Verhoestraete Metalen
Vom Stahlhändler zum innovativen Komplettanbieter in der Metall- und Blechverarbeitung
Kundenbericht Verhoestraete Metalen
- Standort:
- Mitarbeiter:
- Maschinen:
- Größe der Produktionsstätte:
- Roeselaere, Belgien
- 48
- Voortman V304 + V310
- 23.500 m2 auf 70.000 m2 Grundstück
„Wir haben große Fortschritte gemacht, nicht nur bei den Prozessen und der Flexibilität, sondern auch bei der Verkürzung der Auftragsdurchlaufzeiten.“
VIER GENERATIONEN INNOVATION IN DER METALL- UND BLECHBEARBEITUNG
Wo Verhoestraete Metalen 1911 als Stahlhändler begann, hat sich das Unternehmen heute, mehr als ein Jahrhundert und vier Generationen später, zu einem vielseitigen Komplettanbieter in Belgien entwickelt, der innovative Lösungen für die Metall- und Blechbearbeitung anbietet. Auf einem riesigen Gelände von 7 Hektar liefert das Unternehmen jeden Tag handwerkliches Können für Spitzenprojekte.
Ein idealer Zeitpunkt, um dieses Wachstum im Gespräch mit Stéphane Verhoestraete (CEO), Yves de Smet (Leiter Qualität und Wartung) und Robby Delys (Leiter Vertrieb und Backup-Produktion) näher zu beleuchten.
Kundenorientierte, maßgeschneiderte Lösungen
Verhoestraete Metalen bedient einen breit gefächerten Kundenstamm und bietet maßgeschneiderte Lösungen für Unternehmen in verschiedenen Sektoren, darunter Lebensmittel, Bauwesen, Architektur und Kunst. „Eigentlich liefern wir keine Produkte mehr, sondern Komplettlösungen“, betont Stéphane Verhoestraete und verweist auf die veränderte Nachfrage der Kunden. Darauf hat sich das Unternehmen nahtlos eingestellt.
