Voortman VSB Range
Shot blasting machine
The Voortman VSB Range automatic shot blasting machine is designed using the highest quality components for shot blasting plates and profiles for an optimal finished steel surface. Pre-installed blasting programs and automatic functions make the machine simple to learn and operate. Its compact design reduces the footprint without reducing functionality or quality. A minimal footprint is required when combining the shot blasting process with painting, pre-heating, drying and a blow-off unit.
Highly automated process
Increased productivity & reduced labor costs
AUTOMATIC SHOT BLASTING
The VSB Range is one of the most automated shot blasting machines available. Reduce labor costs and increase your productivity with automatic functionalities in the targeting turbines, batching products and profiles, brush height adjustment, and outfeed to further distribution through the production line. Automated in- and outfeeds require very little manual intervention or supervision from your operator.
Reliable & durable
LONGER LIFETIME
VSB Range shot blasting machines are built with superb quality and has proven reliability. With triple housing, a sequential blasting pattern and optional modules for pre-heating and painting, the VSB makes your steel cleaner in a shorter amount of time while saving energy and reducing the need of replacement parts.

Complete surface treatment line
Voortman offers a complete surface treatment line that prepares your products for storage and/or further processing. The VP Primer and VSB Shot blaster can be placed back-to-back to save time, costs and handling space requirements in your production facility. The surface treatment line can be placed at the beginning or end of a Voortman processing line depending on the line’s purpose and goal, workshop layout and steel conditions.
If necessary, a pre-heater and drying tunnel can be added to the surface treatment line. Depending on your output requirements and the size of the profiles, a surface treatment line can be chosen to match. The line is completely autonomous with automatic infeed and outfeed, allowing your operators to focus on feeding and unloading the system.
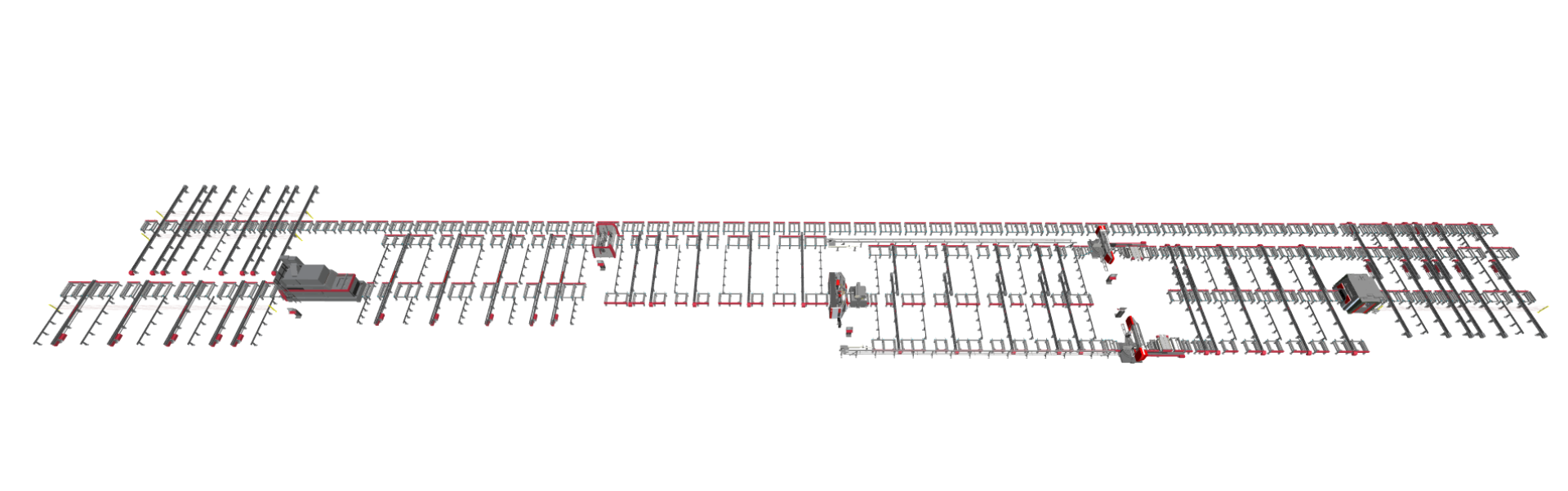
Reduce labor costs and increase efficiency
MSI, also referred to as Multi System Integration, opens the door to fully automate your production by connecting machines with cross transports, roller conveyors, product buffers, and material sensors. Production data only needs to be imported once and then MSI automatically distributes the data to all machines integrated in your production system.
