Snoeck Metalen
The Joint Development of the New Voortman V623
Testimonial Snoeck Metalen
- Location:
- Founded:
- Capacity:
- Employees:
- Industry:
- Wielsbeke, Belgium
- 1992
- 650 tons per month
- 80
- Steel Fabrication
"We are very proud to be the first in Belgium to use the V623. It's a fantastic addition to our workshop"
THE JOINT DEVELOPMENT OF THE NEW VOORTMAN V623
Snoeck is excited about their latest acquisition: the Voortman V623 machine. "We are very proud to be the first in Belgium and the second in Europe to use the V623. It's a fantastic addition to our workshop," says Steven Nachtergaele, manager at Snoeck, enthusiastically.
"Our company was founded in 1992 by the brothers Paul and Piet Snoeck. Since 2015, we have been part of the overarching Willy Naessens Group in Belgium," begins Steven. "We are a construction and production company with our own production workshop where we produce an average of 650 tons of steel per month." Since its inception, the production workshop was already equipped with a Voortman drill and saw line. "Later, a V550 punching/shearing machine and a V320 plasma cutter were added. We were now again looking for ways to further optimize our workshop,” Steven explains.
The collaboration with Voortman resulted in the development of the V623 drilling, milling, and sawing machine. "The V623 was actually a machine that was not yet on the market. Together with Voortman, we created a high-performance machine that has a high degree of autonomy and greatly benefits our production process," Steven explains.
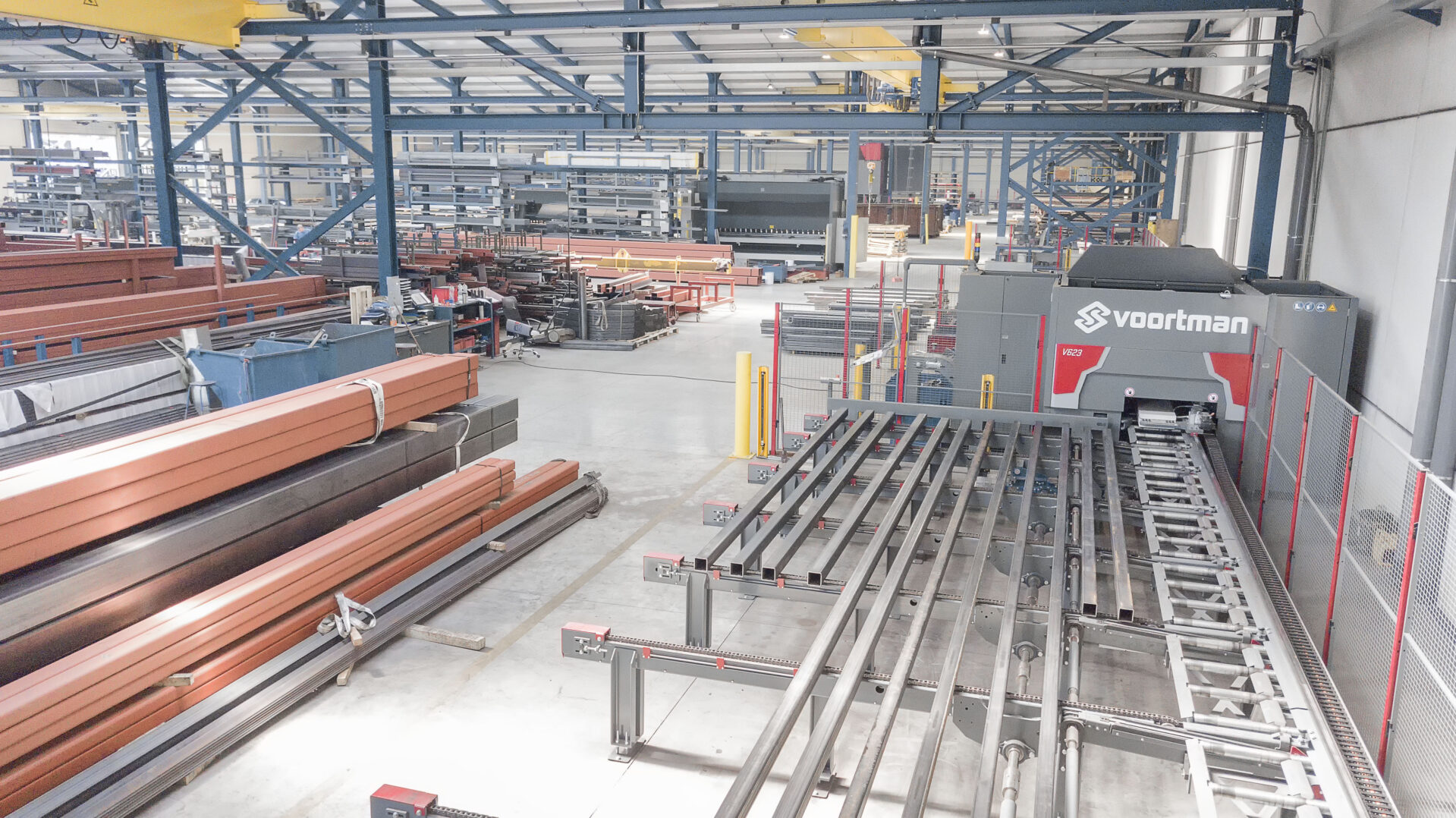
THE IMPACT OF THE VOORTMAN V623 ON SNOECK'S WORKFLOW
The decision to develop a new machine proved to be a great success. Dominiek, Factory Production Control at Snoeck, shares his experiences and enthusiasm about the new addition.
