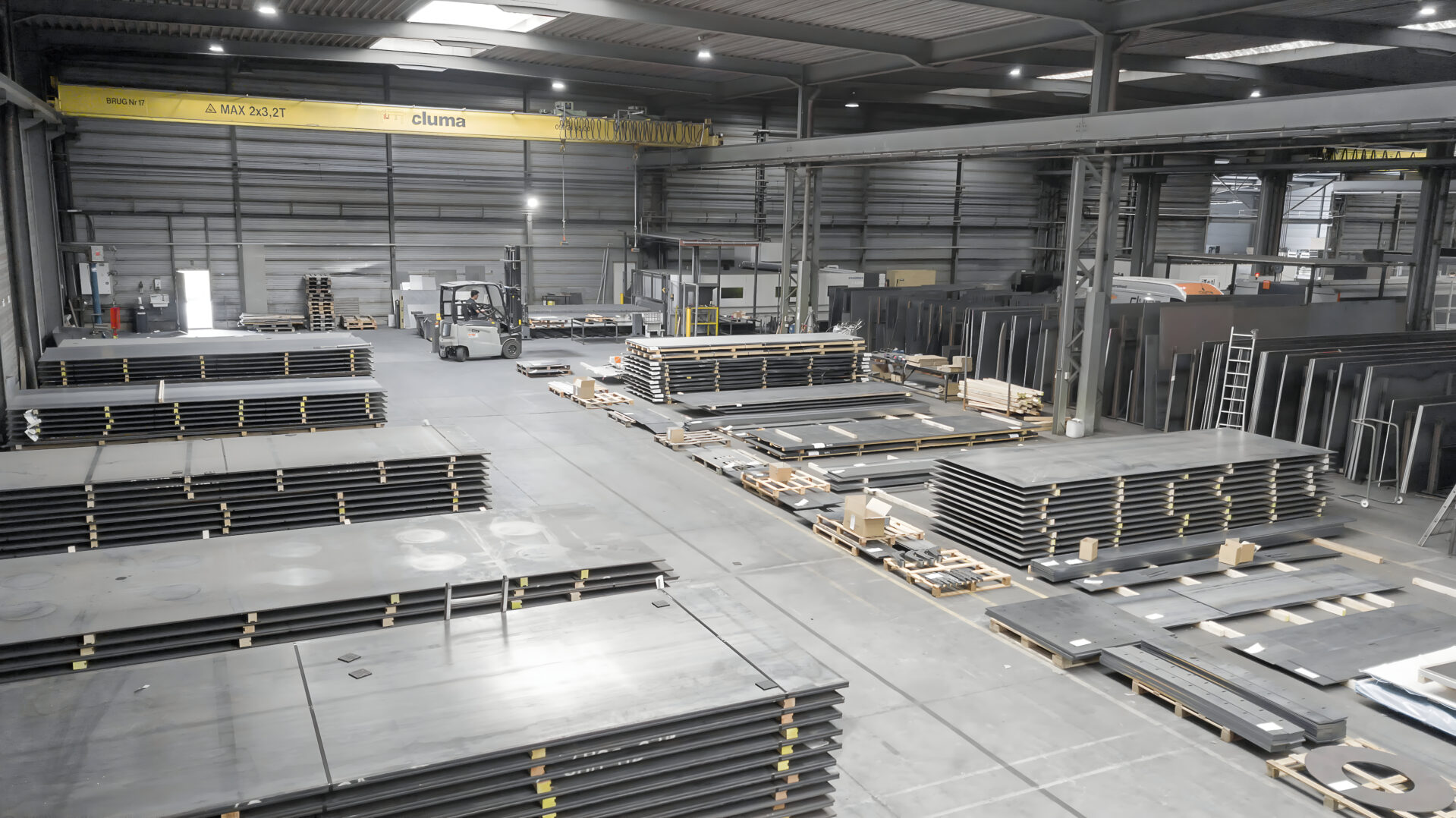
WHAT DOES THE FUTURE HOLD?
Over the next few years, Verhoestraete will focus on further automation, digitization and optimization of its production processes. This includes adapting software to further automate the front end of the production process and redesigning the entire flow in the workshop. And who knows, maybe this will go hand in hand with more new machines and software....