Vacam decides optimal material route
Based on the production on hand, customer preferences and the available machinery in the MSI-line, VACAM automatically decides the optimal route to reach the highest efficiency. MSI designates the end of transporting raw profiles and semi-finished products from machine to machine. MSI stands for one integrated production system. You can track and monitor every profile, product and future planning in real time by using VACAM, Voortman’s proprietary CNC control software installed on every machine.
Designing your optimal layout
Together with you, the Voortman team designs the entire layout based on your current or expected production characteristics, such as type of profiles, product length, number of processes, hours in your work week and budget.
Specifications
Voortman VSB Range | ||||
---|---|---|---|---|
VSB1500-4/15 | VSB1500-6/15 | VSB2500-6/15 | ||
Entrance dimensions | feet | 5-1/4 x 2 | 5-1/4 x 2 | 8-1/2 x 2 |
Plate width | inch | 59 | 59 | 98-1/2 |
Profiles | inch | 40 x 12 | 40 x 12 | 40 x 12 |
Turbines | 4 | 6 | 6 | |
Turbine diameter | inch | 15 | 15 | 15 |
Power per turbine | Hp | 20 | 20 | 20 |
Blasting speed | f/min | 4-1/4 - 6 | 6 - 9-1/2 | 4-1/4 - 6 |
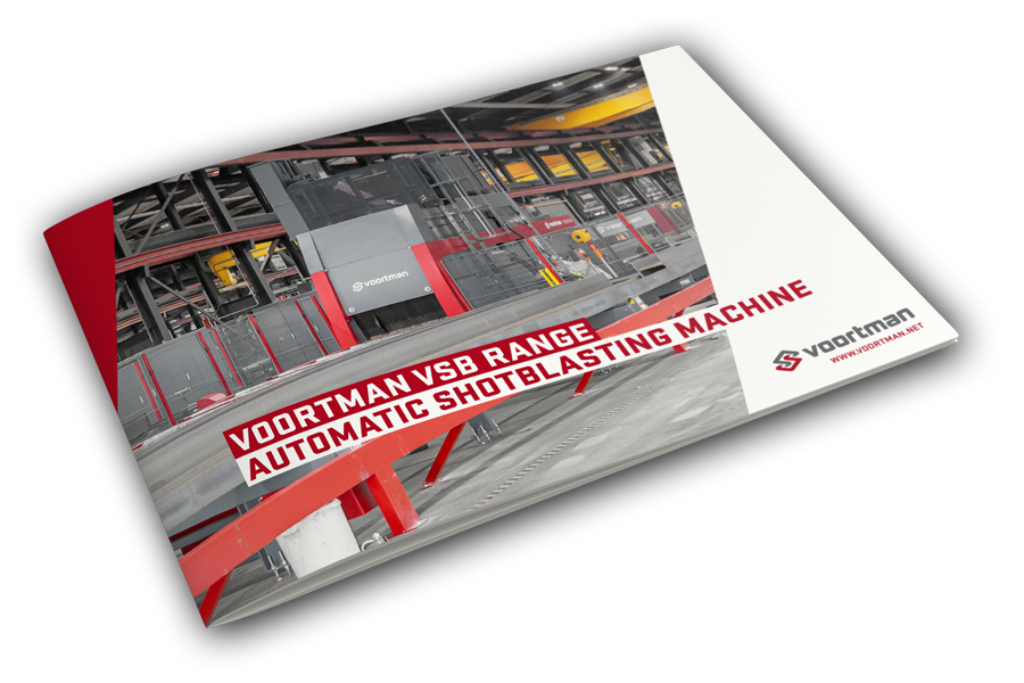