Parker Steel
How Voortman's sectional outfeed provides optimal production flow
Testimonial Parker Steel
- Location:
- Founded:
- Facilities:
- Employees:
- Industry:
- Canterbury, United Kingdom
- 1904
- 3
- 350
- Steel Distribution
"The four-zone outfeed from Voortman has transformed how we operate. It allows us to load and unload beams across multiple zones without interrupting production, drastically reducing downtime."
HOW VOORTMAN'S SECTIONAL OUTFEED PROVIDES OPTIMAL PRODUCTION FLOW
After developing relationships with two other machine manufacturers, Parker Steel, a leading steel stockholder in Canterbury, UK, decided it was the right time to explore new possibilities and form a partnership with Voortman. The introduction of new advanced machinery has been a game-changer, delivering the same output as all three previous machines combined and streamlining operations.
"From the moment Parker Steel explored Voortman’s machinery, it was clear they understood the company’s vision. Parker Steel needed a partner that could innovate alongside them, and Voortman delivered," said Michael Seager, Production Manager at Parker Steel.
Running a 24-hour operation across multiple sites, Parker Steel has seen a dramatic improvement in productivity thanks to Voortman’s advanced automation and superior machine quality. They are now producing nearly the same output with one Voortman machine as they previously did with three older machines.
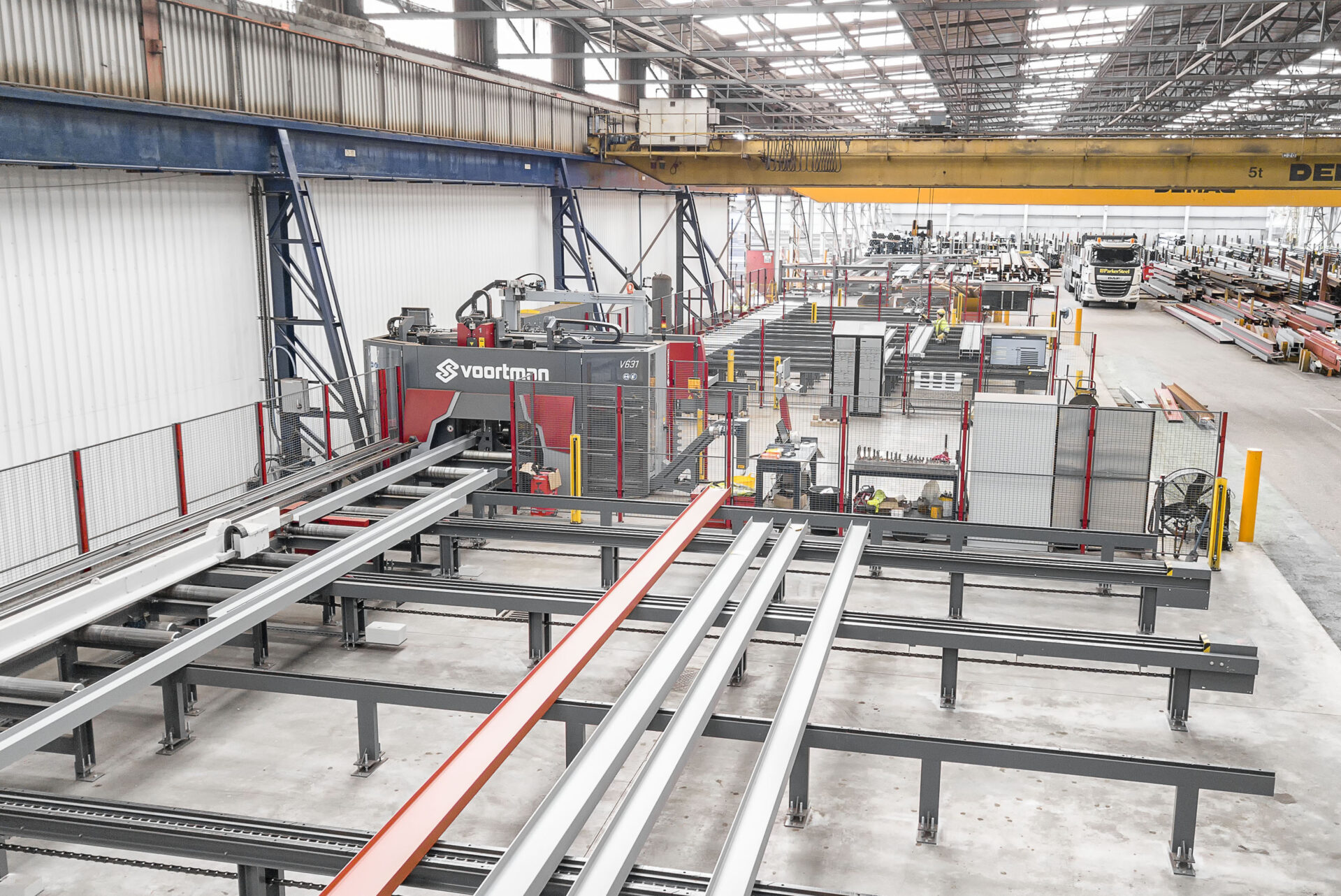
SMOOTHEST INSTALLATION IN 35 YEARS
Andy Kerr, the maintenance manager at Parker Steel, has been with the company for over 35 years. Over this time, he has seen many machines come and go, but his most recent experience with Voortman machines has been a standout. "I’ve never had a project go so well as this one did. This project with Voortman was the first I've ever done with them, and I found their planning and delivery to be exceptional," Andy stated. He noted that the installation process was particularly smooth. "Your guys were very professional, very polite. They know their jobs and deliver what they promise," he added.
