THE MOST AUTOMATED SURFACE TREATMENT LINE
Home | Knowledgebase| The most automated surface treatment line
We offer a complete surface treatment line that prepares your products for further processing. The VP Primer and VSB Shot blaster can be placed back-to-back to save time, costs and handling space requirements in your production facility. The surface treatment line can be placed at the beginning or end of a Voortman processing line depending on the line’s purpose and goal, workshop layout and steel conditions.
If necessary, a pre-heater and drying tunnel can be added to the surface treatment line. Depending on your output requirements and the size of the profiles, a surface treatment line can be chosen to match. The line is completely autonomous with automatic infeed and outfeed, allowing your operators to focus on feeding and unloading the system.
"The guys running the machine are happen to work a lot harder than they used to. Feeding and unloading it as quick as they can, because the machine is definitely putting it through very fast!" Ed Bare | Manager Steel and Pipe Supply, Kansas USA | ![]() |
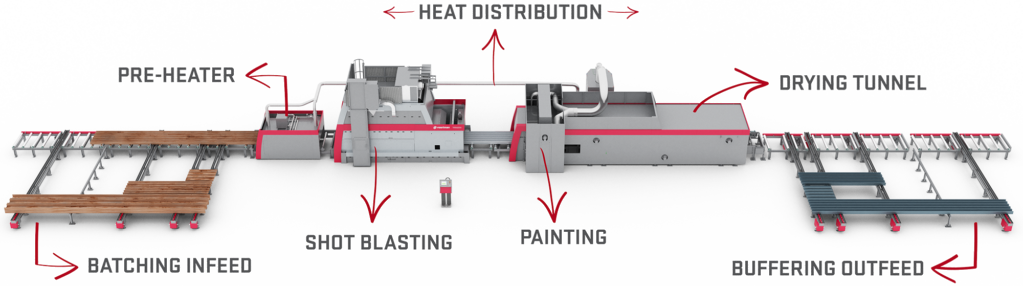
How about a complete blasting-painting system?
This complete surface treatment line saves a considerable amount of
space, time and money. The automatic height adjustment also ensures that the process is highly accurate, which results in perfectly blasted and painted profiles. The infeed and outfeed of the entire blasting-painting system is fully automatic, allowing your operator to focus solely on
loading and unloading profiles.
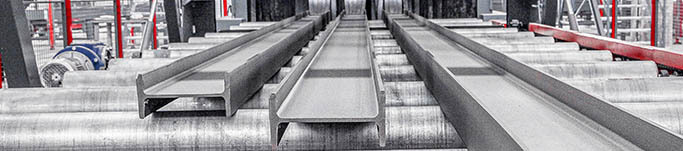
VOORTMAN SHOT BLASTING
VSB Range shot blasting machines are built with superb quality and has proven reliability. With triple housing, a sequential blasting pattern and optional modules for pre-heating and painting, the VSB makes your steel cleaner in a shorter amount of time while saving energy and reducing the need of replacement parts.
The shot blast grit is transported up by an elevator to the separator, where not usable grit is separated from the usable grit and is collected in the grit bunker for re-use. By doing this the next round of shot blasting can be carried out with premium shot blasting grit, meeting the SA2.5 quality norm in the most efficient way.
By blasting at the beginning of the line, rough lengths with the same dimensions can be clustered by your operator and loaded onto the line, resulting in a loading efficiency of 70 to 80%.
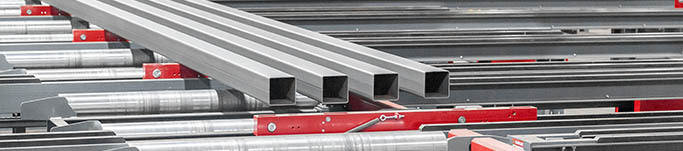
- Our batching functionality automatically positions your profiles at the correct distance and spacing from one another. No edges are left uncovered by turbines with automatically adjustable grid radius;
- Our software automates all of the essential parameters involved in blasting;
- Blowers and brush height adjustments guarantee that all grid recycles inside the blasting container and clean products are outfeed for further distribution.
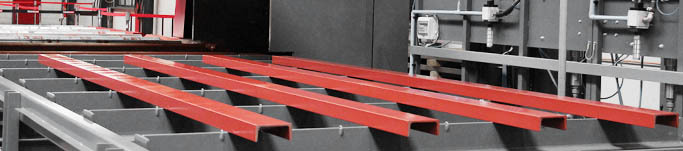
VOORTMAN PAINTING
The VP Range painting machine automatically detects the material dimensions, so it only sprays paint when material is present. This reduces wear on the machine and saves on paint consumables cost. A light barrier near the infeed measures material before entering the VP Range. Then, the upper paint trolley automatically adjusts to the correct height to guarantee an accurate painting process.
