Offshore & Energy Manufacturers
Transform your business with Voortman
In the offshore and energy sector, producing structures like offshore platforms, jackets, wind turbines, and monopiles presents unique challenges due to the harsh environments these constructions must endure. In such conditions, safety cannot be compromised—it's an absolute necessity. This demands that every stationary structure not only exhibits unparalleled rigidity but also adheres meticulously to rigorous welding standards. This is where partnering with Voortman can make a significant difference. With a comprehensive range of dependable solutions, Voortman is equipped to support you on your path to sustainable success, ensuring every project adheres to the highest safety and quality benchmarks.
Below you'll find more info on:
- Easily creating the highest quality complex offshore connections while meeting strict welding standards.
- Profile processing solutions to create components of offshore constructions.
- Accurately cutting long bevel cuts on plates for the productions of wind turbines and monopiles.
1. EASILY CREATE HIGH QUALITY OFFSHORE CONNECTIONS
WHILE MEETING STRICT WELDING STANDARDS
Offshore constructions, including jackets, offshore platforms, power skids, energy pipelines, and various power generation, transfer, and processing units, are engineered to endure the harsh marine conditions. These structures face constant challenges from heavy winds, saltwater exposure, ocean currents, wave action, temperature changes, and the risk of corrosion. The integrity and durability of connections within these structures are critical, emphasizing the importance of high-quality welds of saddle cuts and pipe-on-pipe connections, which often require substantial welding work.
But here are some questions for you:
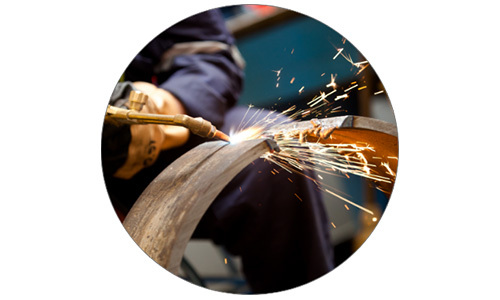
Is your business hampered by the expensive and time-consuming nature of welding?
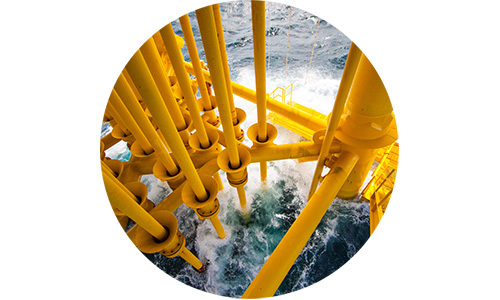
Are you struggling to keep up with the stringent welding regulations, while dealing with complex connections and diversity in pipe sizes?
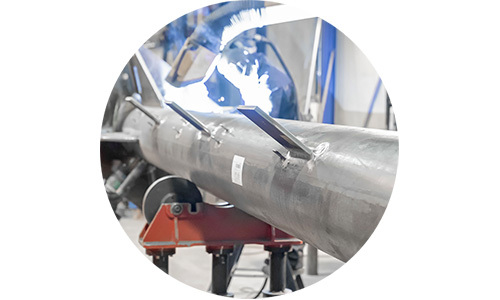
Are you also facing a shortage of skilled welders?
IN THESE CIRCUMSTANCES, IT'S ESSENTIAL TO:

Reduce welding volume and welding hours without compromising quality.
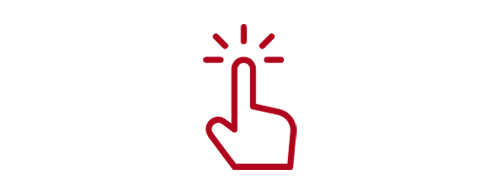
Ensure pipe connection designs accurately meet welding standards.
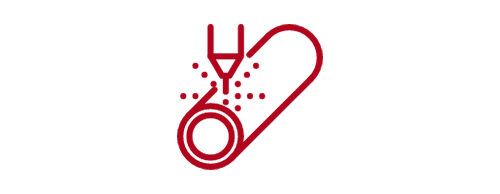
Ensure that machines work precisely and correctly when cutting pipes so that connections fit together seamlessly.
WE KNOW
THIS IS EASIER SAID THAN DONE DUE TO:
1. Complex programming:
3D programs frequently lack the capability to create optimal variable bevels and weld preparation designs for complex objects like pipes for offshore constructions, leading to oversized openings.
2. Variable shapes and tolerances:
The shape of pipes often includes minor deviations from perfect circularity and curved contours along their axis, which, when combined with variations in thickness and diameter tolerances, adds layers of complexity to the programming and preparation process.
3. Material tolerance sensitivity:
Plasma cutting is sensitive to variations in material tolerances, which can result in deviations from the desired weld preparations.
Voortman supports companies in the offshore and energy industries to face these challenges by assisting in both the programming and actual machine processing phase.
