- Automation
- Beam
- MSI
- Plate
- Software
- Fabrication
Designing your layout using a data-driven approach
DATA-DRIVEN APPROACH
Every business and construction is unique and an optimal layout depends on many factors. Voortman uses a data-driven approach, which takes the following factors into account to determine the best layout and configuration to reach your business goals:
- Your processes
- Your production work
- Your workshop space
- Your desired output
- Workload per machine
- Your workshop product flow
- Real-time simulation of configuration running production
- Virtual Reality Experience
Below are some examples of layouts generated for customers using this data-driven approach.
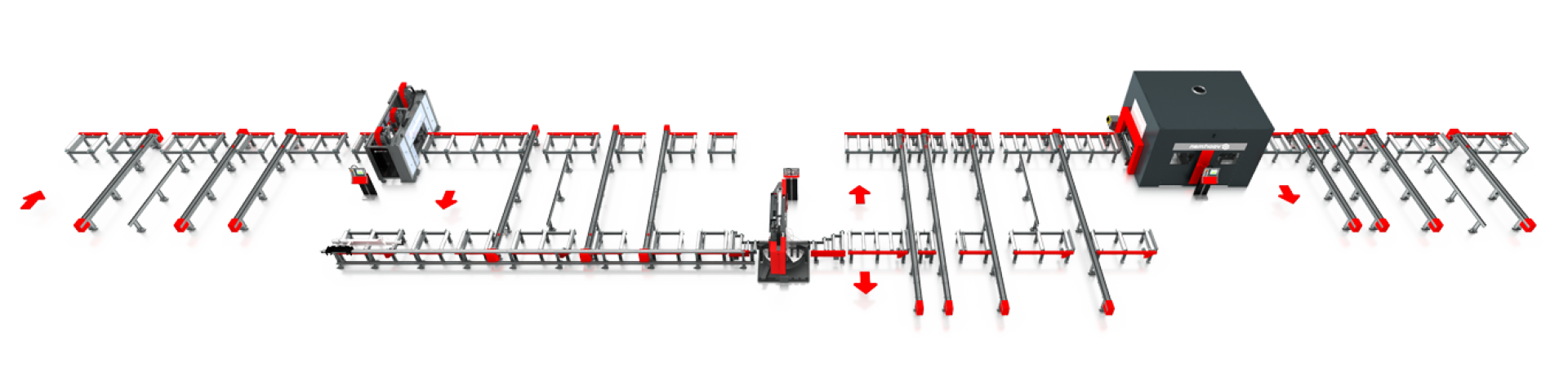
Examples of layouts
Example 1 - Drilling | Sawing | Coping
This example shows the layout and configuration of a medium-sized steel fabricator. In this case nested beams are marked, drilled and milled on the V630 / V631. Profiles are then automatically transported to the VB1050 saw where they are cut-to-length. Finished cut-to-length profiles that don't need additional processing by the coping machine can be transported to the right after passing the saw. When the coper is needed, profiles are automatically transported to the left and moved to the coper so copes, block outs, weld preparations, layout marking and other complex cuts are created
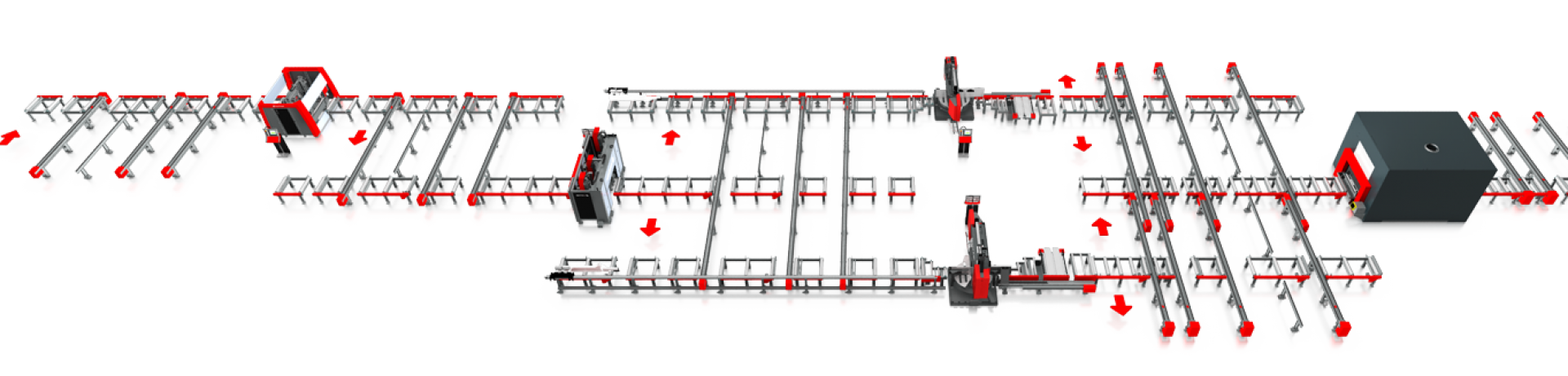
Example 2 - Marking | Drilling | Sawing | Coping
This example shows a layout and configuration at a larger steel fabricator. Voortman's analysis showed that this customer had a lot of marking work in their production, so a separate V704 marking machine was recommended for the layout. This way the V704 marking machine can focus on marking profiles, which are then transported to the V630 / V631 that drills the marked profiles. Positioning the two saws somewhat further down the production line instead of the beginning has the advantage of being faster by requiring fewer front measurements. Full-length raw beams can pass through the marking and drilling units without needing to stop for measuring.
