VOORTMAN V623
MOST AUTONOMOUS COMBINED DRILLING, MILLING & SAWING FOR MISCELLANEOUS STEEL
Introducing the Voortman V623, a high-performance drilling, milling, and sawing machine designed for unmanned operation. Compact and user-friendly, it features robust construction and three powerful drilling spindles. Designed to handle a wide range of profiles, the V623 ensures efficient output with optimal sequencing.
The innovative gripper truck allows automatic loading of nearly any profile, enhancing speed and efficiency without operator intervention. Equipped with advanced VACAM control software, the V623 provides full visibility of all buffers, ensuring seamless process management. With the Voortman V623, you elevate your production capabilities to new heights.
YOU’RE NOT JUST GETTING A MACHINE
YOU’RE GETTING A RELIABLE PARTNER
Meet the Voortman V623, your new best friend in drilling, milling, and sawing. This machine is designed to work tirelessly, even when you’re not around, thanks to its ability to operate unmanned for long periods. Despite its compact size, it’s incredibly user-friendly and built to last, with three powerful drilling spindles that deliver top-notch performance and quality.
The V623 can handle almost any profile up to 300 x 300 mm (11-13/16" x 11-13/16"), producing them in a logical sequence for optimal efficiency. Plus, safety is a top priority, so you can trust that it’s designed to keep everything running smoothly and securely.
And let’s not forget about the VACAM control software. This powerful tool helps operators work even more efficiently, providing full visibility of all buffers on the infeed, outfeed, and short product removal. With the Voortman V623, you’re not just getting a machine – you’re getting a reliable partner that takes your production process to the next level.
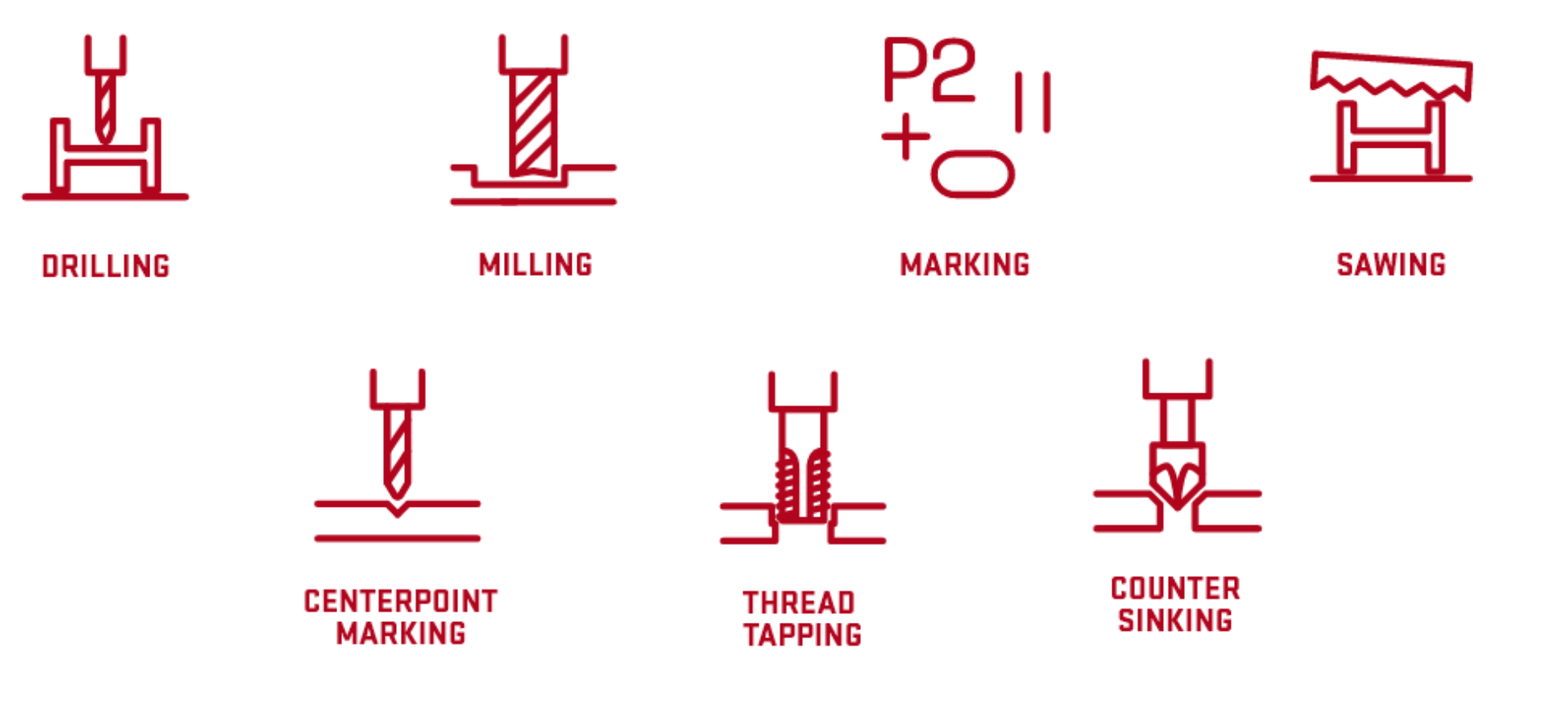
MOST AUTONOMOUS PRODUCTION
The V623 system enhances drilling efficiency with its central storage for 42 tools, allowing seamless and automatic tool switching. Operators can easily add and swap tools without stopping the machine, thanks to an automated tool handler and accessible housing. This setup ensures precise tool measurements and high accuracy for the drilling spindles.