PROGRAMMING PHASE
CONVERTING COMPLEX CUTS INTO PRECISE EASY-TO-HANDLE PROGRAMMING TASKS
Say goodbye to the complexities typically associated with standard CAD software - our pipe processing machine's software streamlines the process for you. It features intuitive wizards and pre-set macros, enabling you to simplify intricate offshore connections into programmable cuts that meet industry standards with ease.
Consider this offshore jacket as a practical example of how the
system operates:
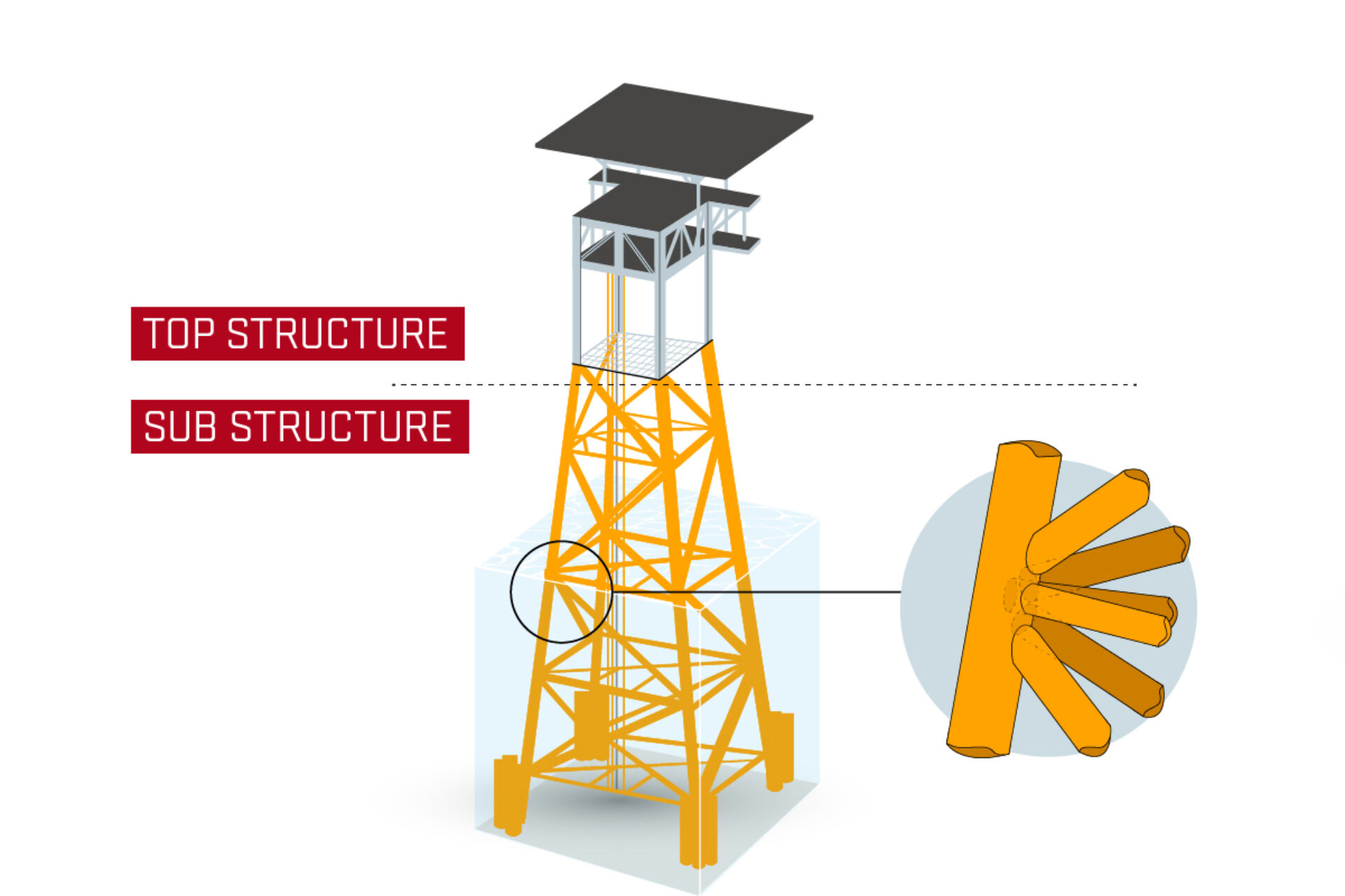
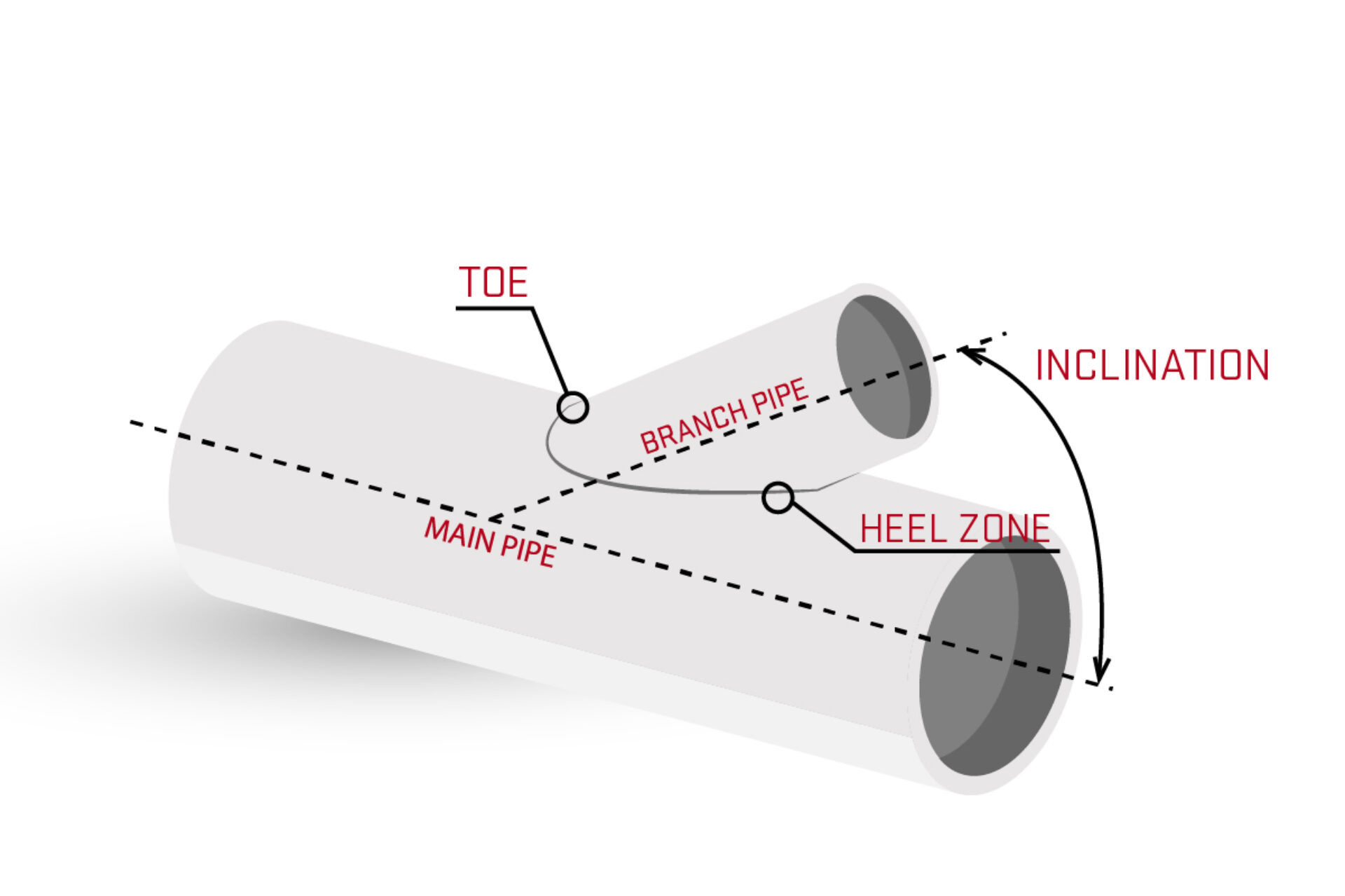
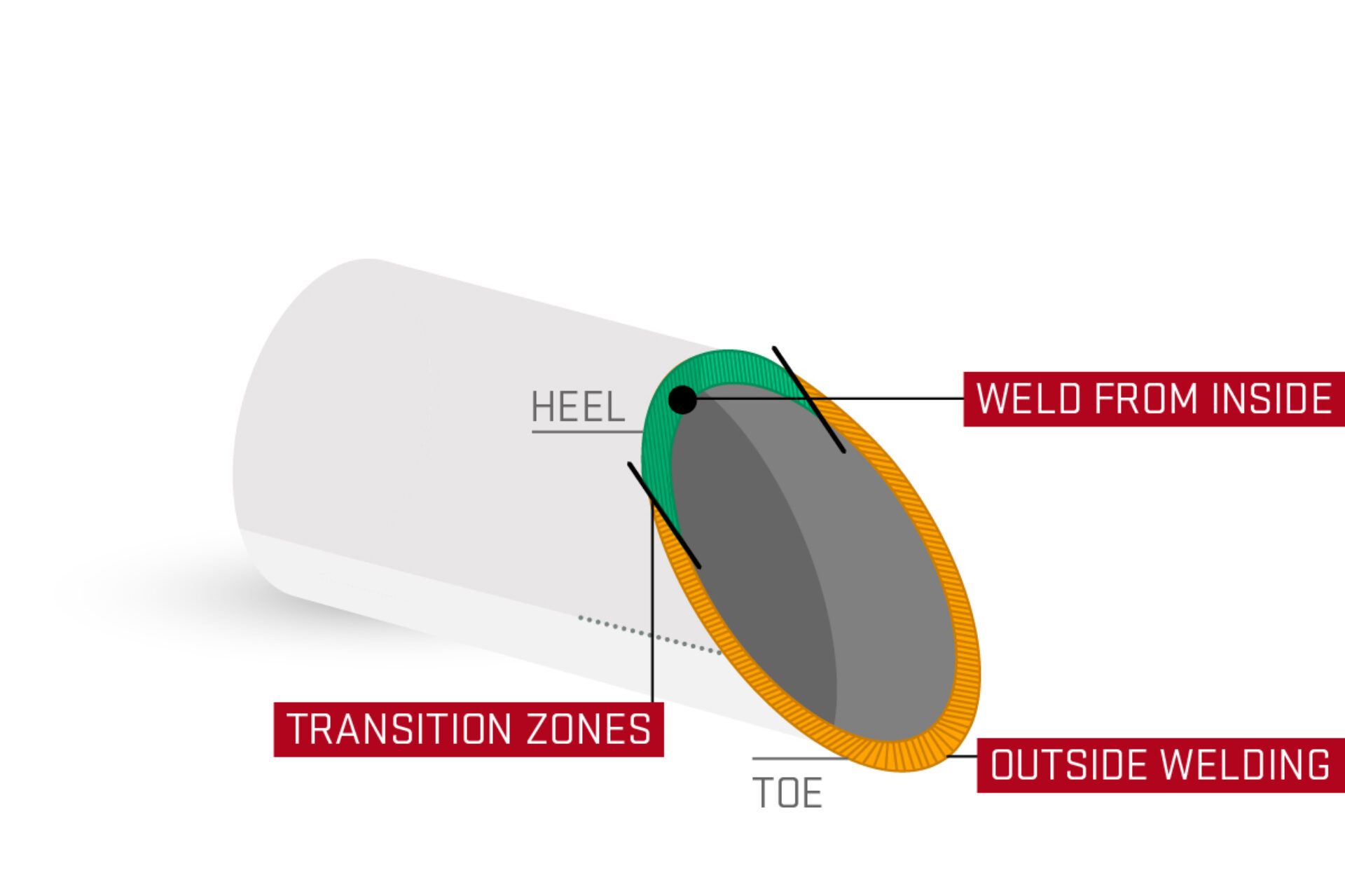
1. Design the bottom structure of the jacket
The jacket consists of complex offshore connections where often multiple pipes come together in a node and steep angles or inclinations are applied.
2. Import your CAD model and employ Corobs Plus
