thyssenkrupp Materials Nederland makes significant efficiency leap with innovative Voortman line
thyssenkrupp Materials Services is a leading global materials distributor and service provider with approximately 380 locations in more than 30 countries. The company offers a wide range of materials, including steel, stainless steel, nonferrous metals and plastics, to customers in a variety of industries. Recently, thyssenkrupp Materials Nederland invested in an advanced production line from Voortman Steel Machinery for its Veghel headquarters.
Beams, profiles, tubes and bar steel are sawed, blasted, painted, drilled and milled at high speed. This will be happening at thyssenkrupp Materials Nederland in one process; faster, more precise, fully automated and with customized solutions. The improved process offers customers in the metalworking industry more and even more accurate machining possibilities with shorter lead times, from work preparation to shipping.
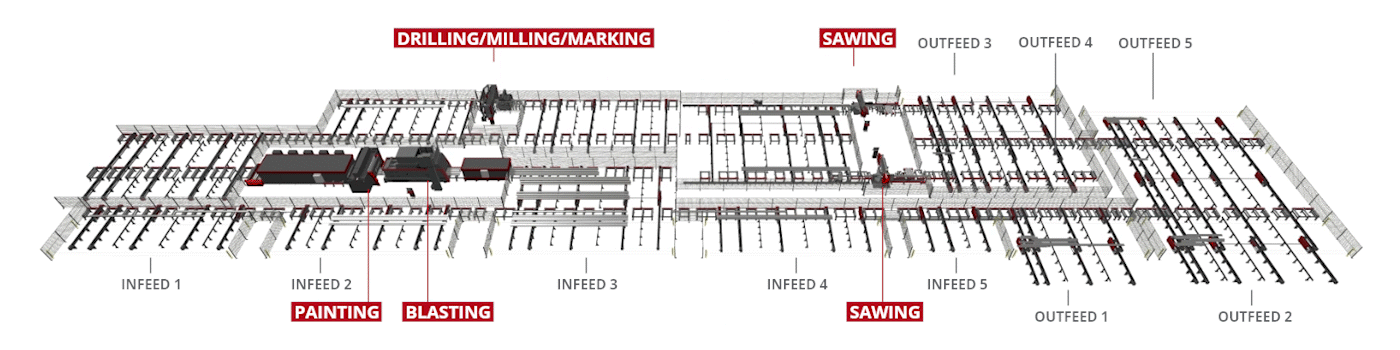
From separate processes to fully automated complete solution
Where the company initially focused on separate processes such as blasting, spraying and sawing profiles, the company recognizes that this process can be organized more efficiently and that customers today are looking for completely processed products and a total solution. One of the reasons is to save time or reduce pressure on manpower. Aware of these challenges, thyssenkrupp Materials Nederland sees adding processes with an optimal automated logistics flow as the key to success.
This vision has led to the investment in an advanced Voortman production line consisting of five machines: two identical VB series sawing machines, the Voortman V631 drilling and milling machine and the blasting and painting line consisting of a Voortman VSB series and VP series. With drilling and milling added, the company can offer customers a more complete package of operations. It represents another step in relieving customers by reducing internal handling.
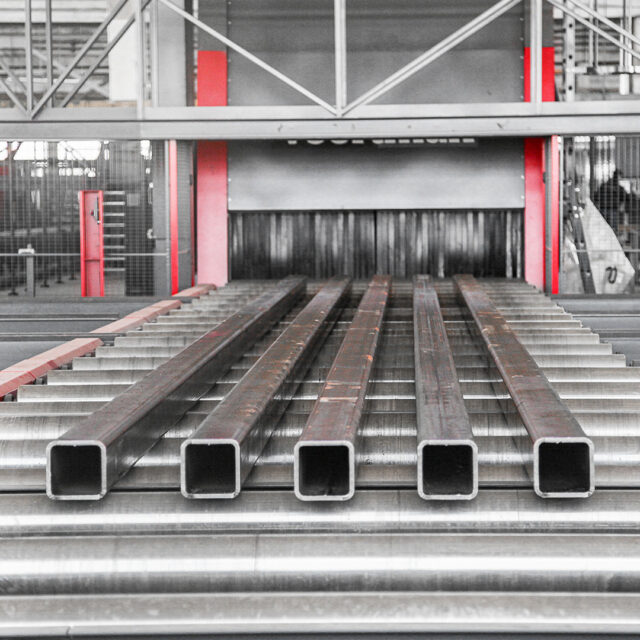
Materials are blasted and painted by the automated surface treatment line. The blasting machine is aligned with the capacity of the entire line.