TRIPLED CAPACITY
"The final result has exceeded all our expectations. The machine performs better than we could have ever dreamed, and our production capacity has not doubled but almost tripled," says Dominiek proudly. "The new machine is not only extremely user-friendly but also works much more autonomously and faster."
The Voortman V623 is specifically designed for continuous unmanned production and can effortlessly handle a wide range of profile dimensions. Thanks to the new innovative gripper wagon, almost all clamping limitations and operator interventions during profile feeding are eliminated. "Loading the machine is very simple and very safe. The new gripper system ensures that there is no fixed zero line anymore so that even slightly bent profiles are processed effortlessly, which is a huge step forward for our production capacity," Dominiek explains.
Additionally, the machine has a central tool storage that accommodates an impressive 42 tools. These 42 tools can be used by all drilling units, resulting in increased autonomy.
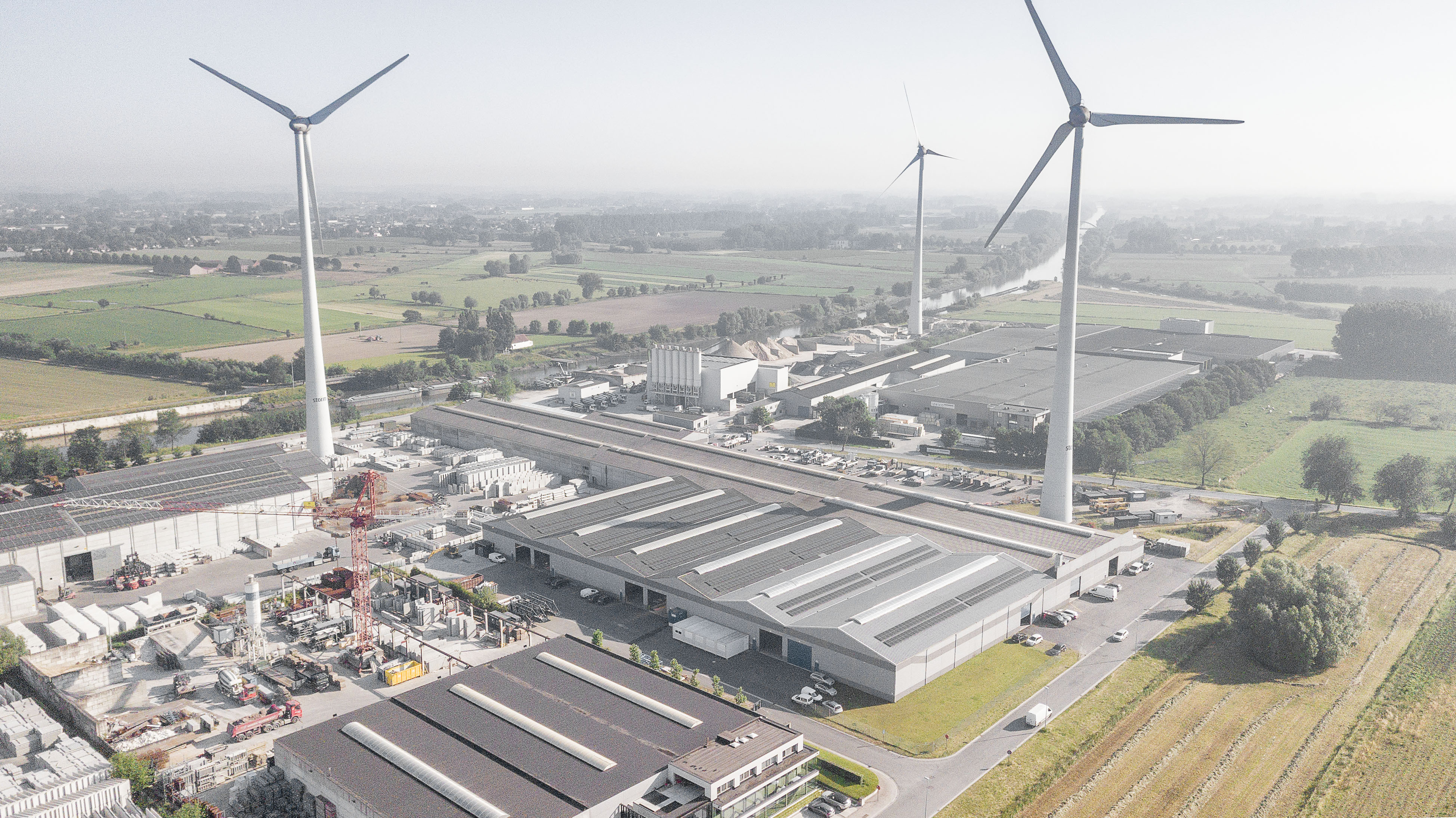
Snoeck, a construction and production company with an average of 650 tons of steel per month.
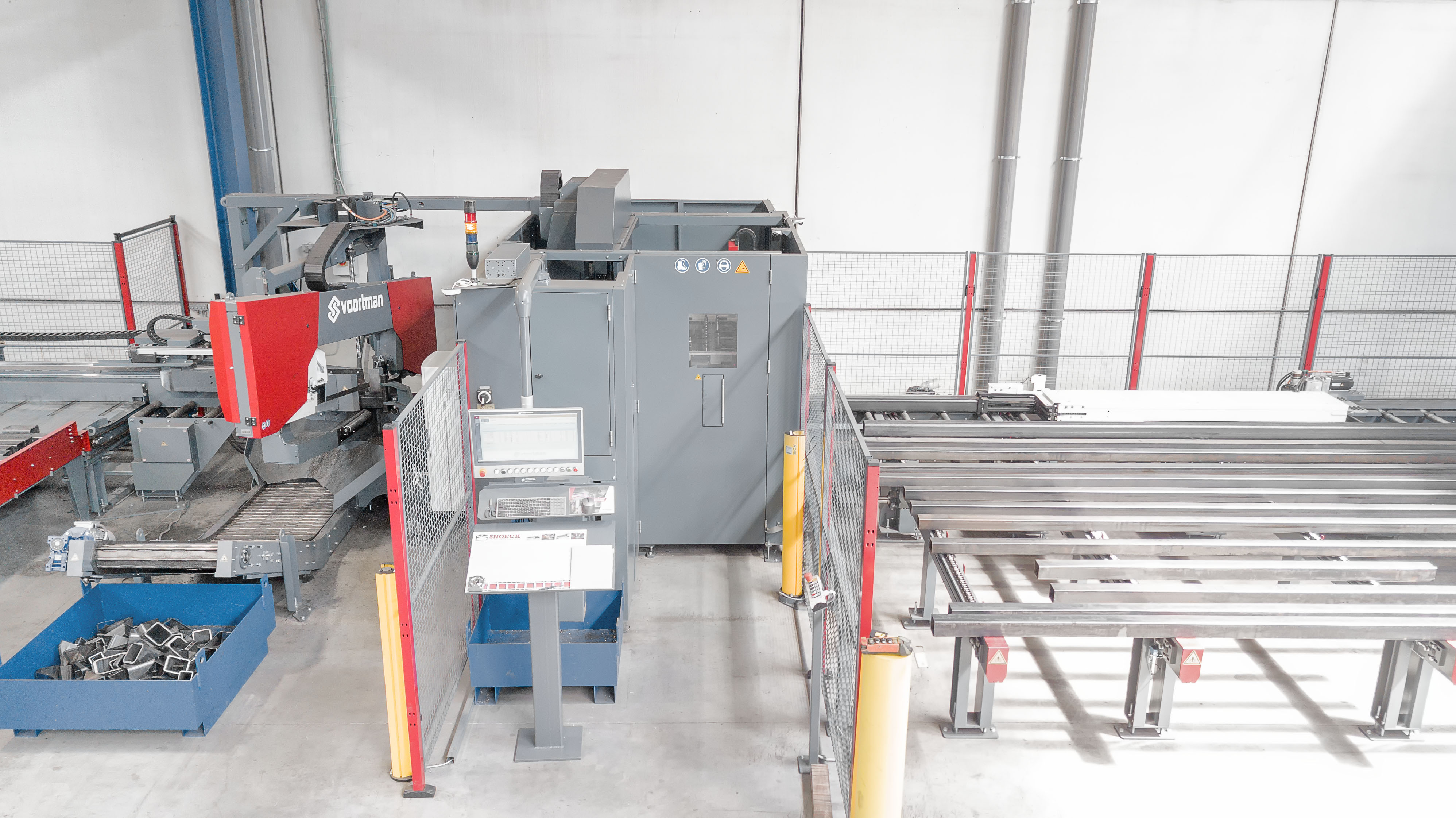
Thanks to the new innovative gripper wagon, a wide variety of profiles are automatically fed in without operator intervention.