Corobs Plus decomposes the connection and joints into the required cuts, thoughtfully considering practical production factors such as welding accessibility, thermal cutting constraints, fitting, and alignment support. In this example, we demonstrate a specific case where a branch pipe needs to be welded onto a main pipe at a typical steep angle. To ensure a seamless fit and weld between the branch and main pipe, it's crucial to weld the heel part of the branch pipe from inside the main pipe. This requires the branch pipe to have an accurate variable bevel, including a so-called transition zone.
3. Create the perfect cutting trajectory
In order to program this variable bevel with transition zone as accurately as possible and thus ultimately cut precisely, Corobs and the macros in the software support you to generate a very detailed cutting trajectory with precise cutting parameters.
The programming has been completed on your behalf; it's time to carry out the processing on the machine with high precision.
MACHINE PROCESSING PHASE
MASTERING PRECISION AND QUALITY WITH VOORTMAN'S PIPE PROCESSING SOLUTIONS
Once programming has been completed on your behalf; it's time to carry out the processing on the machine. The regulations surrounding weld quality in your industry are no joke. You need to make it your top priority to ensure top-notch quality. Your customers demand it, and with offshore structures exposed to extreme conditions, the consequences of an incorrect weld can be catastrophic.
This underscores the need for a pipe cutting process that is as accurate and reliable as possible, eliminating the need for additional grinding or correction welding afterwards and ensuring control over the supply chain and production schedules.. Looking at the Voortman MO pipe cutting machines, the Voortman MO Classic Series is most commonly used by customers in the offshore industry.
