- Plate
- Plasma
- Oxy-fuel
Benefit from magnetic torch mounting
SHARED INNOVATIONS
Because both the plasma and the oxy-fuel torches use the same mounting, they also share all the benefits that come from the built-in technologies. Such as, for example, the fast height control and True Volt.
NO CALLIBRATION NEEDED
This is a magnetic mounting with only 2 perfectly attuned drives, independent of any form of tolerances with no calibration required. In addition to these advantages, the magnetic mounting also influences the speed in the production process.
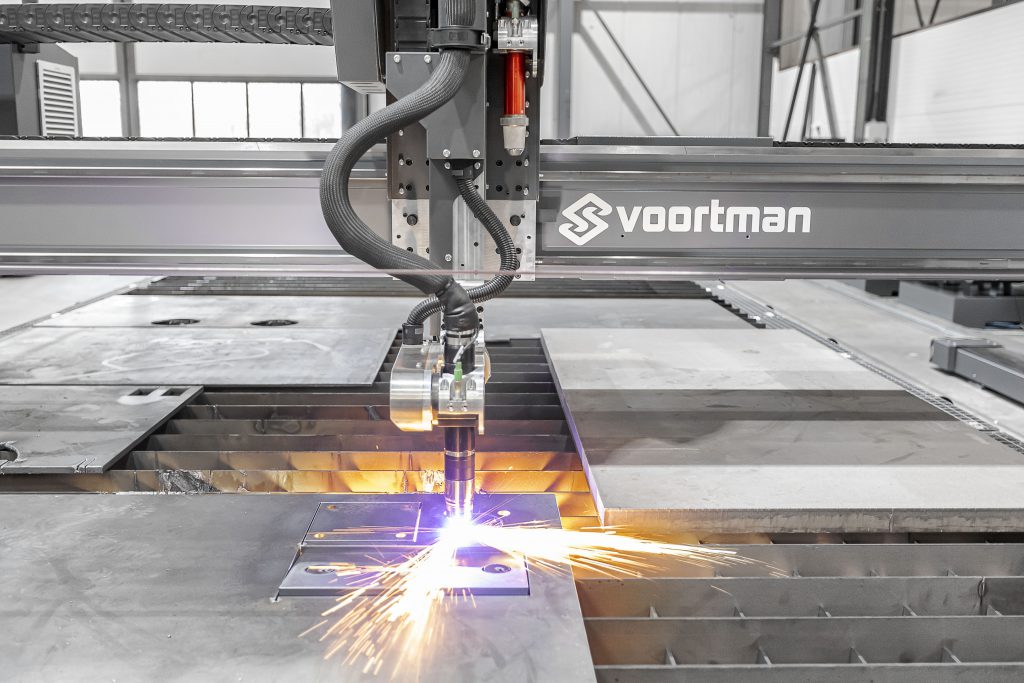
MAGNETIC TORCH MOUNTING
BENEFITS OVERVIEW
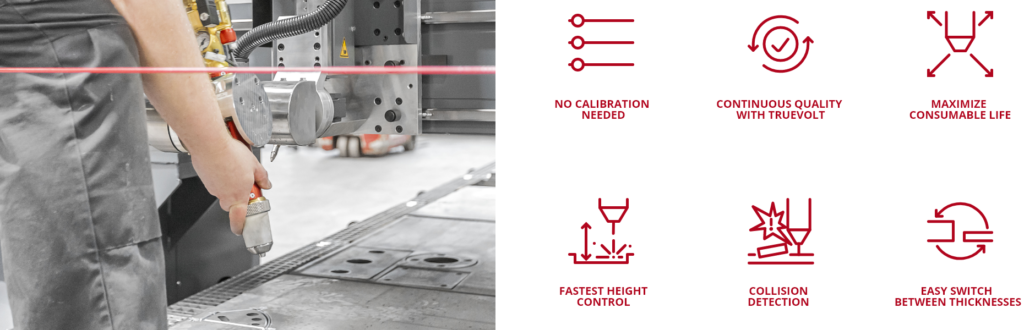
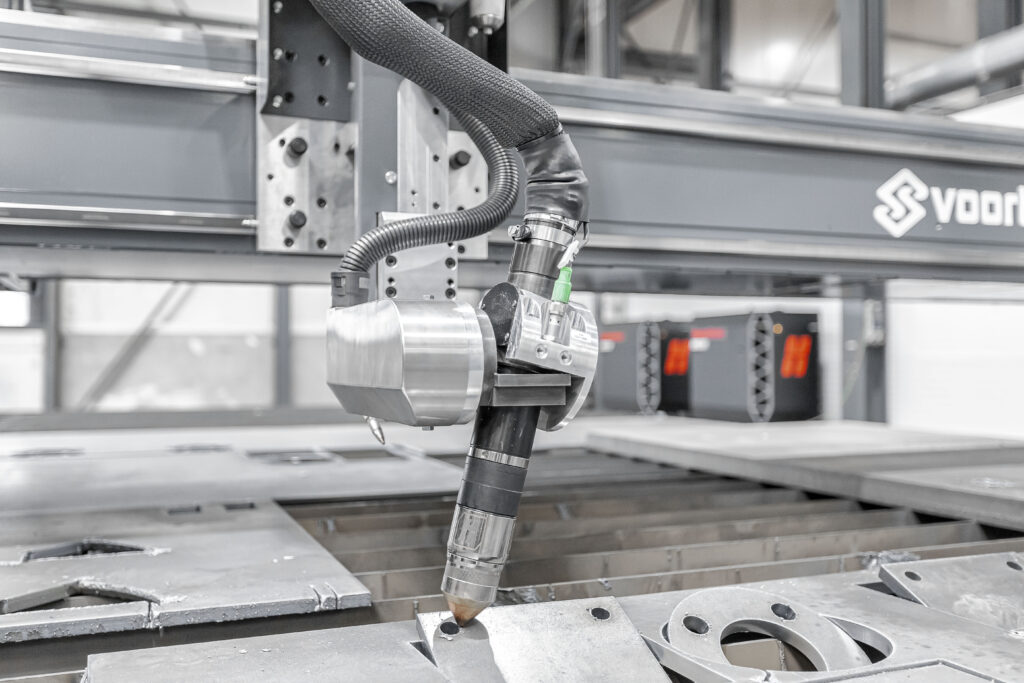
EASY RESTART AFTER COLLISION
When collision occurs your operator is able to remount the torch with a magnetic system to get the machine up and running in no time. And with the same ease, you can quickly switch between different cutting thicknesses by simply exchanging the torches.