The installation involved setting up a Voortman V631 drilling unit and a VB1250 saw with a feeder truck and a small parts removal system. Andy explained that they essentially gave Voortman a blank canvas—a newly prepared area with a concrete slab—and Voortman returned it with "a fantastic machine."
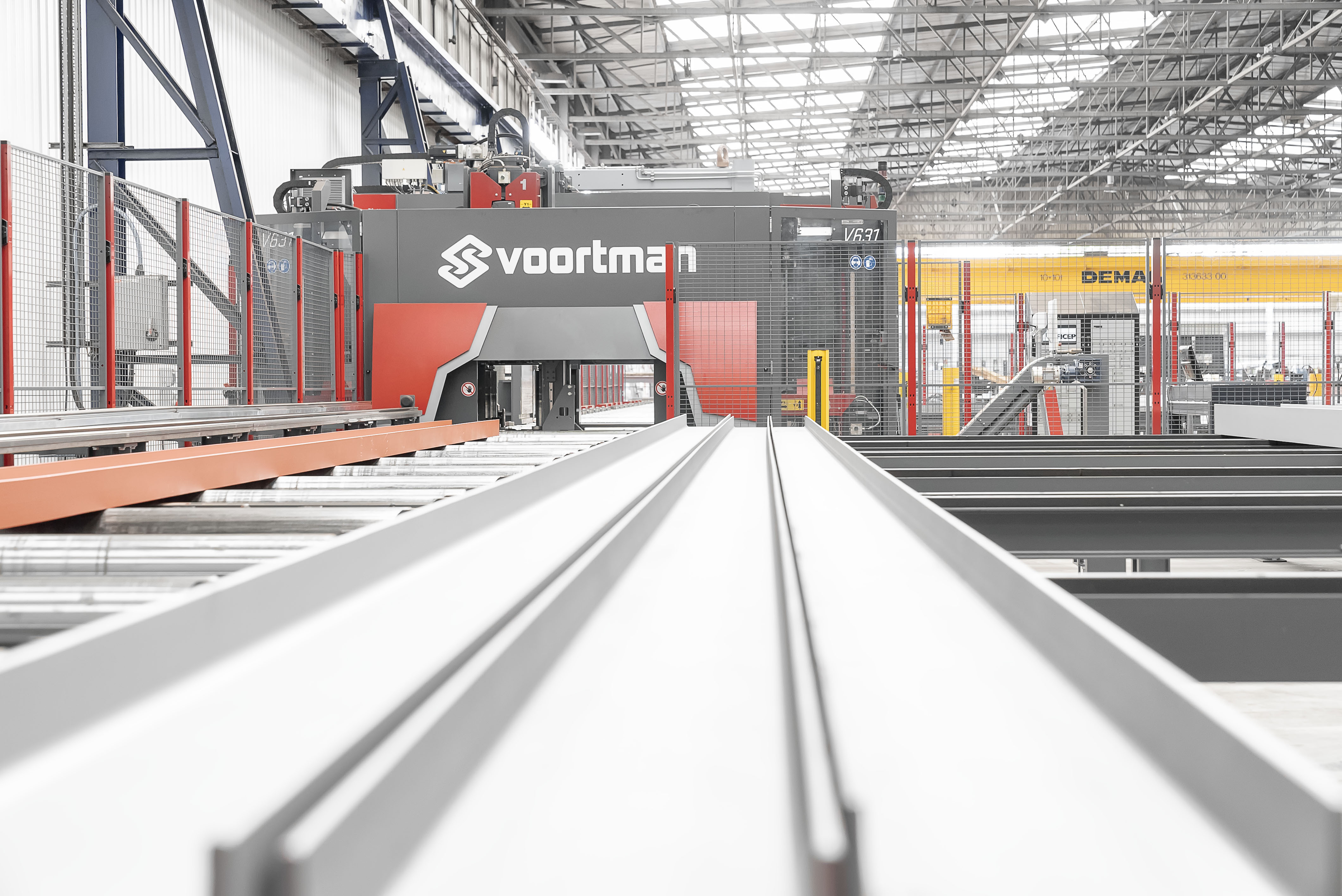
The Voortman V631 with milling capability stands out for its smooth operation and rapid plunge speed, efficiently handling both drilling and milling tasks with impressive precision and speed.
