CCI Leidingsystemen
From Outsourcing to Insourcing: CCI reclaims production efficiency with the Voortman MO machine
Robert van Kaam (left) and Alex Wijnings (right) of CCI Leidingsystemen in front of their Voortman MO Classic pipe processing machine.
Testimonial CCI Leidingsystemen
- Location:
- Founded:
- Facilities:
- Employees:
- Industry:
- Moerdijk, The Netherlands
- 1980
- 2
- 75
- Processing Equipment
'Voortman’s MO machine offered the level of precision and automation we were looking for, enabling us to handle both short segments and complex shapes without additional rework'
BRINGING CUTTING OPERATIONS IN-HOUSE
Facing frequent delays from outsourced cutting services, CCI decided to bring these operations in-house. 'Outsourcing caused too many scheduling issues and added logistical complications,' explains Robert van Kaam, CCI's Operations Manager. 'We needed greater control and efficiency.' By investing in a Voortman cutting machine, CCI has transformed its production process, enabling faster turnaround times, improved quality, and reduced reliance on external suppliers. This strategic shift marks a significant step forward in CCI’s commitment to delivering precise, timely solutions for clients.
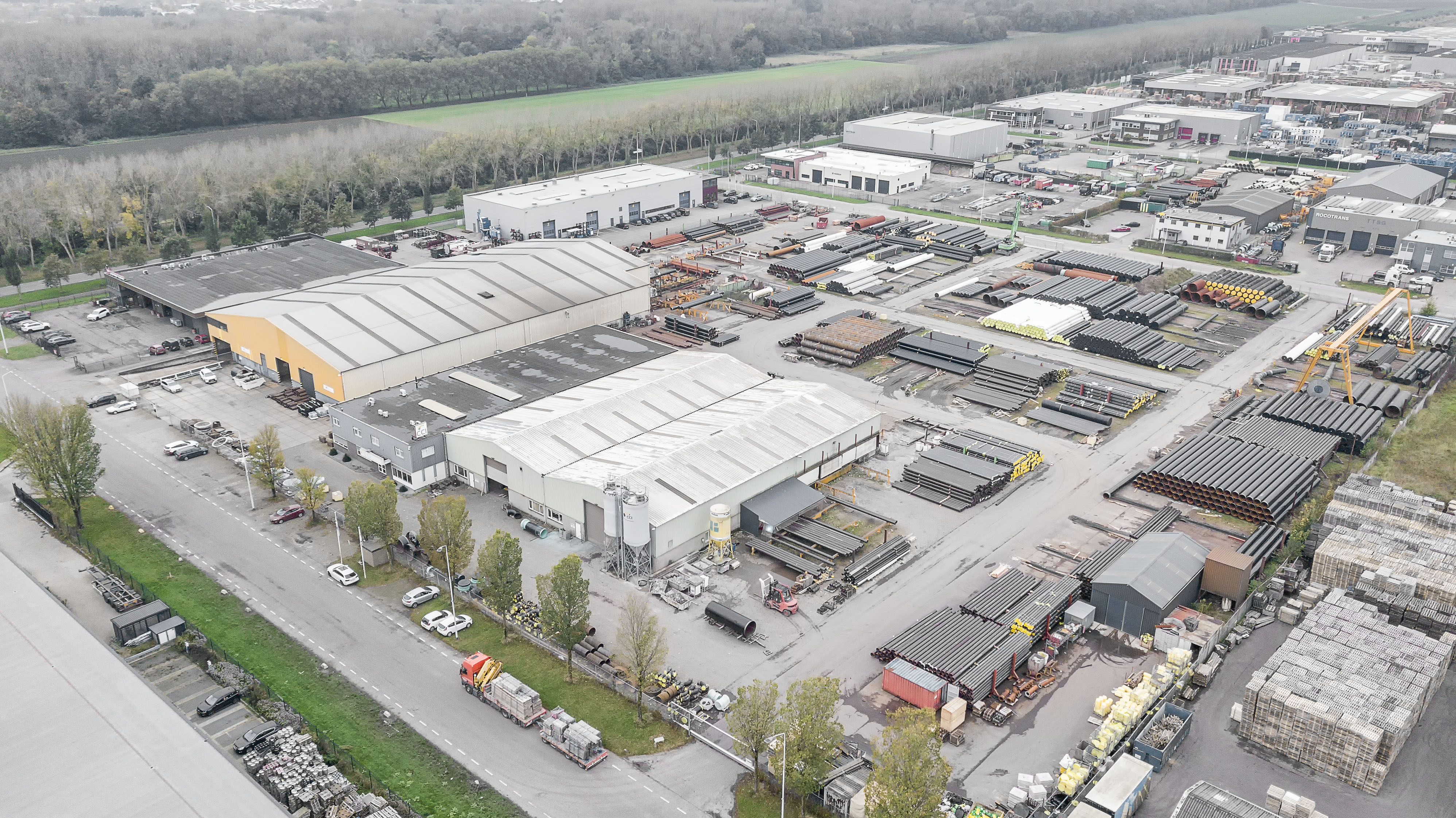
The production facility, strategically located in Moerdijk, close to Rotterdam and Antwerp.
MEETING HIGH DEMAND WITH PRECISION
Robert shares his excitement about the latest addition to their production line. 'At CCI, we specialize in large prefab piping systems for various clients domestically and internationally,' he explains. 'Our expertise lies in manufacturing extensive underground piping systems, with our production facility strategically located in Klundert, close to Rotterdam and Antwerp. This location is ideal for efficient logistics, serving our clientele, which spans water utilities and the petrochemical industry.'
As demand for high-precision, high-volume production grew, CCI recognized the need to modernize its cutting process. 'Our previous cutting methods involved manual handling, which was time-intensive and required significant rework,' Robert recalls. 'To stay competitive and keep up with client expectations, we needed a cutting system that would allow us to streamline production, improve accuracy, and reduce lead times.' After thorough