Machinery & equipment manufacturers
Transform your business with Voortman
At Voortman, we're not just a machinery manufacturer; we're your strategic partner in tackling and navigating shared challenges and trade-offs. Just as we employ a modular approach in our machines, we recognize the diversity in your product offerings. While your commitment to innovation demands periodic updates to your product range, you also strive to minimize stock and work-in-progress. And, of course, there's the quest for the utmost precision and efficiency in your production methods.
In this exciting journey of innovation and efficiency, Voortman supports you with unwavering solutions.
Below you'll find more info on:
- Mastering Just-in-Time production
- Empowering Your Engineering Team: From design to production efficiency
- Achieving First-Time-Right production
1. MASTERING JUST-IN-TIME PRODUCTION
Through flexible machines and solutions with low setup times
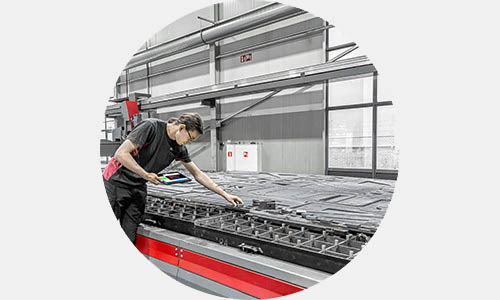
Are you facing a constantly changing product landscape with numerous variations and a need for ongoing innovations and revisions?
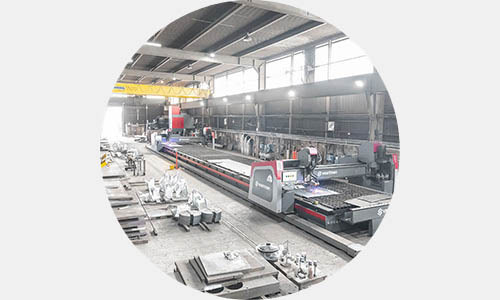
Are you interested in mirroring Voortman's approach to minimize intermediate stock and work-in-progress (WIP), reducing risks, chaos, and tackling logistical challenges?
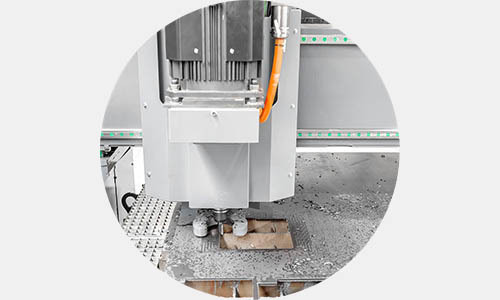
Are you seeking ways to efficiently initiate the right number of batches to meet your desired lead times?
We get it; you don't want to be dependent on forecasts either. You need a production method that allows you to produce the right product with the right materials at the right moment – that's the essence of Just-In-Time production (JIT).
Here's where it gets exciting: Voortman is right there with you in this endeavor. We've crafted a range of solutions to make your JIT process as efficient as it can be. These solutions effortlessly handle various small nesting tasks involving different materials and thicknesses, ensuring a seamless transition from one job to the next. They empower you to break down work into multiple smaller batches without significantly impacting your costs.
What's the secret ingredient? State-of-the-art machines with:
- Unparalleled flexibility and processes
- Lightning-fast setup times
- A suite of innovative features
Let's take a closer look below!
Versatility redefined by Voortman's multi-processing machines
Voortman's plate processing machines are designed to operate in perfect harmony with the principles of Just-In-Time production. They are centered on carrying out multiple processes on one machine, providing flexibility and high-quality parts with low setup times.
One standout machine and a true embodiment of the Just-In-Time approach is the Voortman V310. It’s a marvel, equipped to perform a multitude of tasks at the push of a button. From oxy-fuel cutting and bevel cutting to drilling, milling, marking, thread tapping, and countersinking, this machine stands as a do-it-all solution. Picture this: create weld preparations in one nesting, while continuing drilling, milling and tapping operations in the other nesting further on the cutting table in a split second.
With all these processes on a single machine, operations become streamlined, intermediate stock and work-in-progress are drastically reduced, and your Just-In-Time production process operates at peak efficiency.
However, let's not overlook the versatility of the Voortman V303 and V304 moving-gantry plate machines. These machines offer a high degree of flexibility in your workshop as well, featuring plasma and oxy-fuel cutting, bevel cutting, and marking options.
Efficiency at its best: Voortman's Hybrid Milling in action
Even with these multiple operations at play on a single machine, Voortman is innovating to implement these processes as efficiently as possible and use best of both worlds. A prime example of this is the Hybrid Milling feature.