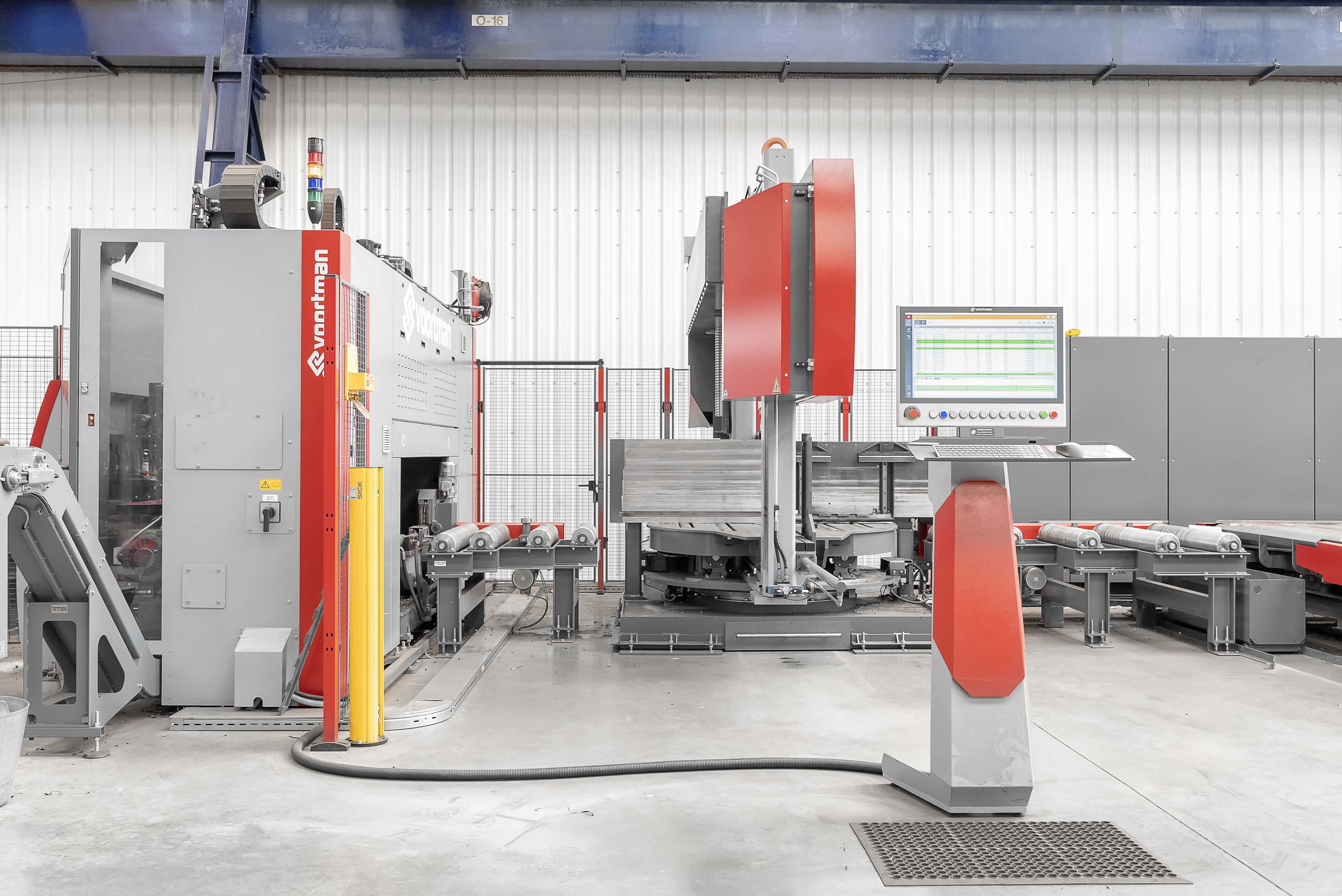
Voortman has been a game changer for the operators, who have quickly adapted to its ease of use and are impressed by the speed and efficiency it brings to their daily tasks.
