Optimizing Mechanical Engineering with the Voortman V310
Hartinger Kranbetrieb's Success Story
"We can optimize the manufacturing process by incorporating the Voortman V310's plasma cutting, oxy-fuel, milling and drilling on one station, so we don't need to put the parts on two or three different machines"
Testimonial Karl Hartinger Kranbetrieb GmbH
- Location:
- Employees:
- Founded:
- Machine:
- Warburg, Germany
- 75
- 1952
- V310
"We can optimize the manufacturing process by incorporating the Voortman V310's plasma cutting, oxy-fuel, milling and drilling on one station, so we don't need to put the parts on two or three different machines"
EXPANDING SERVICES AND SPECIALIZATIONS
Felix Hartinger, one of the three managing directors of Karl Hartinger Kranbetrieb GmbH, discusses the company's expansion into the mechanical engineering sector and their experience with the Voortman V310 machine. Hartinger Kranbetrieb, a company founded in Warburg by Hartinger's grandfather, specializes in rentals, wind power, assembly, and mechanical engineering. "We provide an array of services that include crane rental, transport, assembly and disassembly of wind turbines, machine, heavy, and special transport, as well as salvage and towing. We also offer dismantling and reconstruction of machines or plants before and after transport. As an illustration, he cites a project in Kassel where their team constructed bridges to move hefty weights. A fairly new branch of business engineering and manufacturing complete machines." explains Hartinger.
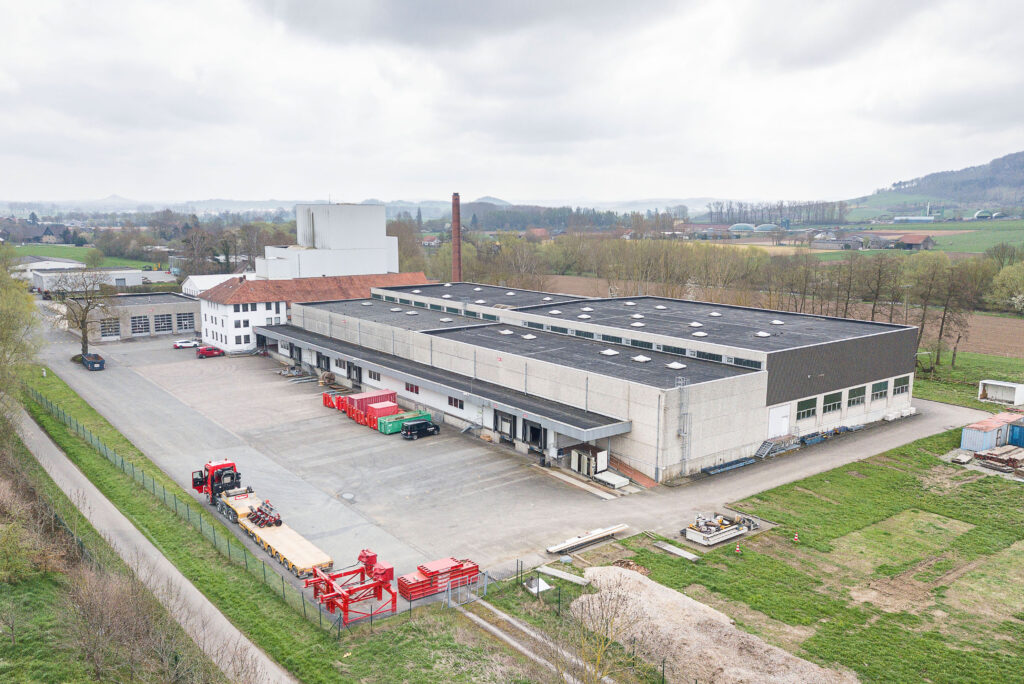
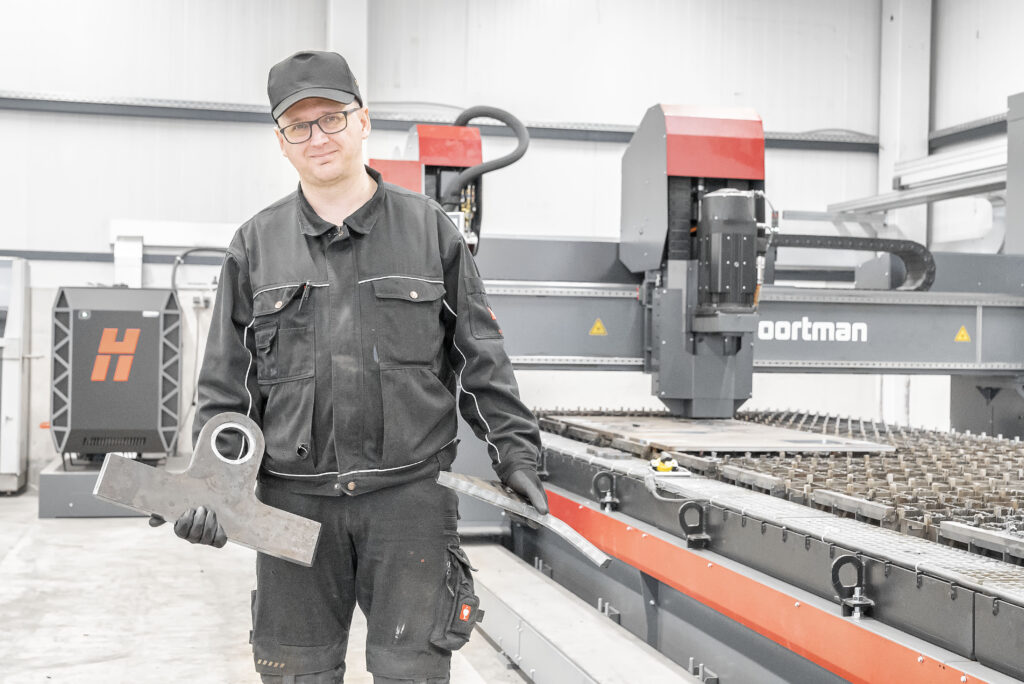
STREAMLINING PRODUCTION WITH THE VOORTMAN V310
Hartinger distinguishes itself in the mechanical engineering sector by
providing complete structures and products with remarkable speed. The Voortman