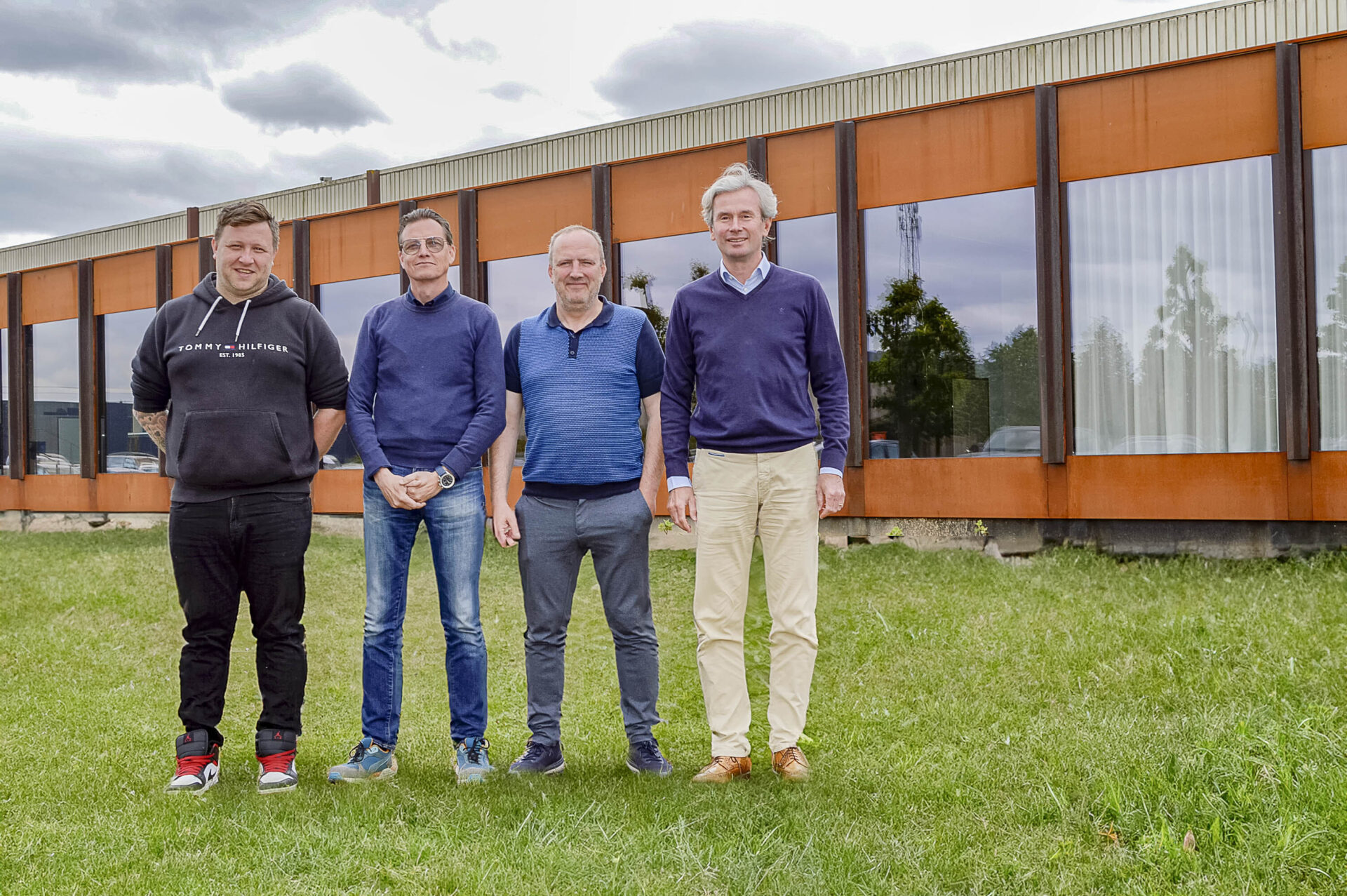
INNOVATION UND DIVERSIFIZIERUNG
Obwohl das Unternehmen seinen Wurzeln in der Metallbearbeitung treu geblieben ist, hat es in den letzten Jahren als Reaktion auf die veränderte Kundennachfrage seine Produktionskapazitäten erheblich diversifiziert. Ein Teil davon ist die Installation einer großen, 28 Meter langen Voortman Blechbearbeitung, bestehend aus einer Voortman V304 und V310. "Die größten Bleche, die wir bearbeiten, sind 12 Meter lang. Es ist also praktisch, dass Sie Ihre gesamte Arbeit von dünn nach dick verlagern können", erklärt Robby Delys.