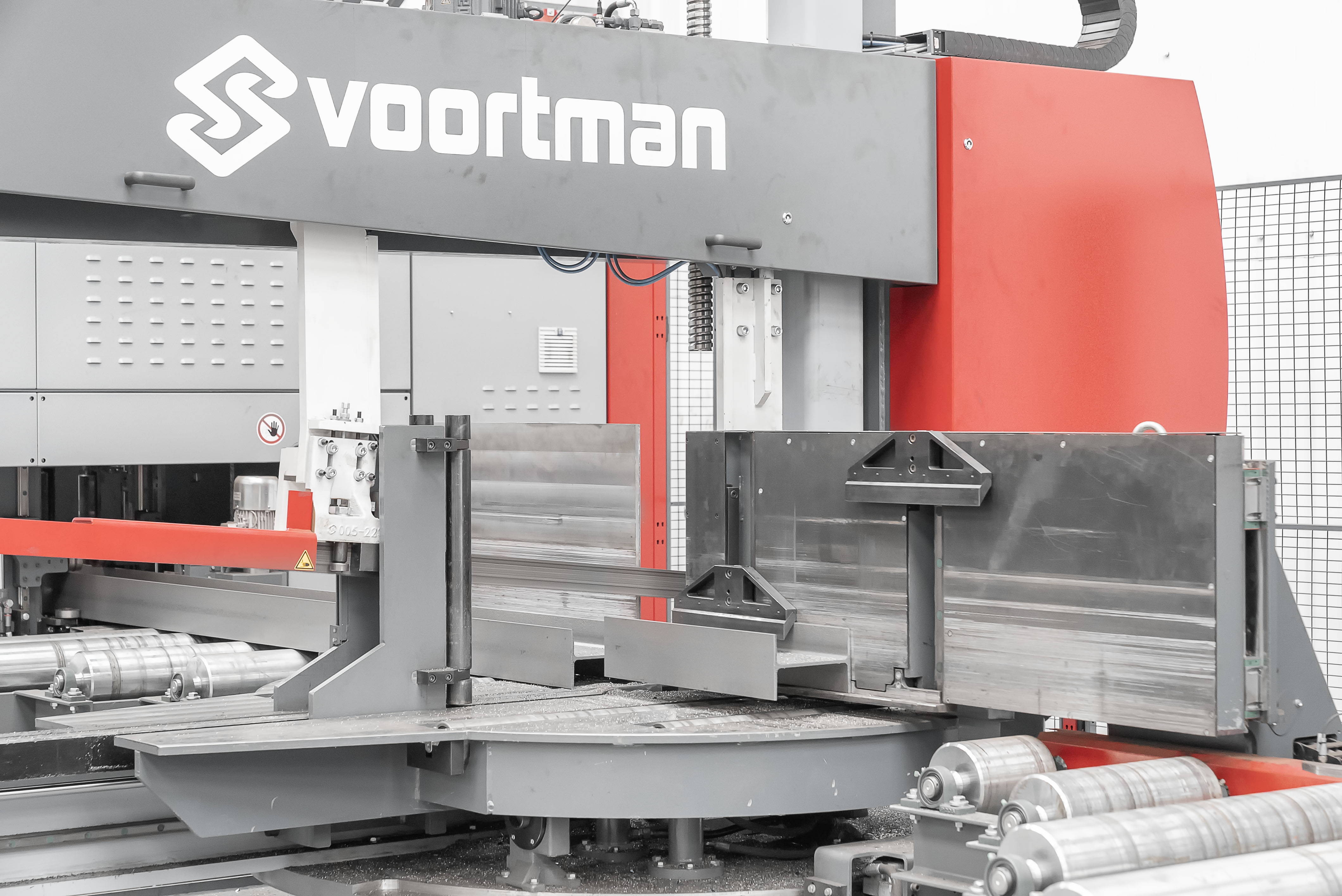
At Parker Steel, the small parts removal system on the Voortman machine has proven to be highly effective, seamlessly handling smaller components while keeping the overall operation running smoothly without interruption.
SUCCESS WITH ZONED OUTFEED
With a lot of Parker Steel's work involving beams up to six meters, Voortman’s sectional outfeed has proven to be an ideal solution for their high-demand environment. By batching similar jobs together, Parker Steel has significantly improved output and efficiency. The innovative four-zone output system enables Parker Steel to work with beams up to 18 meters in length while optimizing workflow efficiency. By breaking the beam line into distinct zones, Parker Steel can keep production moving continuously, even while unloading finished products.
"The four-zone output from Voortman has transformed how we operate," said Michael. "It allows us to load and unload beams across multiple zones without interrupting production. We can now run different operations simultaneously, drastically reducing downtime."