V310 is an optimal choice for the company because it supports the
implementation of projects quickly and at short notice. "We can optimize
the manufacturing process by incorporating the Voortman V310's plasma cutting,
oxy-fuel, milling and drilling on one station, so we don't need to put the
parts on two or three different machines." Hartinger explains.
CONVINCED AFTER VISITING VOORTMAN
The Voortman company was already known to Karl Hartinger, but they discovered their high-quality plasma systems through online research. Hartinger states, "And there we found the system from Voortman, which can offer more for this process than any other manufacturer."
They approached Voortman and visited their facility to view the system firsthand. "What convinced us was that the machine, like the other Voortman machines, is chiefly used for steel construction and machinery and equipment industries. And you can tell that the company really knows what it's talking about when it comes down to beam and plate processing machines."
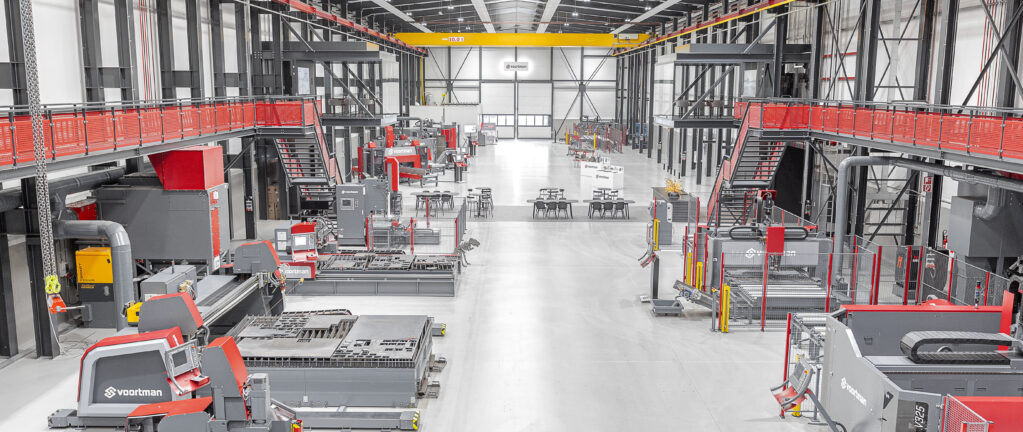
THE IMPACT OF HYBRID MILLING
Shortly after the machine was put into operation, the opportunity arose to update the software, introducing the advantage of performing Hybrid Milling. This process allows for creating contours with mill quality by cutting a part of the contour first, then mill away the remaining part, saving a significant amount of time and simplifying the process overall. Waldemar Wiederkehr, operator and product engineer, shares his thoughts: "Hybrid Milling has truly revolutionized the way we work, making everything more efficient and precise. The machine starts by roughly cutting out the piece with plasma before running the contour once, instead of starting from the center, which significantly speeds up the process compared to working from the center outwards."