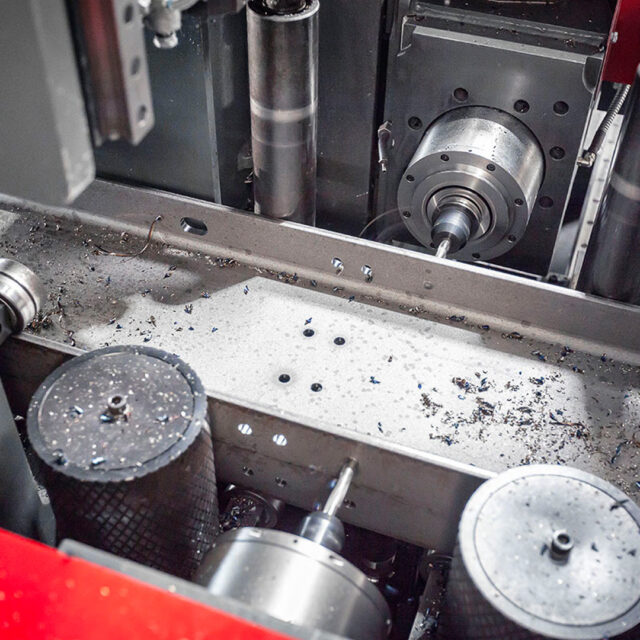
Current processes are expanded with drilling, milling, tapping and marking operations.
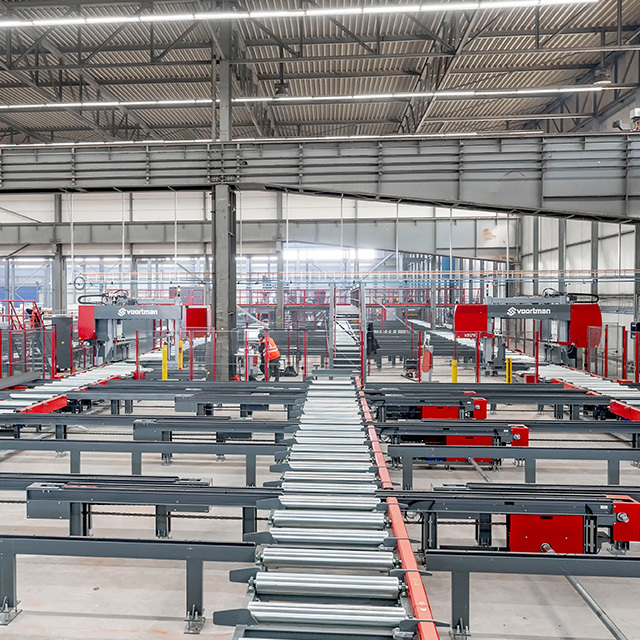
Two Voortman band saws balance the workload.