Das System kann automatisch Bohren, Gewindeschneiden, Fräsen, Plasma-Fasenschneiden, Fasenschneiden und autogenes Brennschneiden mit einer Vielzahl von Materialtypen und -stärken durchführen. Zuvor wurden Bohren, Gewindeschneiden und die Erstellung von Schweißnahtvorbereitungen oft manuell und an separaten Arbeitsplätzen durchgeführt, was zu Ineffizienz und logistischen Herausforderungen führte.
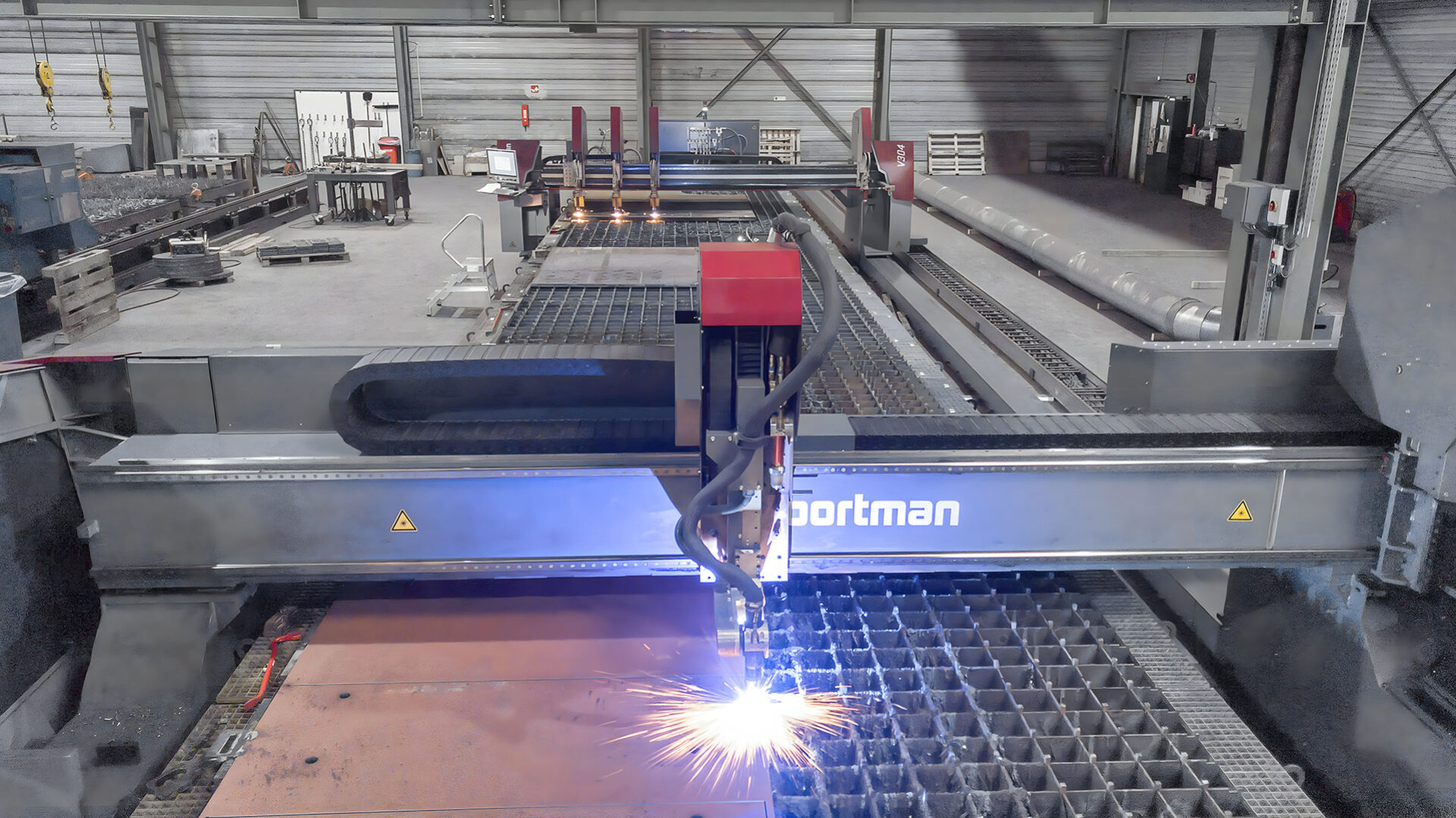
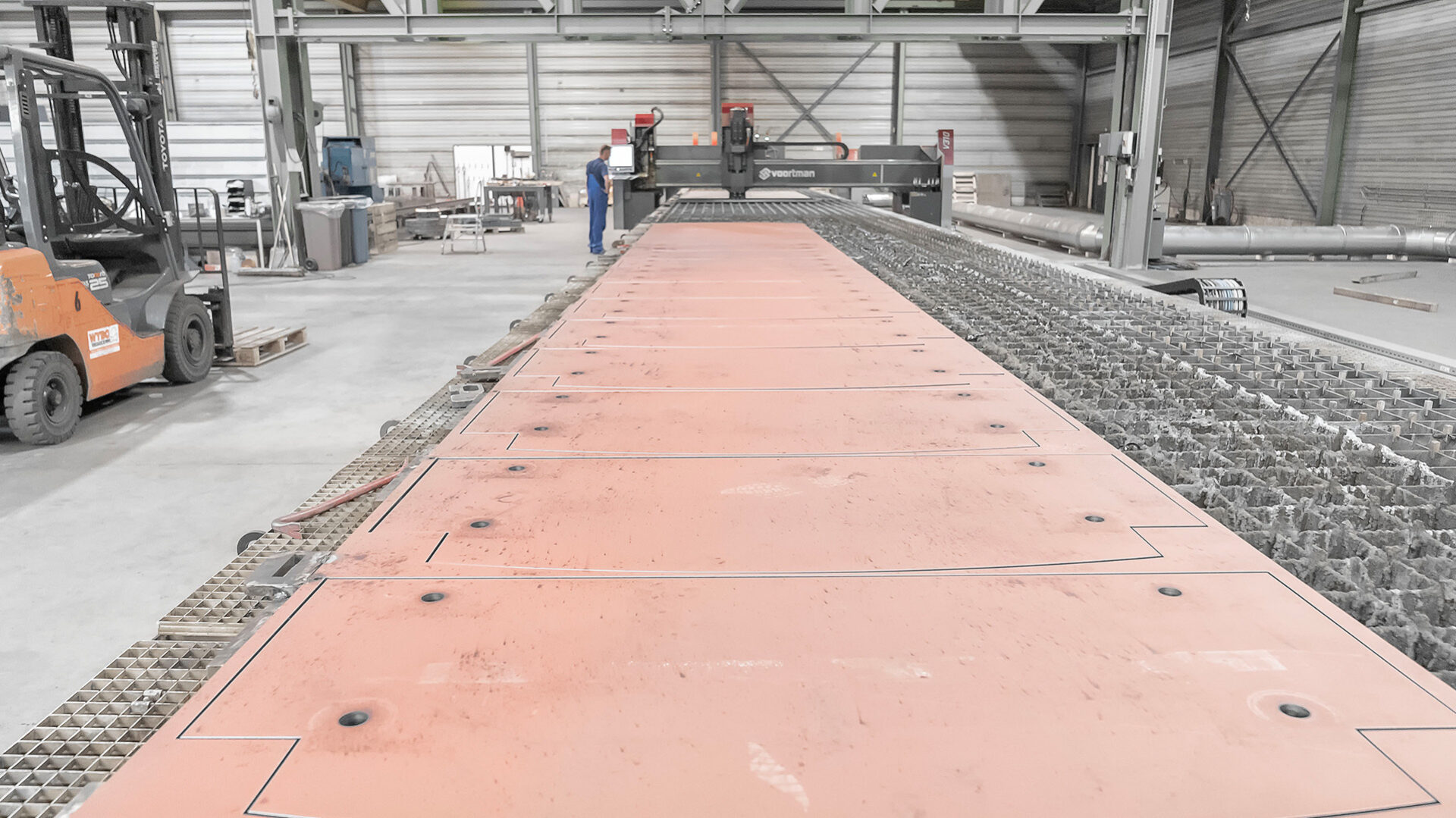
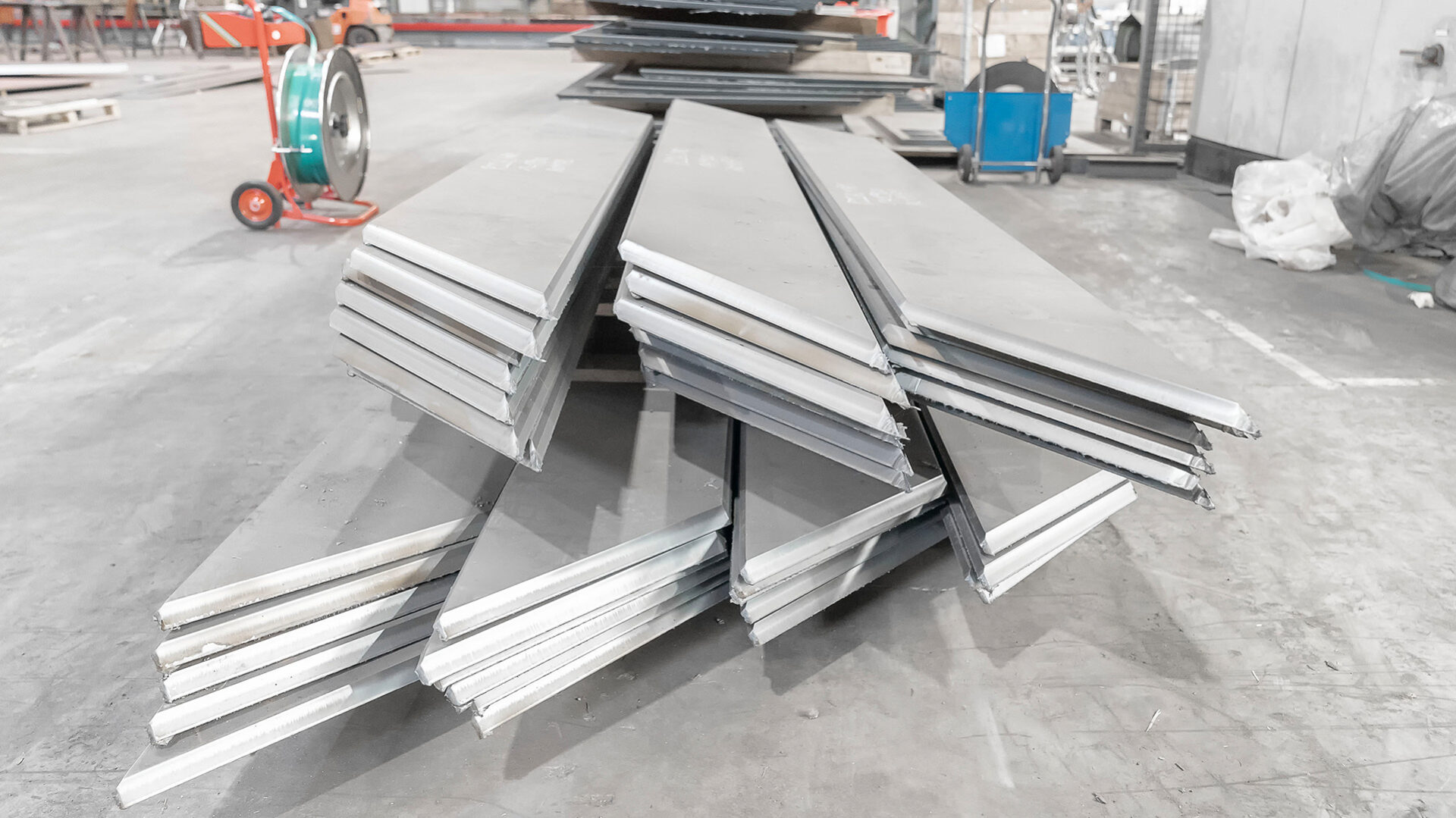
Die hintere Brücke schneidet mit 3 Autogenbrennern, während die vordere Brücke ein langes Blech mit Plasma schneidet.
Die Teile werden aus dem langen Blech geschnitten, wobei die Löcher vorher gebohrt werden, so dass der Schnitt nahtlos fortgesetzt werden kann.