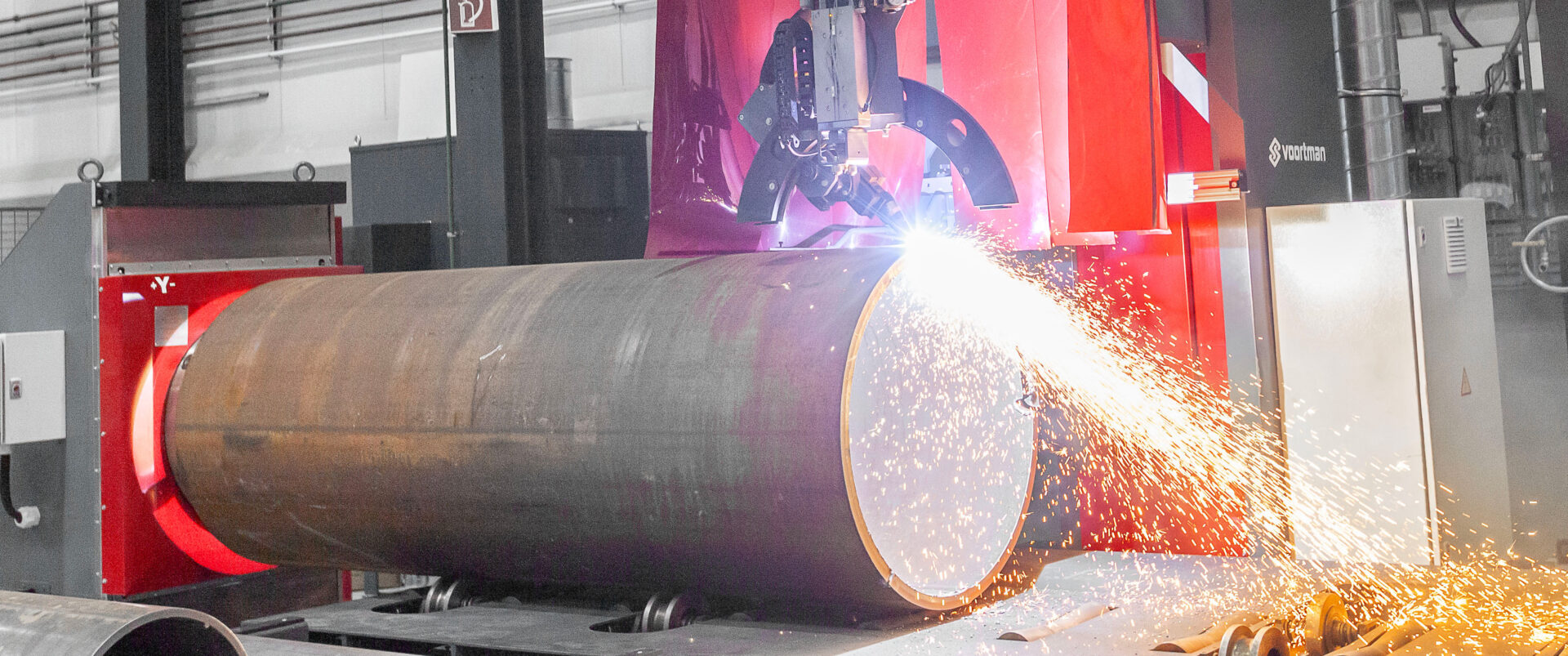
THIS IS HOW THE VOORTMAN MO CLASSIC SERIES STANDS OUT
WHEN IT COMES TO CUT QUALITY:
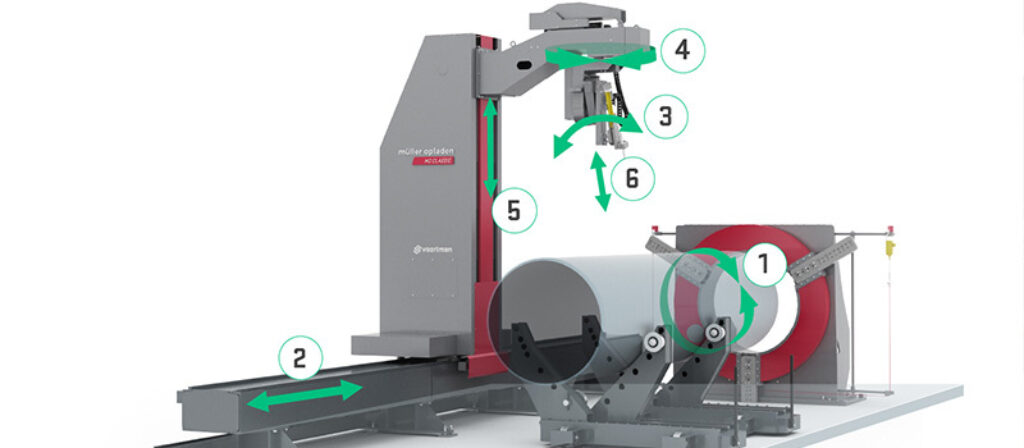
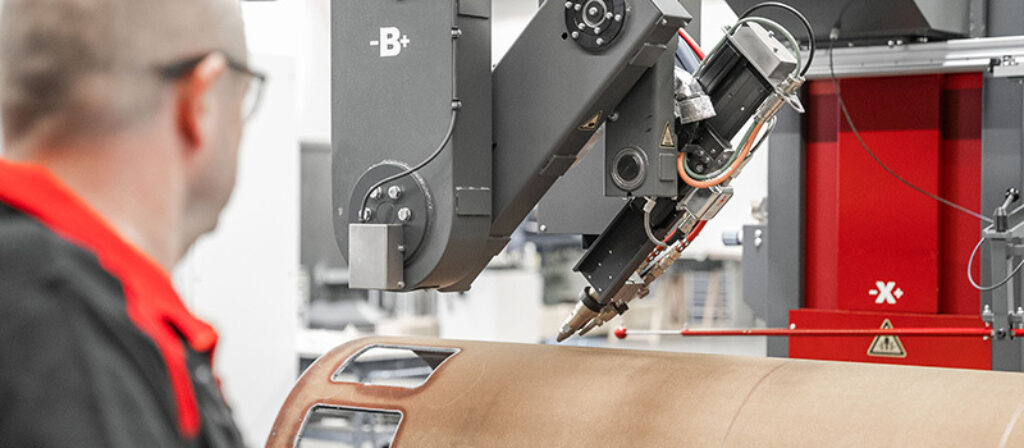
PRECISION CUTTING WITH 6-AXIS FLEXIBILITY
Featuring a 6-axis configuration, the MO Classic introduces enhanced dynamism and adaptability into pipe cutting operations. Specifically, its W-axis—the 6th axis— ensures that the cutting torch always keeps the proper distance to the pipe, adjusting dynamically to deviations in the pipe material during bevel cutting and significantly improving the overall quality of the cut.