The unique V623 gripper truck, with its chain-driven gripper jaw, handles profiles of any size or shape quickly and safely at speeds up to 60 m/min, applying just the right pressure via a hydraulic cylinder. An intelligent sensor identifies materials swiftly, ensuring efficient feeding of various lengths. Additionally, the robust chain mechanism safely transports profiles up to 12 tons, ensuring smooth, uninterrupted production and extended unmanned operation.
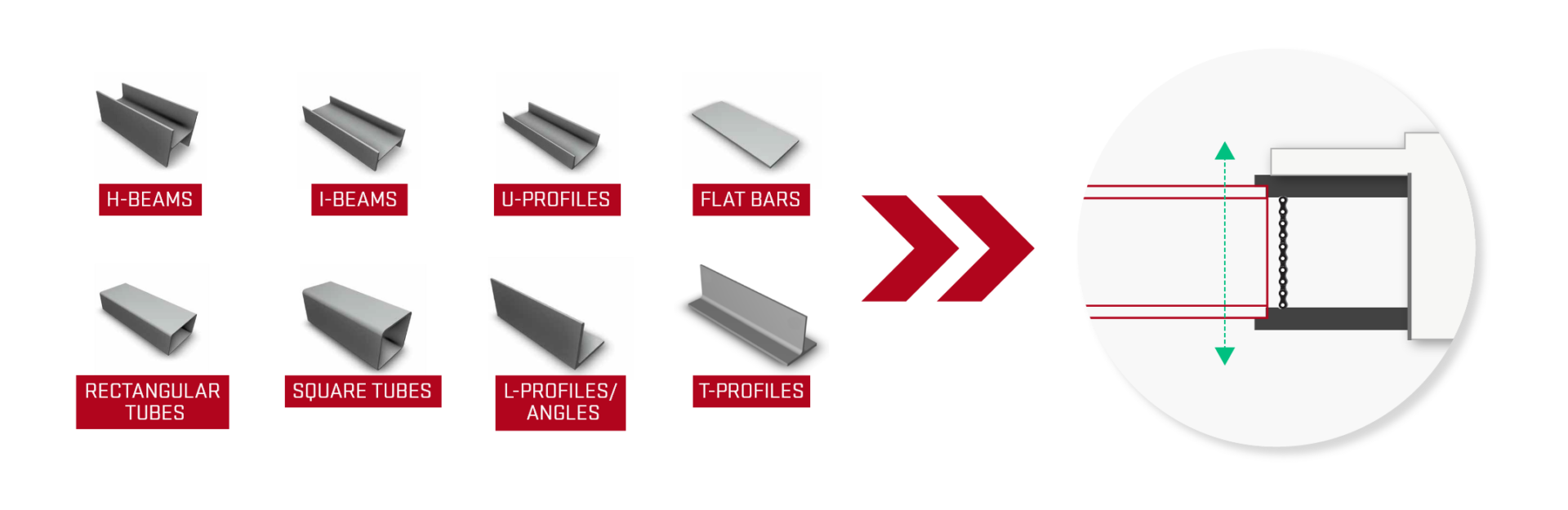
EMPOWERING FLEXIBILITY
The V623 machine enhances profile machining with three drilling units for simultaneous flange and web processing, significantly speeding up operations. Ideal for HSS and carbide tools, it excels in drilling, milling, tapping, and marking. The versatile SK40 units handle holes and milling with precision, supporting tool diameters from 10 to 25 mm (3/8 to 1 inch) and ensuring stability with a robust frame and vibration-eliminating clamp system.
