- Automation
- Plate
- Beam
- Cutting
- Plasma
- Quality
- Manufacturing
- Fabrication
- Coping
Hypertherm® XPR300™ - Benefiting from plasma cutting
Extending plasma cutting: Hypertherm® XPR300™
Plasma cutting technology is not new but the capability and performance continues to develop. Voortman introduces the latest in this technology: the new Hypertherm® XPR300™. This new technology is offered on all machines that utilize plasma cutting such as the V303, V304, V310, V320, V325 and the V807.
Advantages of the Hypertherm® XPR300™
The capabilities of plasma are significantly redefined with this XPR300™ plasma source, which provides considerable advantages for your production and ultimately your bottom line. The XPR incorporates X-Definition™ cut quality by encompassing the newest cutting technologies. This superior cut quality is expressed in mild steel with improved angularity. Besides, it is expressed in superior stainless steel cut quality across all thickness ranges because of gas mixing technology and superior results on aluminium by using Vented Water Injection. The capability and accuracy of the Voortman machines maximize the technology. The Voortman bevel head is also designed to take advantage of the improved torch design that enable you to perform bevel cuts up to 50°.
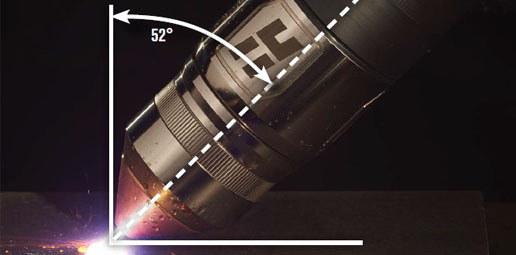
Engineered system optimization
The XPR is engineered with power supply technology which delivers a highly responsive and rapid system feedback and automatically intervenes to eliminate events that negatively impact your system efficiency and consumable life. One of the technologies contributing to these advantages is the Arc response technology™ with automatic torch protection and automatic ramp-down error protection (ARP). First, the torch is protected when consumables are used past their consumable life, which thus extends consumable utilization. Second, the automatic ramp-down error protection improves consumable life by automatically initiating when a cut is about to end in an uncontrolled manner and thereby eliminates the impact of ramp-down errors (see video below).
Optimized productivity and reduced operating costs
When combining the above mentioned factors of superior cut quality and engineered system optimization, your productivity is optimized and your operating costs are reduced. Furthermore, the high cut speed of 300 Amps and the power of 63 kW also contribute to an optimized productivity. Finally, due to the cool nozzle technology which better cools down the nozzle of the new XPR300, consumable life increases which again decreases your overall cutting and operating costs. With all these technologies, the consumable life increases 40% and your operating costs can be reduced by over 50%.