LASER SENSOR TECHNOLOGY FOR CONSISTENT BEVELING ON PIPES
Employing laser sensor technology, the Voortman MO Classic scans for and detects variations along the pipe's surface throughout the cutting trajectory. Positioned close to the the cutting torch, the laser ensures it remains within optimal range for precise monitoring. This data is crucial for adjusting and fine-tuning the cutting height, resulting in consistently accurate bevel cuts and superior tolerances when compared to traditional mechanical tracing methods.
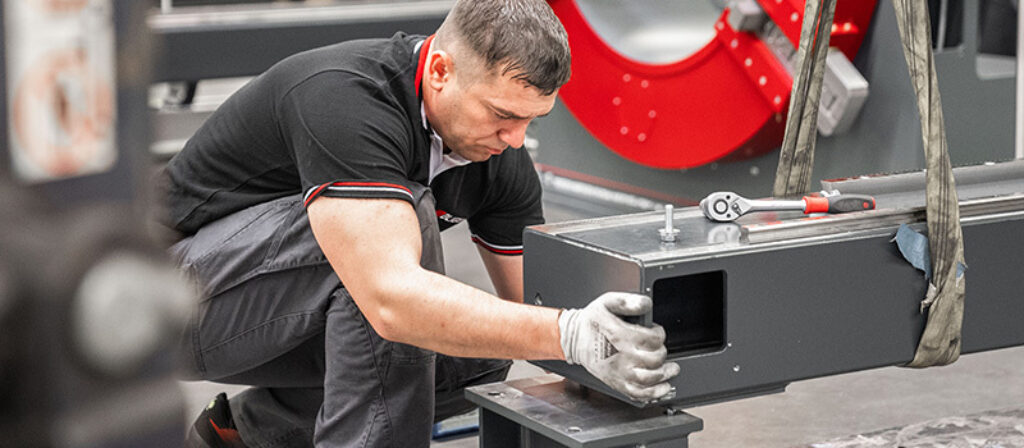
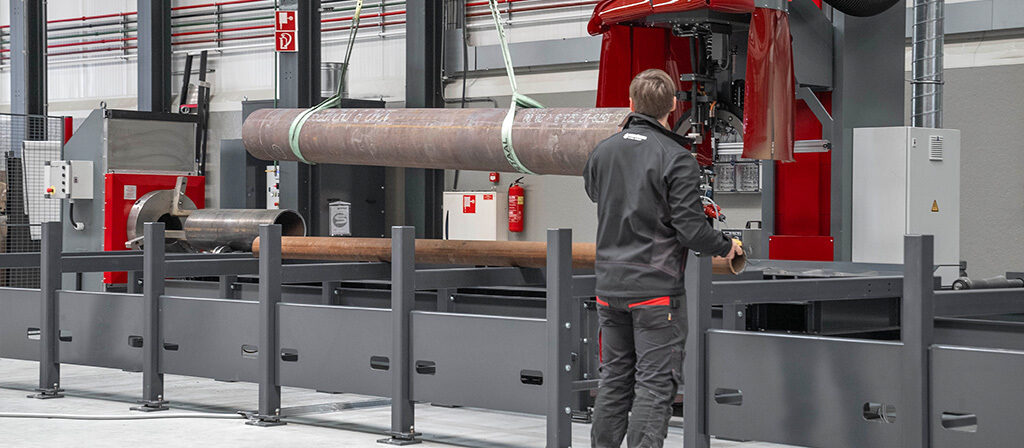
ROBUST AND HEAVY-DUTY X-RAIL
The precision of the Voortman MO machines is significantly enhanced by the robust guidance system. Featuring a sturdy X-rail design, complete with linear guidance and helical rack and pinion drive system, this setup ensures superior accuracy throughout the machining process. This contrasts sharply with other market solutions that rely on roller bearings for positioning, which are not as precise and tend to have more backlash.
EASY FITTING WITH LAYOUT MARKING WITH THE AIR SCRIBER
Aligning multiple pipes during assembly can be complicated by the complex nature of their connections. The MO Classic’s air scriber comes to the rescue by applying essential center and quarter line markings, enabling rapid alignment of pipes. Additionally, the air scriber can mark identification details and product numbers, enhancing the traceability of materials.