Perfekte Schweißnahtvorbereitungen auf Knopfdruck.
Robby Delys skizziert ein Beispiel: "Es ist bedauerlich, dass wir die Maschine damals noch nicht für ein Projekt hatten. Wir arbeiteten an einem Projekt für Wassertanks, bei dem die Bleche mit einer Schweißnahtvorbereitung versehen werden mussten. Wir mussten die Bleche jedes Mal vom Laser wegbewegen, um sie mit einer Fase zu versehen, und dann das Blech erneut zum Walzen bewegen. Jetzt, mit der Voortman-Maschine, kann alles auf einem System erledigt werden, und dann geht es an die Walze für die Bleche. Hätten wir die Maschine damals schon gehabt, hätten wir viel Zeit gespart und könnten viel effizienter arbeiten.
„Das Bohren und Gewindeschneiden erfolgt dank fortschrittlicher Software sogar unbemannt und meist nachts“, sagt Yves De Smet. Produktivität und Effizienz haben sich deutlich verbessert, ebenso die Qualität und die Kontrolle über den gesamten Produktionsprozess. „Wir haben große Fortschritte gemacht, nicht nur bei den Prozessen und der Flexibilität, sondern auch bei der Verkürzung der Auftragsvorlaufzeiten“, sagt Stéphane Verhoestraete.
STOLZ UND MOTIVIERT