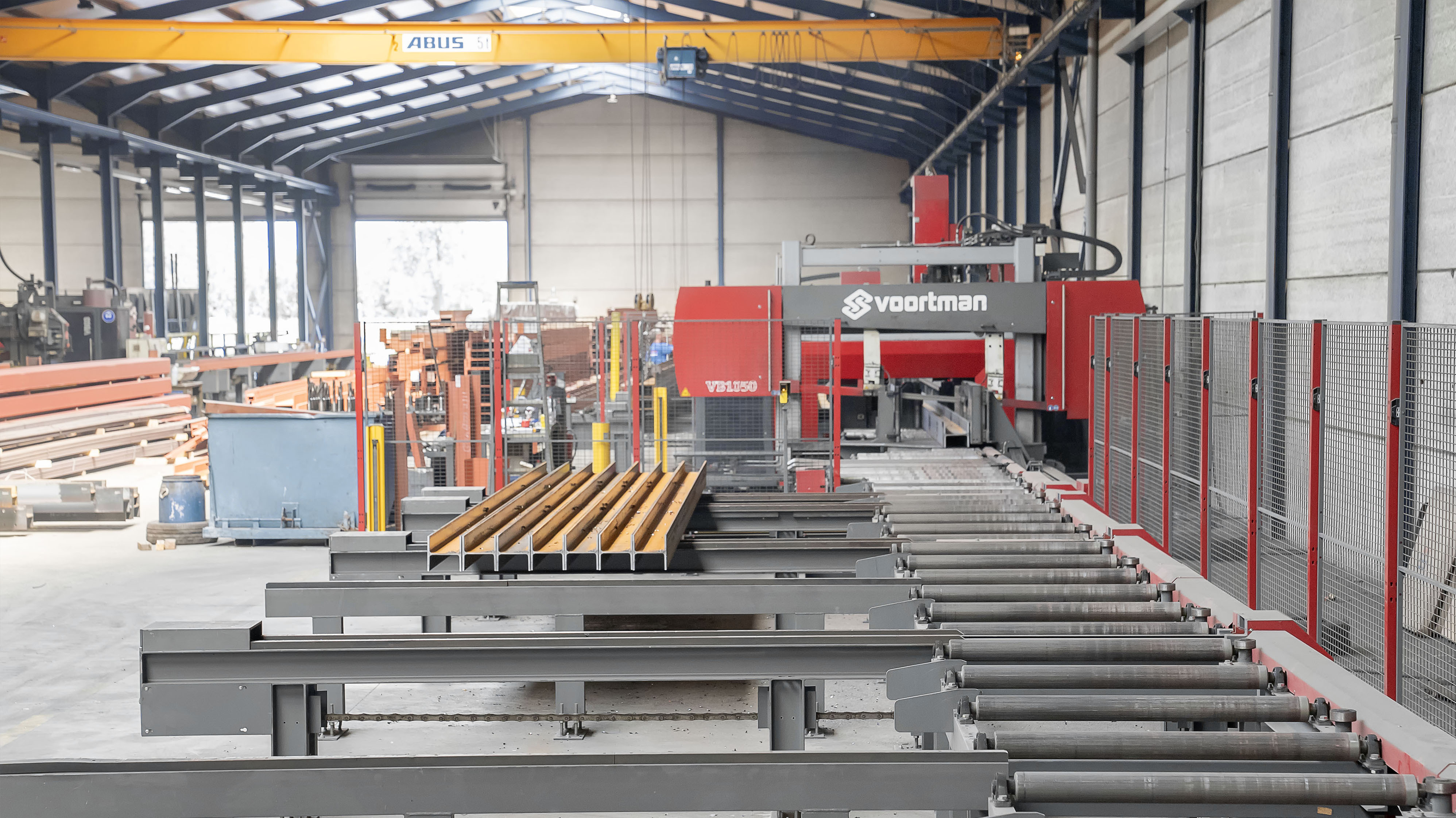
The existing Voortman drill and saw line, now the primary station for all beams. Thanks to this division, Snoeck can speak of a tripling in capacity!