research, CCI chose Voortman as their new cutting solution. Robert emphasizes, 'Voortman’s machine offered the level of precision and automation we were looking for, enabling us to handle both short segments and complex shapes without additional rework.'
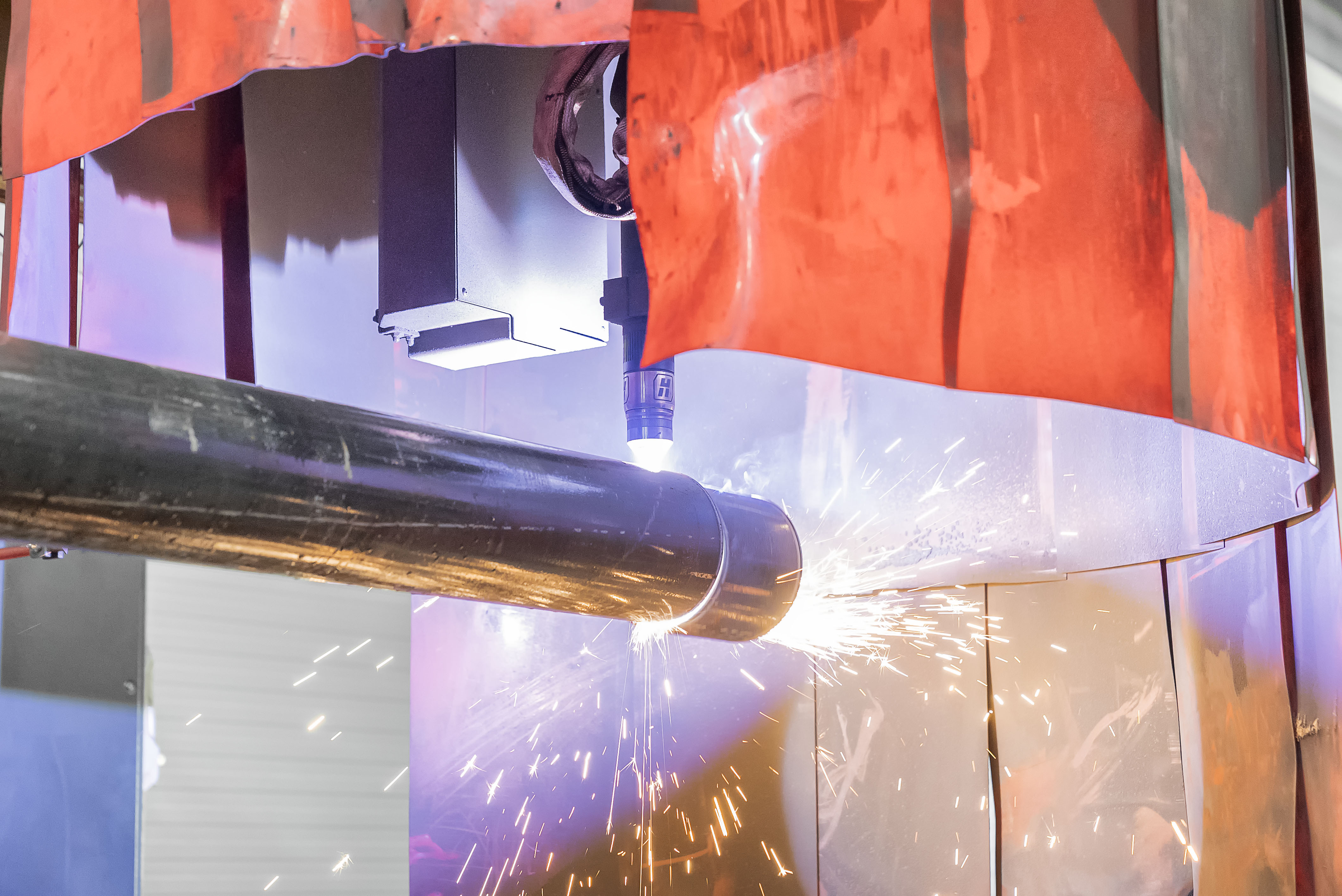
To process pipes ranging from two to 80 inches, CCI selected the Voortman MO Classic, equipped with both 3D plasma bevel and oxy-fuel cutting capabilities.

CCI specializes in large prefab piping systems for extensive underground piping systems.
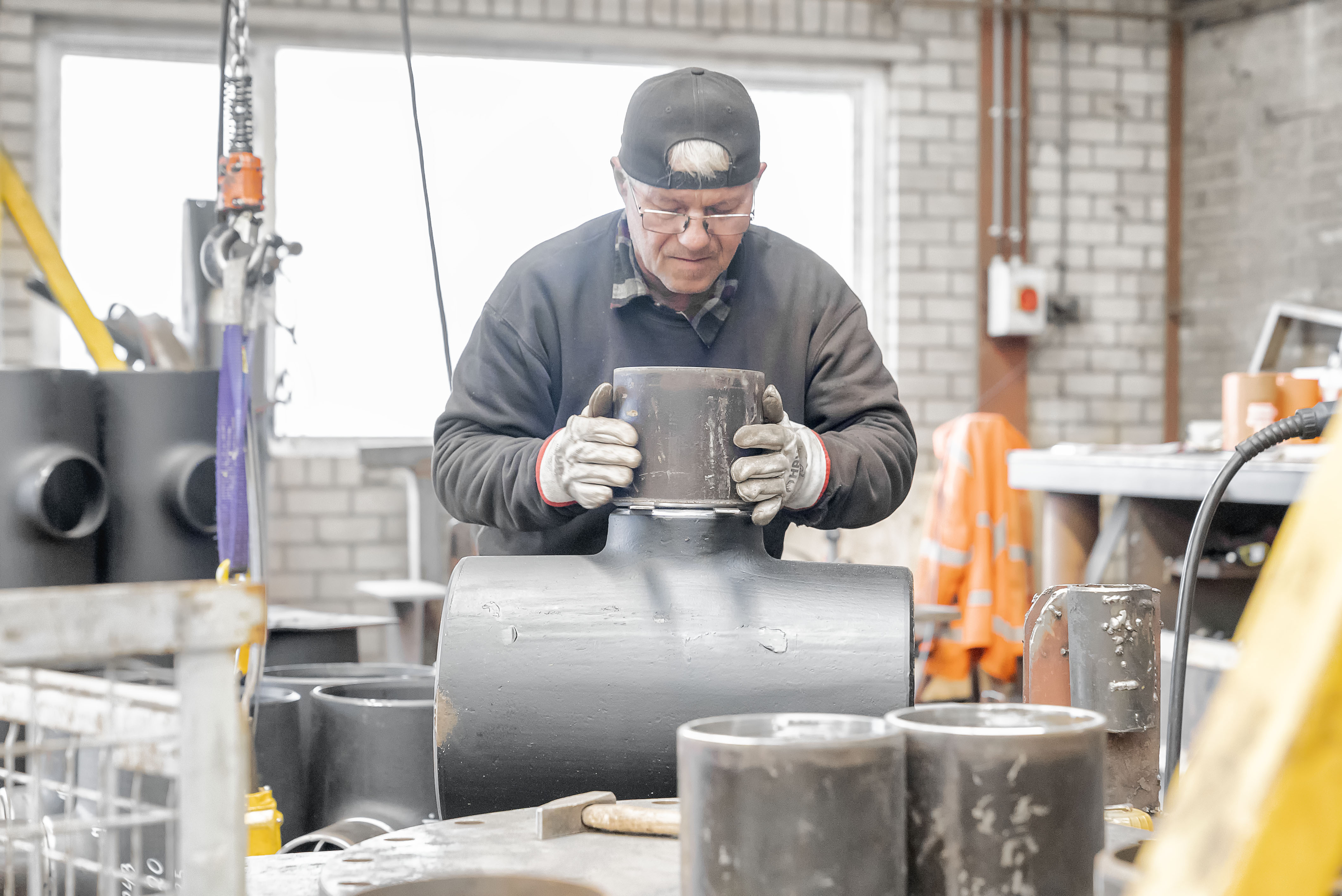
The Voortman machine offers the level of precision and automation to handle both short segments and complex shapes without additional rework.
PE-COATED AND CEMENT-LINED PIPES
The benefits of the Voortman cutting machine quickly became evident. 'The new system is a game-changer,' says Robert. 'With Voortman, we can cut from digital designs directly, allowing one-to-one transfer from drawing to final product, with complex parts cut in a single pass. Additionally, it supports cutting PE-coated and cement-lined pipes cleanly and efficiently, which was a challenge with other machines.
Robert is also impressed with Voortman’s service and support, which has further solidified the success of this investment. 'The training provided by Voortman was outstanding, and their technical support has been quick and effective. Minor adjustments are addressed promptly, and the parts ordering process through their online system is seamless. Our team is motivated, with several employees eager to become machine operators, thanks to Voortman’s responsive assistance.'
Third-party work
Looking forward, CCI plans to leverage the machine's efficiency to take on more third-party work. 'We’ve already had inquiries,' Robert shares. 'We’re now in a position to expand our offerings with reduced turnaround times and higher flexibility. With Voortman, we’re fully prepared to meet the growing demands of the market over the next five years and beyond.'
Alex Wijnings, the company’s dedicated salesman, is actively introducing CCI’s enhanced cutting capabilities to the market. His efforts are focused on ensuring the company connects with clients who can benefit from these advancements, further solidifying CCI’s position as a leader in innovative solutions.