- Automatically detects the material and only sprays when material is actually present;
- The automatic height adjustment also ensures that the painting process takes place very accurately with perfectly blasted and painted rough lengths as a result;
- The machine can use various types of paint, including solvent-based and water-based paint. It can automatically switch between different colors or types of paint;
- Save on energy costs with our economical and energy-efficient drying tunnel.
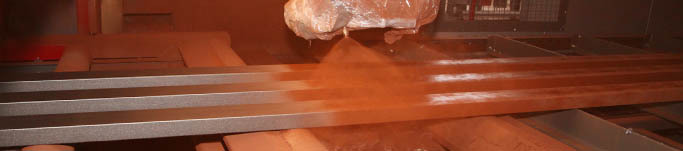
The inside of the painting cabin is layered with a special protective coating to make cleaning easy. Transparent plastic film is placed over the floor and in front of the interior lights. Turning the plastic film replaces the dirty section with new clean plastic, simplifying the cleaning process for your operator. Adding heating in the floor is optional, to speed up the cleaning process.
The paint trolleys inside the machine have their drive chains all connected to the same motor. This guarantees synchronized movement. The trolleys can be fitted with 3 sets of nozzles so you can automatically switch between different paint types.
RAINHAM STEEL IS RUNNING AT FULL CAPACITY
Rainham Steel, a major steel distributor in the UK since 1973, is committed to meeting its customers' demands in a timely and complete manner. With this in mind and the need to increase capacity, the company invested in a Voortman MSI line. A shot blasting and painting line combined with a drill-saw, blasts, drills and cuts profiles to length in full automation. Now that the system is running at full capacity, Rainham can take on more jobs than ever before and is even looking to expand further!
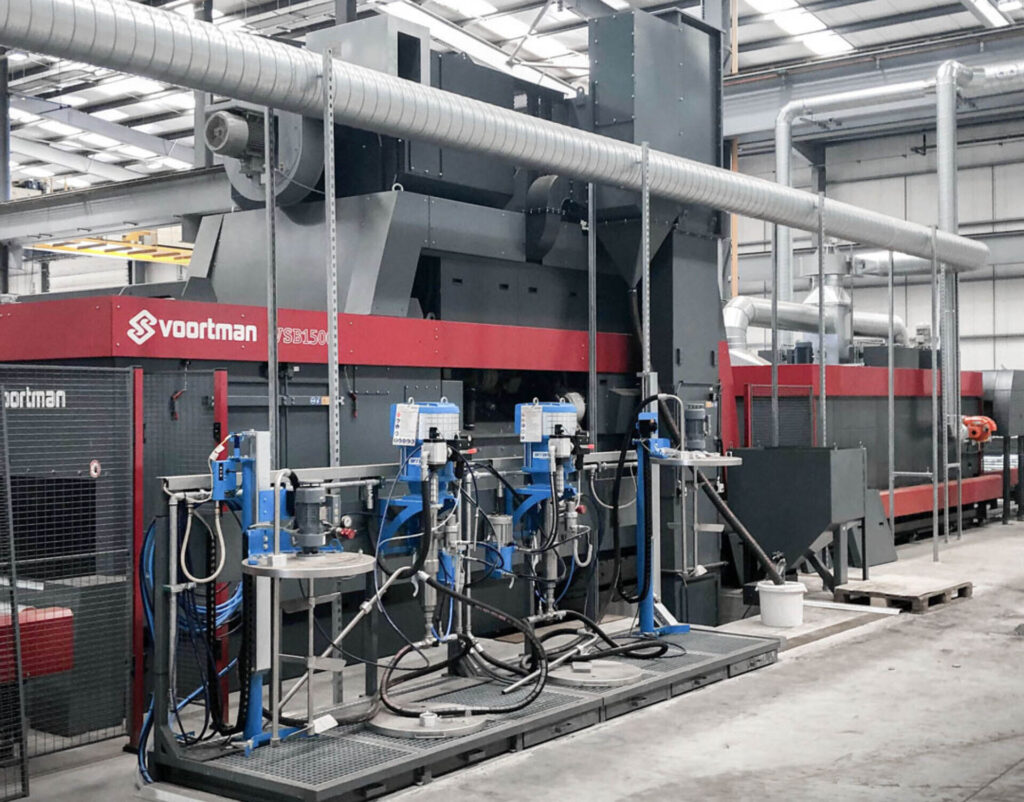