PRECISION AT EVERY ANGLE
OXY-FUEL'S 70° FLEXIBILITY FOR OFFSHORE CUTTING
For complex offshore cuts that exceed plasma's range, oxyfuel cutting offers a solution. The oxy-fuel torch can adjust by 70° for angles from 20° to 160° relative to the pipe axis, providing the necessary inclination to ensure a proper groove weld preparation. Especially with the branch pipe having a small angle, the 70° oxyfuel angle can ensure minimizing the welding volume. Morover, the torch head's ability to rotate 380° further improves maneuverability around the workpiece, especially at the offshore cuts with the variable bevel during the transition zone. Finally, its design protects against dust, dirt, and debris, maintaining cleanliness and functionality in harsh conditions.
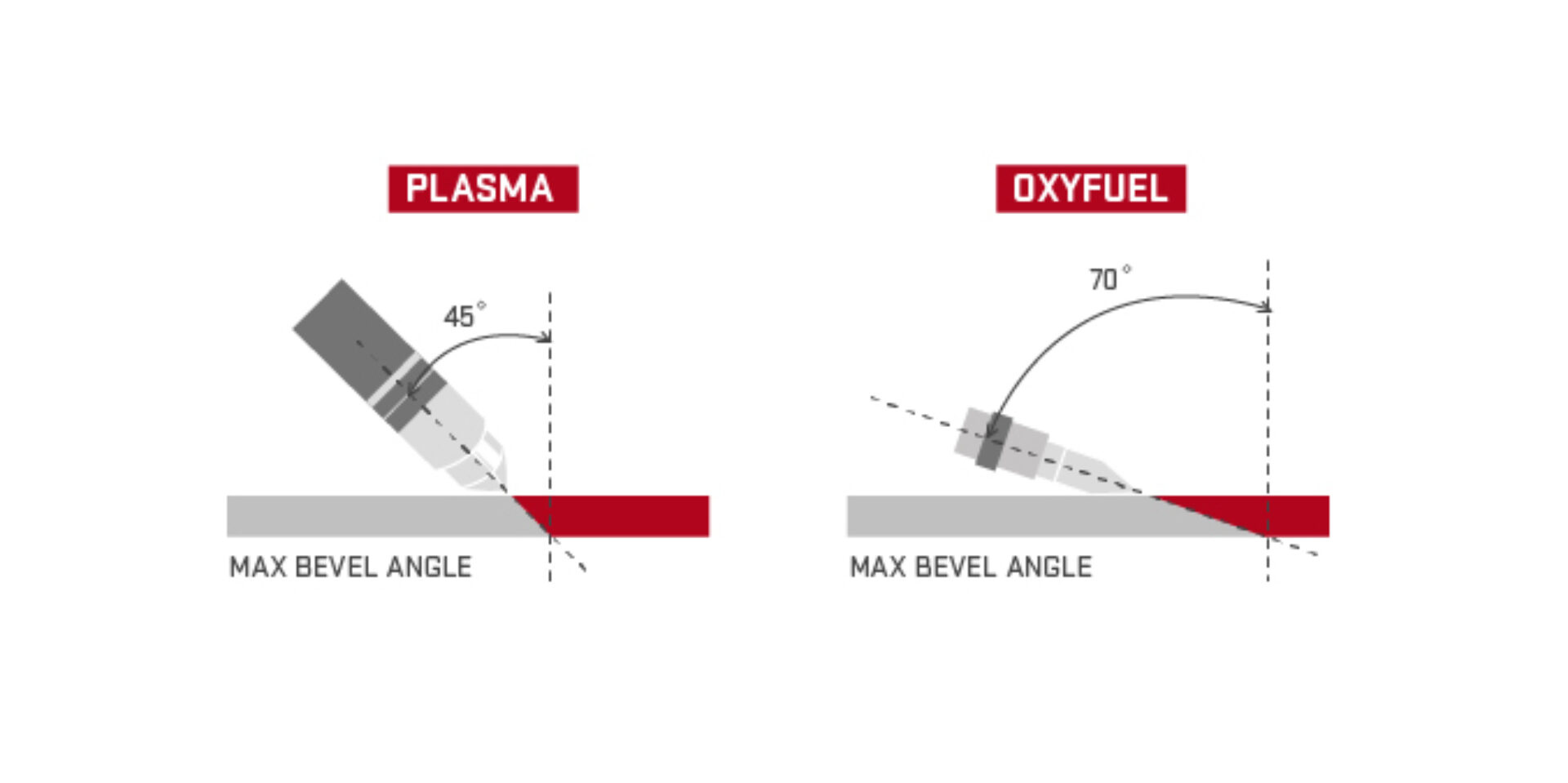
2. PROFILE AND PLATE PROCESSING SOLUTIONS
FOR OFFSHORE CONSTRUCTIONS
Above, we've primarily discussed the precise processing of pipe material, crucial for structures and joints in the supporting bottom structure. Yet, the story doesn't end below the sea level. Above the water, the offshore platform involves a big welded structure comprising mainly plate material welded together along with profile materials like beams, channels, square tubes, or angle profiles. Voortman has been providing profile and plate processing solutions for many years, enabling the production of various parts for offshore structures and jackets. Let's see how these solutions fit in.
