Process equipment manufacturers
Transform your business with Voortman
Are you a manufacturer of pressure vessels, storage tanks, heat transfer & cooling systems, process piping solutions, industrial boilers or process skids? In today's rapidly changing and competitive process equipment landscape, you know you need to be flexible, reduce welding volumes and find ways to efficiently meet the strict welding regulations to stay ahead of the curve and position yourself for long-term success. Take the journey with Voortman and trust in the array of reliable solutions to support you every step of the way.
Below you'll find more info on:
- Reducing welding volume and hours while meeting strict welding standards.
- Justifying your in-house production returns with enhanced flexibility and machine utilization.
- Solutions for skids, cooling towers and pipe racks.
1. REDUCE WELDING VOLUME & HOURS
While meeting strict welding standards
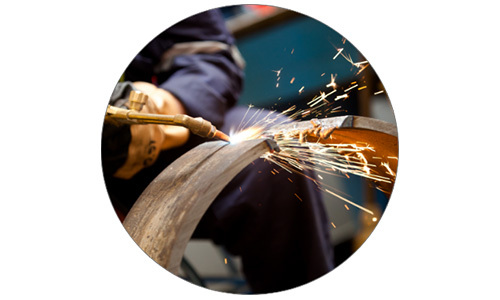
Is your business hampered by the expensive and time-consuming nature of welding?
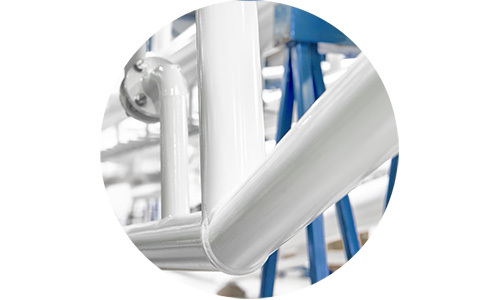
Are you struggling to keep up with the increasingly stringent welding regulations?
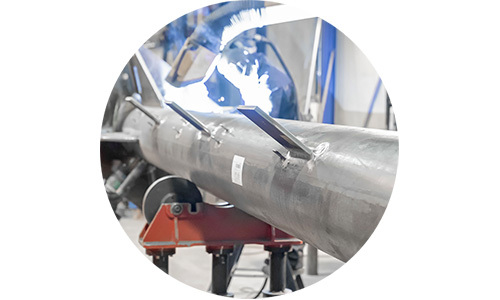
Are you also facing a shortage of skilled welders?
IN THESE CIRCUMSTANCES, IT'S PIVOTAL TO:

Reduce welding volume and welding hours without compromising quality
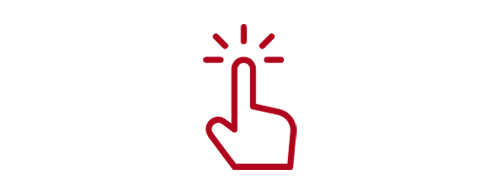
Comply designs with welding standards accurately and avoid weld preparation where it's not needed.
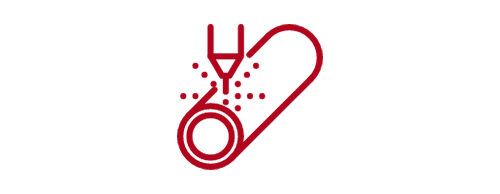
Make sure machines do the right thing when processing pipes, plates, and domes or dished ends, so they fit together properly.
WE KNOW
THIS IS EASIER SAID THAN DONE DUE TO:
1. Complex programming:
3D programs frequently lack the capability to create optimal weld preparation designs for complex objects like pipes, leading to oversized openings.
2. Variable shapes and tolerances:
Pipes are often slightly egg or banana-shaped with variations in thickness and diameter tolerances, further complicating the programming and preparation process.
3. Material tolerance sensitivity:
Plasma cutting is sensitive to variations in material tolerances, which can result in deviations from the desired weld preparations.
Voortman supports businesses in the process equipment industry tackle these challenges
by assisting in both the programming and actual machine processing phase
PROGRAMMING PHASE
Converting complex cuts into precise easy-to-handle programming tasks
If your manufacturing method revolves around cutting long plates with long bevels, rolling them, and welding them together, programming tends to be relatively straightforward compared to pipe processing.
With pipe processing as your main manufacturing method, cuts are often more complex due to variable bevels, and precision is key. This is where Voortman's software on the Voortman MO pipe processing machines steps in to make your life easier.
