INGENIEURSKUNST BEI MASSIVEN DRUCKBEHÄLTERN
für die weltweite Öl- und Gasindustrie
„Wir hatten uns bereits verschiedene Schneidemaschinen auf dem Markt näher angesehen, aber keine kam an die Kapazitäten dieser Maschine heran.“
Kundenbericht Energy Weldfab
- STANDORT:
- GEGRÜNDET:
- GRÖßE:
- White Oak, Texas
- 1990
- 121.406 M2
„Wir hatten uns bereits verschiedene Schneidemaschinen auf dem Markt näher angesehen, aber keine kam an die Kapazitäten dieser Maschine heran.“
INGENIEURSKUNST BEI MASSIVEN DRUCKBEHÄLTERN
EnergyWeldfab bewirtschaftet 30 Morgen Land und eine fast 130.000 Quadratmeter große Anlage in WhiteOak, Texas. Zweihundert Mitarbeiter arbeiten emsig in zwei Schichten und widmen sich der Herstellung massiver Druckbehälter für die Öl- und Gasindustrie. Das Know-how des Unternehmens liegt in den Bereichen Metallbiegen, Schweißen, Lochschneiden, Rohrfittings sowie der sorgfältigen Endbearbeitung und Lackierung von Behältern, die für Kunden auf der ganzen Welt bestimmt sind. Mit einer stolzen Geschichte von fast einem Vierteljahrhundert ist das Familienunternehmen ein vertrauenswürdiger Lieferant von Verarbeitungsanlagen für den Öl- und Gassektor. Die Produkte, die verarbeitet werden, umfassen ein breites Spektrum an Metalldicken von weniger als 0,25 bis 8 Zoll. Die Komplexität dieser Behälter, die durch mehrere Verbindungspunkte gekennzeichnet sind, macht umfangreiche Schneid- und Schweißarbeiten erforderlich.
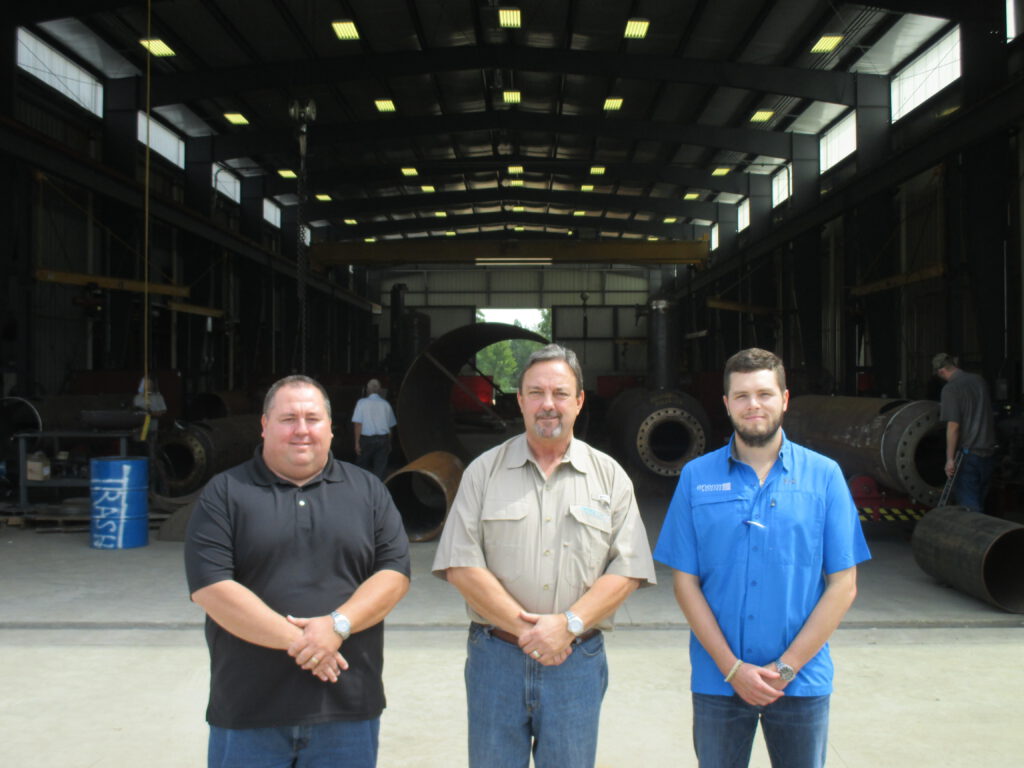
TRANSFORMATIVE LÖSUNGEN FÜR MEHR WACHSTUM
Bis vor kurzem setzte Energy Weldfab auf die traditionelle Methode des manuellen Schneidens mit einem Autogenbrenner, eine Praxis, die seit ihrer Gründung in der Branche tief verwurzelt ist. Vice President Stoney Lake erklärt: „Das war von Anfang an unser Industriestandard. Das haben wir schon immer so gemacht." Da ihr Geschäft jedoch ein erhebliches Wachstum verzeichnete, erwies