Automated layout marking reduces errors and boosts efficiency, while a separate unit ensures precise underside marking. Hydraulic clamps and pneumatic height measurement maintain stability and accuracy, making the V623 perfect for smooth, precise, and efficient machining.
EVERYONE CAN MILL
No knowledge required with automatic milling paths
You can create any contour with the push of a button, without limitations or additional knowledge required. Our VACAM Software allows your detailers to do what they do best - constructing - whereafter VACAM does the rest!
- No expertise needed
- No programming needed
- Not dependent on operators
Having explored the benefits of the milling process, you may be wondering what's next. Are you able to work with this? Of course! Unlike other companies, we make it very simple for you.
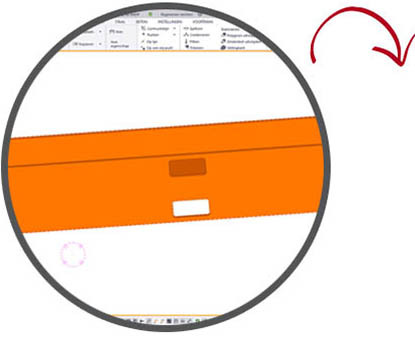
1
DETAIL IN CAD
As you are used to; construct with your detailing software.
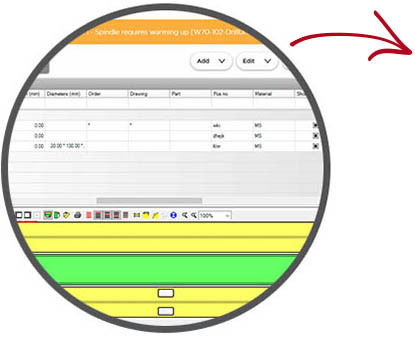
2
SEND TO VACAM
VACAM automatically recognizes the shape of a contour, ensuring that it conforms to the position and material of the part to ensure manufacturability.
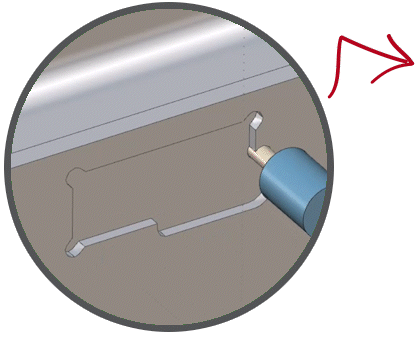
3
THE PERFECT MIX
Our milling module automatically defines the best tools and parameters, which results in the most efficient milling path. Voortman Research and Development has conducted extensive testing to arrive at the right mix of templates for each contour, each type of profile. A unique combination of mechanical engineering and steel construction expertise.
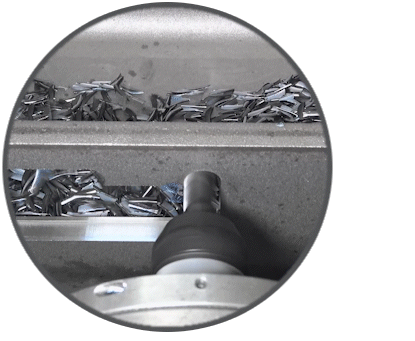
4
START
Push a button and get what you want. It has never been this easy.
One-pass milling
divided into two milling packages
ADVANCED SAWING
Our advanced saw is designed to revolutionize your workflow. Featuring a versatile mitre angle range from -60° to +45° and the outfeed gripper enabling double mitering, this saw expands your project possibilities. The outfeed gripper securely clamps material during sawing, ensuring stability and accuracy with every cut. Cables and hoses are conveniently placed above the saw for easy access and effortless cleaning. The smaller 41 x 1.3 mm (1 5/8 x 1/20 inches) saw blade achieves speeds of up to 10 mm/sec (0.4 inch/sec), delivering exceptional speed and power for even the most demanding tasks.
OPTIMAL UTILIZATION OF FLOOR SPACE
Our outfeed system revolutionizes your production workflow by seamlessly transporting products across various zones and boosting productivity. With an intelligent sensor ensuring precise product positioning and a pneumatic drag-dog system gently guiding items along customizable cross transports, efficiency is at its peak.
The V623 automatic discharge system efficiently handles clean cuts, offcuts, and short products, eliminating manual clean-up and managing saw chips to keep your work area tidy. Capable of accommodating double miter products up to 500 mm (20 inches), our robust conveyor belt swiftly removes offcuts, enhancing operational speed. The product division system further extends unmanned production periods, managing workflows with a 2700 mm (106.3 inches) wide output and a 2600 kg (5732 lbs) capacity, all while maintaining a noiseless environment.