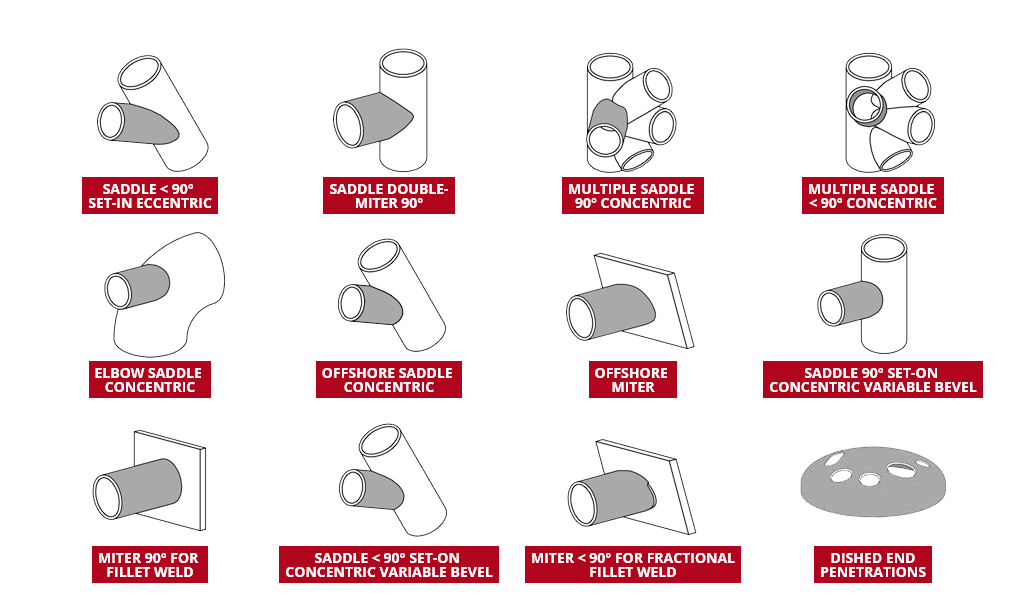
USE THE PREDEFINED MACROS
No more struggling with standard CAD packages - the software on the pipe processing machines handles the complexity for you. With easy-to-use wizards and predefined macros, you can create precise cuts that meet industry standards without any hassle.
Voortman even offers market-specific cutouts to ensure your programming aligns as closely as possible with these industry standards.
Make the transition from programming frustrations to seamless productivity.
MACHINE PROCESSING PHASE
Mastering precision and quality with Voortman's solutions for accurate bevel cutting
The regulations surrounding weld quality in your industry are no joke. You have to be on top of your game and spend extra time ensuring the quality is top notch. Your customers demand it, and with high-pressure products like boilers and pressure vessels, the consequences of a faulty weld can be catastrophic.
This underscores the need for a cutting process that is both accurate and adaptable to various materials. By enabling the cutting process to adapt to material variations, minimal deviation in weld preparation can be achieved, eliminating the need for additional grinding or corrective welding afterwards. It all comes down to maintaining a constant height control.
PERFECTING LONG BEVEL CUTS ON PLATES
For long plates that are cut, rolled, and welded together, maintaining dimensional accuracy over the entire long bevel cut can be a challenge. One of the most important aspects here is maintaining the proper cutting height throughout the cutting process. The cutting height is maintained by ensuring the torch follows the top surface of the material. Voortman plate processing machines, such as the Voortman V310, excel in this regard by automatically measuring the length of the plasma arc from electrode to material and making adjustments to compensate for consumable wear.
However, proper programming and deck maintenance also play a vital role in upholding the correct cutting height, especially for long bevel cuts. For a comprehensive understanding of how all these elements come together, we invite you to watch this latest bevel cutting webinar video.
PRECISION PIPE CUTS BY EXTENDING GANTRY PLATE MACHINES
The Voortman moving-gantry plate processing machines offer the flexibility to expand their capabilities by incorporating a Voortman Pipe Cutting Unit as an extension. Herewith you can seamlessly process both plate and pipe material on the same station.
The height control used for this Pipe Cutting Unit is quite similar to the one for the plate processing machines. But here's the exciting part - It also dynamically adjusts to variable bevels with changing arc lengths by utilizing a predictive model, ensuring precision throughout the pipe cutting process.
LASER SENSOR TECHNOLOGY FOR CONSISTENT PIPE BEVEL CUTS
In the previous examples, Voortman maintains a constant cutting height by automatically adjusting the plasma arc. While this approach is effective, there are alternative solutions worth considering.
For instance, Voortman's MO pipe processing machines employ laser sensor technology to scan and monitor irregularities in the pipe or dome. This information is then used to control the cut height, ensuring reliable bevel cuts. This video shows you how this works.