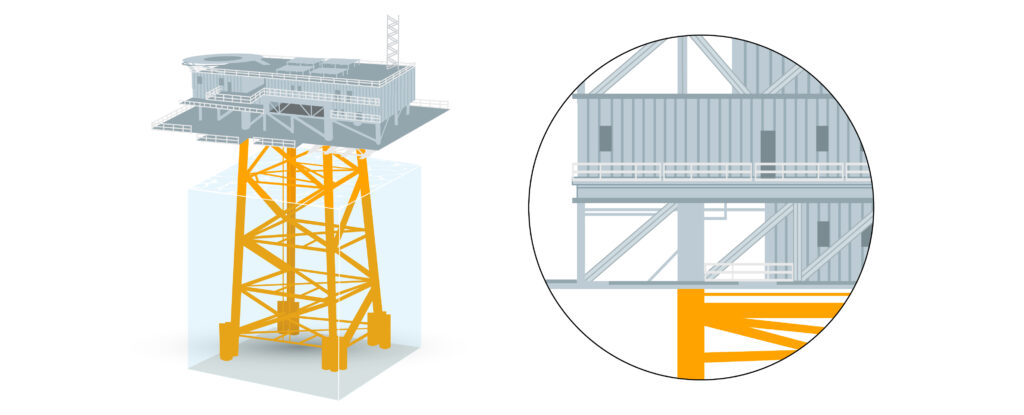
Voortman V807 Robotic profile cutting machine

The Voortman V807 excels in processing offshore floor level
structures that involve a multitude of horizontally aligned I/H profiles,
requiring accurate beam-to-beam cope connections. Additionally, it proves highly effective in producing numerous stairs within offshore platforms, that require straightforward, double-sided angled channels. The machine seamlessly integrates drilling, milling, sawing, punching, shearing, and layout marking functions into a single, compact system, offering unparalleled flexibility and economic advantages. By consolidating these processes into one machine, it not only ensures a faster return on investment but also maximizes floor space efficiency, making the V807 indispensable for achieving both precision and efficiency in sophisticated construction tasks.
>> EXPLORE THE V807
Voortman V303 Plate processing machine
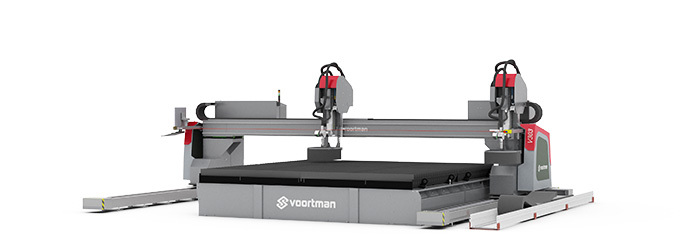
The Voortman V303 plate processing machine is well-suited for offshore construction projects, offering a seamless blend of efficiency and precision. Its compact design, coupled with intelligent features, makes it the perfect choice for crafting beveled plate parts with unparalleled accuracy. Automated measurement of the plasma arc's length and adjustment for consumable wear ensure a consistently high-quality bevel cutting experience. Further enhancing cutting quality is Voortman's unique bevel control, known as NON-Tool Center Point (NON-TCP), which distributes dynamics across the entire machine rather than just the bevel unit. Moreover, with Xtensive Bevel Cutting technology, even the most intricate bevel cuts are effortlessly automated, eliminating the need for manual corrections and pre-cutting, thereby saving valuable time and effort.
3. ACCURATE PRODUCTION OF WIND TURBINES AND MONOPILES
WITH VOORTMAN'S MOVING-GANTRY PLATE PROCESSING MACHINES
For very long plates that are cut, rolled and welded together for the production of wind turbines and monopiles, you can consider integrating a flatbed machine with a long cutting table. Both the V310 plate drilling and cutting machine, as well as the V303 or V304 plasma cutting machine, can be equipped with such an extended table and can do the job. However, as you know, maintaining dimensional accuracy over the entire long bevel cut can be a challenge. One of the most important aspects here is maintaining the proper cutting height throughout the plate cutting process.

PERFECTING LONG BEVEL CUTS ON PLATES
The cutting height is maintained by ensuring the torch follows the top surface of the material. Voortman plate processing machines, excel in this regard by automatically measuring the length of the plasma arc from electrode to material and making adjustments to compensate for consumable wear.
However, proper programming and deck maintenance also play a vital role in upholding the correct cutting height, especially for long bevel cuts. For a comprehensive understanding of how all these elements come together, we invite you to watch this latest bevel cutting webinar video.