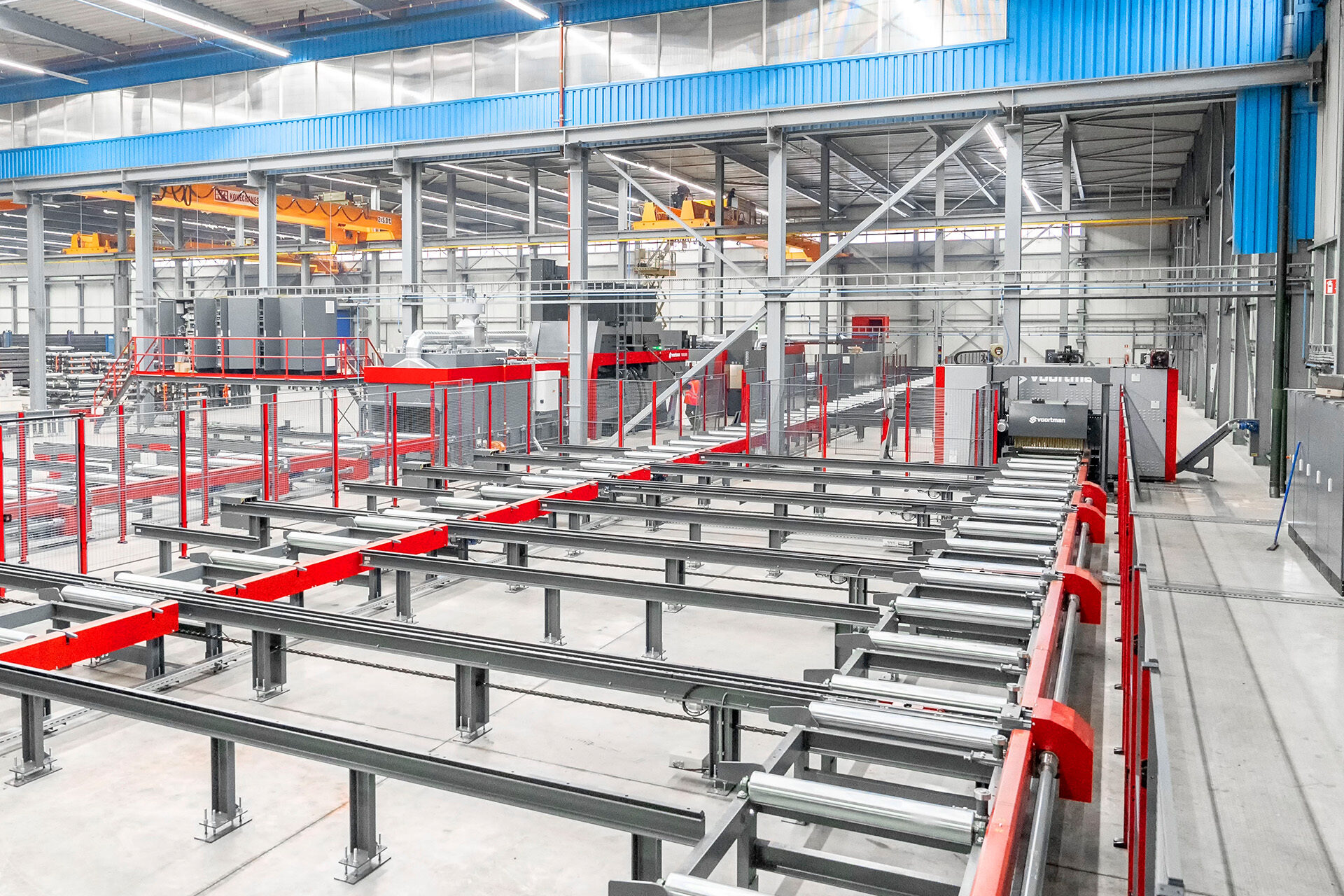
Transforming into a full-service one-stop-shop
"Important step to support our customers even better"
"With this investment, customers can expect more machining capabilities from us with higher efficiency and flexibility. With this we are taking an important step to support them even better." said Peter Henne, general manager thyssenkrupp Materials Nederland. "The choice to cooperate with Voortman to renew the production process in Veghel was a logical one, as both companies are well acquainted with each other; Voortman has been a valued customer of thyssenkrupp Materials Netherlands for quite some time."
Efficiency and reliability anchored in logistics flow
The development of this optimal production line required a thorough analysis of thyssenkrupp's production data and product mix over the past year. Voortman designed and evaluated various layouts and scenarios. The result is an optimized layout in which steel beams, profiles and bar steel are processed via streamlined efficient routes.
Profiles are first blasted and painted fully automatically by the blasting and painting line and then go either through the Voortman V631 profile drilling and milling machine or directly to one of the two Voortman VB saws, both equipped with a short piece removal system. It is a continuous process where the next profiles are already buffered and automatically transported to the next machine in the line to one of the outfeed locations. Once there, the Smart Unloading screens significantly speed up the sorting and shipping process by easily displaying which profiles are ready for shipment to the customer. The complete line ensures product traceability, allowing thyssenkrupp to remain "in control" at all times and guarantee reliable delivery times.