Neben der Effizienz bemerken die Bediener auch eine deutliche Verbesserung des Bedienungskomforts. Dies führt zu einer erhöhten Motivation. "Die Bediener sind stolz auf die Maschine, sie können auch wirklich über eine Reihe von Dingen nachdenken, z. B. ob Sie tagsüber oder nachts bohren, welche Risiken bestehen, was das eine Szenario im Vergleich zum anderen bedeutet. Dadurch kommen sie wirklich zu großartigen Lösungen und Erkenntnissen", sagt Stéphane Verhoestraete.
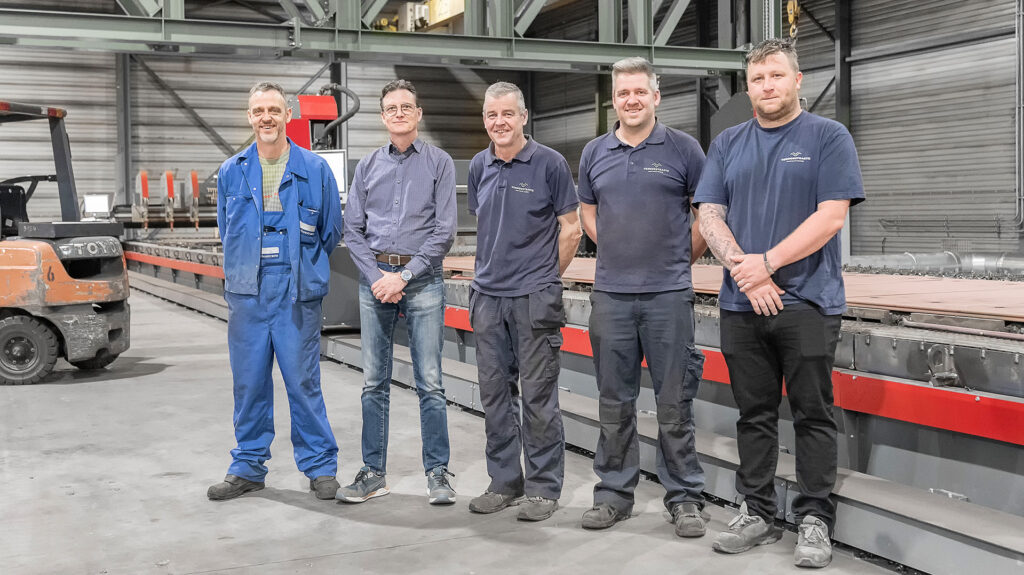
KAPAZITÄT FÜR MEHR UND EINE VIELZAHL VON PROJEKTEN
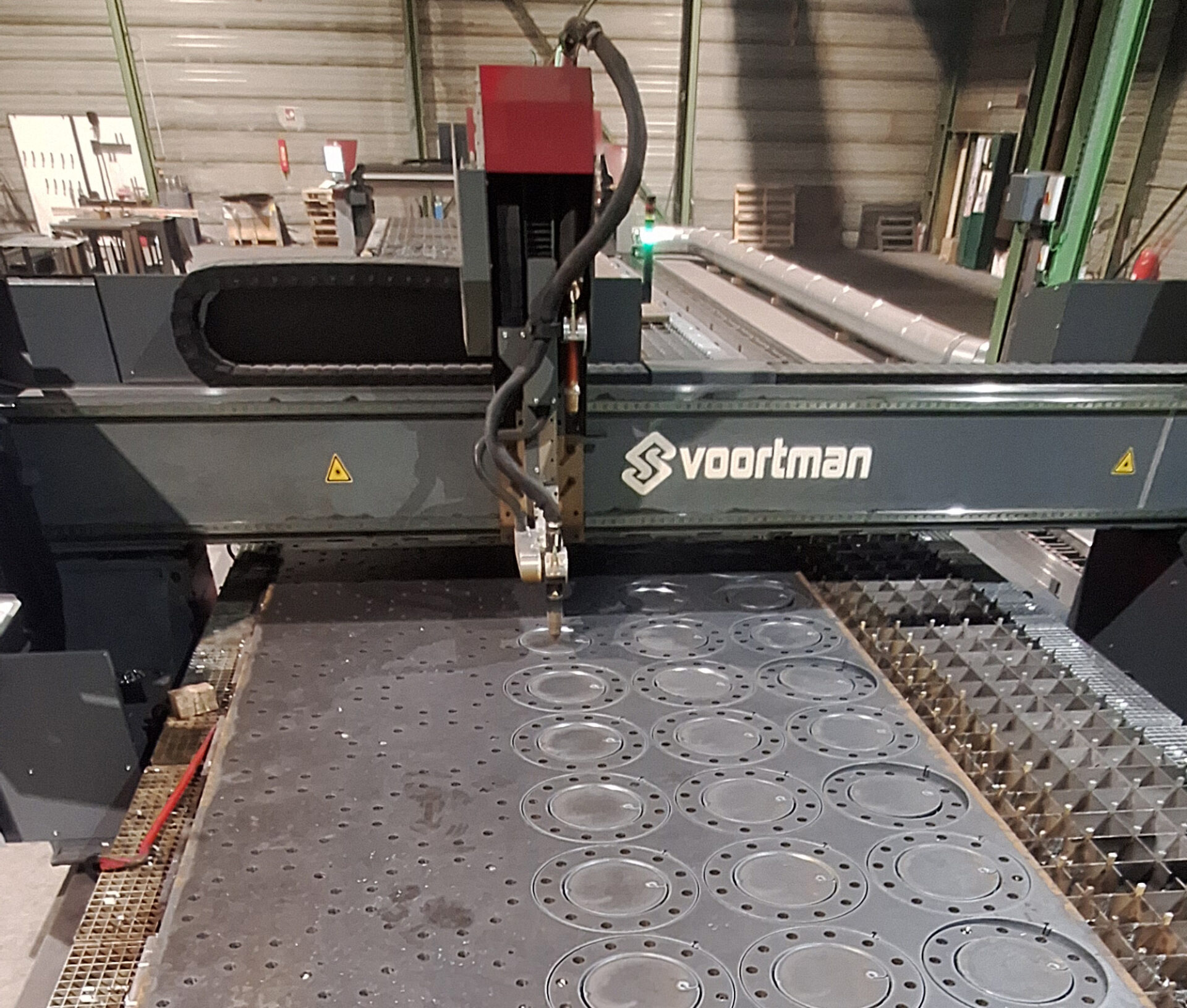
Die neuen automatisierten Verfahren wie Fasenschneiden, Bohren und Fräsen ermöglichen es Verhoestraete, größere und komplexere Projekte zu übernehmen. So haben sie beispielsweise kürzlich an dem hier abgebildeten Projekt gearbeitet, bei dem über 1.000 Bohrungen erstellt werden mussten, was mit dem manuellen Bohren in der alten Situation unmöglich gewesen wäre. „Wir haben jetzt auch ein sehr großes Projekt für Windturbinen hier auf See, ein Projekt, das wir in Anbetracht der gewünschten Anzahl von Teilen, der Geschwindigkeit und der Vorlaufzeit in der alten Situation niemals hätten durchführen können“, erzählt Delys.