sich der alte Ansatz als unzureichend, um der steigenden Nachfrage nachzukommen. Die Einstellung zusätzlicher Arbeitskräfte war aufgrund des Mangels an qualifizierten Fachkräften keine Option. Lake erklärt: „Wir stehen vor einem echten Fachkräftemangel. Früher war das nicht so. Arbeiter mit Erfahrung bei Rohrinstallationen klopften an unsere Tür. Heute ist es schwierig, Personen zu finden, die einen Behälter manuell auslegen und die Löcher genau schneiden können." Energy Weldfab erkannte die Notwendigkeit einer umfassenden Änderung zum Schutz des Unternehmens und war sich bewusst, dass eine transformative Lösung unerlässlich war.
EINE MODERNE ROHRPROFILSCHNEIDEMASCHINE
Um dieser Herausforderung zu begegnen, hat Energy Weldfab in eine hochmoderne 3D-Rohrprofilschneidemaschine investiert, die den arbeitsintensiven manuellen Schneidprozess ersetzen würde. Die ausgewählte MO Heavy-Duty-Maschine ist in der Lage, Rohre mit einem Gewicht von bis zu 30 Tonnen zu schneiden. Lake zeigt sich zufrieden: „Wir hatten uns bereits verschiedene Schneidemaschinen auf dem Markt näher angesehen, aber keine kam an die Kapazitäten dieser Maschine heran.“ Ihre Fähigkeit, größere Zylinder zu handhaben, übertraf jede andere verfügbare Option." Dieses vollautomatische System ermöglicht ein effizientes Profilieren von Rundrohren und gewölbten Enden (Kupeln). Ermöglicht wird dies durch eine Software, die den Informationsaustausch zwischen den sechs Achsen der Maschine, den Schneidbrennern und der CAD/CAM-Anwendungssoftware nahtlos koordiniert. Das System von Energy Weldfab verfügt über zwei Schneidbrenner, die mit einem autogenen Schneidbrenner Rohre mit einer Wanddicke von bis zu 6 Zoll schneiden, und ein Hypertherm HyPerformance HPR400XD, ein 400-Ampere-High-Definition-Plasmasystem, das hauptsächlich zum Schneiden von Edelstahlteilen oder Teilen mit dünneren Wänden verwendet wird.