THREE OUTPUT ZONES
A remarkable aspect of the V623 is the ability to process profiles with a double mitre cut. "The machine automatically feeds the square tubes through, and the second gripper takes them over at the back, allowing us to make a perfect saw cut behind the gripper without any problems," Dominiek explains.
The system uses three different zones for output. In the first zone, all clean cuts and short products are automatically discharged with a conveyor belt under the saw. The second zone contains a discharge system with two sections up to 600 mm, and in the third zone, products of different lengths are precisely positioned on the outfeed
"This is done according to the project or in the most space-saving way," explains Dominiek. "The discharge is fully tailored to our type of product. Voortman carefully analyzed our production process and determined the optimal flow."
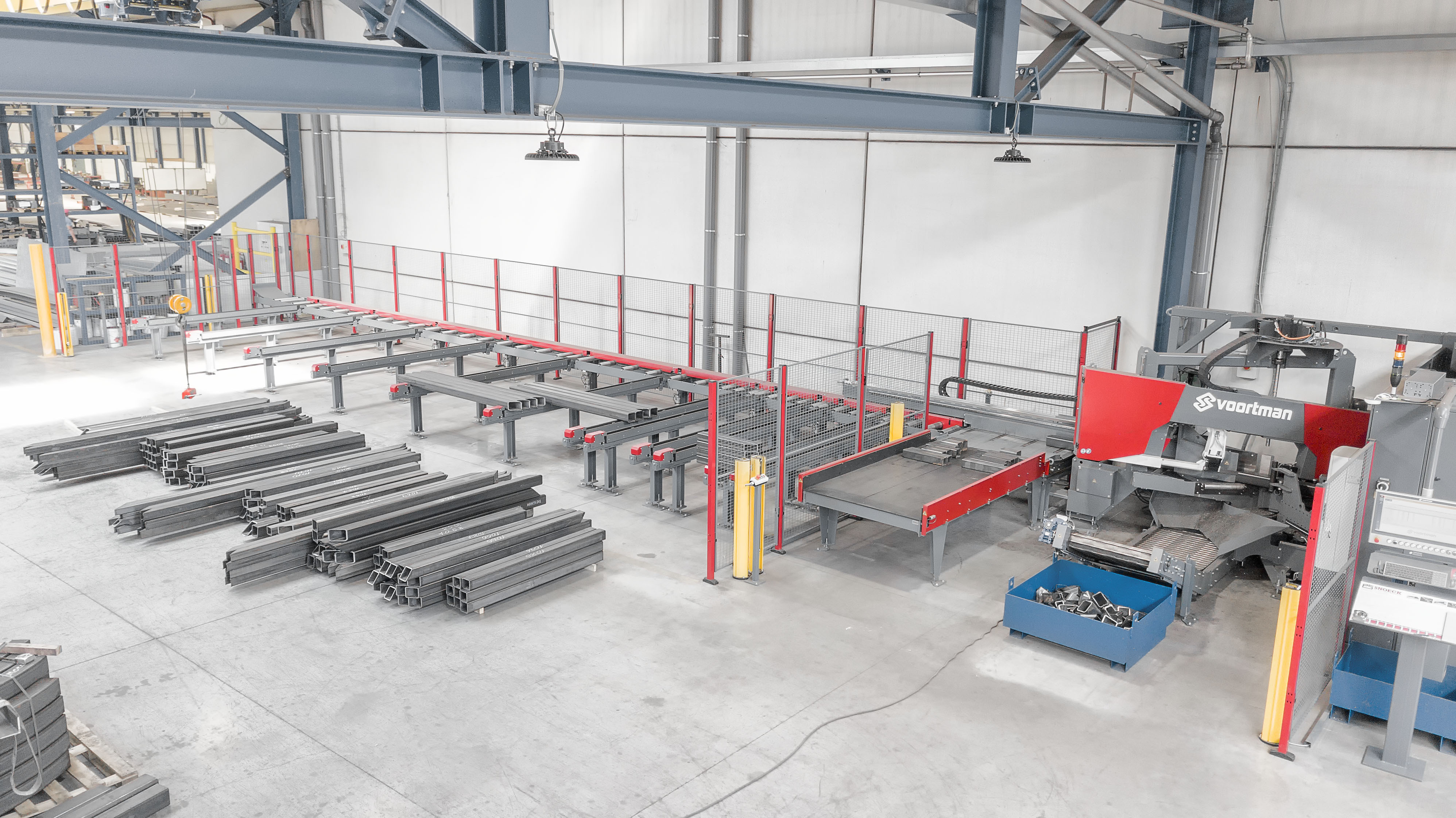
In the third outfeed zone, products of various lengths are accurately positioned on the outfeed based on the project or the most efficient method.