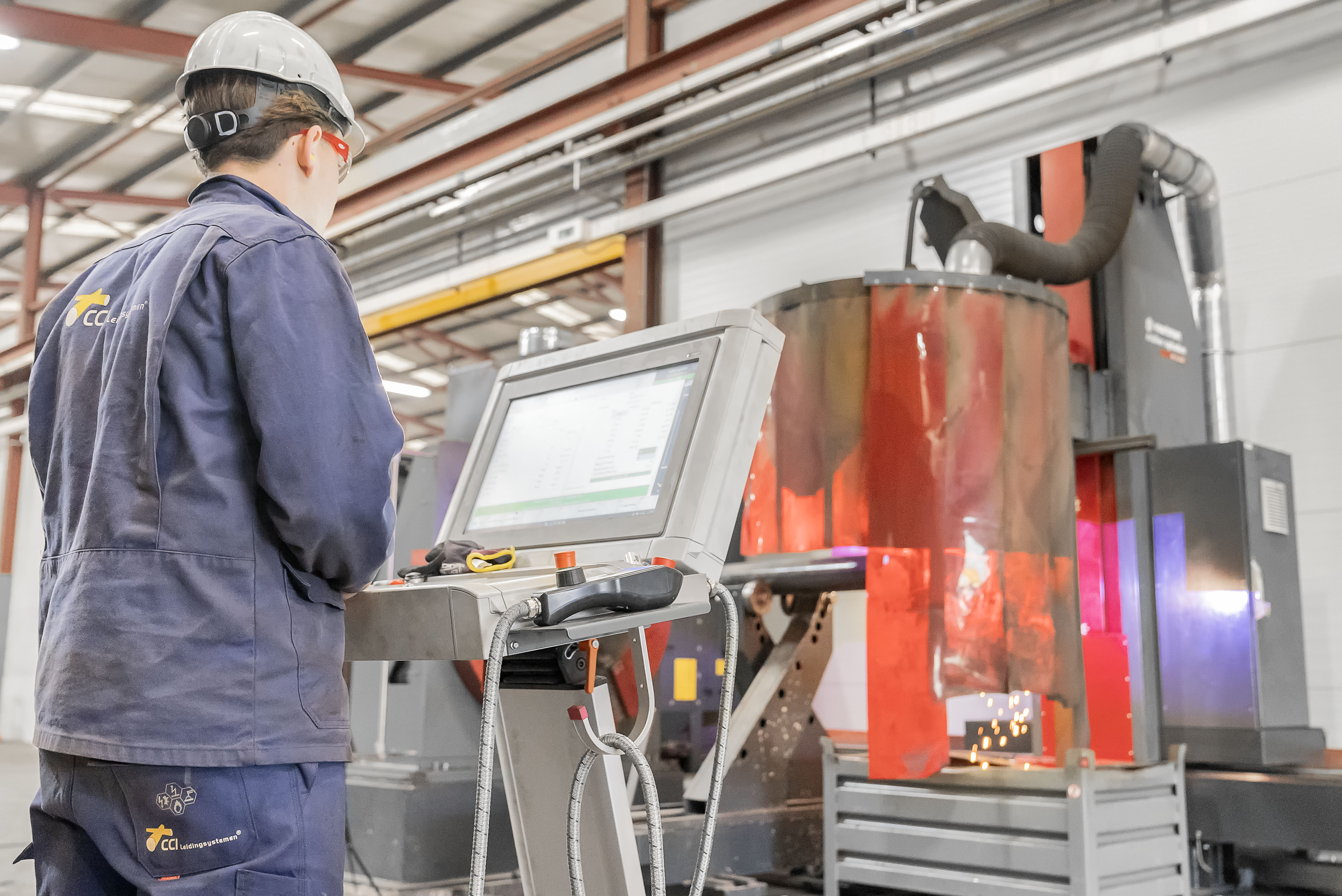
One-to-one transfer from drawing to final product, with complex parts cut in a single pass.