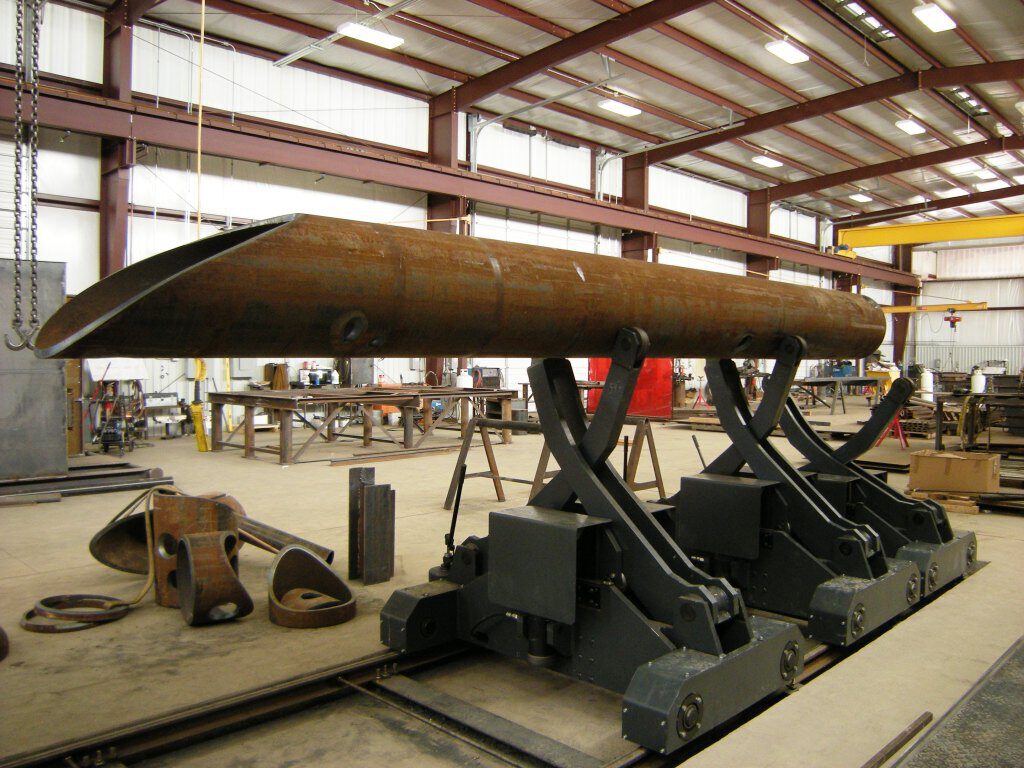
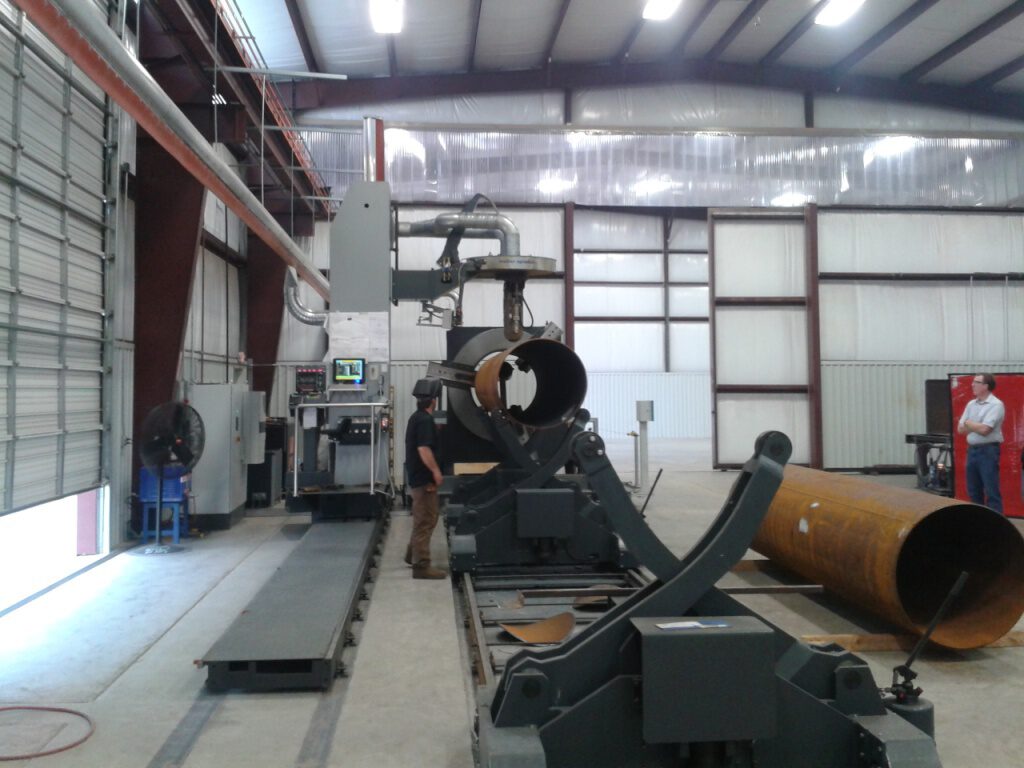
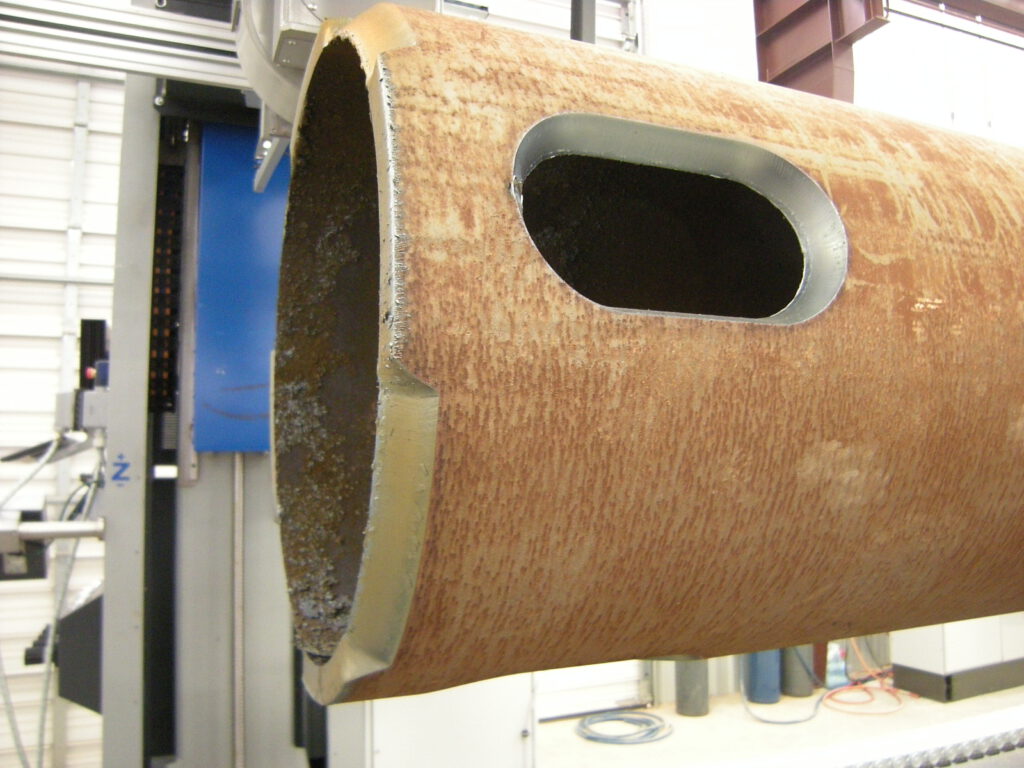
EINZIGARTIGE PRÄZISION UND PRODUKTIVITÄT
Die Ergebnisse waren nach Angaben des Unternehmens wirklich außergewöhnlich, mit deutlich verbesserter Präzision und Produktivität. Eine Aufgabe, für die früher zwei Personen und sechs Stunden benötigt wurden, kann jetzt in nur 18 Minuten erledigt werden. Lake erklärt den vorherigen Prozess :„Früher mussten zwei Mitarbeiter Linien auslegen und die zu verbrennenden Löcher signieren. Danach baten wir die Qualitätskontrolle, die Abmessungen und die Ausrichtung zu überprüfen. Nach der Genehmigung schnitten die beiden Mitarbeiter die Löcher und reinigten die Kanten. Abschließend wurde eine weitere Qualitätskontrolle durchgeführt. Heute erledigt unsere Rohrprofilschneidemaschine all diese Aufgaben nahtlos und konsolidiert fünf Schritte in einem." Darüber hinaus hat die Implementierung des neuen Systems zu einer Verringerung der Abweichungen bei der Teilequalität geführt. „Die Schnittqualität ist überraschend und die Fasenschnitte sind punktgenau.“