The data also showed that this customer performs more than the usual amount of saw cuts, so it was well worth investing in a highly automatic sawing process with two saws and a short product removal system (SPRS) based on volume. Marked and drilled profiles can be simultaneously cut to length, and short pieces are automatically transported sideways. When the coper is needed, profiles are automatically transported to the coper infeed cross transports for further processing, such as copes, block outs or weld preparations.
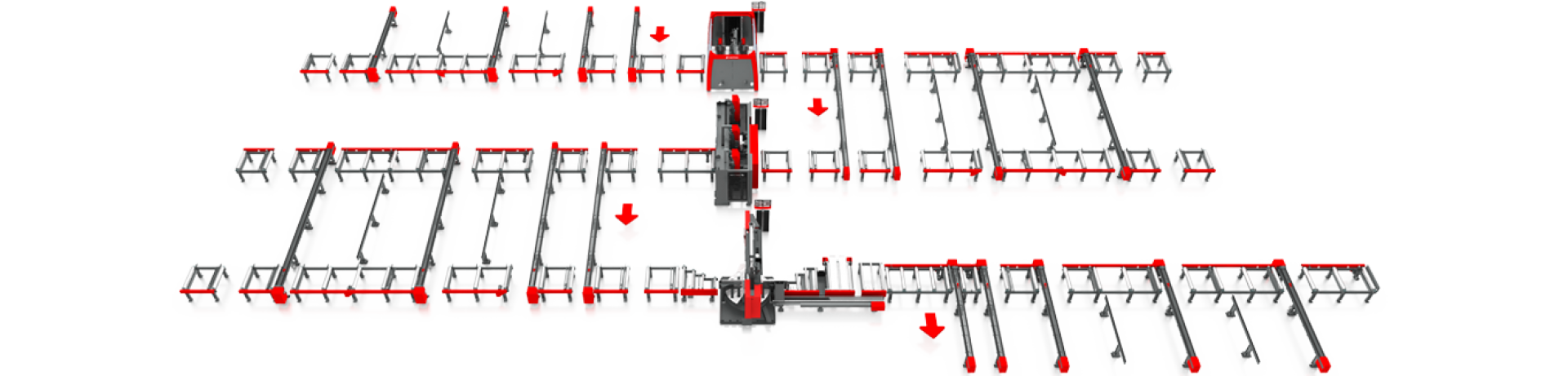
Example 3 - U-Shape Marking | Drilling | Sawing
This example shows a layout and configuration at a customer that had limited workshop floor space. Voortman designed this "double U-shape" configuration to maximize utilization of their floor space. A coping machine was not included in this beam line, since analysis showed this customer did not have sufficient copes and block outs to justify the value of a coping machine. Analysis also recommended adding a separate V704 marking machine to deal with a large volume of layout marking. This way the V630 or V631 drilling machine can focus solely on drilling and milling, increasing its capacity and throughput. The marked, drilled and milled profiles are finally cut-to-length by the VB1050 saw and automatically transported sideways on the outfeed cross transports.