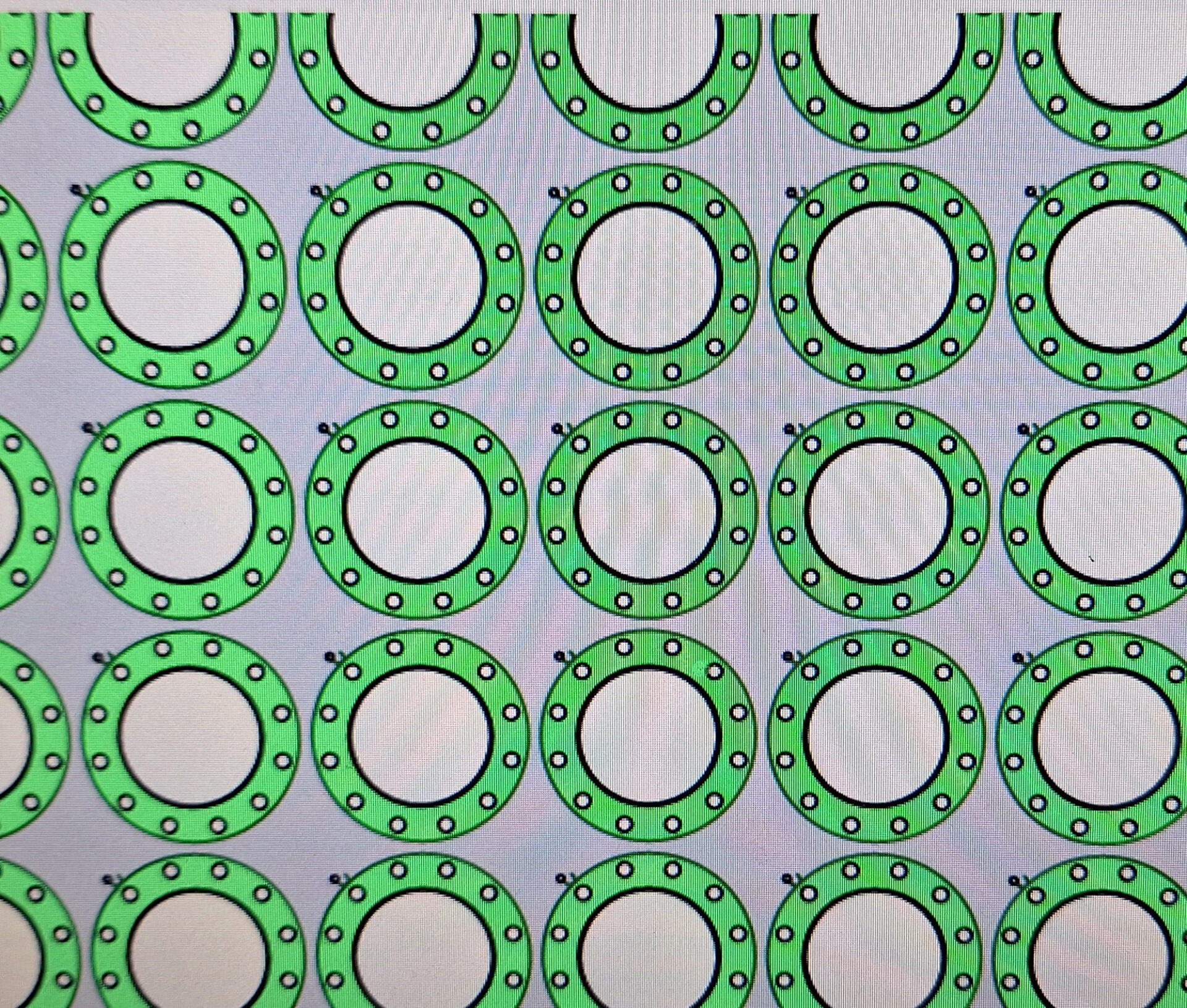
EIN ONE-STOP-SHOP ZUR ENTLASTUNG
Mit der Investition in die All-in-One-Kombimaschine von Voortman werden hochwertige Teile geliefert, die der Kunde montieren kann. „Sobald das Produkt beim Kunden aus dem Lkw kommt, kann der Kunde mit dem Schweißen und der Montage beginnen, das ist unsere Absicht“, sagt De Smet. „Wo wir früher die Bleche zuschneiden und zur weiteren Bearbeitung an den Kunden zurückschicken oder durch Dritte bearbeiten lassen mussten, können wir das jetzt alles vor Ort erledigen.“ Stéphane Verhoestraete fährt fort: "Als One-Stop-Shop wollen wir den Kunden entlasten.'' Diese Entlastung geht über die Wertschöpfung durch Produktion und Betrieb hinaus. Wir denken auch im Designprozess mit dem Kunden mit, wobei Verhoestraete als verlängerter Arm für Kunden ohne eigenes Designbüro fungiert. Eine wunderbare Form des Co-Engineerings und der Partnerschaft, in der der One-Stop-Shop-Gedanke noch weiter zum Ausdruck kommt.
DIE ÜBEREINSTIMMUNG MIT VOORTMAN IST DA
Bevor die endgültige Investition getätigt wurde, besuchte Verhoestraete den Voortman Campus in Rijssen. "Der Besuch und die Vorführung brachten viele neue Erkenntnisse. Es war auch schön zu sehen, dass Voortman die Maschinen, die sie selbst entwickeln, auch zur Herstellung verschiedener Teile ihrer eigenen Maschinen verwendet", sagt De Smet.