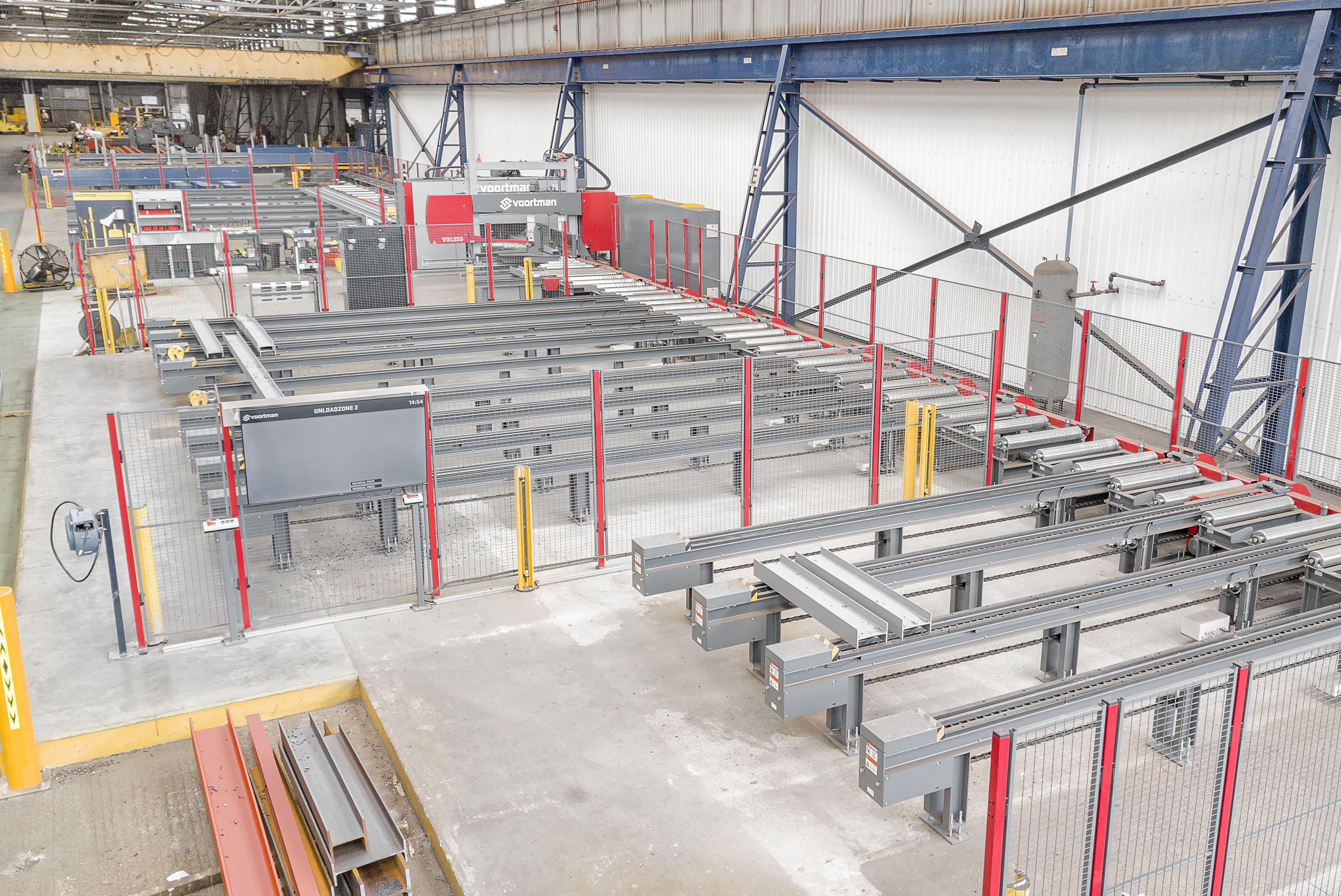
The new system features a four-zoned outfeed, allowing Parker Steel to optimize production by running multiple processes simultaneously, significantly increasing efficiency and reducing downtime.
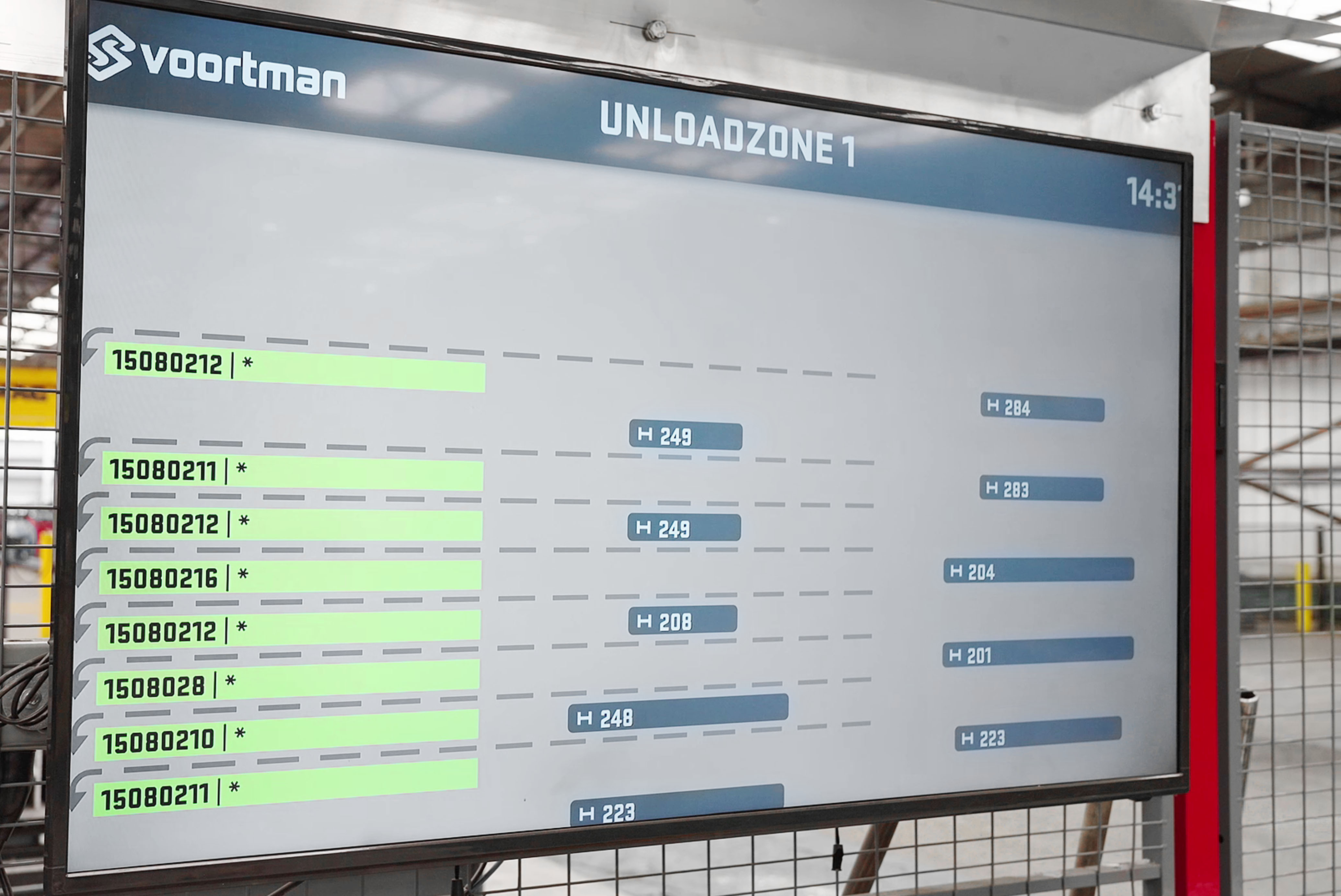