VOORTMAN V310 & HYPERTHERM XPR300 WORKING IN PERFECT HARMONY
When Hartinger first started using the Hypertherm XPR300, they immediately noticed the difference in quality compared to their previous power source. The XPR300's simplified wear parts and significantly optimized service life made it an attractive option for the company. Franz Bäumer says, "We find that the wear parts are significantly simplified, and the service life of the wear parts has again been significantly optimized."
The integration of VACAM software with the Hypertherm power source was another major advantage for Hartinger. The software allowed them to streamline their processes, eliminating the need to set any parameters manually. Franz shares, "You select a strength and can start directly. So in just a few steps, you can achieve optimal quality."
Moreover, VACAM provides real-time data on the wear parts, helping the Hartinger team plan their work more efficiently. "If I were to start this, it already says -22, which means there would be the change of the various parts necessary. That way I can plan it better," says Waldemar Wiederkehr, who operates the Voortman V310.
SIX MONTHS OF SUCCESSFUL USE
After
using the V310 machine for six months, Hartinger reports minimal problems in
terms of error messages or technical malfunctions. The machine's expectation
plan is detailed, making it easier to maintain and operate. "We can use it
for oxy-fuel cutting up to 50 millimeters in thickness. We can cut plasma,
including bevels, utilize drilling, thread tapping, countersinking and
milling," Hartinger elaborates.
Hartinger commends the training provided by Voortman, which enabled them to start production quickly after installation. He also appreciates their ongoing support and assistance with any questions. "We are very convinced of the V310 and the entire service and handling of the Voortman company and would buy the same machine again at any time," he concludes.
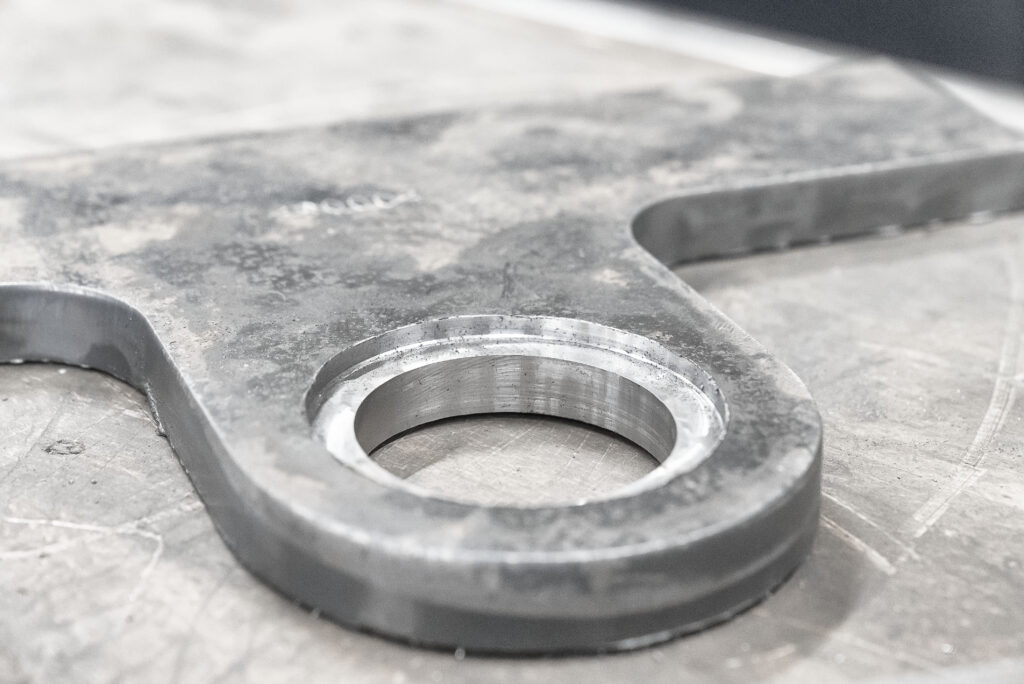
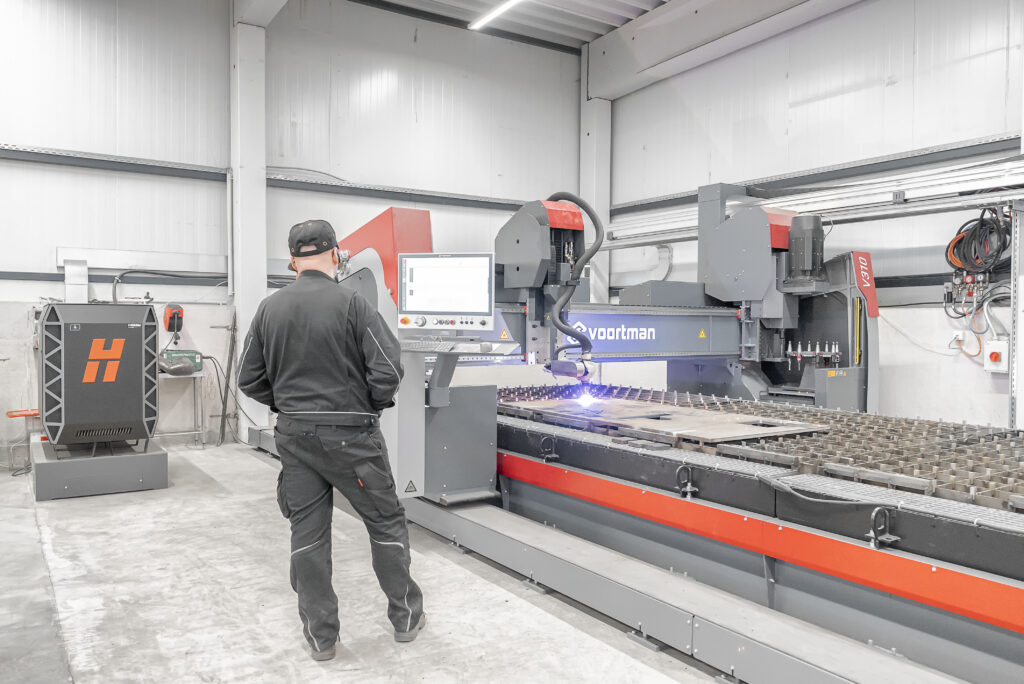
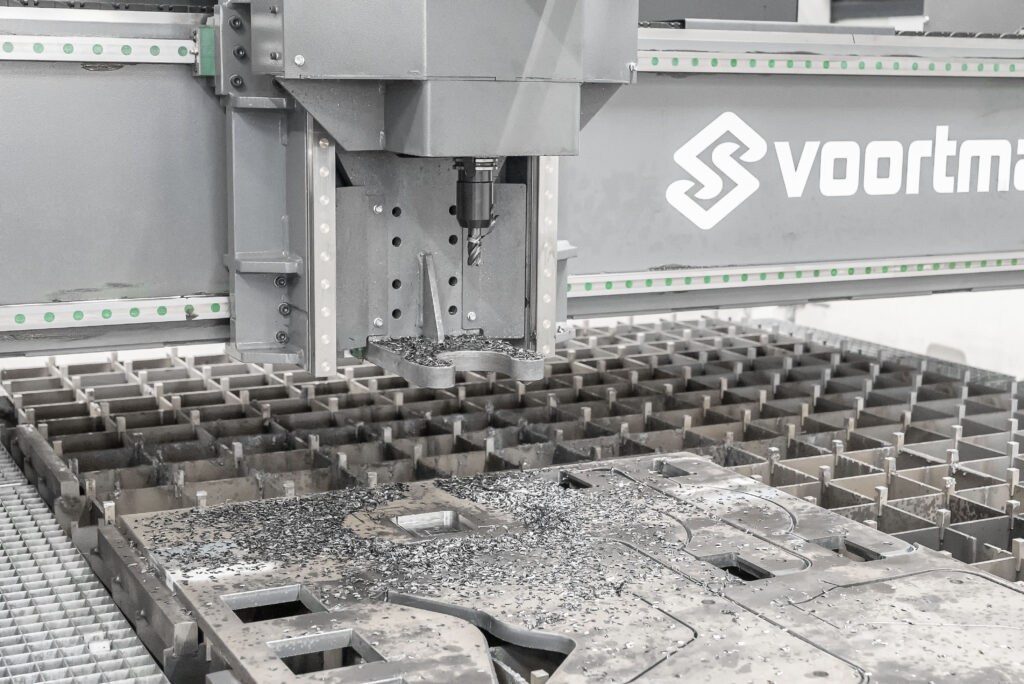