Die Zusammenarbeit mit Voortman wird als sehr positiv empfunden. „Die Maschine und der dazugehörige Service sind hervorragend; es ist ein Gesamtpaket, das wirklich zu empfehlen ist“, erklärt Delys. „Darüber hinaus ist die Art und Weise, wie Voortman Software und Digitalisierung betrachtet, wichtig für die Übereinstimmung mit unserer strategischen Vision“, fügt Stéphane Verhoestraete hinzu.
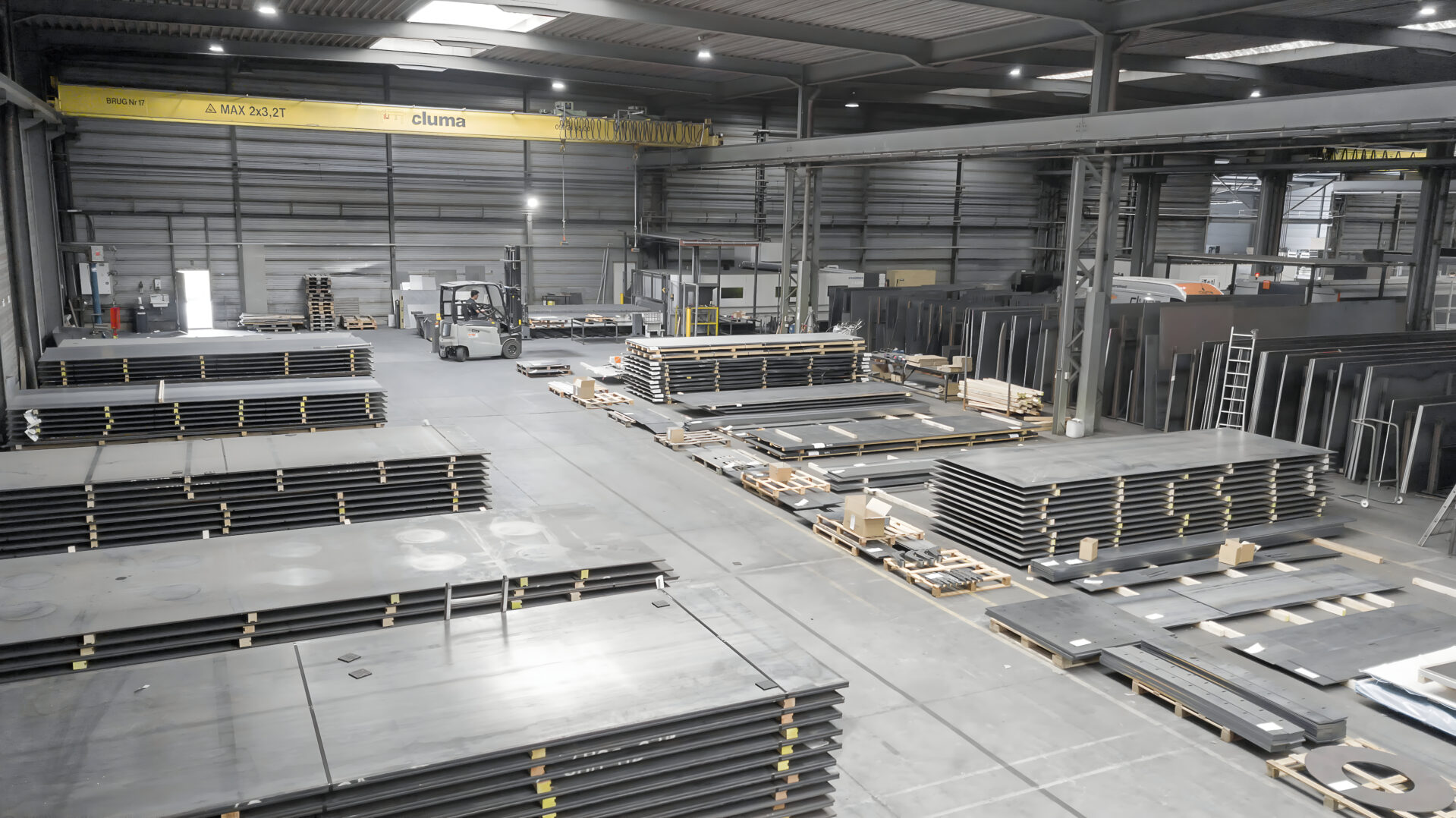
WIE SIEHT DIE ZUKUNFT AUS?
In den nächsten Jahren wird sich Verhoestraete auf die weitere Automatisierung, Digitalisierung und Optimierung seiner Produktionsprozesse konzentrieren. Dazu gehören die Anpassung von Software zur weiteren Automatisierung des Front-Ends des Produktionsprozesses und die Neugestaltung des gesamten Ablaufs in der Werkstatt. Und wer weiß, vielleicht geht dies Hand in Hand mit weiteren neuen Maschinen und Software....