Smart Unloading screens deliver real-time data on product IDs and locations, making them ideal for efficiently unloading and bundling orders for projects or customers.
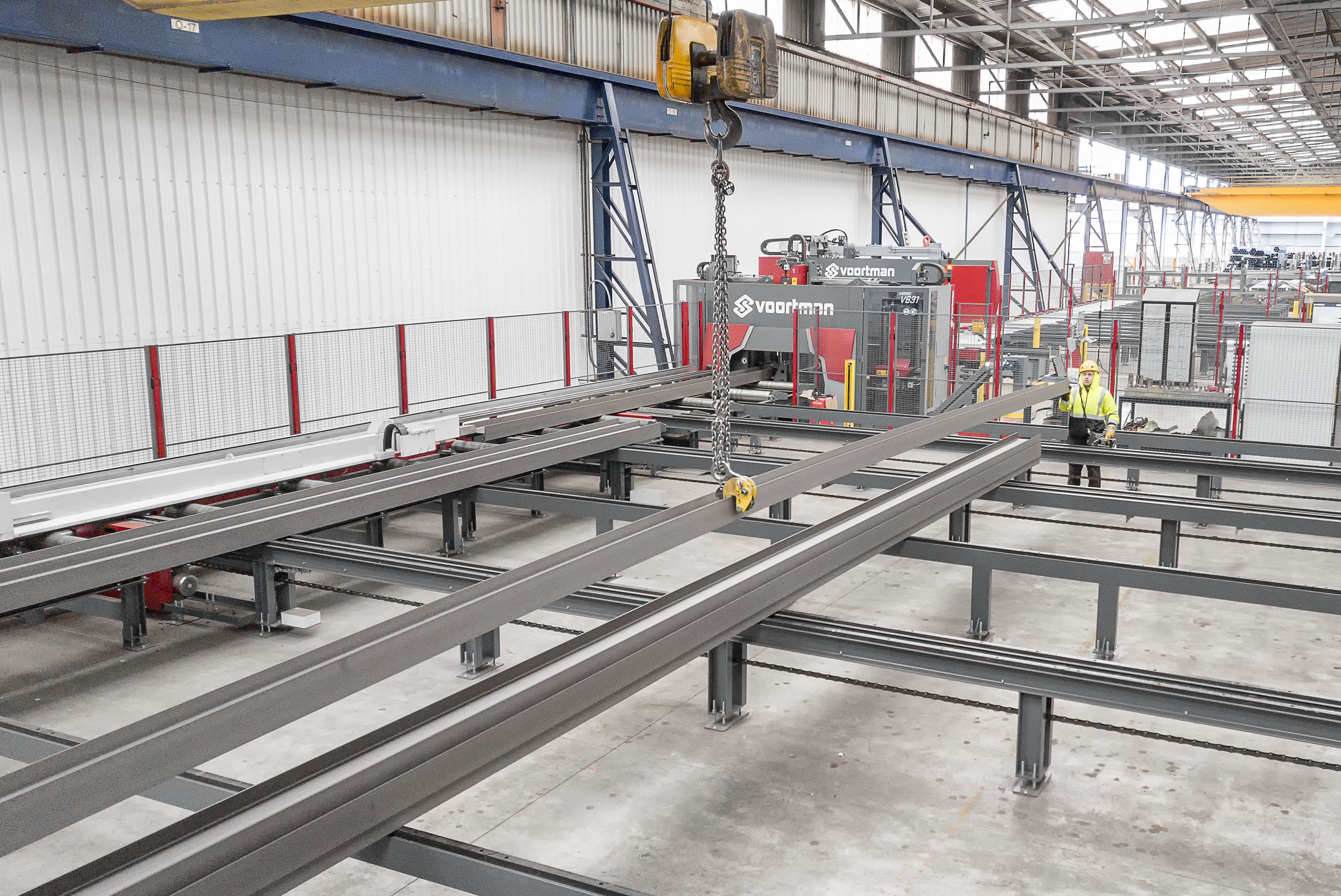
Double light curtains ensure safe loading and unloading of materials with uninterrupted processing.