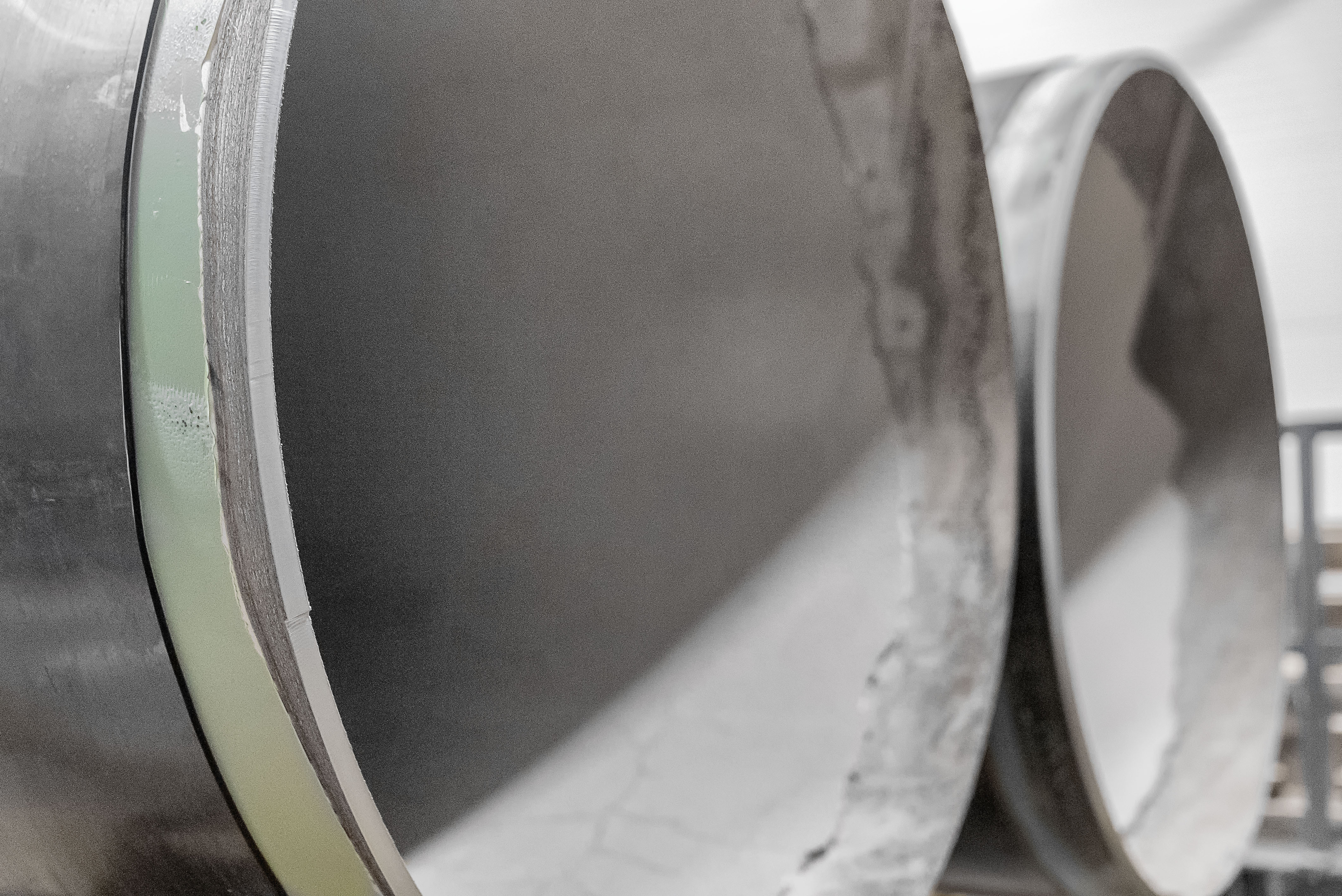
It supports cutting PE-coated and cement-lined pipes cleanly and efficiently, which was a challenge with other machines.