2. ACCELERATING YOUR IN-HOUSE PRODUCTION RETURNS
With enhanced flexibility and machine utilization
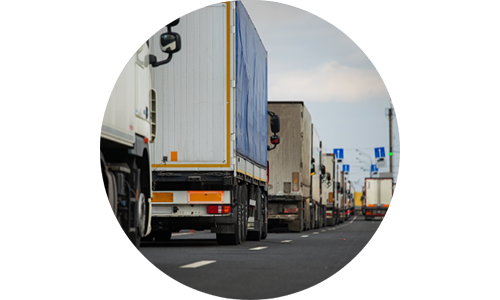
Are you tired of the risks and costs of outsourcing your plate and pipe processing?
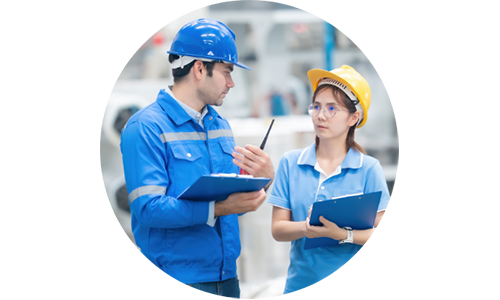
Not sure how to make a compelling business case for bringing the entire production process in-house?
WITH VOORTMAN'S FLEXIBLE MACHINES, YOU CAN:
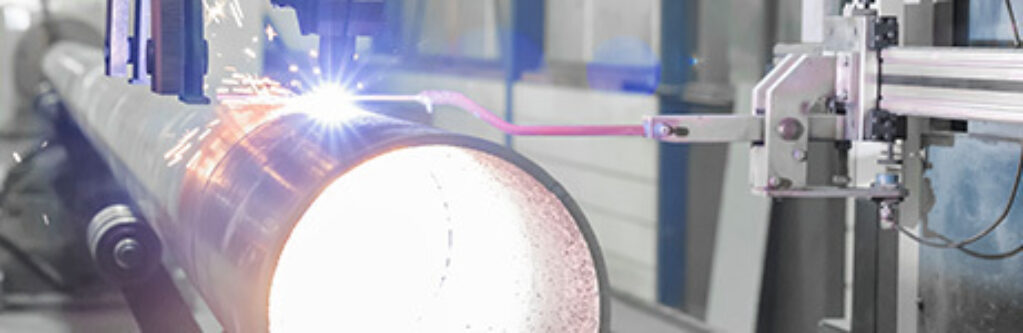
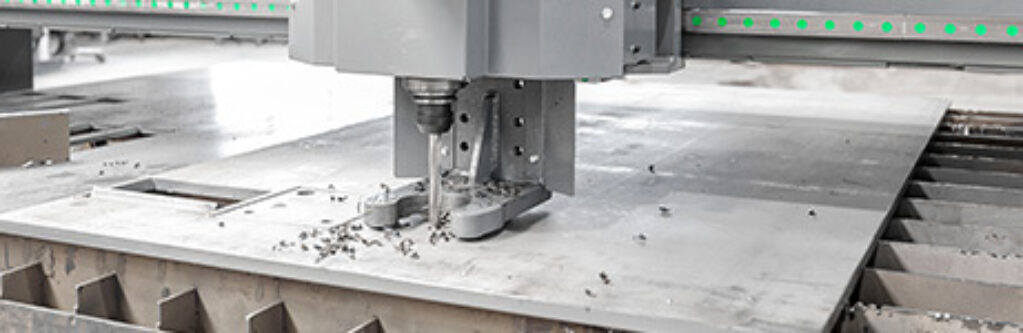
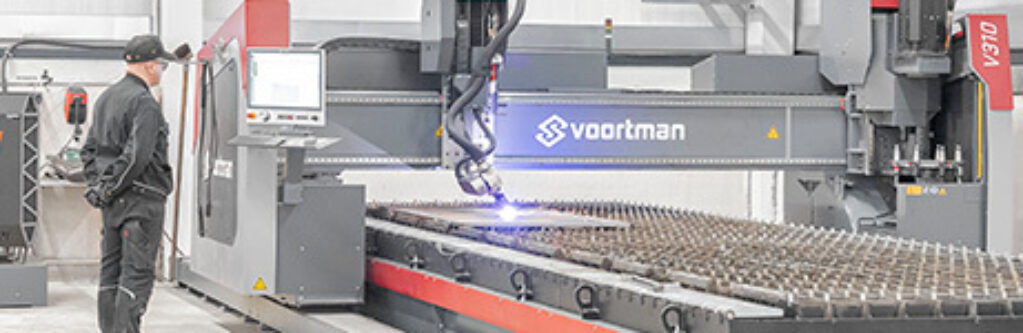
TAKE FULL CONTROL OVER YOUR PRODUCTION
UTILIZE A RANGE OF MACHINE PROCESSES IN A COMPACT AREA
RESPONSIVELY ADDRESS CHANGING PRODUCTION REQUIREMENTS IN REAL-TIME
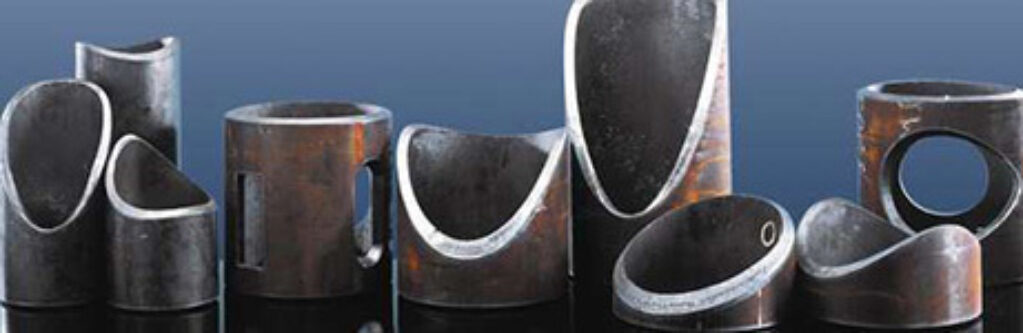
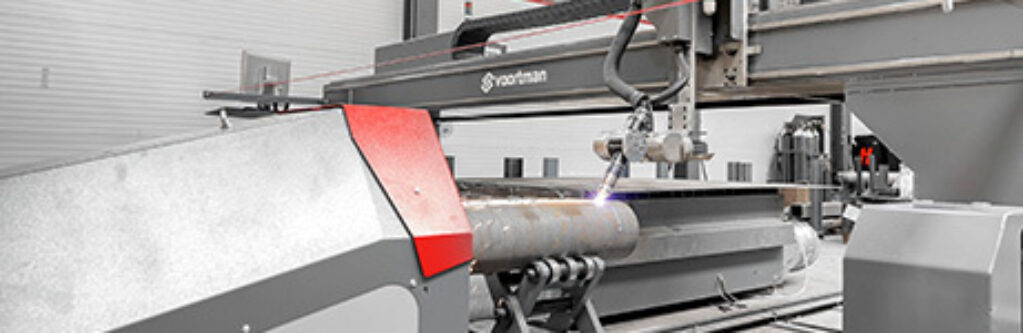
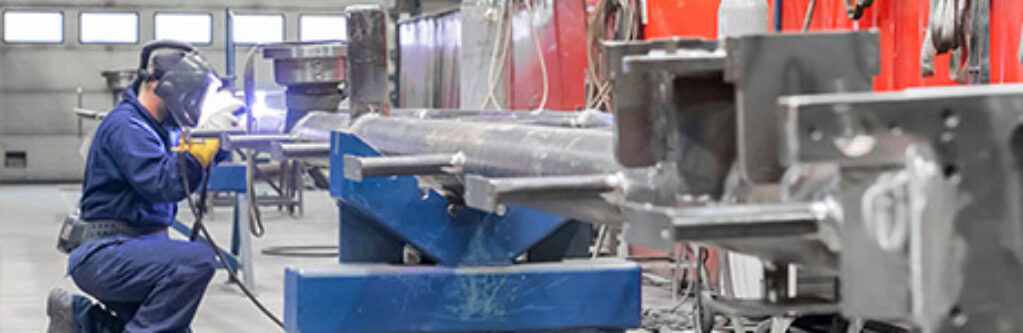
HANDLE VARIOUS TYPES OF PROFILES AND SIZES
MAXIMIZE MACHINE UTILIZATION, ALLOWING IN-HOUSE PRODUCTION TO PAY OFF SOONER
PUT AN END TO CONCERNS ABOUT YOUR WELDERS REMAINING IDLE
FLEXIBILITY WITHIN THE VOORTMAN MO PIPE PROCESSING RANGE
Looking at the Voortman MO pipe processing machine range, there are several aspects of flexibility that can be identified. Starting with the choice of three different machine types, each allowing for different profile types and pipe diameters that can be processed.
PROCESS PIPES, DOMES OR DISHED ENDS ON A SMALL FOOTPRINT
With unique patented rotary chuck
The Voortman MO Classic and MO Heavy-Duty pipe processing machines feature a unique and patented rotary chuck that can be flipped over, allowing you to process both large pipes, domes and dished ends on a compact footprint. This offers a distinct advantage compared to alternative machines that typically demand a more extensive footprint. It's a perfect and ideal all-in-one solution for the flexible production of pressure vessels.