Here's how it works: you start by cutting part of a contour, then smoothly switch to milling to finish the job. The outcome? Impressive time savings with exceptional quality. Check out these videos to see machine manufacturer Karl Hartinger Kranbetrieb share his firsthand experience with this Hybrid Milling technology and the time savings it can bring!

Benefit from a long cutting table
Particularly when you're dealing with the labor-intensive task of handling various materials and plates, you need to consider integrating a flatbed machine with an extended table to further elevate your JIT capabilities. Both the V310 plate drilling and cutting machine, as well as the V303 or V304 plasma cutting machine, can be equipped with an extended table.
With this setup, you can load different types of plates sequentially, optimizing your workflow. For instance, load a Hardox plate at the front of the table and a structural steel plate further down the system. After processing the Hardox plate, the machine seamlessly shifts to work on the structural steel plate. This minimizes manual plate changes, reduces machine downtime, and ultimately lowers your operational costs.
Effortless job to job transitions with preset parameters
Seamless and automatic job or material transations are enables by Voortman's VACAM Software, integrated into our plate processing machines. No manual programming or adjustments are needed. This aligns with Voortman's one-button automation philosophy, making complex processes accessible to individuals of all skill levels with a single button press. Our goal is to simplify and enhance your production, with a strong emphasis on maintaining efficiency as a top priority in your operations.
Efficiency Unleashed: Streamlining Plate Processing
with VACAM's Buffer, Sequencing, and Unmanned Mode Functions
If you opt for a plate processing system with a long cutting bed and load multiple plates that differ in material type or thickness, the Buffer, Sequencing and Dashboarding functions of the VACAM Software become instrumental in smooth automatic transitioning between diverse jobs and nestings.
2. EMPOWERING YOUR ENGINEERING TEAM:
From design to production efficiency
