Voortman MO Heavy Duty
The MO Heavy-Duty cuts pipes, vessels, and exchangers up to 4000 mm / 160".
- Complex pipe cutting on large diameter pipes, pressure vessels, heat exchangers, boilers and tanks
- Round pipes and/or dished ends with a maximum diameter of up to 4,000 mm / 160"
- Equipped with 6 CNC-controlled axes
- 3D cutting performed with plasma and oxyfuel
- Extreme solid design
- High-quality, reliable and accurate pipe profiling
INTRODUCTION
The Voortman MO Heavy-Duty is built for extreme 3D profiling. It handles pipes up to Ø4.000 mm with ease. Its 6 CNC-controlled axes, combined with advanced plasma and oxy-fuel cutting, ensure precision and efficiency in the toughest conditions. Designed for heavy industries such as offshore, shipbuilding, and large-scale infrastructure, it handles oversized materials with precision and reliability. When size, strength, and accuracy matter, the MO Heavy-Duty gets the job done.
6 AXIS PROCESSING
EFFICIENT & VERSATILE
HIGH QUALITY AND RELIABILITY
HEAVY-DUTY SERIES
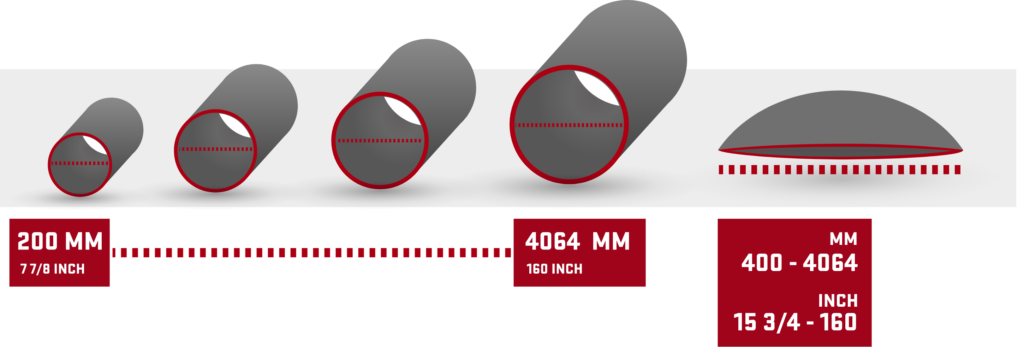
MAIN BENEFITS
UNMATCHED PRECISION
CUSTOMER EXPERIENCE
"We had encountered various cutting machines in the market, but nothing came close to the capabilities of this machine."
Stoney Lake - Vice President Energy Weldfab
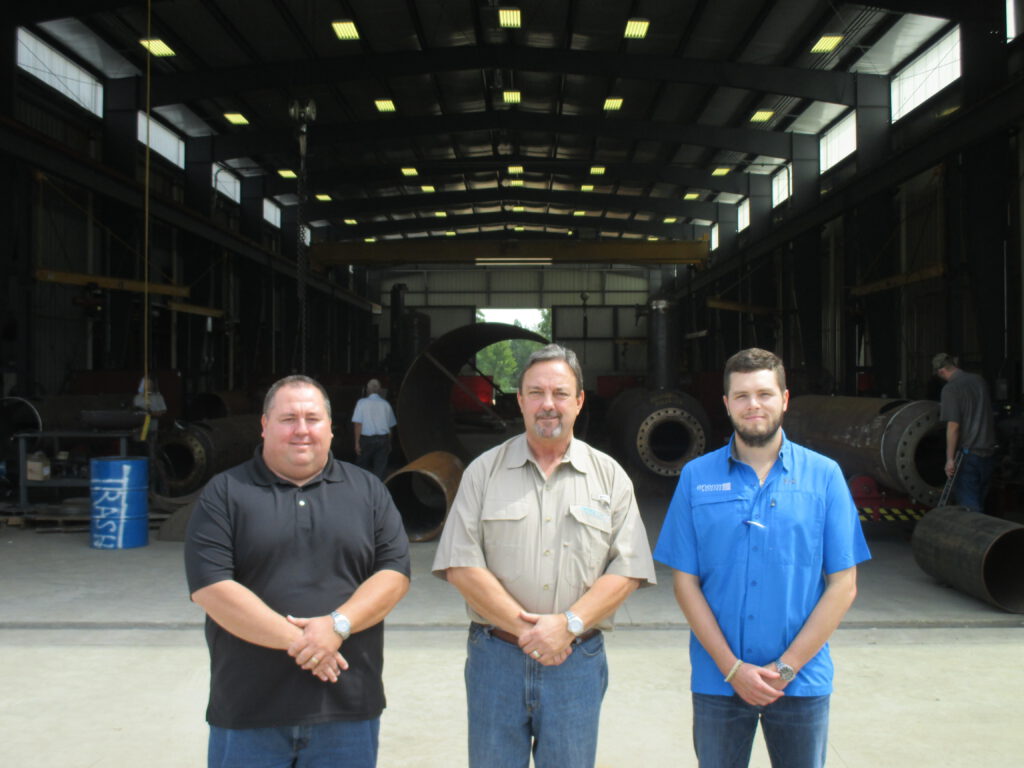
SPECIFICATIONS
Voortman MO Heavy-Duty Series | ||||
---|---|---|---|---|
2500 | 3000 | 4000 | ||
Weight of standard machine | lbs | 48501.698 | 52910.943 | 61729.433 |
Number of CNC axes | axes | 6 | 6 | 6 |
Max. workpiece weight | lbs | 88184.905 | 88184.905 | 88184.905 |
Min. - max. clampable round pipe diameter | inch | 7 7/8 - 100 | 7 7/8 - 120 | 7 7/8 - 160 |
Min. - max. cuttable workpiece length | inch | 11 13/16 - 472 7/16 | 11 13/16 - 472 7/16 | 11 13/16 - 472 7/16 |
Min. - max. wall thickness for cutting with oxy-fuel /plasma | inch | 3/16 - 7 1/16 / 1/16 - 3 1/8 | 3/16 - 7 1/16 / 1/16 - 3 1/8 | 11 13/16 - 472 7/16 |
Max. size of chuck opening | inch | 47 1/4 | 47 1/4 | 59 1/16 |
Min. - max. clampable diameter for dished ends | inch | 15 3/4 - 100 | 15 3/4 - 120 | 15 3/4 - 160 |
Max. torch angle | ° | +/- 70 / 45 | +/- 70 / 45 | +/- 70 / 45 |