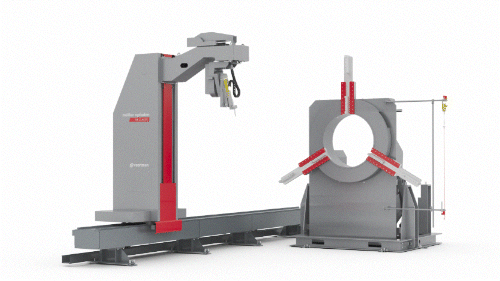
LEAN ON THE HIGHLY FLEXIBLE VOORTMAN PLATE MACHINES
We're not just highlighting the versatility of our pipe processing machines; our plate machines are equally remarkable.
The Voortman V310 moving-gantry plate machine does it all. With a simple push of a button, you can achieve bevel cutting, drilling, milling, marking, tapping, and countersinking. Imagine creating beveled plates or connection plates, then seamlessly moving on to drilling and milling tube sheets and baffles, all using the same machine. However, plate cutting machines such as the Voortman V303 and V304 also offer a high
degree of flexibility in your workflow with plasma, oxy-fuel, bevel cutting and
marking options.
But it doesn't stop there. When you combine these moving gantry machines with a Voortman Pipe Cutting Unit, you can cut your pipes and plates on one station on a small footprint. This opens up a world of possibilities, allowing you to create flanges and pipe connections of the highest quality. Not only does this streamline your production, but it also simplifies the manufacturing process by eliminating the need for multiple machines. Say goodbye to complex routing and excessive inventory. Experience ultimate efficiency and flexibility with our cutting-edge plate processing machines.
GET THE JOB DONE!
Here's a glimpse of what these flexible machines can produce:
Pressure vessel
Heat exchanger
Piping connections or spools
Storage tank
3. PROFILE PROCESSING SOLUTIONS
FOR PROCESS SKIDS, UTILITY SKIDS, COOLING TOWERS AND PIPE RACKS
Voortman doesn't just specialize in pipe and plate processing solutions; we also excel in profile processing solutions that cater to the manufacturing of components for process skids, utility skids, cooling towers, and pipe racks as well.
Voortman V807 Robotic profile cutting machine

The Voortman V807, a robotic profile cutting machine, can cut profiles into any desired shape. Whether you need to process transverse beams for pipe racks, or beams for skids, this machine is equipped for the job. The V807 merges various functions yielding an economic edge over individual drilling, milling, sawing, punching, shearing, and layout marking systems. By integrating these processes into one machine, it facilitates a faster ROI while using minimal floor space.
>> EXPLORE THE V807
Voortman Drill Saw line
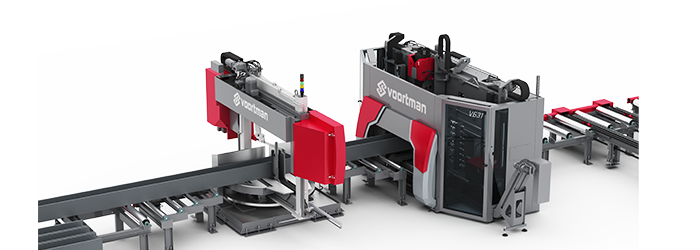
The advanced Voortman drill-saw lines are another viable solution. These can process profiles for structures such as pipe racks, cooling towers, or supports for heat exchangers. This compact system streamlines logistics by reducing the need for crane or forklift usage due to its single in- and outfeed. Simply measure the entire raw profile once, process it in a single run. The unique feeder rolls can handle materials of any length and support dual-side loading. Moreover, loading and unloading can be done even while the machine is in operation, thanks to the integrated light curtains.
CUSTOMER STORIES:
SUCCESS WITH VOORTMAN PIPE CUTTING MACHINES
BASF's Modernization journey
To optimize pressure vessel production
Established in 1865 and headquartered in Ludwigshafen, Germany, BASF stands at the forefront of the chemical industry, continuously seeking ways to enhance its production capabilities. The company is taking significant strides in modernization by integrating the advanced Voortman Müller Opladen Heavy-Duty pipe cutting system into its pressure vessel manufacturing process. This strategic upgrade underscores BASF's commitment to improving production accuracy, efficiency, and safety, while minimizing manual labor reliance.
A few weeks back, we visited BASF together with Ralf Hamacher, who showcased the capabilities of the Voortman MO Heavy-Duty machine, highlighting the impact on optimizing pressure vessel production.