EASE OF OPERATION
Operators can now focus on their work instead of wasting time on cleanup and maintenance, thanks to the V623 machine's innovative features. Internally cooled drills minimize residue, extend tool life, and reduce cleaning time by deploying a mist of oil and compressed air, while a chip conveyor efficiently removes drilling and milling debris. The saw section's overhead cable and hose design enhances safety and reduces maintenance costs.
Loading materials is smooth and efficient, with pneumatic drag-dogs and silencers ensuring precise and quiet operations. Advanced dual light curtains and an automatic hatch for tool changes ensure safety and minimal downtime. The 24-inch multi-touch control panel, combined with intuitive VACAM software and network connectivity, streamlines workflow. Additionally, Hakorit sound-damping strips on pneumatic drag-dogs enhance the handling of steel profiles, creating a quieter and more efficient workplace.
INTEGRATION IS SIMPLE
DSTV and DSTV+ (nesting) import and produce parts and nestings without any programming. VACAM also supports manual creation of optimal nestings based on single DSTV files and can even export these as DSTV+ macros to make the creation or editing from parts in VACAM and on the machine a lot easier.
VACAM CONTROLS ALL MACHINES
Once an operator learns to use VACAM on one machine, they can effortlessly operate any other Voortman machine. All Voortman machines feature the same user-friendly VACAM software, ensuring consistent system component behavior across the board. This uniformity allows operators to switch between machines with ease, without having to relearn command locations or control screen settings after the initial VACAM training. The visual interface and user experience are standardized across all Voortman machines, providing a familiar and intuitive environment for operators.