FROM REACTING TO BREAKDOWNS TO PROACTIVE MAINTENANCE
Andy Kerr highlights the improvements in their current maintenance process since the installation of the Voortman machine. "Our pre-planned maintenance is now much more proactive," he says. "With the new machine, we follow a set schedule—maintenance happens every Saturday night. This is a big change from before, when we were always reacting to breakdowns. Now, our maintenance calendar is far more structured, allowing us to stay on top of tasks without scrambling to fix unexpected issues." This proactive approach helps Parker Steel avoid downtime and keeps operations running smoothly.
Andy’s experience with Voortman’s customer support has been equally positive. "The support has been fantastic. If we have an issue, we can just phone the number on the console, and someone comes online within minutes. They can help us keep running until we get feet on the ground," he explained. He also appreciated the professionalism and thoroughness of the service engineers who have come to assist when needed.
Voortman’s machines have not only increased productivity but also allowed Parker Steel to stay ahead of the competition in an ever-evolving industry. Their advanced technology, such as automated unloading systems and enhanced flexibility, has enabled Parker Steel to meet the growing demands of its customers while maintaining a lean workforce. "Voortman machines have pushed us further into the market, allowing us to exceed customer expectations and stay ahead of our competitors," Seager noted.
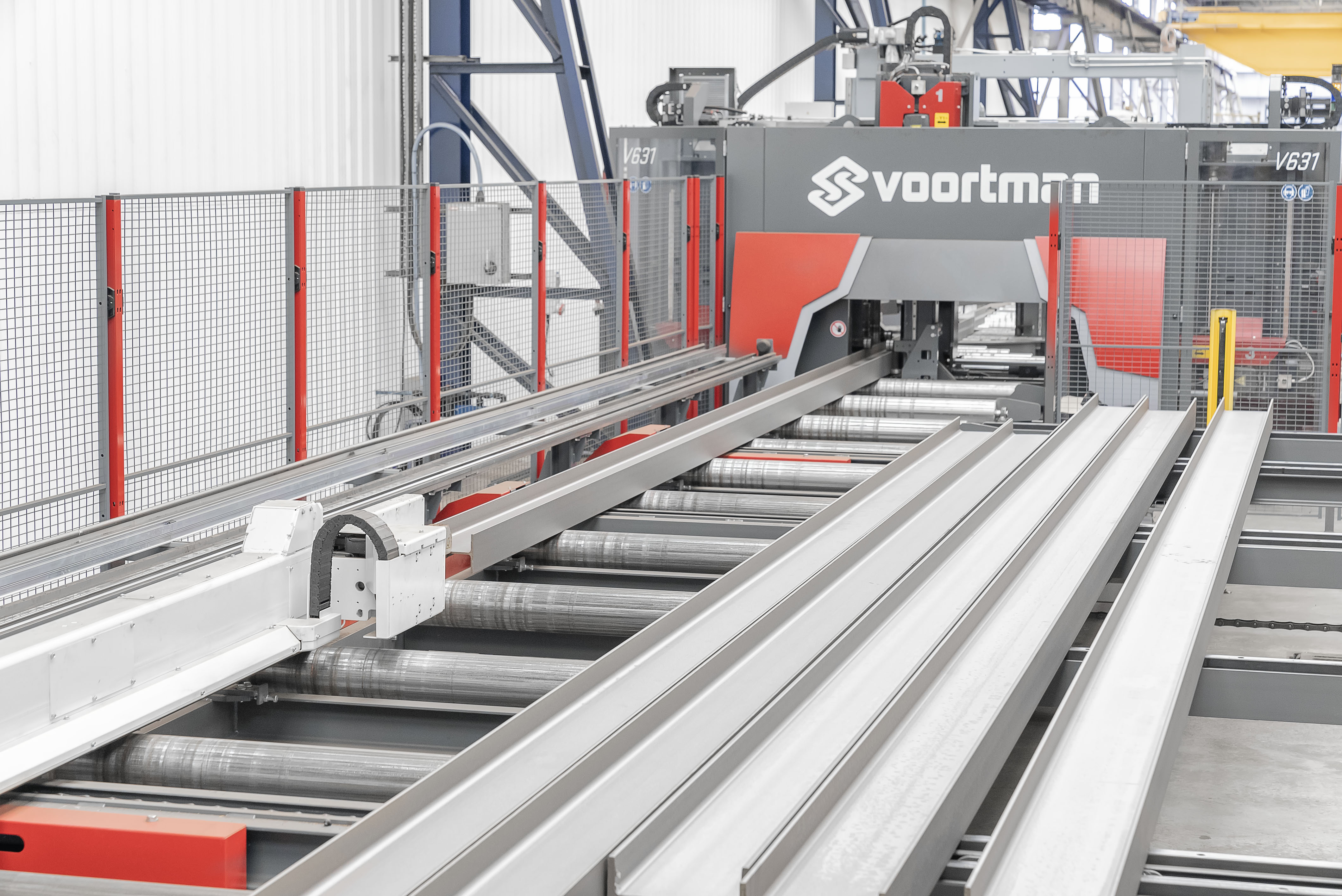
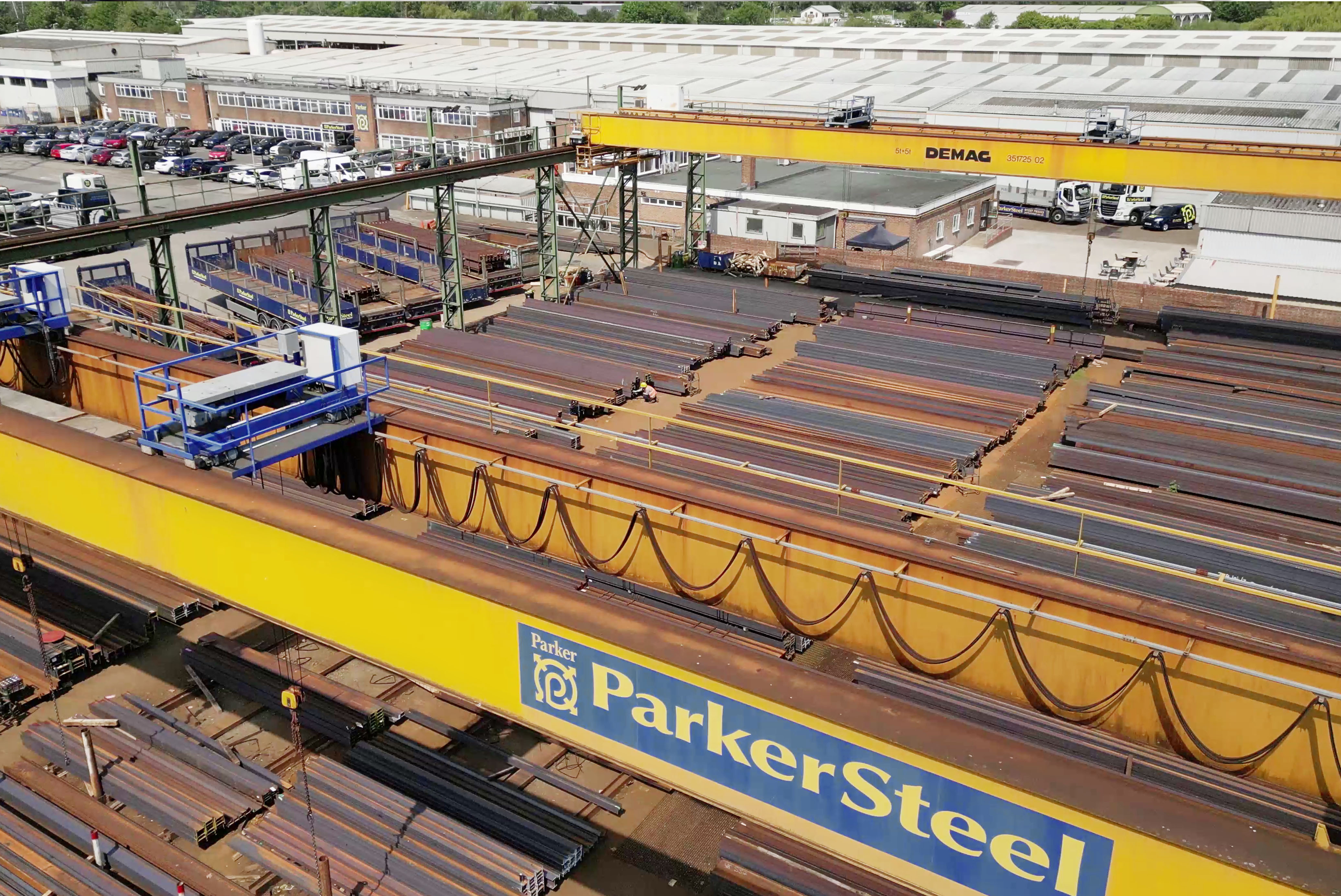