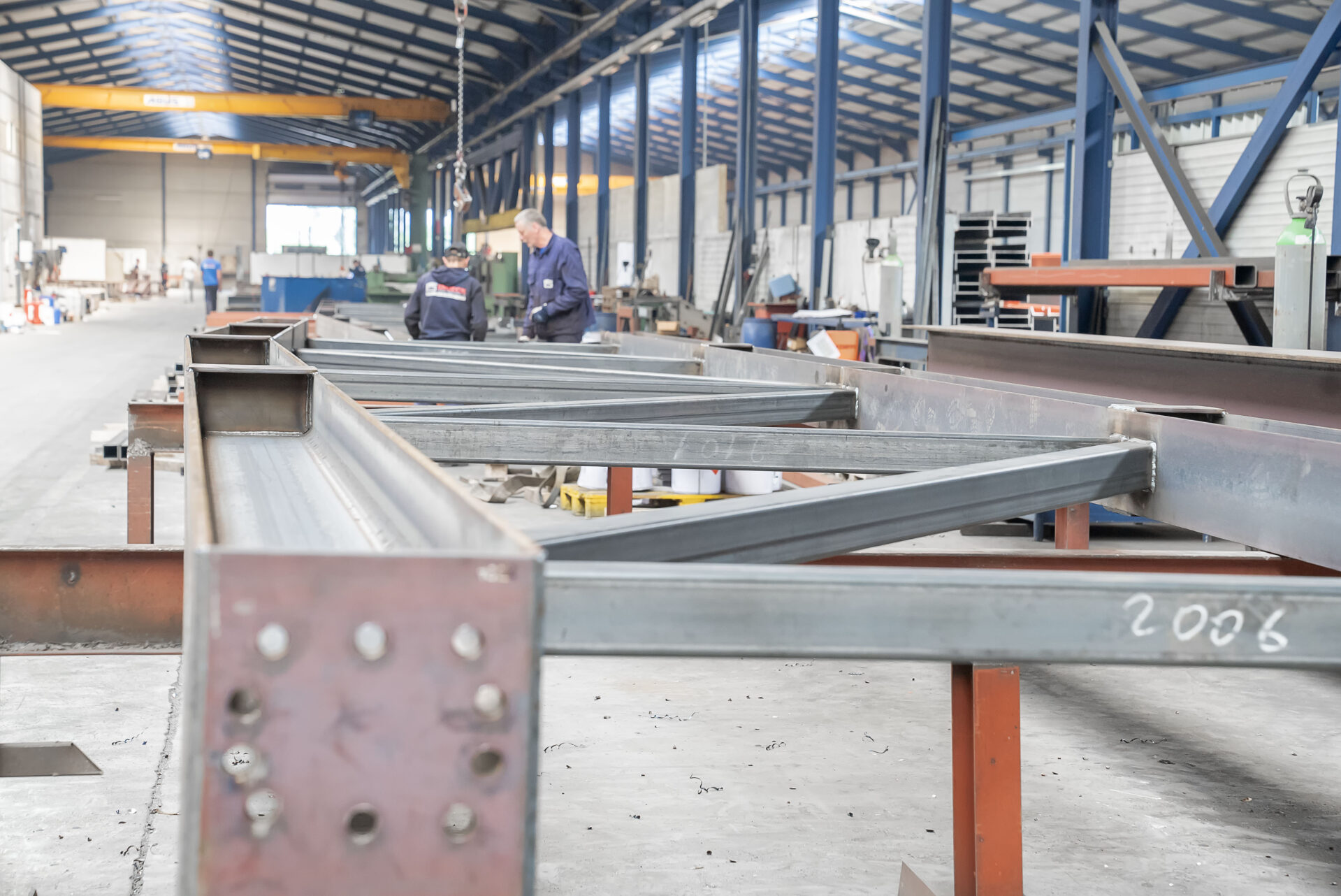
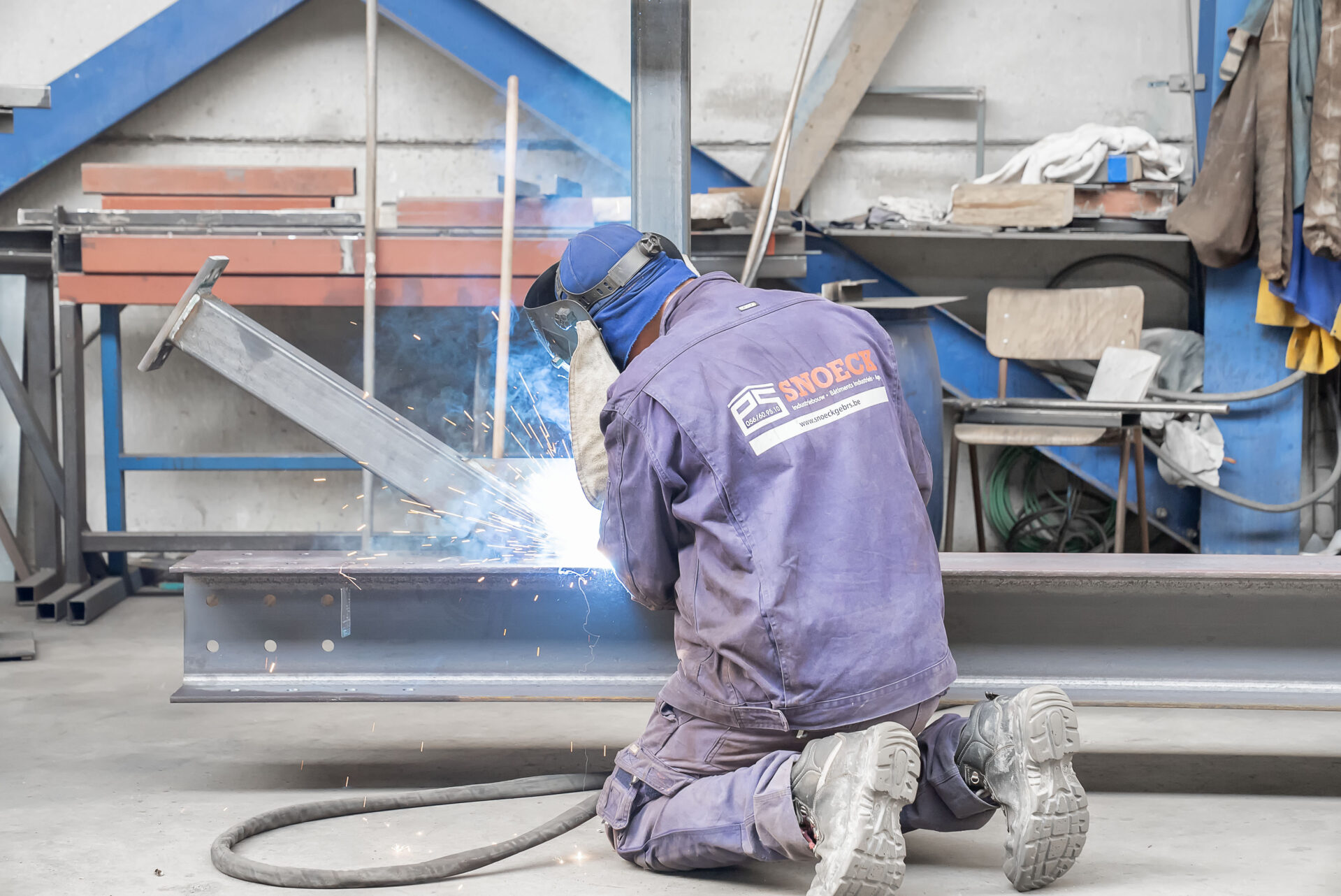
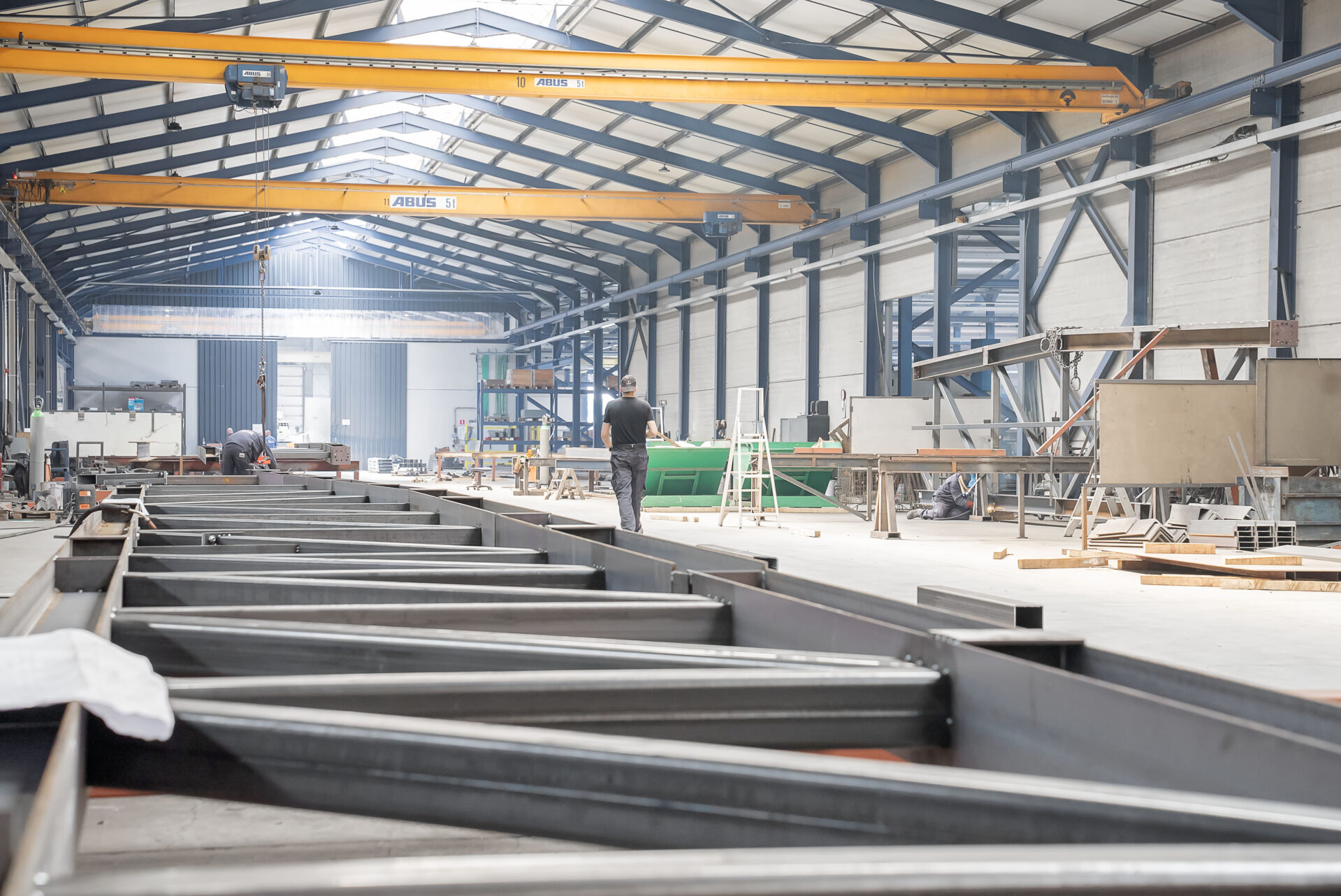
SEAMLESS COMMUNICATION AND RELIABLE SUPPORT
Steven is particularly pleased with the trajectory with Voortman. "We had a very pleasant journey with Voortman from the beginning of the development to the delivery. Everything went smoothly. The final machine was even more performant than we initially expected. That was a nice extra," says Steven proudly. For Snoeck, it is important that the communication line with Voortman is short so that they can rely on quick interventions and targeted maintenance. "This way, we can focus on production and are partly relieved by Voortman in our daily operations," explains Steven.
As a Red Label customer at Voortman, Snoeck benefits from unparalleled service and support. "We are helped within the hour. Materials ordered today before 3:00 PM are present tomorrow. Annually, we plan preventive maintenance together with Voortman to ensure optimal operation. I think we can now solve 90% over the phone or online. If it cannot be solved by ourselves, Voortman comes on-site and resolves it in no time. Thanks to the service contract, we can run 100% continuously," says Dominiek.
Steven concludes: "We can certainly recommend Voortman in all areas, both in terms of the machines themselves and maintenance, delivery, and products. We hope to continue a beautiful growth in the coming years. Within the Willy Naessens Group and Snoeck, it is important that we continue to invest in our people and our equipment. So who knows, in the future, maybe more machines from Voortman?"