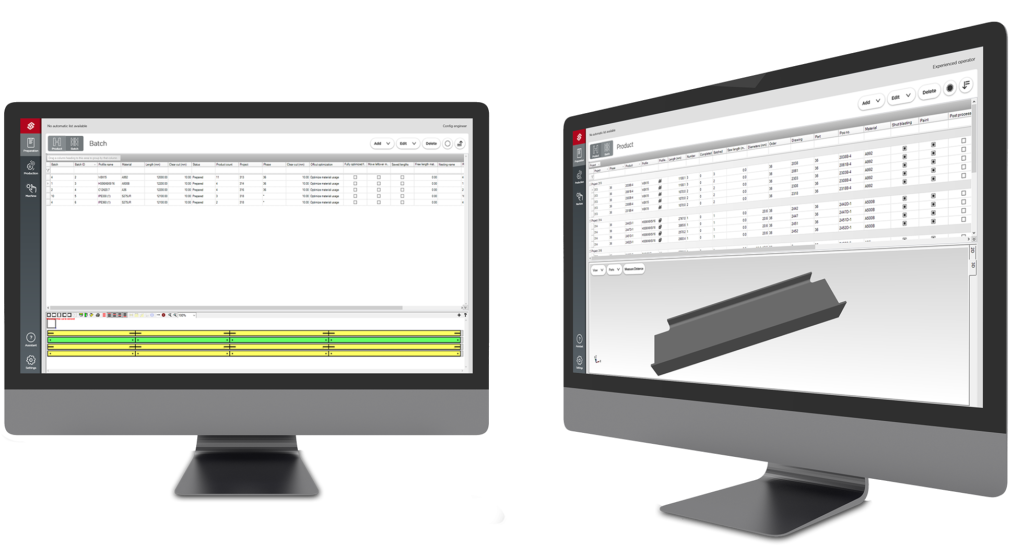
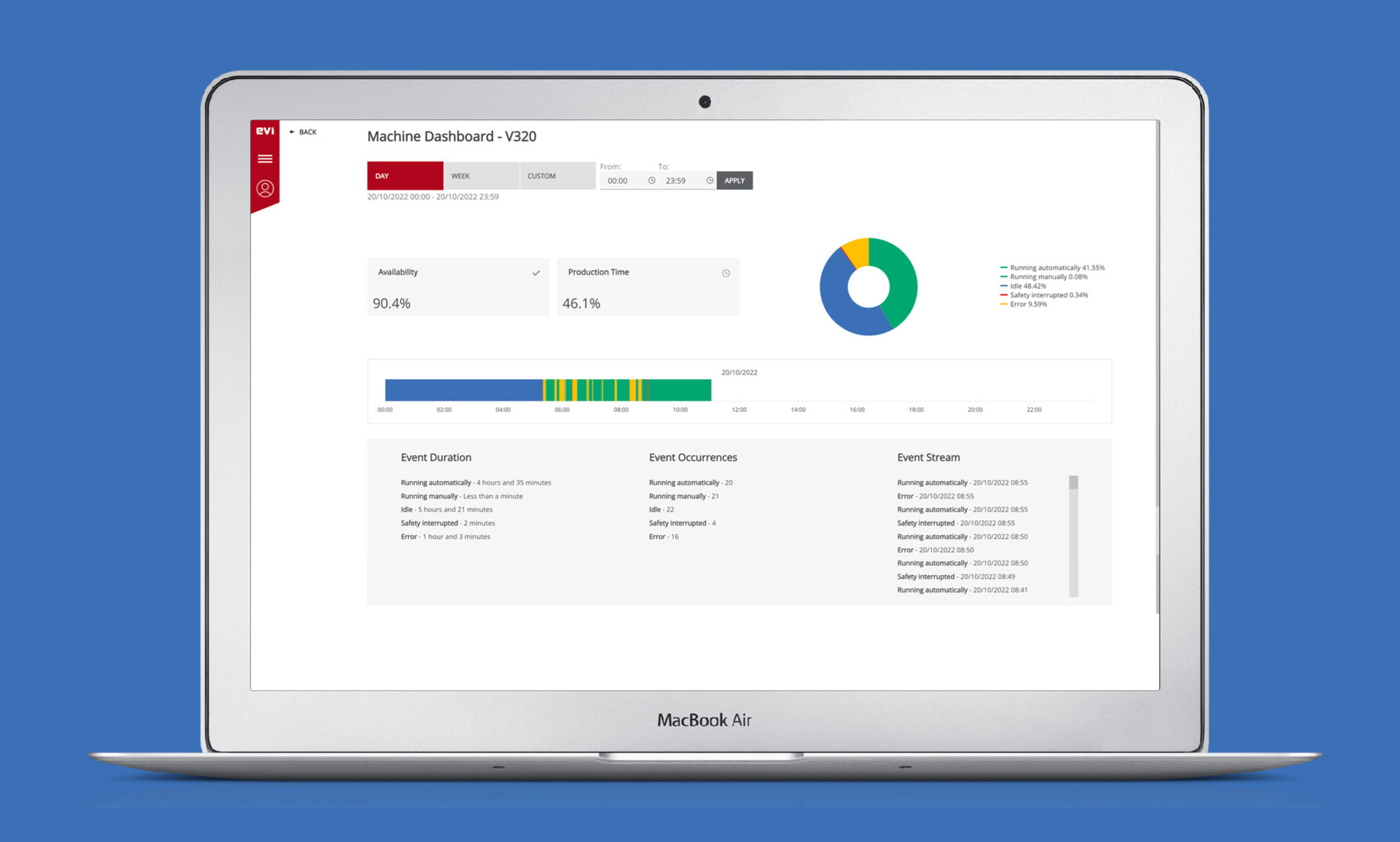
Meet EVI
EVI is your go-to digital assistant for machine monitoring and insights. Whether the machine is on, off, running, or idle, EVI keeps you informed. With seamless connectivity, EVI ensures you're always in the loop through the EVI app on your mobile phone, tablet, or the EVI webpage on your laptop.
EVI's instant notifications alert you if the machine stops or isn't running correctly, making it as convenient as instant messaging. By closely monitoring the machine, EVI aims to:
- Increase output
- Prevent downtime
- Improve production efficiency
- Free operators from constant supervision
EVI is your reliable software solution for optimizing machine performance.
Specifications Voortman V623
The Voortman V623 | |||
---|---|---|---|
Voortman V623 | Drill | Voortman V623 | Saw | ||
Operating range | inch | 7/32 – 12 - 1-1/2 – 12 | - |
Material weight | lbs. | 4,000 | - |
Linear material weight | lbs./ft | 67 | - |
Machining and positioning | Servo motors | - | - |
Spindles | 3 | - | |
Positioning speed X | ft/min | 197 | - |
Rotational speed | rpm | 0 – 5,600 | - |
Tool changer | Tools for all three units | 42 | - |
Tool holder | SK40 | - | |
Drilling diameter | inch | 13/64 – 1 37/64 | - |
Thread tapping | M6 – M30 | - | |
Drilling machine weight | lbs. | 13,500 | - |
Operating range 0° | inch | - | 12 x 12 |
Operating range 15° | inch | - | 12 x 12 |
Operating range 30° | inch | - | 12 x 12 |
Operating range 45° | inch | - | 12 x 12 |
Operating range -60° | inch | - | 12 x 10 |
Feed approach speed | inch/sec | - | 0.40 |
Saw band drive | HP | - | 5.5 |
Saw band speed, stepless | ft/min | - | 130 – 440 |
Saw band size | inch | - | 050 band saw blade |
Saw band inclination | - | 8° | |
Sawing machine weight | lbs. | - | 5,100 |