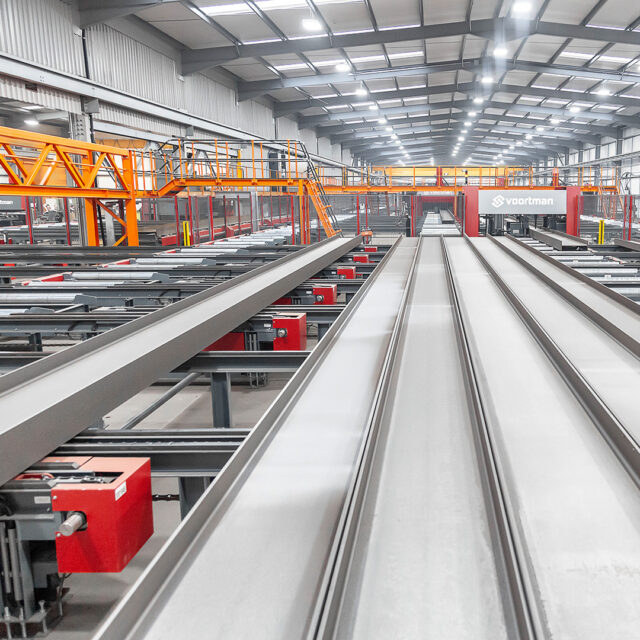
Materials are continuously buffered to the datum line. With automatic buffering and load balancing between machines, bottlenecks are eliminated when one process is faster than another.
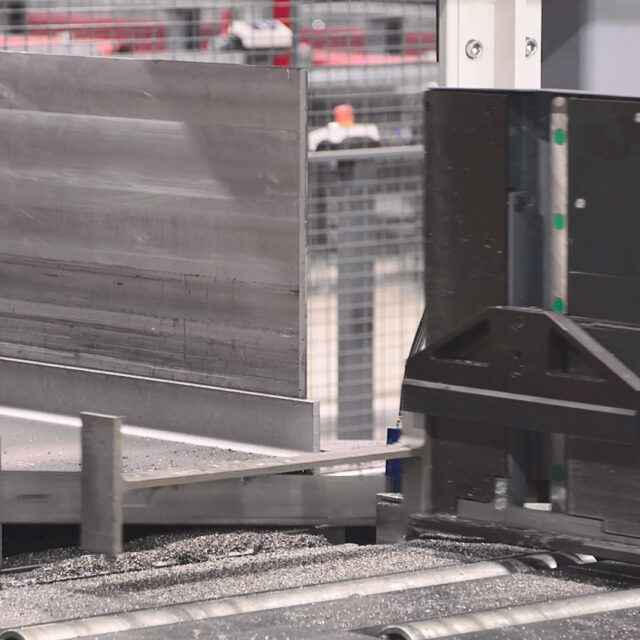
Both saws are equipped with an automatic short piece removal system that automatically removes small products to keep production running autonomously.
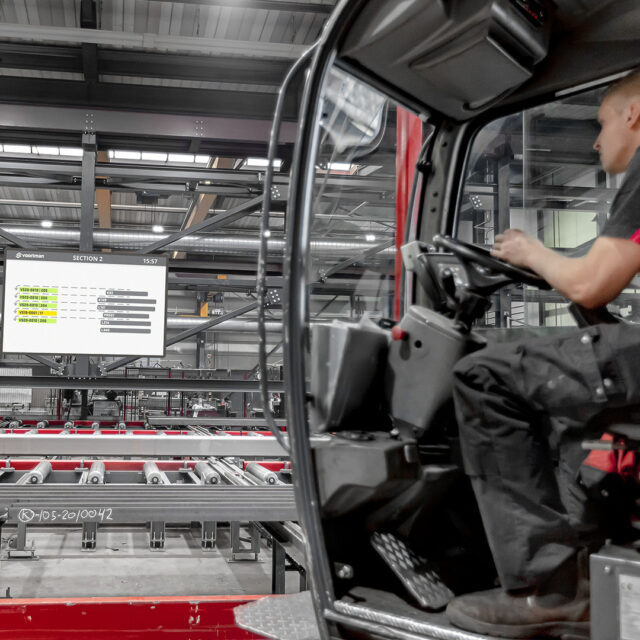
Sorting is made easy at the outfeed zones with Smart Unloading. Screens indicate which profiles are ready to be shipped.
Ready to take YOUR business to unprecedented heights?
Do you also want to stay competitive in a rapidly changing manufacturing landscape? To stay ahead and achieve long-term success, it's crucial to become a one-stop-shop that adds value for your customers, find the optimal logistics route and create transparency in your value chain through automation and digitization. At Voortman, we understand your unique challenges and are here to support your path to success.