Voortman takes production efficiency to the next level by not only optimizing production processes but also supporting your engineering department. This empowerment allows your engineering team to create products that are optimized for maximum production efficiency. To achieve this, it's crucial to understand the actual production costs associated with your products.
Uncover True Costs with Voortman's Innovative Quoting Solution
We address a fundamental question: What is the real cost of 'Part A'? Gain control over this critical aspect with Voortman's innovative Quoting solution, which enhances your cost calculation approach.
Let's sketch an example!
V630 Profile Drilling Machine Drill Unit
We illustrate this concept with an example involving the design and manufacturing of the following highlighted cable support for the drilling unit of a V630 profile drilling machine, manufactured in-house at Voortman Parts Manufacturing using our V310 plate processing machine.
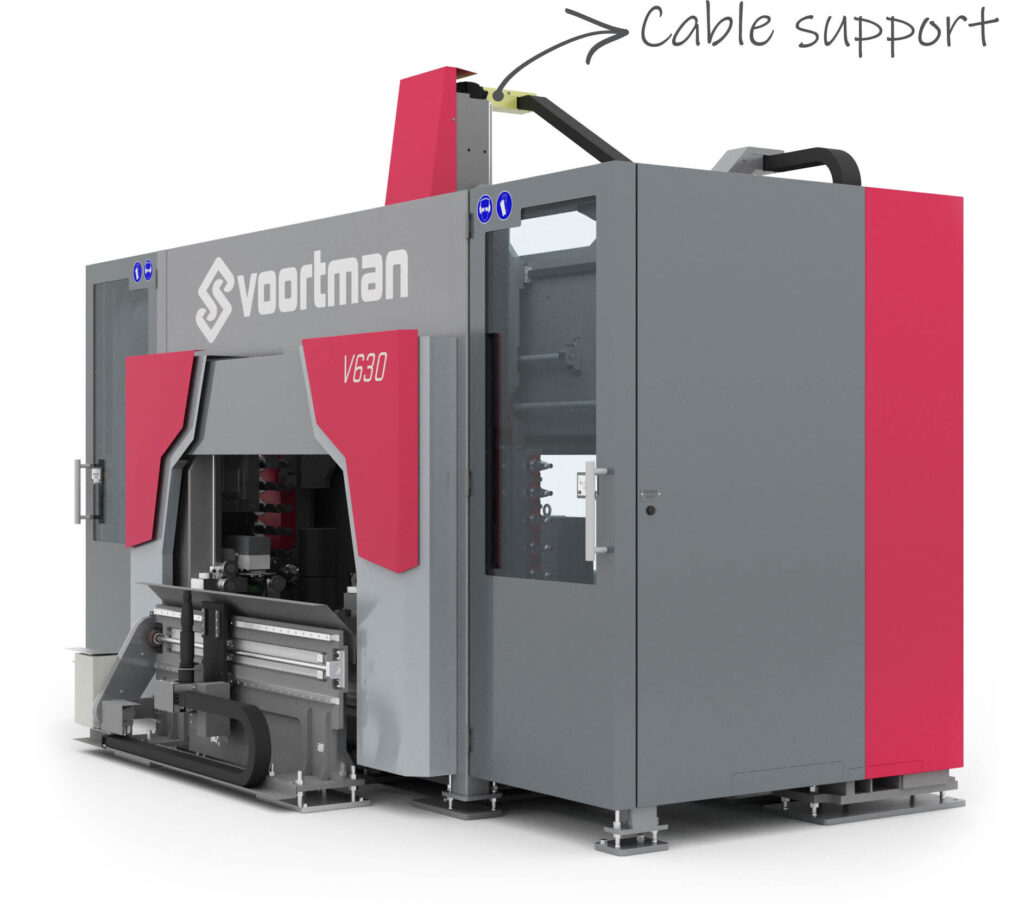

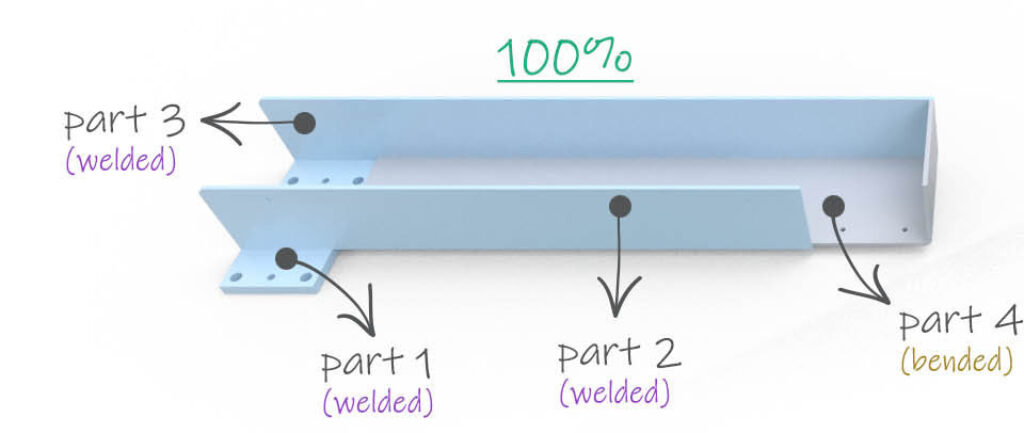
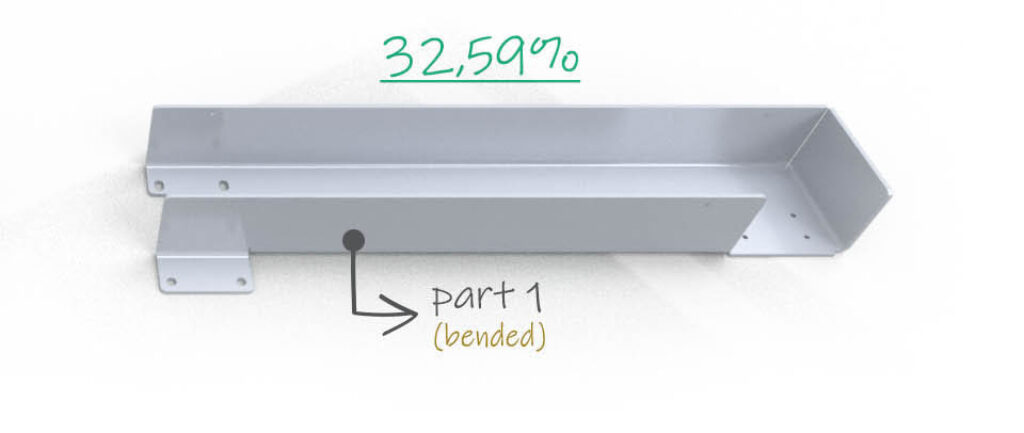
There are two distinct methods for designing and crafting this component:
- Welding most of the multiple cut parts together, with a small amount of bending included.
- Bending a cut plate.
The difference? The second method is 67,41% cheaper when it comes to material costs + operational costs.
How we figured this out? Simply by following the steps below.
3. ACHIEVING FIRST-TIME-RIGHT PRODUCTION
Consistently yield flawless results
Picture a scenario where every component, every piece, and every product emerges flawlessly on the initial attempt. No rework, no wasted materials, and no delays. This is the essence of First-Time-Right production, an indispensable element, particularly when embracing the Just-In-Time (JIT) manufacturing approach.
As we produce a significant portion of our machine parts with our own machines, we understand the importance of high quality parts which are spot on the first time. Quality remains our utmost priority, whether it's in our customer service, processing technologies, or the robustness of our machines. It's an integral part of everything we do.
Explore how our mastery of quality in various plate processing technologies can benefit you.