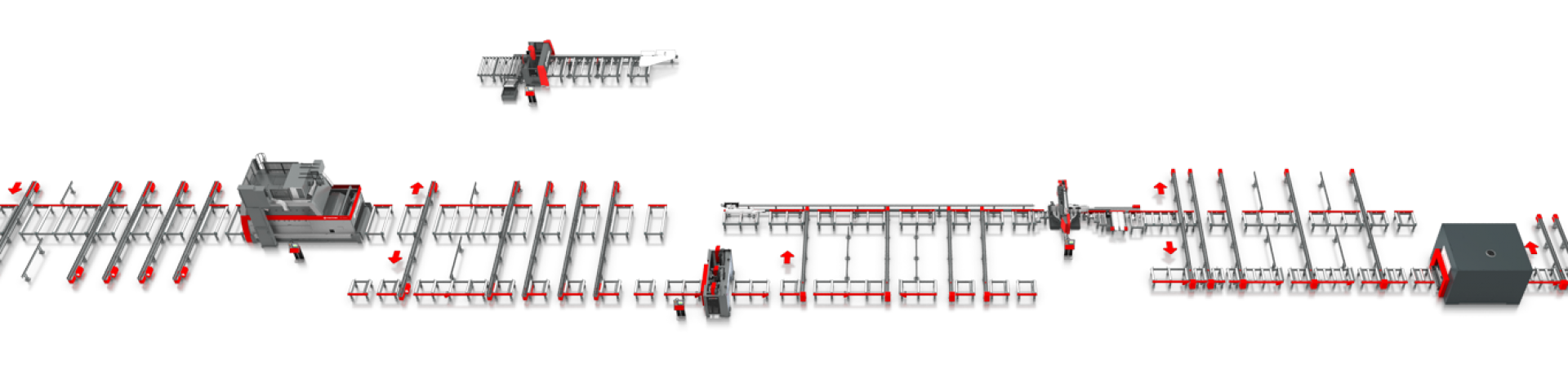
Example 4 - Shot blasting | Drilling | Sawing | Coping | Plate cutting & drilling
This layout and configuration starts with shot blasting nested beams and plates. The advantage to shot blasting at the very beginning of the line is that it provides higher efficiency and less wear on the VSB shot blasting machine. Shot blasted plates are transported to the left to be cut and drilled on the V320 plate cutting & drilling machine. Shot blasted beams are transported to the right and on to the V630/V631 for drilling and marking, and then cut to length with the VB1050 saw. A short product removal system (SPRS) was included on this customer's saw based on the amount of short products in their production. Short products and products which don't need to be processed on the coping robot are transported to the left outfeed cross transports, while profiles that need copes are sent right to the coper.
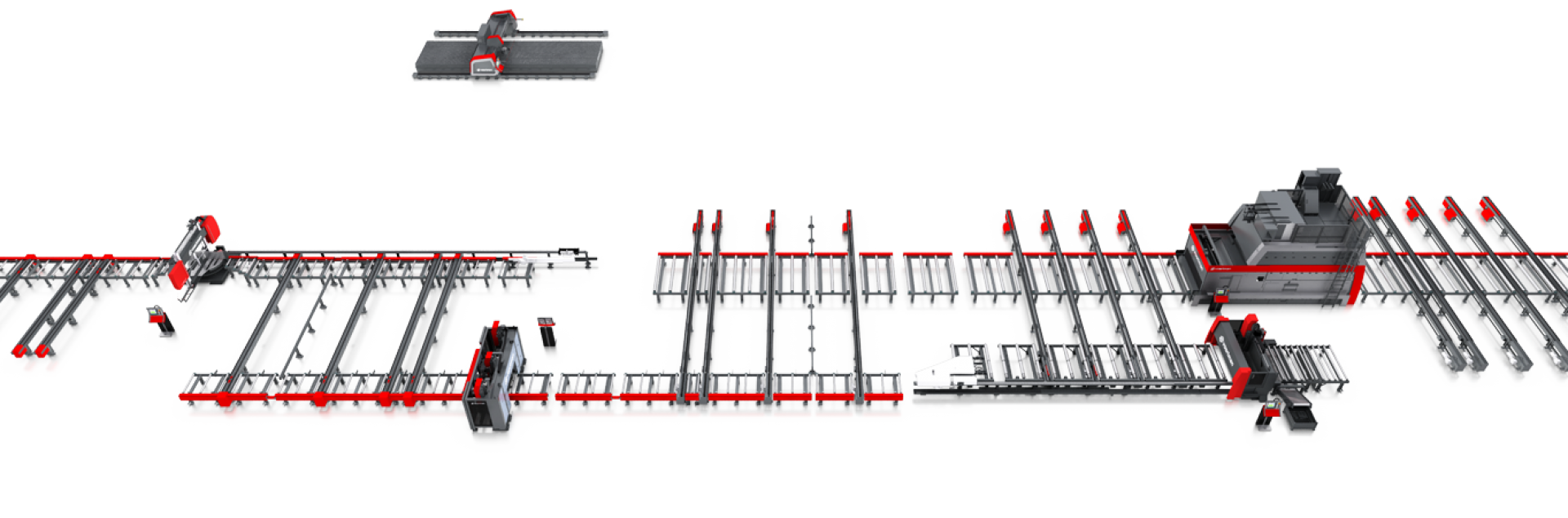
Example 5 - Shot blasting | Plate drilling & cutting | Drilling | Sawing
Similar to Example 4, this customer's layout starts with a VSB shot blasting machine. Shot blasted plates can be processed on the V320 like the previous example, however plates are now automatically transported left to the V320 plate cutting & drilling machine connected to the production line. A stand-alone V304 plate cutting machine was recommended and added since analysis showed that this customer produces a significant amount of larger parts such as plate girders, haunches and strip connections. Shot blasted beams are automatically transported towards the V630 or V631 to drill and mill before finally being cut to length with the VB1050 saw. The customer doesn't produce enough small parts to justify adding a short product removal system (SPRS) in this example.
A fully automated production system
Let's design your layout!
Let's start finding ways to reach your goals! Contact us today for a consultation with one of our experts! With decades of experience, proven solutions and our responsive worldwide service, you can Accelerate Your Performance and make a difference with Voortman and lead the way in your market!