Voortman V600
Beam drilling on a small footprint
The Voortman V600 beam drilling machine is ideal for structural steel fabricators and manufacturers alike with limited floor space. The horizontal drill and cabin move along the profile, reducing the footprint while providing a full array of automated functions including drilling, thread-tapping, countersinking, and centerpoint marking.
Extensive capabilities on a small footprint
SMALL FOOTPRINT
The Voortman V600 beam drilling machine is ideal for structural steel fabricators and manufacturers alike with limited floor space. The V600 drilling table is available in various lengths, so it can be supplied to customer requirements. The horizontal drill and cabin move along the product, reducing the overall footprint needed by 50% compared to a machine with cross transports and roller conveyors at the in- and outfeed. This machine brings the power when space is an issue.
Process multiple parts & profiles with a variety of processes
PROCESS MOST PROFILE TYPES
The V600 can process I-Beams, H-Beams, Channels, Flat bar, Angle iron, T-bar, Square tubes and Rectangular tubes. Even profiles which have already been assembled can be further processed on the V600 - all without manual programming in the software, improving your ROI.
FLEXIBLE PROCESSING
The Voortman V600 is able to change up to 5 tools suitable for drilling, thread-tapping, countersinking and centerpoint marking. This amount of tools increases your flexibility and freedom in carrying out a diverse range of processes with the V600.
PROCESS MULTIPLE PARTS LINEARLY
The Voortman V600 can process multiple parts in a row. It is possible to place multiple parts at the table. This saves time, because when the drill is processing the second product, the operator has time to turn the first beam while the machine keeps processing. It is even possible to place multiple products behind each other, so that the machine makes multiple identical products in one operation. During training Voortman trainers will teach you a number of valuable benefits.
INTEGRATION IN YOUR WORKSHOP
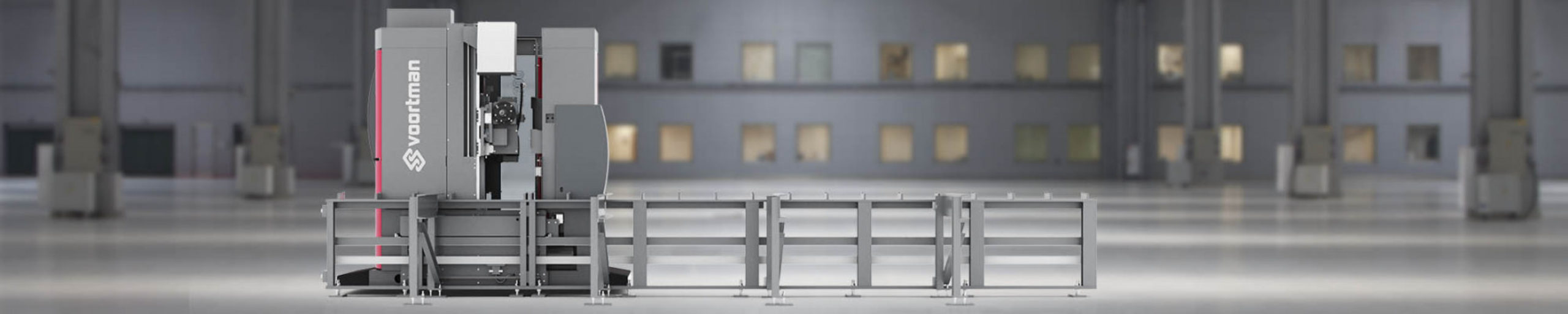
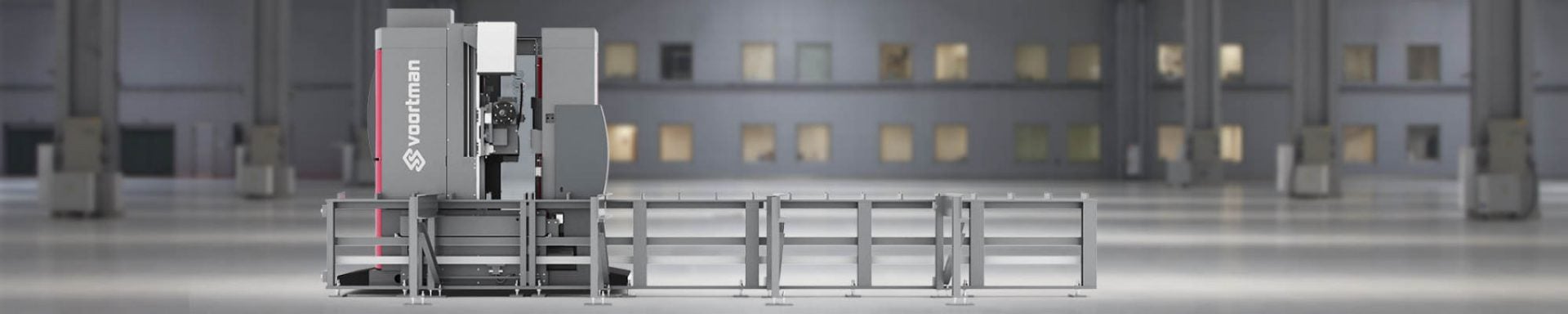
The V600 fits in any workshop with a table that can adjust based on the customer’s requirements in profile length, desired output, type of profiles processed, and products created. The Voortman team will assist you in choosing the correct table length, and the V600 only needs a power supply, giving you freedom to place the machine in the best possible location with fewer issues.
The V600 is extremely flexible. Even if you have profiles longer than the table, the machine can continue operation on these profiles after you’ve moved the profile. The V600 has safety features built-in and doesn’t require fences, giving you access to the V600 from all sides and the ability to connect the machine mechanically with your own storage system or assembly line.
Specifications
Voortman V600 | ||
---|---|---|
Voortman V600 | ||
Operating range | inch | 1-3/8 - 42 |
Working height | inch | 36 |
Drilling and positioning | Servo motors | |
Positioning speed X | f/min | 100 |
Positioning speed Y | f/min | 115 |
Positioning speed Z | f/min | 100 |
Drilling units | Horizontal | 1 |
Nominal power | Hp | 40 |
Speed | rpm (stepless) | 0 - 2.500 |
Tool changer | 1 x 5 | |
Drill holder | SK40 | |
Drill diameter | inch | 13/64 - 1-9/16 |
Thread tapping | M6 - M30 | |
Machine weight | lbs | 6,600 |