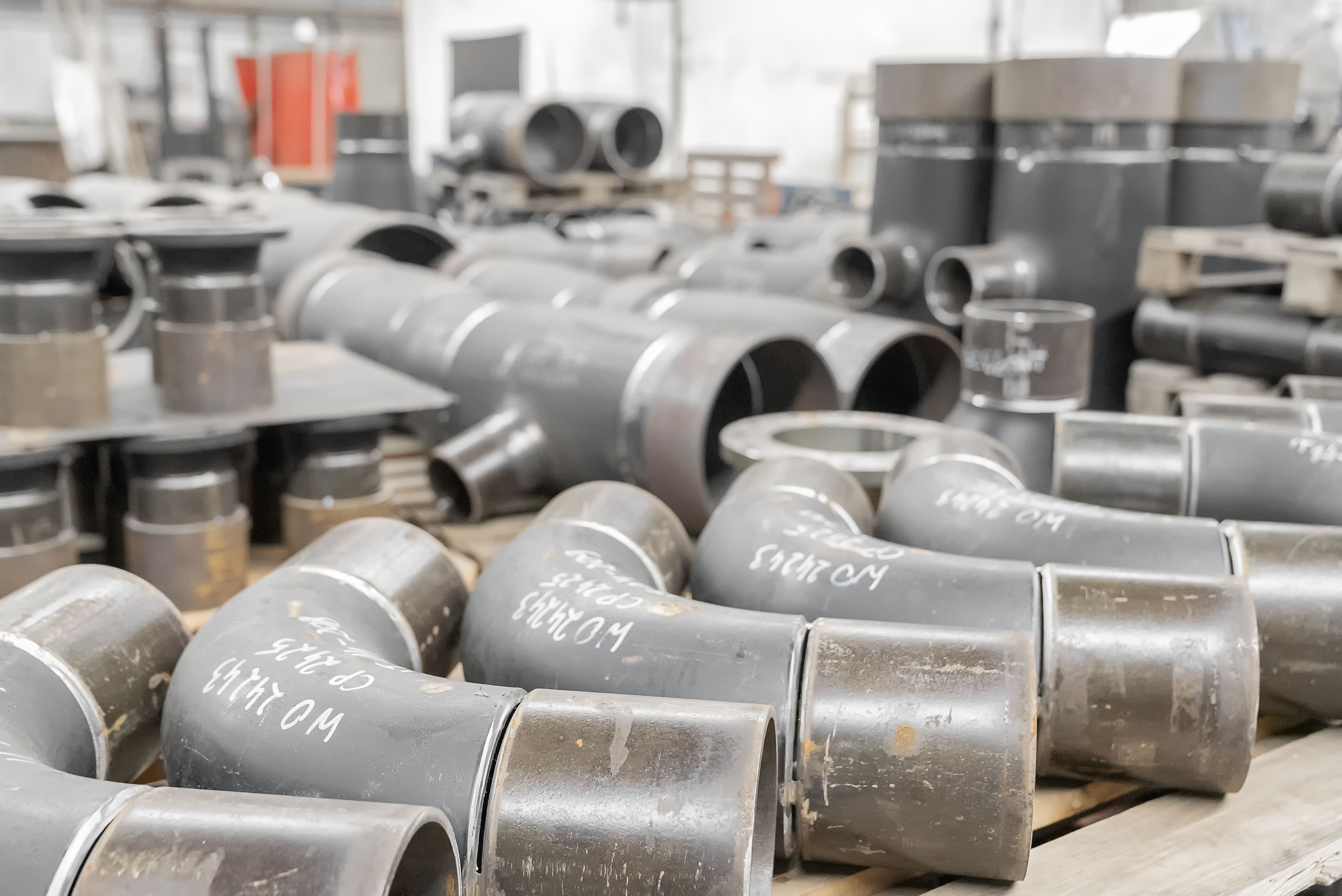
CCI plans to leverage the machine's efficiency to take on more third-party work.